「ちょっとだけ形を変えるだけでしょ?」
設計変更をそんな軽い気持ちで考えていませんか?
実は、設計変更は製造現場全体に大きな影響を与えることが多く、対応には時間もコストもかかります。
この記事では、なぜ設計変更が大変なのか、その理由と注意点を初心者の方向けにわかりやすく解説します。
設計変更が引き起こす主な影響
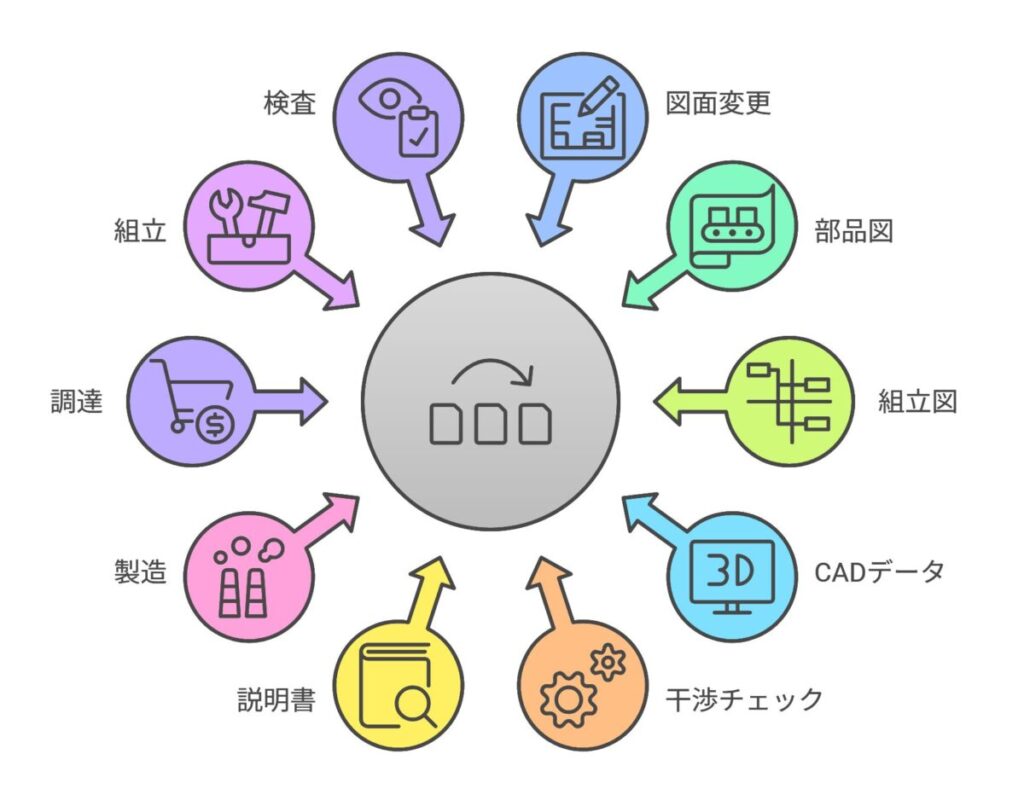
1. 図面変更だけでは終わらない
設計図を変更しただけでは済まず、以下のように多くの作業が連動して変わります。
- 部品図の修正
- 組立図・部品表(BOM)の更新
- CADデータの再作成
- 干渉チェックのやり直し
- 説明書やマニュアルも修正
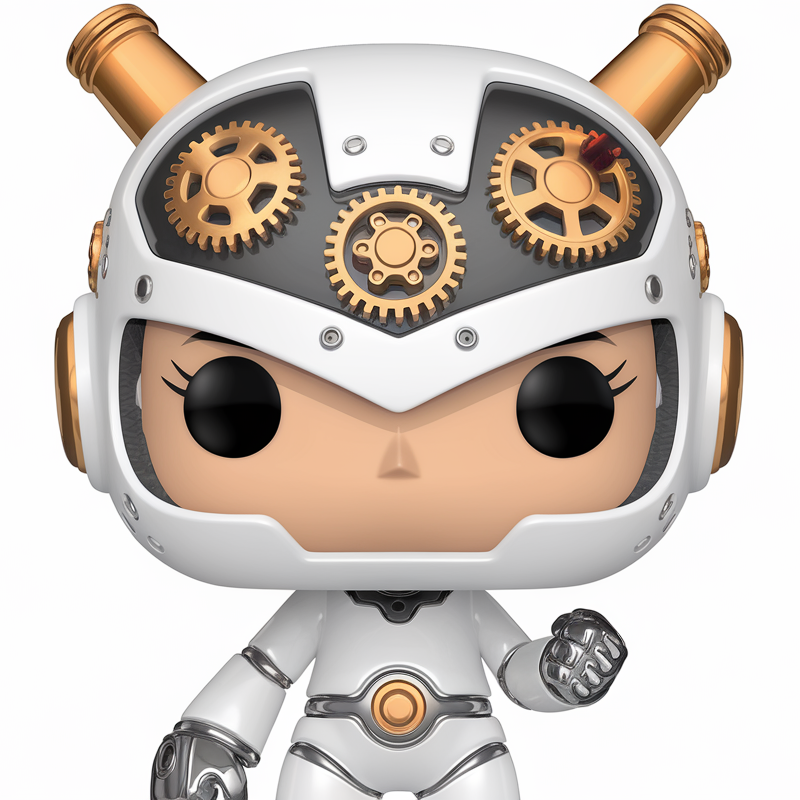
小さな形状変更でも、関連資料・システムすべての見直しが必要になる場合があります。
2. 製造・調達への影響
設計変更の内容によっては、部品の作り直しや発注のやり直しが発生します。
- すでに発注していた部品が使えなくなる
- 金型や治具を作り直す必要が出てくる
- 加工方法そのものを変える必要がある
これにより、納期の遅れや在庫のムダが発生してしまいます。
3. 組立や検査への影響
部品の形や位置が変わると、組立手順や検査内容も見直す必要があります。
- 組立治具が合わなくなる
- 組立順番を変更しなければならない
- 検査基準や検査項目も修正が必要
設計変更は、実際の現場作業にも大きく関わる問題です。
設計変更にかかる“見えないコスト”
― 意外と知らない、後工程への影響 ―
