機械図面を見ると、「Ra3.2」や「▽▽▽」といった記号を見かけたことはありませんか?
これは部品の表面のなめらかさ(=表面粗さ)を示すものです。
初心者の方は、「そこまで細かく気にしないとダメ?」と思うかもしれませんが、表面粗さは部品の性能や寿命に直結する大事な設計要素です。
表面粗さとは?
表面粗さとは、目に見えない微細な凹凸の大きさのことです。
たとえば金属の板を削ったとき、ツルツルかザラザラかという違いが、表面粗さにあたります。
表面粗さは「Ra(算術平均粗さ)」という単位で表され、数値が小さいほどなめらか(高精度)、大きいほど荒い仕上げになります。
粗さ記号 | 代表的なRa値 | 仕上げ状態 |
---|---|---|
▽▽▽▽ | Ra0.8以下 | 高精密研磨 |
▽▽▽ | Ra1.6程度 | 精密加工品 |
▽▽ | Ra3.2程度 | 一般的な機械仕上げ |
▽ | Ra6.3以上 | 荒加工・鋳造面など |
なぜ部品に表面粗さの指定が必要なの?
― 機能を守り、ムダな加工を防ぐため ―
機械設計の図面を見ると、「▽▽▽」や「Ra1.6」などの表記を見かけることがあります。これは部品の「表面のなめらかさ(表面粗さ)」を指定する記号です。
でも、これを見た初心者の方は、
「そんな細かい凹凸まで指定する必要あるの?」
と疑問に思うかもしれません。
実はこの表面粗さの指定には、ちゃんとした“意味”があります。
以下で、2つの大きな理由をわかりやすく説明していきます。
理由①:部品の機能を保証するため
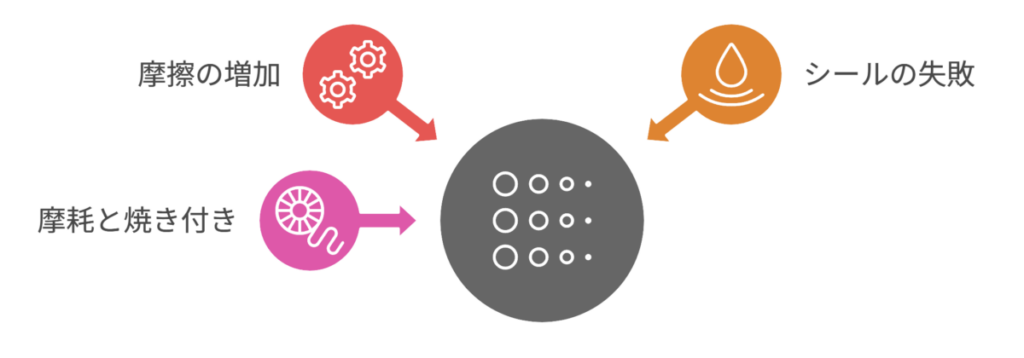
部品の表面があまりにもザラザラ(粗い)だと、機械としてうまく動作しない場合があります。代表的なトラブルをいくつか紹介しましょう。
摩擦が大きくなる
たとえば、軸がブッシュの中で直動する場合。
表面がザラザラしていると滑らかに動かず、摩擦が大きくなって直動がスムーズにいきません。
シールが効かなくなる
Oリングやガスケットなどの密封部品は、接触面がなめらかでないとしっかり密着せず、隙間から漏れが発生してしまいます。
