研磨は、部品の仕上げ加工として、表面粗さや寸法精度を向上させるために重要な工程です。設計図面には、必要な研磨箇所や条件を適切に指示する必要があります。この記事では、研磨指示の基本的な内容やポイントを解説します。
研磨指示 “G” について
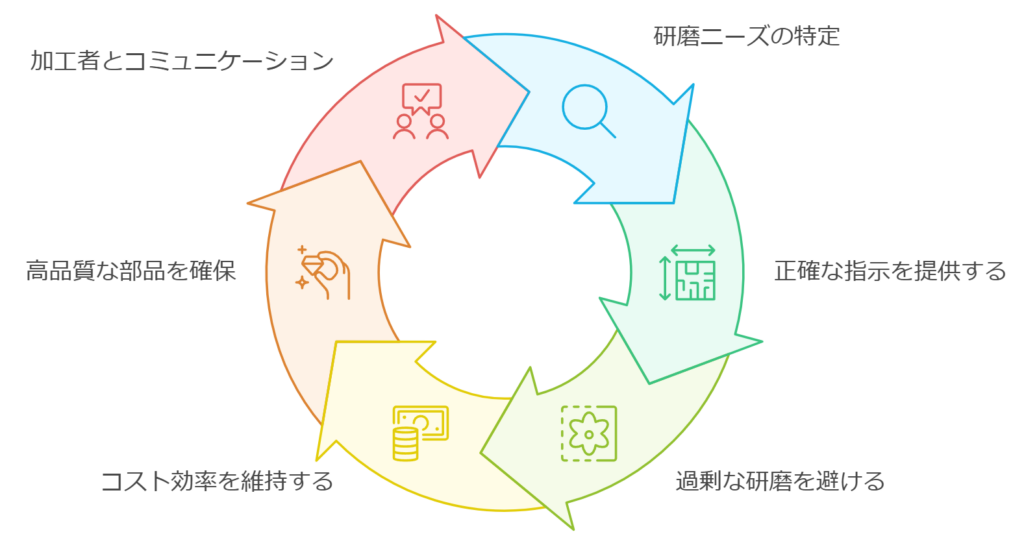
図面上で使用される「G」という研磨指示は、グラインディング(Grinding) を意味します。これは、部品の表面を精密に仕上げる加工方法であり、主に以下のような目的で使用されます。
- 寸法精度の向上
- 表面粗さの改善
- 組み付け時の摩擦や機械的な問題を防止する
以下では、「G」研磨指示の詳細な意味や図面における使い方、注意点について解説します。
図面上の「G」の記載方法
図面において「G」を用いた研磨指示を記載する際には、以下のように表記します。
例1: 指定箇所の表記
部品の上面に研磨加工を施す場合
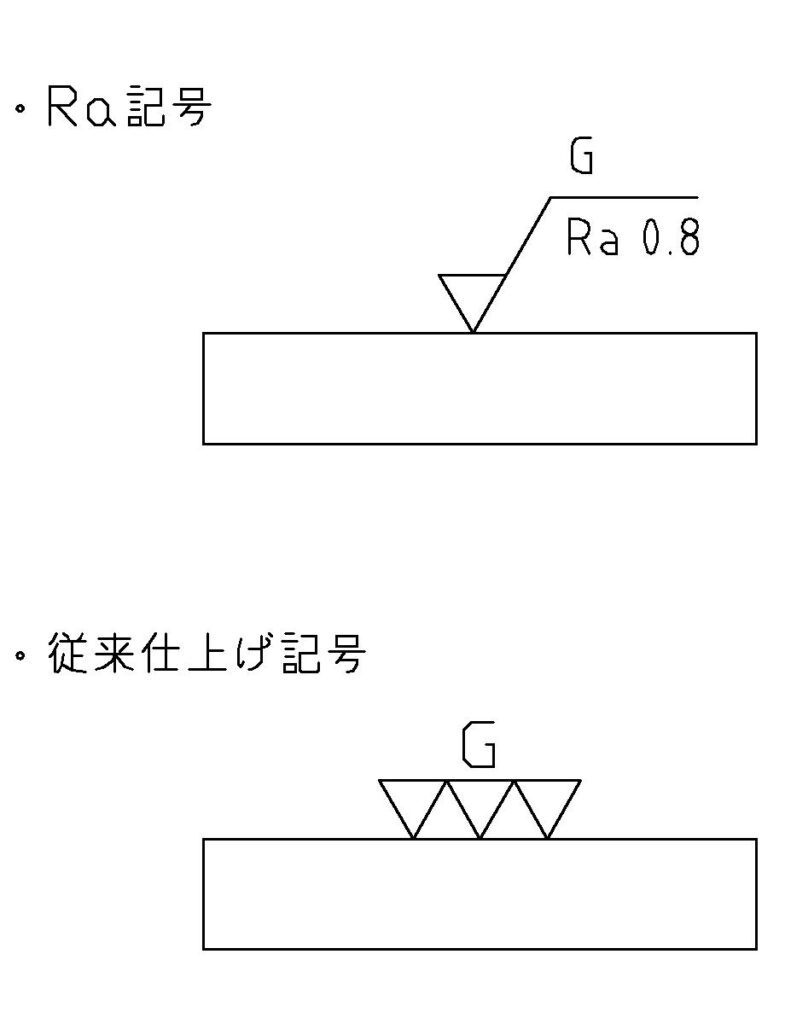
例2: 寸法公差との併記
軸の外径に研磨加工を施し、寸法公差を設定する場合
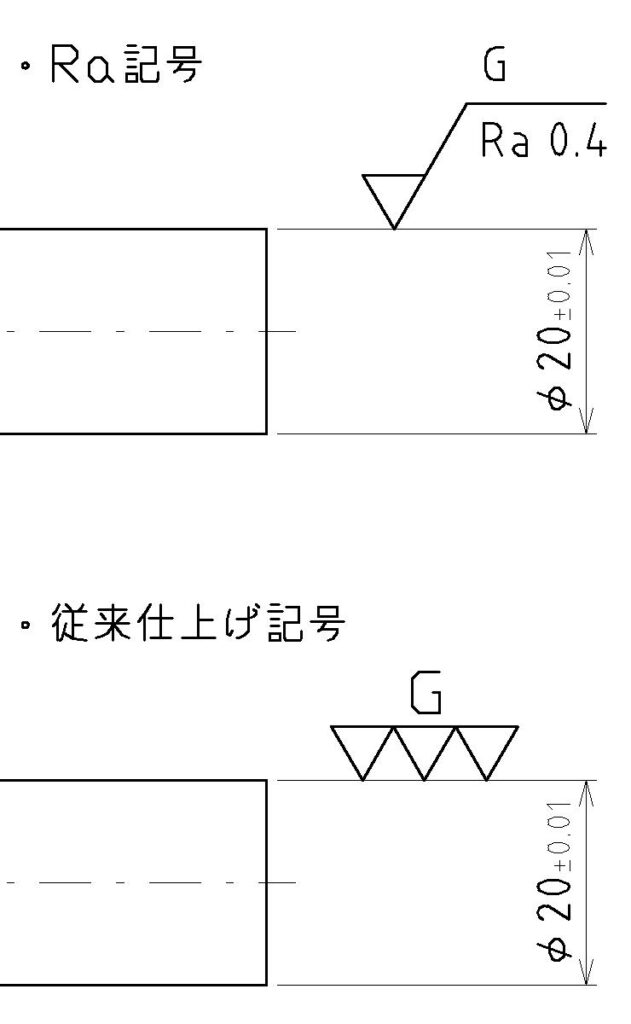
図面における研磨指示の基本
研磨指示を図面に明確に記載することで、加工者との認識齟齬を防ぎます。以下の項目を図面に盛り込むことが一般的です。
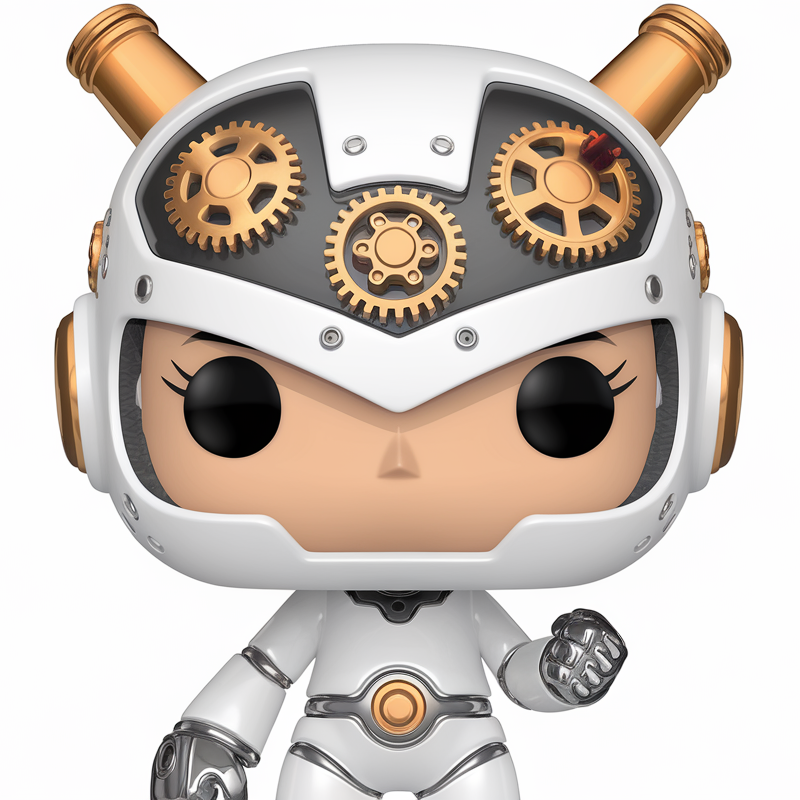
研磨指示の情報は加工者との認識が非常に重要となります。
コストがかかる加工となるため、注意事項や特記事項などあれば詳細に書きましょう。
会社ごとのルールや実績をもとに正しく伝わるように指示を書きましょう。
