機械設計では、部品の形を考えるときに「どこから加工するか」がとても重要になります。
加工しやすい形状にすることで、コストや納期、品質に大きな差が出るからです。
特に意識したいのが、「片側(片面)から加工できる形状」にすること。
なぜ片側から加工できると良いのか?
逆に、両側や横方向から加工する形状だと何が問題なのか?
この記事では、段取り替えの手間や加工精度の観点から、
片面加工のメリットと設計の工夫について、初心者にもやさしく解説します!
加工は“ひとセット”で終わるのがベスト!
切削加工では、部品を工作機械に固定(セッティング)して加工を行います。
このセットした状態で、できるだけ多くの加工を一気に終わらせるのが理想です。
両面加工が必要になるとどうなる?
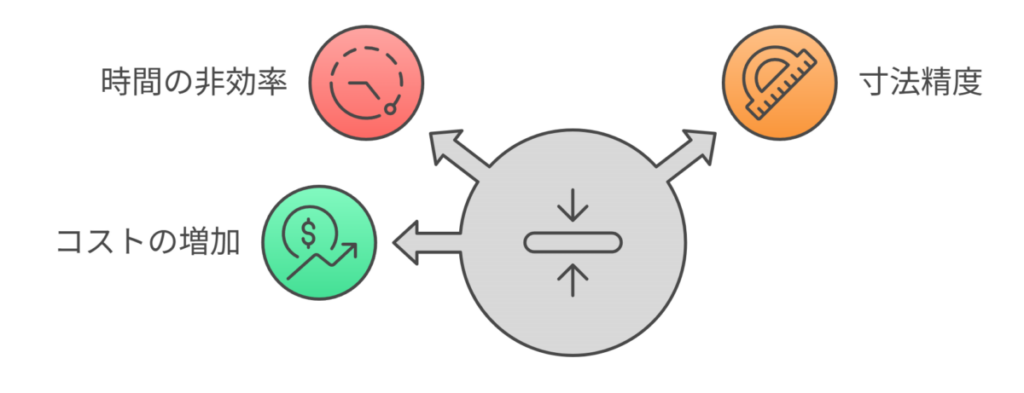
部品を裏返して再固定する必要が出てくると、以下のような問題が起きやすくなります。
🚫 段取り替えに時間がかかる(作業効率ダウン)
🚫 固定ミスで寸法ズレが出やすい
🚫 追加の治具や工具が必要でコストが上がる
【初心者向け】段取り替えが多いと、なぜ時間がかかるの?
機械設計では「加工がしやすい形状」を考えることがとても大切です。
その中でよく出てくるキーワードが「段取り替え」という言葉です。
「段取り替えって何?」「なんでそんなに時間がかかるの?」
そう感じた方に向けて、やさしく解説します!
「段取り替え」とは?
段取り替えとは、加工中の部品を加工機にセットし直す作業のことです。
🔍 例えば…
- 部品を裏返してもう一面を加工したい
- 横から穴を開けたいので横向きに固定し直したい
- 一部だけ別の工具や治具が必要になる
このようなときに、一度機械を止めて部品のセットをやり直す必要があります。
これが「段取り替え」です。
なぜ段取り替えに時間がかかるの?
部品を正確に再セットするのが難しい
裏返したとき、元の位置とピッタリ合わせるのが大変です。
ほんの0.1mmずれただけで、加工精度が落ちることもあります。
作業者の手作業が増える
段取り替えは自動ではできません。
作業者が一度部品を取り外し、向きを変えて、再度固定し直します。
段取りのたびに確認が必要
再セット後は、位置合わせや原点出しなどの確認が必要です。
これがまた、数分〜十数分のロスになります。
加工内容によっては治具や工具も交換
例えば側面加工をするためには専用の治具を使うこともあり、
段取りのたびに準備→固定→調整の流れが必要です。
段取り替えが多いとどうなる?