摩耗や焼き付きが起きやすくなる
部品同士が接触してこすれ合う部分(摺動部)では、表面が粗いと、摩耗が早く、焼き付きの原因にもなります。
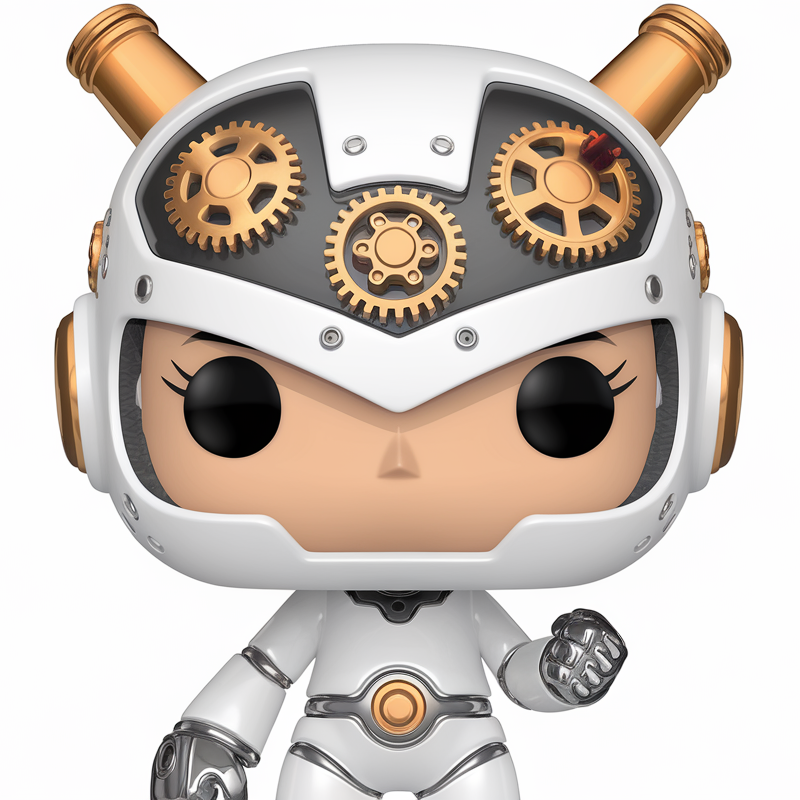
つまり、表面粗さを適切に管理しないと…
部品が本来の性能を発揮できず、「正しく動かない機械」になってしまうのです。
理由②:コストと加工工数を抑えるため

逆に、どこでもかしこでも“超キレイな仕上げ”を指定してしまうのも、設計ミスです。
滑らかにしすぎるとコストが高い
表面をピカピカにするには、「研磨」や「仕上げ加工」に時間と技術が必要です。
精度が必要ない場所まで高精度仕上げにすると、ムダにコストがかかります。
見えない・使わない面まで高精度指定しない
部品の裏側や、他の部品と接触しない部分などは、多少表面が荒くても機能に影響しないことが多いです。
そういう部分までRa1.6などと細かく指定すると、加工に手間がかかって納期も伸びてしまうかもしれません。
🔍 だからこそ大切なのは…
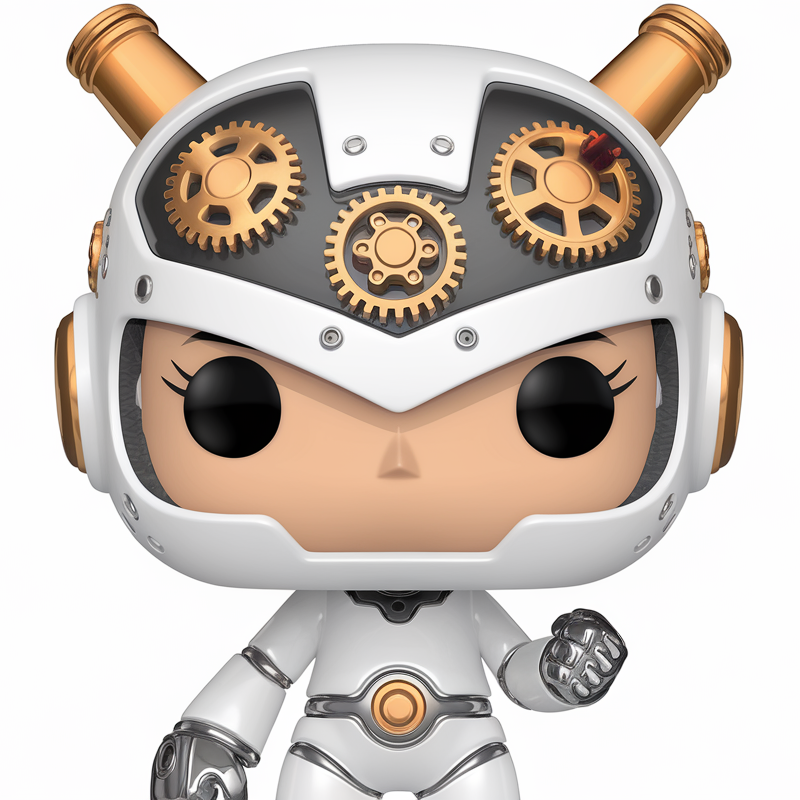
「この面は動きに関係するからRa1.6」「この面は見えないから荒加工でOK」など、
必要な面にだけ適切な表面粗さを指定することです。
表面粗さは「機能とコストのバランス」調整のカギ
- 粗すぎると…
- 正しく動かない、摩耗や漏れの原因になる
- なめらかすぎても…
- 無駄な加工、コストアップ、納期遅延
だからこそ、表面粗さの「適切な指定」が設計のセンスを問われるポイントです。
部品が「正しく動く」ために、そして「ムダな加工を減らす」ために。
設計者として、表面粗さを意識した図面作成ができるようになりましょう!
表面粗さの例:どんな場面で重要?
― 機能に応じて“仕上げレベル”を使い分けよう ―
「部品の表面がどれだけツルツルかザラザラか」――
これが 表面粗さ(ひょうめんあらさ) です。
実はこの「表面のなめらかさ」は、機械の性能やコストに直結する重要な要素です。
では、どんな場面で、どれくらいの粗さが求められるのでしょうか?