✅研磨箇所の明示
- 対象部品のどの面や部位を研磨するかを明確に記載。
- 例: 「上面を平面研磨」「内径を円筒研磨」
✅表面粗さ
- 必要な表面仕上げを数値で指示。
- 記号例: Ra0.8, Rz6.3など。
- 高精度な仕上げでは Ra0.2以下を指定する場合も。
✅寸法精度
- 研磨後の寸法公差を明記。
- 例: ϕ20±0.01mm
✅加工後の仕上げ方向
- 必要に応じて研磨の仕上げ方向(直線的、回転的)を指示。
✅特別な注意事項
- 熱処理後の研磨や、研磨後の熱影響の回避など。
研磨記号の使用
- JIS規格では、表面仕上げを示す記号が定義されています。
- 記号を用いて「この面を加工」や「仕上げを指定」することが可能。
図面での研磨指示の注意点
🚫過剰な指示を避ける
- 研磨指示が多すぎると加工コストが上がるため、必要最小限の箇所に留めます。
🚫表面粗さと寸法精度の整合性
- 表面粗さが極端に小さい場合、高精度な寸法加工が必要となり、加工難易度が上がります。
- 適切なバランスを考慮してください。
🚫後工程を考慮
- 研磨は最終仕上げとして指定されることが多いですが、後工程で溶接や組み立てがある場合、過剰な仕上げは無駄になる可能性があります。
研磨の種類とその特徴
代表的な研磨加工
✅平面研磨
- 平面部の仕上げ加工に使用。
- 表面精度が求められるプレートや治具でよく使用。
✅円筒研磨
- シャフトや穴の内周を精密に仕上げる加工。
- 軸受部やガイド部で用いられる。
✅鏡面研磨
- 表面粗さを極限まで減らし、鏡面状態に仕上げる加工。
- 光学機器や高精度部品で必要。
✅バフ研磨
- 見た目を美しくする装飾目的や軽い仕上げ加工で使用。
- ステンレスやアルミ部品の外観仕上げに利用。
