機械設計において、材料の表面粗さは、製品の性能や耐久性、コストに大きく影響を与える重要な要素です。表面粗さとは、材料の表面の微細な凹凸を指し、加工方法や加工条件に応じて異なります。この粗さは、寸法精度や摩擦、耐久性、密封性などに影響を及ぼすため、設計段階で適切に管理される必要があります。
表面粗さの測定と表記
表面粗さは通常、Ra(算術平均粗さ)やRz(最大高さ粗さ)などのパラメータで表され、単位はマイクロメートル(μm)です。Raは、測定対象の表面から算出される平均的な高さの差を表し、Rzは表面の最も高い点と最も低い点の高さ差を示します。
図面や仕様書では、これらの数値が指示されることで、製造現場で求められる表面の仕上がり具合が明確になります。
表面粗さRaと従来仕上げ記号▽の関係
✅機械設計の図面において、表面粗さを指定する際によく使用されるのが▽記号です。
✅この記号は、表面の仕上げの度合いを視覚的に示し、加工業界で一般的に使われています。
✅通常、▽の数が多いほど、表面が滑らかであることを意味し、表面粗さの値(Ra)も低くなります。
Ra(算術平均粗さ) | 従来仕上げ記号 |
50a , 100a | ~ |
12.5a , 25a | ▽ (1発) |
3.2a . 6.3a | ▽▽ (2発) |
0.4a . 0.8a , 1.6a | ▽▽▽ (3発) |
0.012a , 0.025a , 0.05a , 0.1a , 0.2a | ▽▽▽▽ (4発) |
表面粗さと▽記号の関係
表面粗さの指定は、製造工程で部品の機能や寿命、コストに大きく関わるため、適切に指定することが重要です。過剰に滑らかな表面仕上げを要求すると、加工コストが上昇し、製造時間も長くなる可能性があります。設計者は、機能に必要な最低限の表面粗さを見極め、過剰な要求を避けることが重要です。
表面粗さが重要な理由
摩擦と摩耗
✅表面が粗いと摩擦が増加し、部品同士が擦れやすくなり、摩耗が進みます。
✅逆に、過度に滑らかな表面は潤滑がうまく機能しない場合があります。
✅適切な表面粗さを選定することで、摩耗を最小限に抑え、製品の寿命を延ばすことが可能です。
密封性
✅シール部やガスケットなど、密封性が求められる箇所では、適切な表面粗さが重要です。
✅粗すぎると漏れが発生し、滑らかすぎると潤滑不良や接触不良の問題が生じる可能性があります。
✅シールの性能や信頼性に直接影響を与えるため、表面粗さの管理が不可欠です。
接合部の強度
✅接合面における表面粗さは、ボルトや溶接などの接合部の強度や信頼性にも影響を与えます。
✅粗すぎる表面では、接触面積が減少し、応力集中が起こりやすくまります。
✅設計段階で適切な表面仕上げを指示することが重要です。
見た目と触感
✅製品の外観品質や触感も、表面粗さに大きく左右されます。
✅滑らかな仕上げは高級感や美しさを演出します。
✅しかし、場合によっては適度な粗さが必要とされる場合もあります。
表面粗さの指定方法
表面粗さは、製造業における標準的な基準として、ISO 4287やJIS B0601などの規格によって管理されています。これらの規格では、表面粗さの測定方法や記号の使い方が定められており、設計図面には指定された記号や数値が記載されます。
たとえば、”Ra 1.6″ と表記された場合、その面は1.6μmのRa値で仕上げられることを意味します。
加工方法と表面粗さの関係
表面粗さは、加工方法に強く依存します。たとえば、以下のように加工法ごとに仕上がりの粗さが異なります。
表面粗さは「μm(マイクロメートル)」単位で表され、加工方法ごとに異なります。
加工方法 | Ra(μm) | Rz(μm) |
---|---|---|
研磨仕上げ | 0.05 ~ 0.2 | 0.1 ~ 1.0 |
ラッピング | 0.01 ~ 0.05 | 0.05 ~ 0.2 |
フライス加工 | 1.6 ~ 6.3 | 6 ~ 25 |
旋盤加工 | 0.8 ~ 3.2 | 3 ~ 15 |
鋳造 | 12.5 ~ 50 | 50 ~ 200 |
📌 用途に応じた表面粗さの目安