🚫 生産効率が悪くなる(=加工時間が長くなる)
🚫 手間が増えるため人件費・コストが上がる
🚫 セットミスによる不良品のリスクも上がる
設計者ができる工夫
- 片面から加工できる形状にする(裏返さない)
- 穴は貫通形状にして、両面加工を避ける
- 横穴などは別部品に分けて構成するのも手
- 加工部位は一方向からアクセスできるよう配置する
✅ 段取り替えとは「加工機への再セット」のこと
✅ 段取りが多いと、時間・コスト・精度すべてに影響する
✅ 設計段階で「段取りが少なく済む形状」にすると現場が楽になる!
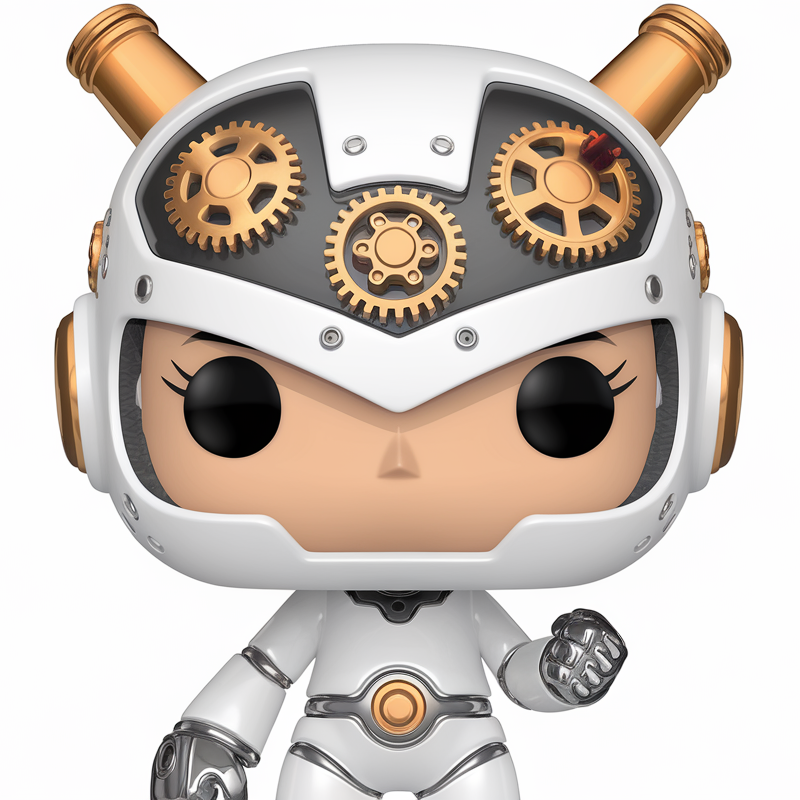
段取り替えを減らすことは、現場の効率と品質を上げるカギです。
「加工者の手間を減らす」という視点を持つと、
設計の質がグッと上がりますよ!
工夫ポイント:片面加工で完結させよう!
以下のような工夫をすると、片側からの加工で済む場合が増えます。
穴は可能な限り貫通穴にする
止まり穴(途中で止まる穴)よりも貫通穴の方が加工が簡単です。
両面から掘る必要もなく、バリ取りも楽になります。
横向きの穴や溝は避ける
横穴や側面溝は、加工機を横方向から当てる必要があり、追加段取りが必要になるケースが多いです。
全体を同じ面で加工できる形状にする
たとえば、部品の高さ方向にすべての加工要素(穴、溝、ポケット)が収まるように設計することで、裏返し不要な構造が実現できます。
どうしても裏面から座グリをしたいときの設計の工夫
機械設計では、「片側(片面)から加工できる形状が理想」とされています。
理由は、加工の段取り替えが不要になり、コストも精度も安定するからです。
しかし現実には、裏面からの座グリ(ザグリ)加工がどうしても必要になるケースもあります。
たとえば…
- ボルトの頭を裏面に隠したい
- 裏面からナットを沈めて固定したい
- 外観上、表面には穴を開けたくない
このような場合、裏面からの追加加工が避けられないことがあります。
裏面からの加工は「段取り替え」が必要
裏面に加工をするためには、加工途中でワークを裏返して再セット(段取り替え)する必要があります。