✅ラッピング研磨
- 砥粒を含む研磨液を用いて、工作物とラップ盤を相対運動させることで表面を仕上げる加工方法。
- 摩擦による微細な削り出しで表面を加工するため、高い精度と滑らかな仕上がりが得られます。
研磨加工の推奨点
📌加工業者との確認を怠らない
図面だけでは伝わりきらない場合、事前に打ち合わせを行い、仕上げ基準を共有しましょう。
📌試作品段階で基準を明確化
初期段階で仕上げ基準を確認し、量産時に統一性を保つ。
📌検査基準の設定
表面粗さ計や三次元測定機を用いて、指示通りの仕上がりを検査します。
研磨のメリットと適用箇所
機械設計において、研磨は製品の品質向上に大きく寄与する工程です。研磨は、材料表面の平滑化や仕上げを目的とし、性能や外観の向上を図ります。本項では、研磨のメリットと具体的な適用箇所について解説します。
研磨とは
研磨とは、砥石や研磨紙、特殊な研磨液を使用して、材料表面を削り取ったり磨いたりすることで、所望の表面状態を得る工程です。研磨の目的は、次の2つに大別されます:
▶ 機能的な目的: 部品の摩擦低減や密封性向上など。
▶ 外観的な目的: 見た目の美しさや表面の均一性を確保。
研磨のメリット
✅表面の平滑化
- 材料表面の凹凸を減らすことで、摩擦抵抗や表面疲労を低減します。
- 特に回転部品や摺動部品では寿命の向上に寄与します。
✅寸法精度の向上
- 研磨により高精度な寸法調整が可能です。
- これにより、厳密なはめあいや位置決めが求められる部品での使用が可能になります。
✅耐食性の向上
- 表面を滑らかにすることで腐食を発生させる原因となる微細な凹凸を除去し耐食性を向上させます。
- 特にステンレス材料で効果的です。
✅外観の改善