✔ 軸受や摺動部 → Ra 0.1~0.4 μm(研磨仕上げ)
✔ シール部品 → Ra 0.2~0.8 μm
✔ 一般機械部品 → Ra 1.6~6.3 μm(旋盤・フライス加工)
✔ 鋳造品・鋳物 → Ra 12.5 μm以上(粗い仕上げ)
加工法の選定は、必要な表面仕上げとコスト、精度のバランスを考慮する必要があります。たとえば、高精度で滑らかな仕上げが必要な場合は研削加工やラッピングが用いられますが、コストが上がるため、設計者は最適な加工法を選定する必要があります。
表面粗さとコスト
表面粗さを小さくする、つまり表面をより滑らかにするほど、加工コストが上昇します。したがって、製品の機能に適した最小限の表面粗さを指定することで、コストを抑えることが重要です。過度に厳しい表面仕上げを指定すると、製造工程が増加し、コストが無駄にかかることになります。
設計段階で適切な表面粗さの選定を行うことは、製品のコストパフォーマンスを最適化するために欠かせません。
表面粗さの理解と標準片の活用
機械設計では、部品の表面粗さは、機能性や加工性に直接影響を与える重要な要素です。例えば、滑らかな表面が必要な摺動部品や、適切な粗さが求められる接着面など、使用環境や機能に応じた表面仕上げが求められます。このため、設計者が表面粗さの感覚を正確に把握することが、部品設計や加工指示の精度向上につながります。
表面粗さの基礎知識
表面粗さは、加工面の凹凸を数値化したものです。主に以下のような指標で表されます:
- Ra(算術平均粗さ):表面の凹凸の平均高さを算出した値
- Rz(最大高さ粗さ):最も高い部分と最も低い部分の差を基準とした値
これらの数値が小さいほど、表面は滑らかであると評価されます。
表面粗さ標準片とは
表面粗さ標準片は、異なる粗さに仕上げられたサンプル片で、触覚や視覚を通じて表面粗さを確認するために使用されます。
各片には具体的なRaやRzの数値が刻印されており、実際の部品表面と比較することで、粗さの感覚を掴むことが可能です。
標準片を使った粗さ感覚のトレーニング
表面粗さ標準片を活用することで、設計者や加工担当者は以下の能力を養うことができます。
✅触覚での確認
標準片を指や爪でなぞることで、表面の滑らかさを感覚的に理解する。
✅視覚での確認
光の反射具合や仕上げ模様を観察し、加工跡の特徴を把握する。
✅数値と感覚の一致
数値で表された粗さと実際の手触りを対応付けることで、加工現場での精度確認が容易になる。
表面粗さ感覚の重要性
数値だけで表面粗さを理解することは難しく、実際の感覚と乖離が生じる場合があります。そのため、設計者が標準片を用いて粗さを直感的に理解することが非常に重要です。
感覚を身に付けることで、以下のような設計精度が向上します。
📌加工指示書の適切な作成
📌部品の仕上げ面の品質確認
📌適切な表面処理方法の選択
表面粗さ感覚を活用した設計の事例
- 滑らかさが求められる摺動面
- 表面粗さ標準片を参照し、Ra 0.8以下の仕上げ指示を設定。
- 接着性向上が必要な接合面
- 標準片を用いて適切な粗さ範囲(例:Ra 3.2〜6.3)を選定。
- 見た目を重視する装飾部品
- 標準片を比較し、光沢感と滑らかさを確認した上で指示書を作成。
表面粗さは機械設計における重要な設計要素の一つであり、その理解は製品の品質や性能に直結します。表面粗さ標準片を使用して触覚と視覚で感覚を掴むことで、設計の精度を向上させることが可能です。
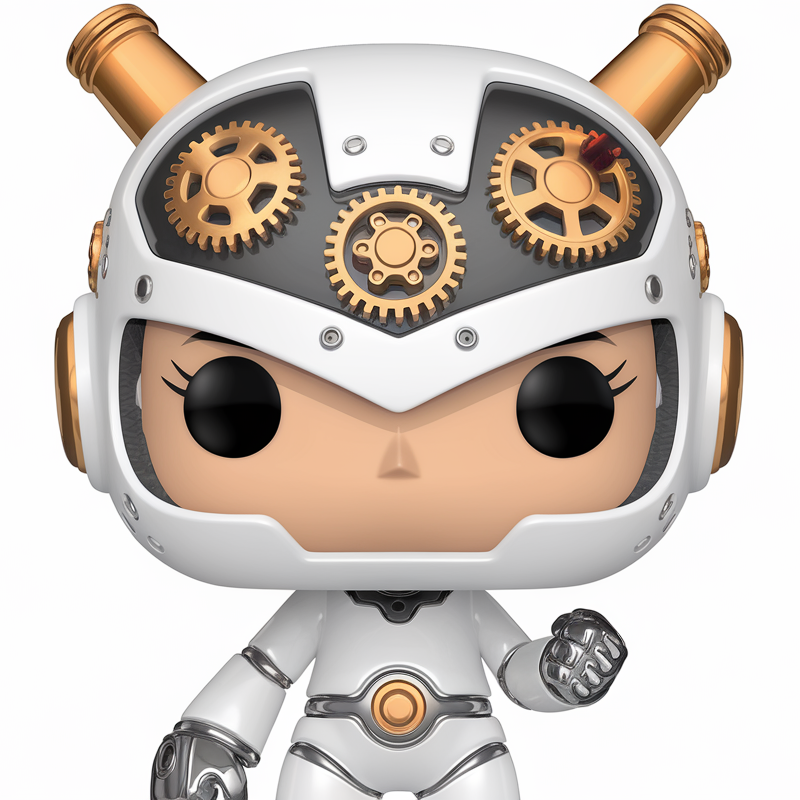
設計者や加工担当者は、このツールを積極的に活用し、より高い設計品質を追求しましょう。
まとめ
材料の表面粗さは、機械設計における製品の機能性や耐久性に直接的な影響を及ぼすため、正確に指定し管理することが重要です。摩擦や摩耗、接合強度、密封性、さらには外観にまで関与するため、表面粗さの適切な管理は、設計者にとって不可欠な要素です。加工法やコストとのバランスを考慮しながら、必要な粗さを選定することで、最適な製品品質を実現できます。
コメント