機械設計においてH7公差は、穴のはめあいで非常によく使われる標準的な公差範囲です。
その理由には、加工の容易さや標準部品との互換性などが挙げられます。
ここでは、H7が広く採用されている理由について詳しく解説します。
H7とは?
✅ 「H7」は、JIS B 0401(ISO 286)で定められたはめあい公差の一つです。
✅ 穴の寸法公差に適用される代表的な値です。
✅ 「H」とは穴側を示し、「7」はその公差範囲を表しています。
✅ 基準寸法に対して穴の加工下限値がプラスマイナスゼロで、公差幅は一定範囲内に収まる仕様です。
たとえば、基準寸法がφ20 mmの場合、H7の公差幅は+0.000 mm ~ +0.021 mmとなります。
この範囲は、加工精度を確保しつつも製造コストを抑えられる、非常にバランスの良い設定です。
加工容易性と精度のバランス
機械設計において、穴のはめあいにはH7公差がよく採用されます。これは、「加工のしやすさ」と「適切な精度」のバランスが取れているためです。
では、具体的にどのようなメリットがあるのでしょうか?
加工の容易さ:一般的な加工方法で対応可能
H7の公差範囲は 0 〜 +0.018mm(φ10mmの場合) であり、ドリル加工+リーマ仕上げや、NC加工で容易に実現できます。
✅ 一般的な加工設備で対応可能(特別な高精度機械が不要)
✅ 追加工が少なく済む(加工コストを抑えやすい)
👉 H6やH5のような厳しい公差は、研削加工が必要になり、コストが増加してしまいます。
適切な精度:軸とのはめあいがしやすい
H7は、標準的な軸公差 h6やh7 との組み合わせで、適度なクリアランスや圧入が得られるため、多くの機械部品で適用されます。
✅ H7/h6 → 軽い圧入(回転部やスライド部に適用)
✅ H7/g6 → わずかなガタつきがある摺動部に適用
👉 H7を使えば、多くのはめあい条件に対応しやすい!
コストと精度のバランスが良い
✔ H7は加工しやすいため、コストが低い
✔ はめあい公差として十分な精度を確保できる
✔ 部品交換やメンテナンス時にも調達しやすい標準寸法
→ 高い精度を求めすぎるとコストが上がり、低すぎると機能が損なわれるため、H7が最適な選択肢になることが多い。
H7は、「加工しやすくコストが低い」かつ「十分な精度を確保できる」という理由から、機械設計の標準的な穴公差として広く使われています。
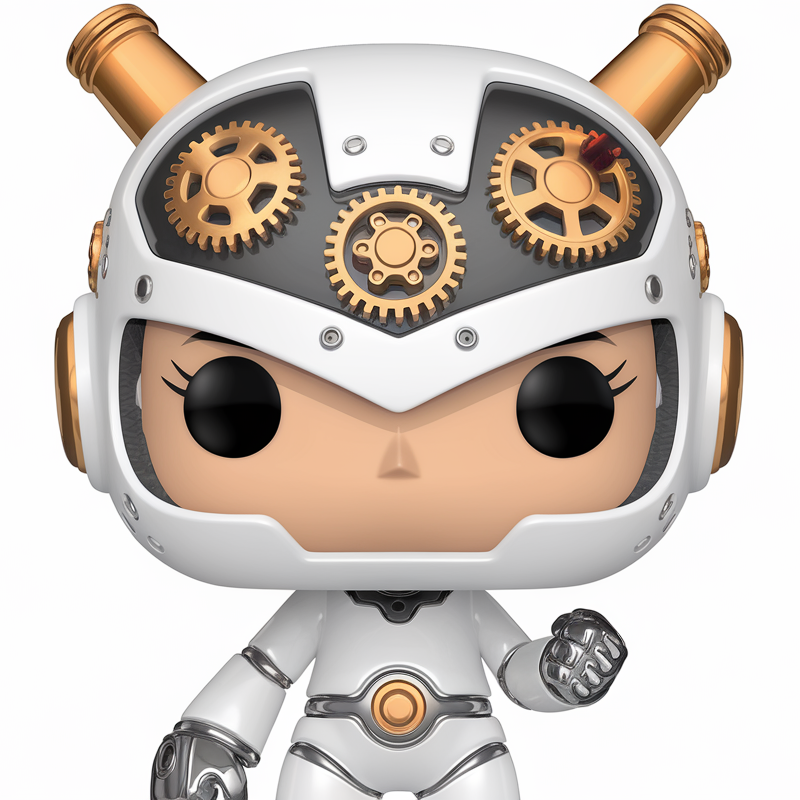
特別な高精度加工が不要な範囲で、適切なはめあいを実現できるため、コストと精度のバランスが取れた最適な公差といえるでしょう。
一般的な機能要件に対応
機械設計において、穴のはめあいにはH7公差が広く採用されています。その理由の一つが、一般的な機能要件に対応しやすいという点です。
では、具体的にどのような機能要件に適しているのでしょうか?