- 表面を鏡面仕上げにすることで、美しい外観が得られます。
- 特に装飾的な部品や食品機械などでは重要な要素です。
✅機能性向上
- 表面粗さを低減することで、密封性や熱伝導性を向上させ、製品性能の向上に繋がります。
材料研磨の適用箇所
📌摺動部品
🔍例:軸受け、スライドレール
- 表面粗さを低減することで摩擦を減らし、スムーズな動きを実現します。
📌シール面
🔍例:シャフトとシールの接触部
- 密封性を向上させ、漏れを防止します。
📌精密機械部品
🔍例:歯車、シャフト(回転軸)
- 寸法精度や表面粗さの改善により、性能を最大化します。
📌装飾部品
🔍例:ステンレスパネル、アルミフレーム
- 美しい外観を求められる部品に適用されます。
📌耐腐食部品
🔍例:食品機械、医療機器
- 耐腐食性を向上させるため、ステンレス部品に研磨を施すことが多いです。
研磨の注意点
🚫過剰な研磨による強度低下
材料の表面を削りすぎると、製品の耐久性に影響する可能性があります。
🚫コストと時間の増加
高精度の研磨には手間がかかるため、必要以上の研磨はコスト増に繋がります。
🚫適切な仕上げの選択
用途に応じて粗研磨と仕上げ研磨を使い分けることが重要です。
研磨は、機能性向上と外観改善の両面で機械設計において欠かせない工程です。適切な研磨を行うことで、部品性能の向上や製品寿命の延長が可能となります。用途に応じた適用箇所や研磨条件を考慮し、効率的かつ効果的な設計を目指しましょう。
まとめ
研磨指示は部品の性能や外観、耐久性を左右する重要な要素です。必要箇所に的確な指示を行い、過剰な研磨を避けることでコストを抑えつつ高品質な部品を設計することが可能です。正確な図面作成と、加工者とのコミュニケーションが成功の鍵となります。
コメント