「ちょっとだけ形を変えたいだけなのに、なんでこんなに大変なの?」
設計変更が発生すると、実はたくさんのコストが水面下で発生しています。
しかもその多くは、「図面を書き直すだけ」では済まない、“見えないコスト”なのです。
ここでは、設計変更でよく発生するコストの種類とその影響をわかりやすくご紹介します。
主なコスト項目とその内容
コスト項目 | 内容 |
---|---|
再設計費 | 設計者が再度考え直し、CADデータや図面を修正する手間が発生します。 ➤ 数時間〜数日の作業になることも。 |
材料ロス | すでに加工や製造が始まっている場合、その部品がムダになることがあります。 ➤ 使えない在庫が増えるだけでなく、廃棄にもコストがかかる場合も。 |
再製作費 | 金型や治具を再作成する必要が出ると、大きな費用が発生します。 ➤ 数万円〜数十万円の追加コストになるケースもあります。 |
調達コスト | 新たな部品や材料を手配する必要があり、納期や価格の調整が発生します。 ➤ 特殊部品の場合は、リードタイムの遅れにも直結。 |
納期遅延 | 設計変更によってすべての工程が後ろ倒しに。 ➤ 顧客からの信頼を損ねるリスクもあります。 ➤ 最悪の場合はペナルティやキャンセルの可能性も。 |
なぜ“見えない”のか?
これらのコストは、図面1枚を書き直すだけと思っていると見落とされがちです。
でも実際には、「1つの変更」が設計・製造・組立・納品すべてに波及します。
たとえば…
- ボルト穴の位置を2mmずらしただけで…
- 部品の再加工が必要
- 組立治具が使えなくなる
