部品設計において、「深い溝」や「深い穴」を設けたくなることはありますが、切削加工では“深さ”が大きな課題になることがあります。
今回は、「なぜ深い溝・深穴がNGなのか?」と「どう工夫すればよいか?」を初心者にもわかりやすく解説します。
なぜ深い溝・深穴は避けたほうがいいの?
細長い工具が必要になる
深い部分を削るためには、長くて細い工具(エンドミルやドリル)を使う必要があります。
しかし、これには大きなデメリットがあります。
工具が“たわむ”・“ビビる”
細長い工具はたわみやすく、振動(ビビリ)が発生しやすくなります。
これにより以下のような問題が起きます。
🚫 加工精度が不安定になる
🚫 表面が粗く仕上がる
🚫 工具の破損リスクが高まる
🚫 追加の仕上げ加工が必要になる(工数・コスト増)
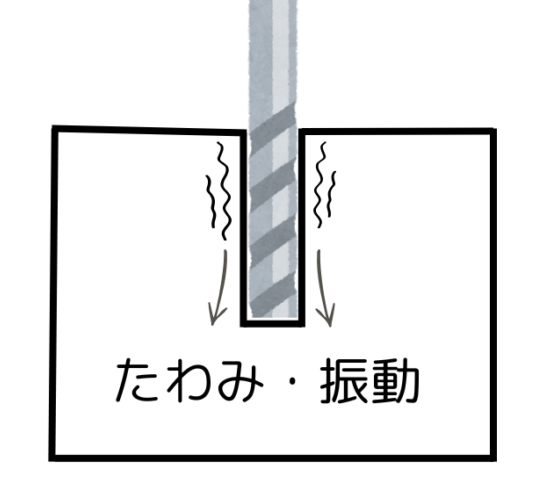
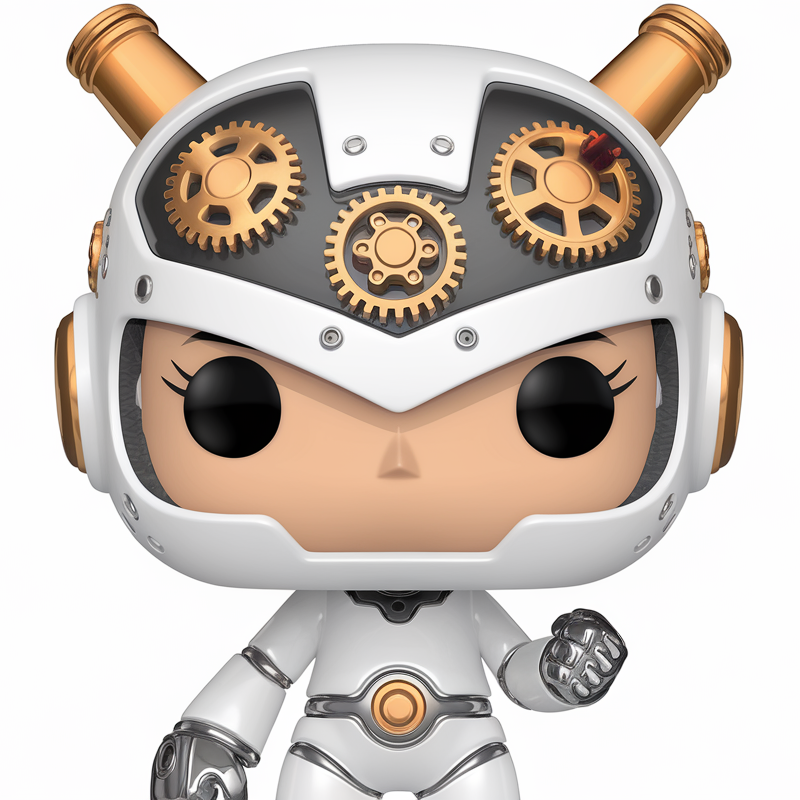
特に、穴の深さが直径の5倍を超えると、加工難易度が一気に上がります。
設計の工夫ポイント
溝や穴はできる限り浅く設計する
設計段階で、「本当にこんなに深くする必要があるか?」を見直してみましょう。
浅くできれば、それだけで加工コストと精度の問題が軽減されます。
どうしても深くなる場合は段付きにする
やむを得ず深い形状が必要な場合は、以下のような設計上の工夫をしましょう。
- 段付き形状にすることで工具のたわみを抑える
- 多段穴にして、短い工具でも届くようにする
- 裏側からも加工できる構造を検討する(貫通穴や分割構造)
精度の高い穴加工は意外と難しい!?