軸との適切なクリアランスが得られる
H7公差の穴は、軸との適切なすきま(クリアランス)や圧入具合を得やすいため、回転、摺動、固定などさまざまな機能に対応可能です。
軸の公差 | はめあいの種類 | 例 |
---|---|---|
h6 | 軽い圧入 | ベアリング、プーリー |
g6 | わずかにガタあり | スライド機構、摺動部 |
f7 | しっかりしたすきま | 軸受けブッシュ、調整機構 |
👉 H7は、はめあいの種類を選択することで、多くの機能に対応可能!
組立やメンテナンスがしやすい
- 適度なクリアランスがあるため、部品の組付けが容易
- 摩耗や熱膨張による影響を受けにくい設計が可能
- 交換部品の互換性が高く、メンテナンスがしやすい
👉 H7の穴を基準に設計することで、標準品の使用や部品交換が容易に!
標準規格で広く採用されている
H7はJISやISOなどの標準規格に採用されており、市販の部品との互換性が高いため、部品調達や設計の自由度が向上します。
✅ 標準部品(軸、ブッシュ、ベアリングなど)がH7に適合する設計になっている
✅ カタログ品の活用ができ、特注部品を減らせる
👉 H7を採用することで、汎用部品の利用が可能になり、コスト削減にも貢献!
H7は、軸との適切なはめあいが得られ、組立・メンテナンスがしやすく、標準規格に適合しているため、さまざまな機械設計で使いやすい公差です。
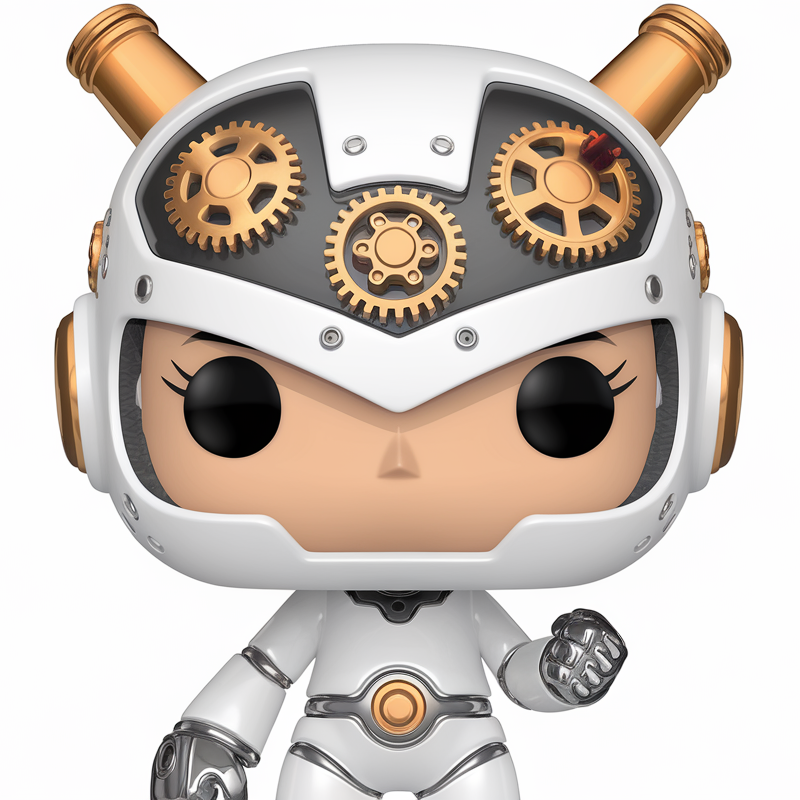
一般的な機能要件に幅広く対応できるはめあい公差として、多くの設計で採用されています。
豊富な標準部品の選択肢
機械設計において、穴のはめあいには H7 が広く採用されています。その理由の一つが、H7公差に対応した標準部品が豊富に揃っている ことです。標準部品の活用は、設計の自由度を高めるだけでなく、コスト削減や納期短縮にもつながります。
市販の軸・ベアリングがH7基準で作られている
H7は JIS(日本工業規格)やISO(国際規格) において、一般的な穴の公差 として定められています。そのため、多くのメーカーが H7に適合する軸やベアリング、ブッシュ を製造しています。
- H7の穴にピッタリ合う軸(h6、g6など)がすぐに手に入る
- ベアリングやブッシュの寸法設計がH7基準になっている
- 市販部品を組み合わせるだけで、スムーズなはめあいが実現
👉 特注加工をせずに、既存の部品を活用できる!