- 対応するカバーの設計も変更
- 組立順序や説明書も見直し
👉 結果的に、関係する部署すべての手間と時間が増えるのです。
設計者が気をつけたいポイント
✅ 変更前に本当に必要か再確認する
✅ 影響範囲をよく把握する(図面だけでなく周辺部品や工程も)
✅ 関係部署と早めに相談する
✅ 変更内容を明確に記録・共有する(ECOや変更通知など)
設計変更は「一見簡単でも、じつは複雑」な作業です。
特にコスト面では、再設計・ロス・納期遅延など、目に見えにくい部分で大きな影響が出ます。
だからこそ、設計段階でのミスや見落としをできるだけ防ぐことが重要です。
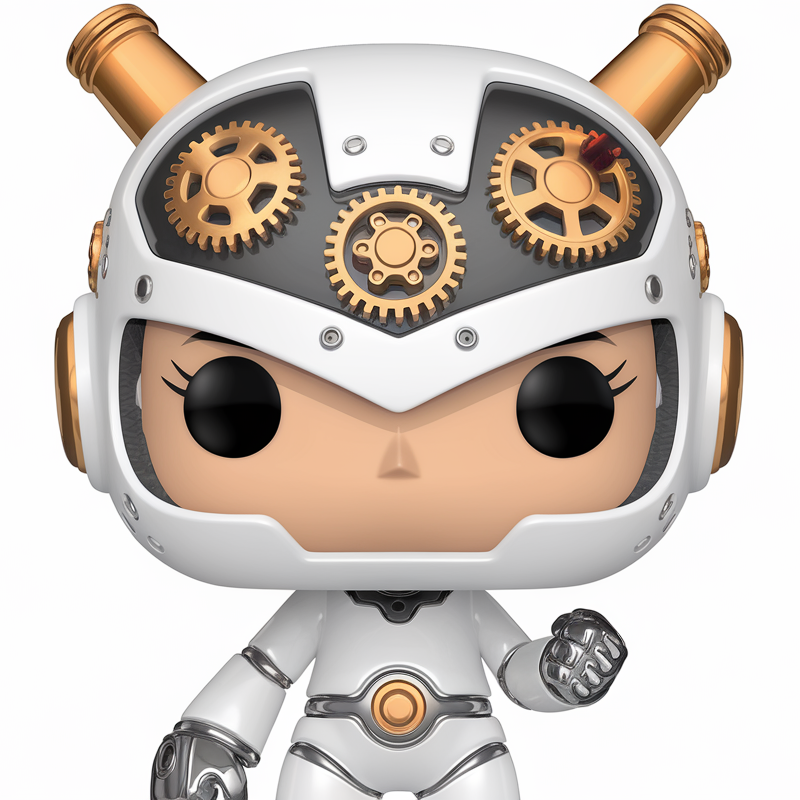
「ちょっと変えるだけ」のつもりが、大きな手戻りにならないように――
変更の前には一呼吸、全体を見渡す目が設計者には求められます。
設計変更を避けるためのポイント
― 最初の一手が、後の大きな手戻りを防ぐ ―
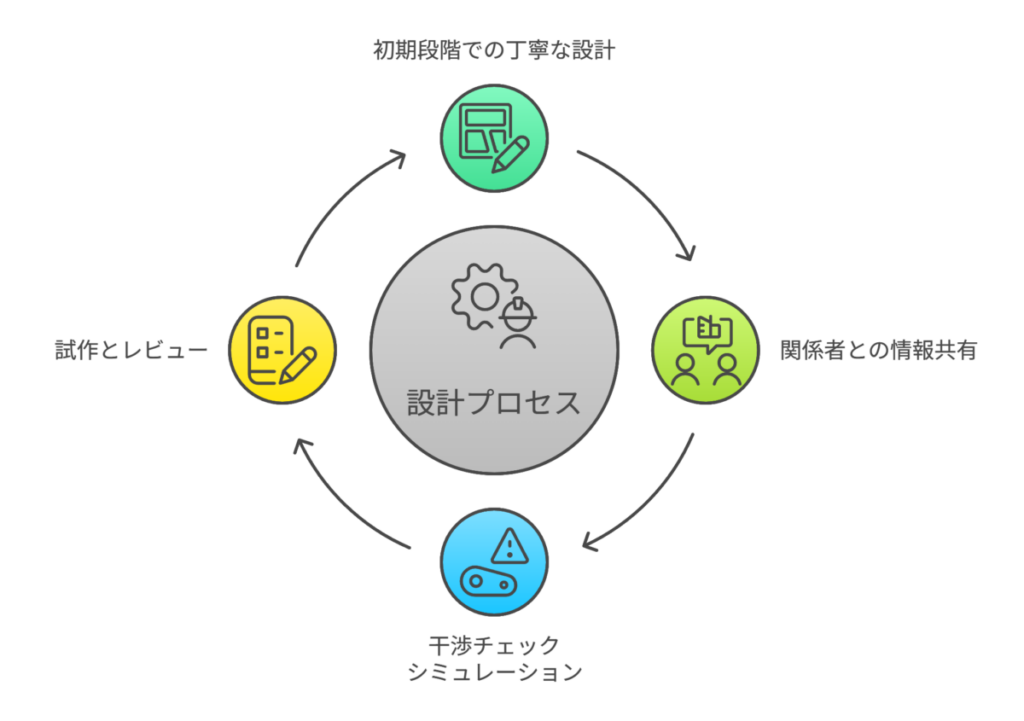
設計変更はコストも時間もかかる、できれば避けたいトラブルです。
では、どうすれば「後から困る」ような変更を防げるのでしょうか?
答えはシンプルです。
設計の初期段階で、しっかりと考え抜くこと。
ここでは、設計変更を最小限にするための4つの重要ポイントをやさしく解説します。
① 初期段階での丁寧な設計と検討
設計を始めるとき、「とりあえず形にしてから考えよう」というのは危険です。
最初の考えが甘いと、後から次々に修正が必要になります。
- 本当にその構造で組み立てられる?