~設計時に気をつけたいポイント~
機械設計の中でよく登場する「穴加工」――
一見シンプルで、「ただドリルで穴を開ければいい」と思われがちですが、実は精度を出すのがとても難しい加工のひとつです。
本項では、「精度の高い穴加工ってなぜ難しいの?」という疑問に対し、設計初心者向けにわかりやすく解説します。
穴加工の“精度”って何?
穴加工における「精度」とは、主に以下の要素を指します。
✅ 穴の位置精度(設計図通りの正確な位置に穴があいているか)
✅ 穴の寸法精度(穴の直径が指示通りになっているか)
✅ 真円度・真直度(穴の形が歪んでいないか)
✅ 面粗さ(穴の内面が滑らかかどうか)
精度の高い穴加工が難しい理由
ドリルだけでは寸法精度が出にくい
一般的なツイストドリルは、削りながら逃げる(ズレる)性質があり、
- 穴が真円にならない
- 穴径が少し大きくなる
- 貫通穴ではバリが出る
といった問題が起きやすくなります。
穴の位置がズレやすい
材料の硬さや切削条件によって、工具が材料に食い込む方向が変わるため、設計通りの位置に穴を開けるのは意外と難しいのです。
深穴や小径穴は特にシビア
細いドリルは折れやすく、深い穴はビビリや逃げが発生しやすくなります。
そのため、工具や加工条件の選定が非常に重要です。
精度が必要な場合の加工方法
精度の高い穴が必要な場合は、以下のような加工を組み合わせます。
加工方法 | 特徴 |
---|---|
下穴あけ(ドリル) | 荒加工。おおまかな穴をあける |
リーマ仕上げ | 穴径と表面粗さを高精度に仕上げる |
ボーリング加工 | 1つずつ工具で穴径を仕上げる精密加工 |
ホーニング加工 | さらに高精度・高品位な面を出す特殊加工 |