部品選定がしやすく、調達が簡単
機械設計では、できるだけ 標準品を活用すること が重要です。H7は、多くの標準部品に適合しているため、設計の手間を減らし、調達のしやすさを向上させます。
- 軸、ベアリング、ブッシュ、ギアなどのカタログ品がH7に対応
- 特注品を作る必要がなく、調達コストやリードタイムを削減
- すぐに交換・補修できるため、メンテナンス性も向上
👉 設計・製造・メンテナンスのすべての工程でメリットがある!
コスト削減と納期短縮が可能
標準部品を活用することで、コストと納期の両方を最適化 できます。
- 既製品を使うことで、特注加工のコストを削減
- 大量生産されている標準品は価格が安い
- すぐに入手できるため、納期が短縮される
👉 H7を採用することで、コストパフォーマンスの良い設計が可能!
H7公差の穴は、市販の軸やベアリング、ブッシュと適合するため、豊富な標準部品を選択できる という大きなメリットがあります。これにより、設計の自由度が向上し、コスト削減や納期短縮が可能 になります。
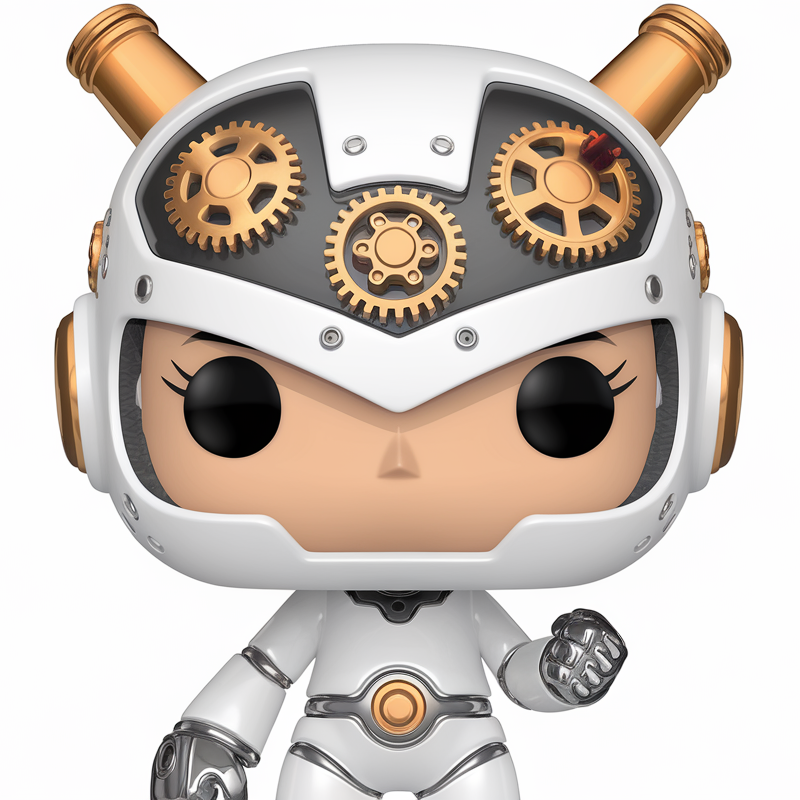
多くの機械設計において、H7が 最もバランスの取れたはめあい公差 として採用されています。
柔軟な組み合わせが可能
機械設計において、穴のはめあいにはH7が頻繁に使用される 理由の一つに、「柔軟な組み合わせが可能であること」が挙げられます。H7は 様々な軸公差と適合し、多様な用途に対応できる ため、設計の自由度が高まります。
多様な軸公差と組み合わせ可能
H7の穴は 適度な精度と加工容易性を兼ね備えた公差 であり、さまざまな軸公差と組み合わせることで、異なるはめあいを実現 できます。
✅ H7 – g6(すきまばめ):回転軸やスライド部品に最適
✅ H7 – m6(中間ばめ):軽い圧入や位置決めに適用可能
✅ H7 – p6(しまりばめ):しっかり固定する用途に対応
👉 軸側の公差を調整することで、用途に応じた最適なはめあいを選べる!