この作業が増えると、以下のようなデメリットがあります。
🚫 段取り時間が増えて、コストアップにつながる
🚫 位置決めの再現性が必要で、精度確保が難しい
🚫 反対面との位置ズレのリスクがある
工夫ポイント①:基準面をしっかり設ける
裏返しても確実に位置決めできる基準面や基準穴を設計に取り入れましょう。
これにより、再セット時のズレを最小限に抑えることができます。
工夫ポイント②:裏面座グリの公差を緩める
できるだけ裏面座グリの寸法公差を緩めに設定することで、加工精度のハードルを下げられます。
「一般公差」など、機能に支障のない範囲で許容値を広く設計することが大切です。
工夫ポイント③:干渉する相手部品に「逃がし」を設ける
裏面から座グリをする理由が「相手部品と干渉するから」である場合は、
相手側の部品に逃がし形状を設けて回避できないか検討するのもひとつの方法です。
たとえば、相手部品にボルト頭が収まる穴や溝を追加すれば、裏面からの座グリが不要になる場合もあります。
設計要求や機能上、どうしても裏面から座グリが必要になることもあります。
その場合でも、基準面を設けたり、公差を緩めたり、相手部品に逃がしを設けるなどの工夫により、
段取り替えによるリスクやコストを最小限に抑えることが可能です。
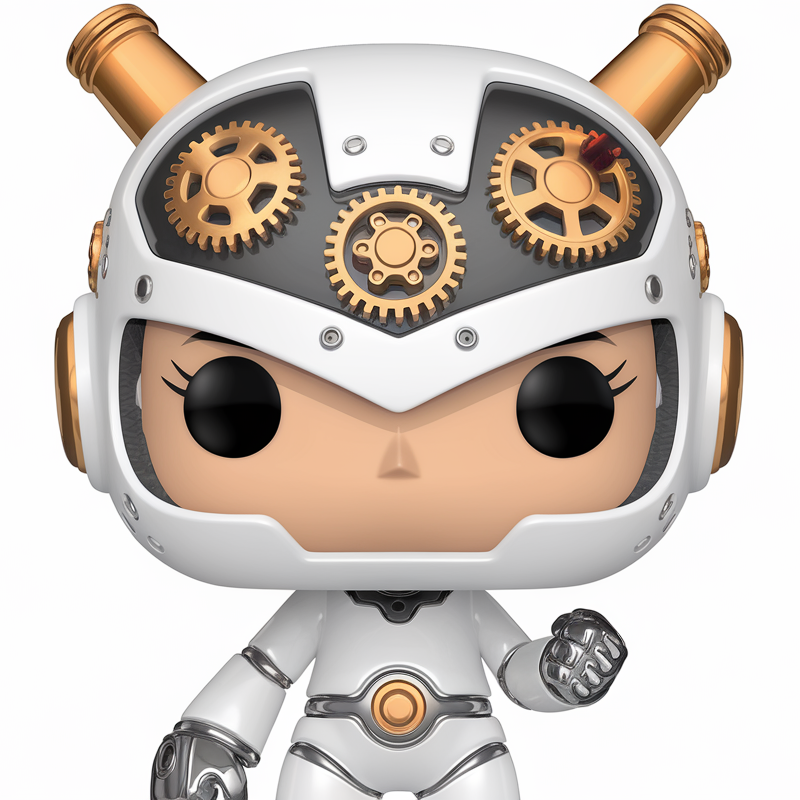
大切なのは、「裏面加工があるから仕方ない」で終わらせず、
製造現場にやさしい設計を常に意識することです。
設計時に意識するチェックポイント
- 裏返さずに、加工すべてが完了できるか?
- 加工面が1面で完結しているか?
- 加工の都合で、部品を複雑にしていないか?
まとめ
✔ 加工性を上げるには「片側から加工できる形状」にすることが基本
✔ 裏返しや段取り替えは、精度やコストのリスクを生む
✔ 穴は貫通、形状はシンプルを心がけると◎
設計者が少しだけ「加工の現場」を意識することで、
品質・コスト・納期のバランスがぐっと良くなります。
「作りやすい形にする」ことも、設計者の大切な仕事です!
コメント