設計者が気をつけたいポイント
- H7公差など精密な穴寸法は、それなりの工程とコストがかかる
- 高精度が本当に必要か?を見極める
- 止まり穴か貫通穴かで加工のしやすさが変わる
- 穴位置の基準は明確に!(基準面や基準穴をしっかり設計)
✔ 精度の高い穴加工は、「ただ穴をあけるだけ」では実現できない
✔ 寸法、位置、真円度など、気を配る要素が多い
✔ 加工方法の選定や公差指示の工夫が重要
✔ 設計者も「加工の現場感覚」を意識すると良い
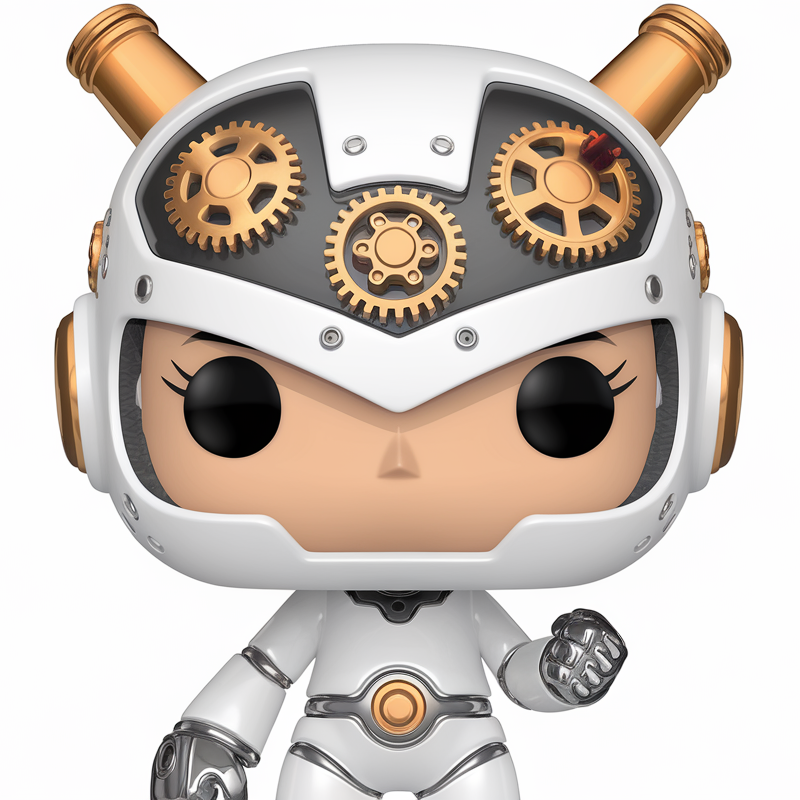
穴は設計の中でも頻出する要素だからこそ、「ただの穴」と侮らず、加工難易度にも目を向けることが重要です。
溝加工の直角度を確保するには?~逃がし加工の重要性を解説~
切削加工において「溝の直角度」をしっかり確保することは、部品精度を左右する大切なポイントです。
特に、深い溝を加工する場合には、加工工具のたわみが原因で、きれいな直角が出せなくなることがあります。
今回は、そんなときに役立つ「逃がし加工」の考え方を、初心者向けにやさしく解説します。
なぜ直角度が悪くなるの?
溝の加工には主にエンドミルという工具を使います。
このエンドミル、直径が細いまま深く削ろうとするとどうなるでしょう?
🚫 切削中に横から力(反力)がかかる
🚫 工具がわずかにたわむ・曲がる
👉 その結果、まっすぐ削れず、側面が傾いてしまう
つまり、工具が「逃げて」しまって、直角が出ない=直角度不良が起こるのです。
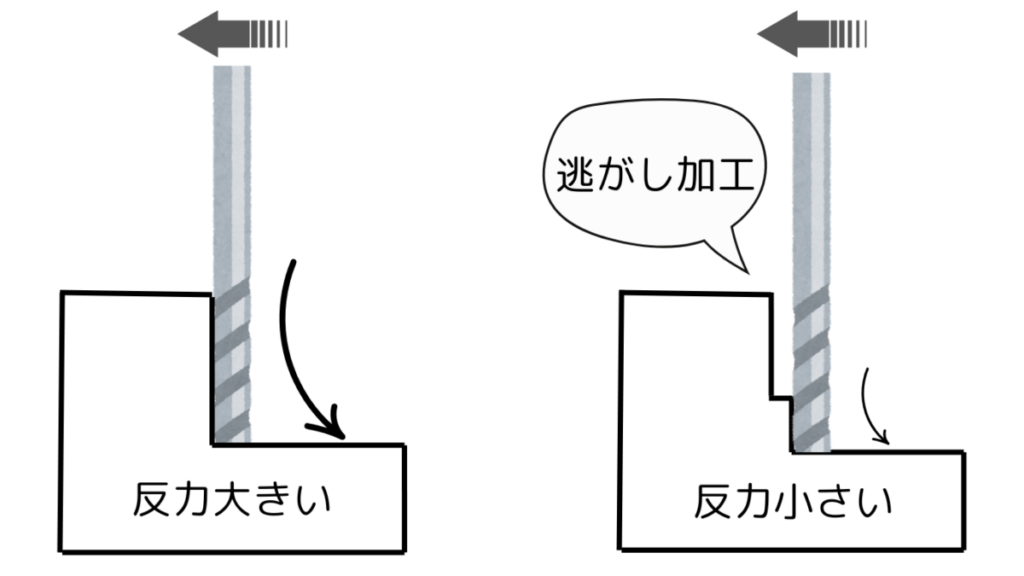
解決策:逃がし加工+段付き設計!