標準部品との適合性が高い
H7の穴は、市販の軸やベアリング、ブッシュなどの標準部品と適合しやすいため、特注加工なしで様々な部品を組み合わせることができます。
- ベアリングのハウジング部の穴寸法はH7が基本
- リニアブッシュやブッシュ類もH7基準で設計されている
- 既存の部品を柔軟に組み合わせて、最適な設計が可能
👉 H7を選ぶことで、部品の選定がスムーズになり、設計変更にも柔軟に対応できる!
設計の自由度が向上
H7を基準とすることで、設計時に以下のようなメリットが得られます。
✅ 設計段階で公差調整がしやすい → 軸側で微調整が可能
✅ 試作・変更が容易 → 公差の互換性が高いため、変更しても大きな問題が発生しにくい
✅ 異なる用途でも流用しやすい → 同じH7の穴を使い、用途ごとに適切な軸を選べばOK
👉 「設計の柔軟性」+「製造の効率化」=最適な公差選定!
H7の穴は 様々な軸公差と組み合わせることで、すきまばめ・中間ばめ・しまりばめを柔軟に選択できる ため、多くの設計に採用されています。
また、標準部品と適合しやすく、設計変更や流用が容易な点 も大きなメリットです。
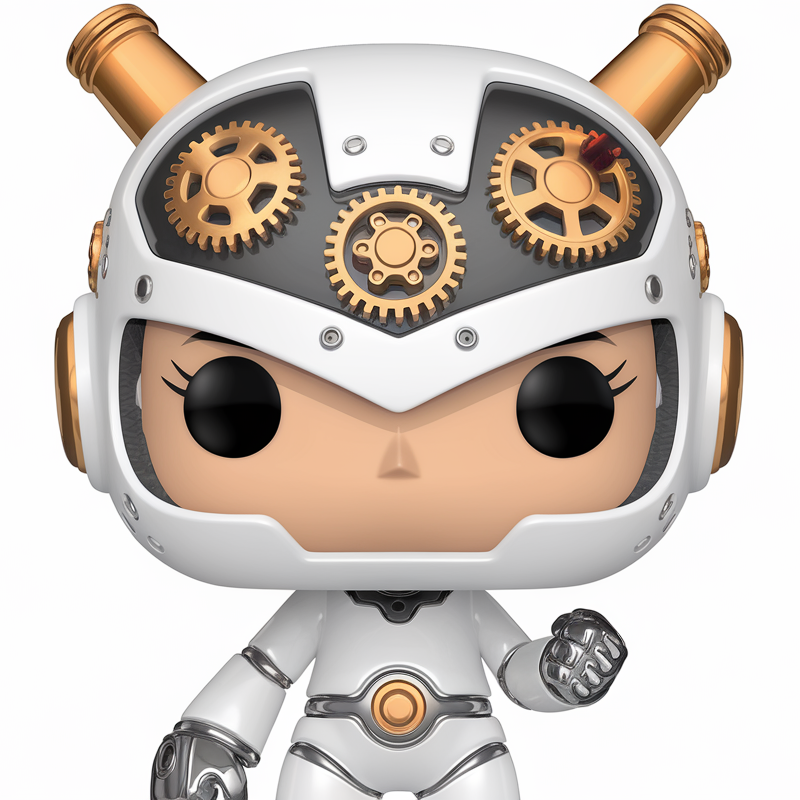
このように、H7は機械設計において「使いやすさ」と「柔軟性」を兼ね備えた最適なはめあい公差 なのです!
品質管理と再現性
機械設計において、穴のはめあいにH7がよく使われる 理由のひとつに、品質管理がしやすく、再現性が高い ことが挙げられます。H7を採用することで、寸法のばらつきを抑えながら安定した製造が可能 となり、設計・加工・組み立ての各工程での精度を確保できます。
国際規格に準拠している
H7は、ISO(国際標準化機構)やJIS(日本産業規格)などの公差規格で定められた一般的な公差 です。そのため、世界中のメーカーで 同じ基準の寸法精度 を保証でき、異なる工場や国で製造しても品質が一定 になります。
- ISO 286-1 / JIS B 0401 による標準化
- どのメーカーでも同じ基準で製造できる
- 異なる工場間での互換性が高い
👉 規格化された公差を使うことで、品質管理がしやすくなる!