- 材料や部品は調達しやすい?
- 必要な強度は確保できる?
👉 こうした点を最初に丁寧に検討することが、後工程を守るカギになります。
② 関係者とのこまめな情報共有
設計者だけが内容を理解していても、他部署(製造・組立・調達など)が同じ認識でなければ、思わぬミスにつながります。
- その部品、加工できる?
- 組立現場で問題にならない?
- 納期や予算に影響しない?
👉 こまめに確認・共有することで、「後から聞いてない!」を防げます。
③ 事前の干渉チェックやシミュレーション
CADを使えば、パーツ同士がぶつかっていないか(干渉チェック)を簡単に確認できます。
また、最近では3Dシミュレーションを活用して、動作確認や強度解析も事前に行えるようになりました。
👉 手戻りの原因になりやすい見落としや干渉は、設計中にしっかり潰しておくのがポイントです。
④ 試作やレビューの段階で不具合を見つける
量産前の試作や、他の設計者とのレビュー(設計検討会)はとても有効です。
- 他人の視点で見てもらう
- 実際に形にして問題点を洗い出す
👉 「小さな試作で、大きな失敗を防ぐ」ことができます。
設計は最初が肝心!
設計変更が発生すると、コスト・納期・信頼性に大きな影響を与えてしまいます。
そのため、「とりあえず作る」ではなく、
- しっかり考える
- 共有する
- チェックする
という基本を丁寧に行うことで、「後からの大変な変更」をぐっと減らせます。
ポイント | 内容 |
---|---|
丁寧な初期設計 | 最初にじっくり考える |
情報共有 | 周囲とのすり合わせを忘れずに |
干渉・動作チェック | CADやシミュレーションを活用 |
試作とレビュー | 小さく試して、大きな失敗を防ぐ |
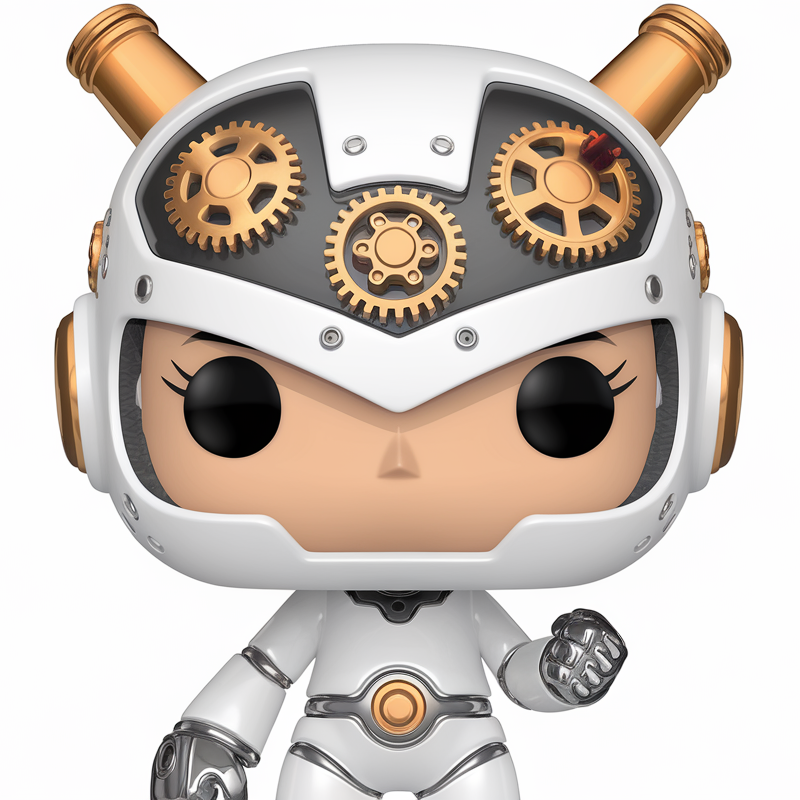
設計とは、未来のトラブルを未然に防ぐための仕事です。
一手間を惜しまないことが、結果的に楽な工程・高い品質・安心な納品につながります。
まとめ:設計変更は「全体を動かす」大きな作業
設計変更は、単なる図面修正ではありません。
製造・調達・組立・検査・納期など、すべての工程に影響を与える可能性があります。
だからこそ、設計段階での見落としは少なく、
関係者と連携しながら慎重に進めることが重要です。
「小さなミスが大きな損失に」――これが設計変更の怖さなのです。
コメント