この問題を防ぐためのポイントがこちらです。
不要に深くしない(設計段階で深さを見直す)
まず、そもそもそんなに深い溝が必要か?をチェックしましょう。
深さを浅くできれば、それだけで直角度問題の多くは解消します。
逃がし加工(段付きにする)
やむを得ず深い場合は、「段付き形状」にして、深さを分割することが有効です。
こうすることで、工具の突き出し量(長さ)を短くでき、たわみが減るため、直角度が安定します。
目安:エンドミル径の2倍以内にする
例えば、直径6mmのエンドミルを使う場合、加工深さは12mm以内にするのが理想です。
それ以上になる場合は、段付き設計や裏側加工などの工夫を検討しましょう。
設計の工夫が加工品質を左右する!
よくあるNG | 改善の工夫例 |
---|---|
細いエンドミルで深く削る | 浅くする/段付きで逃がす |
深さの指定が曖昧 | 加工限界を考慮して寸法指定 |
✅ 溝の直角度が悪くなる原因は、工具のたわみ(逃げ)
✅ 深さはできる限りエンドミル径の2倍以内
✅ それ以上の深さが必要なときは、段付き形状で逃げ加工を設ける
✅ 設計段階での配慮が、精度とコストを大きく左右します!
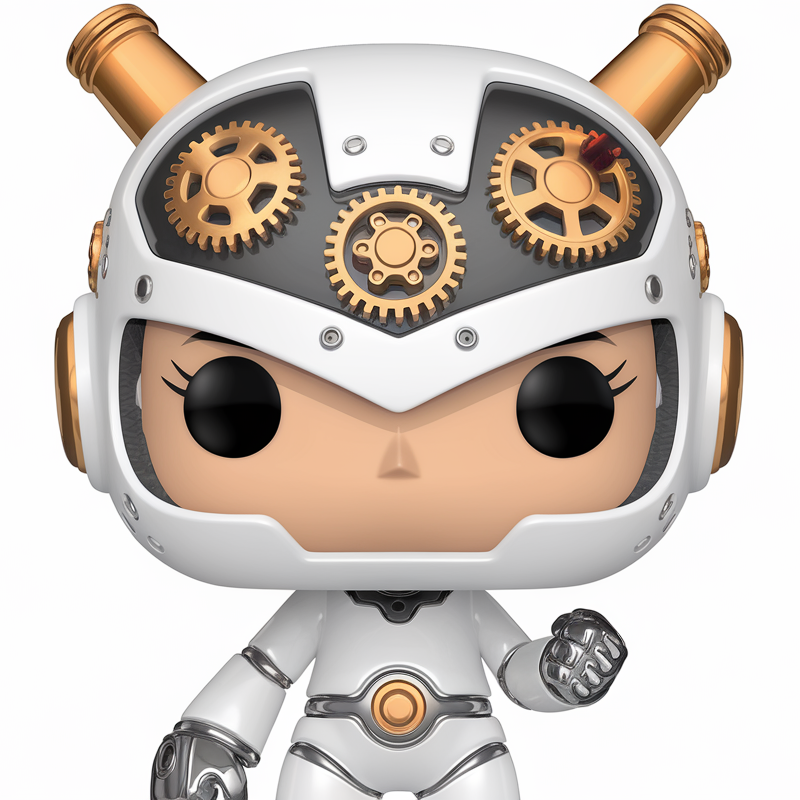
設計と加工の「ちょっとしたギャップ」を埋めるのが、精度を保ちながらコストを下げるカギです。
迷ったら、加工者と相談しながら形状を決めていきましょう!
まとめ
設計者のひと工夫が、現場の負担を軽くする
「切削加工は、できるだけシンプルに・浅く」これが鉄則です。
見た目には同じような形状でも、加工しやすさとコストには大きな差が出てきます。
設計段階で深い溝・深穴に気づいたら、本当に必要か、形状を見直すことが重要です。
コメント