寸法のばらつきを抑えやすい
H7の穴公差は ±0.01~0.035mm程度(穴の径による) で管理されており、加工の際に ばらつきを抑えながら安定した品質を確保できる のが特徴です。
- 一般的な加工機(ボール盤、フライス、旋盤)で高精度な仕上げが可能
- 測定しやすい寸法公差の範囲に収まる
- 同じ公差で加工すれば、異なる製造ロットでも精度を再現しやすい
👉 大量生産時でも寸法精度を安定させられる!
検査が容易で品質保証しやすい
H7の穴は、多くの測定工具(ゲージ、ノギス、マイクロメーター など)で 簡単に測定でき、合否判定がしやすい というメリットがあります。
- プラグゲージ(通り・止まりゲージ)で瞬時に検査可能
- ノギスや内側マイクロメーターでも測定しやすい
- 製品ごとの検査工程がシンプルになり、品質保証が容易
👉 検査工程がシンプルになり、トレーサビリティも向上!
組み立て時の互換性が高い
H7の穴を使うことで、製造ロットや部品メーカーが異なっても、問題なく組み立てが可能 になります。これは、品質の安定性だけでなく、部品の交換や修理のしやすさ にもつながります。
- 同じH7の穴なら、異なる工場の部品でも適合
- メンテナンス時の部品交換がスムーズにできる
- 長期にわたる再現性の確保が可能
👉 H7なら、長期間にわたって同じ品質の製品を維持できる!
H7の穴がよく使われる理由のひとつは、品質管理のしやすさと高い再現性 です。国際規格に準拠し、寸法のばらつきを抑えやすく、測定・検査も簡単 なので、大量生産時でも安定した品質を確保できます。また、異なる工場やロットでも同じ基準で製造できるため、組み立て時の互換性も高く、メンテナンスもしやすい のが大きなメリットです。
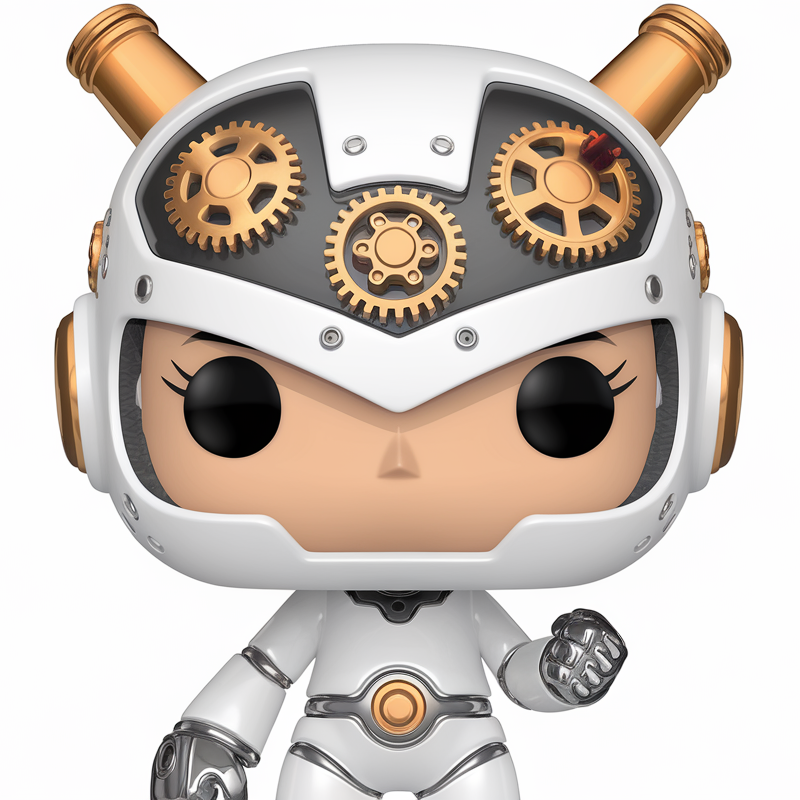
このように、H7は「高精度なはめあい」と「品質の安定性」を両立できる、公差設定の標準 なのです。
まとめ
H7公差は、機械設計においてコスト、機能、品質管理のバランスが優れた選択肢です。加工が容易で、標準的な市販部品と高い互換性があり、また軸公差との組み合わせで多様な用途に対応できるため、設計者にとって非常に汎用性の高い公差範囲です。設計における信頼性や効率を高めるためにも、H7公差は多くの機械設計で採用され続けています。
コメント