使用部位ごとの表面粗さの目安
使用部位 | 推奨される粗さ | 理由・機能 |
---|---|---|
軸とベアリングの接触面 | Ra0.8〜1.6 | 摩擦を減らし、スムーズに回転させるため |
シール接触部(Oリングなど) | Ra1.6以下 | 滑らかにすることで、密着性を高めて漏れを防ぐ |
一般的な外装カバー | Ra6.3〜12.5 | 手触りや見た目は気にするが、精度は不要 |
溶接部・鋳物の表面 | Ra25以上でもOK | 表面は荒くても、機能に影響しないため |
📌Ra(アールエー)とは?
Raは「粗さの単位」で、数字が小さいほどなめらか、数字が大きいほどザラザラです。
設計時の注意点:やりすぎに注意!
表面粗さは「とにかく滑らかにすれば良い」というものではありません。
設計の際には、次のポイントに注意が必要です。
機能に必要な面だけに指定する
全ての面をRa1.6などとすると、加工に手間がかかり、コストが一気に上がります。
たとえば、見えない裏側や、性能に関係しないカバー部分まで高精度仕上げは不要。
加工方法とのバランスを考える
加工方法によって「自然に得られる粗さ」は決まっています。
加工方法 | おおよその仕上がり粗さ |
---|---|
フライス加工 | Ra3.2前後 |
旋盤仕上げ | Ra1.6前後 |
研磨仕上げ | Ra0.8以下も可能 |
加工に合わない粗さ指定は、追加工が必要になることも。
図面上での明確な指示が重要
表面粗さの記号「▽」「▽▽」「Ra○.○」を正確に記載しましょう。
特に重要な面(ベアリング接触部、シール面など)は、注記で補足説明しておくとトラブル防止になります。
表面粗さは「必要なところだけ」が設計のキモ
✅ 機能を発揮させるために滑らかに
✅ 不要なところは加工しすぎない
✅ 加工方法・コストとのバランスが重要
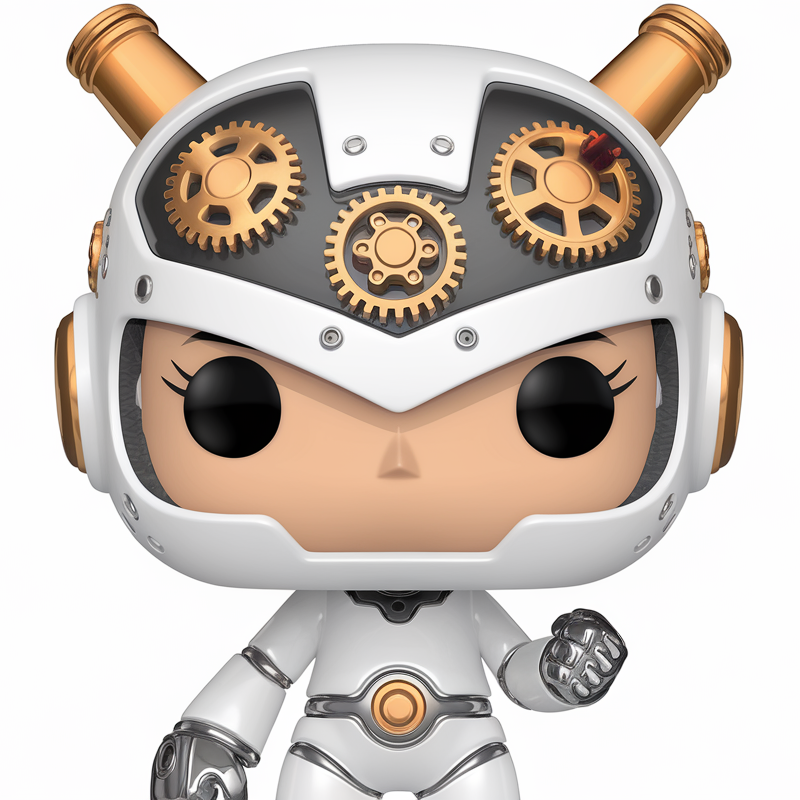
こうした「メリハリある粗さ指定」が、プロの設計者のスキルです。
部品図面を描くときは、粗さの意味と役割をしっかり意識して指定していきましょう!
まとめ:必要だからこそ、無駄にしない
表面粗さは、単なる「見た目」ではなく、機械の性能・耐久性・信頼性に直結する重要な要素です。
しかし、やりすぎれば無駄なコストや時間がかかるため、バランスの取れた設計が必要です。
表面粗さを理解することは、「正しく動く設計」と「無駄を省いた製造」の第一歩!
設計者として、必要な箇所だけに適切な指示を出せるようになりましょう。
コメント