機械設計において、形状公差は部品の形状が理想的な形状からどれだけズレを許容するかを規定する重要な要素です。部品の精度を高め、機能性や組み立て性を保証するためには、形状公差の適切な設定が不可欠です。ここでは、代表的な形状公差である「直線度」「平面度」「真円度」「円筒度」について、図面指示方法を具体的な数値を使いながら解説します。
形状公差とは?
形状公差は、部品の基本形状を規定するための幾何公差で、他の部品や基準に依存しない、単体の部品の形状を管理します。主な形状公差には以下があります。
✅直線度:直線がどれだけ真っ直ぐであるか。
✅平面度:平面がどれだけ平らであるか。
✅円の真円度:円がどれだけ完全な円形であるか。
✅円筒度:円筒がどれだけ完全な円筒形をしているか。
これらは、部品が設計通りの機能を果たすために必要な形状を保証します。
直線度(Straightness)
直線度は、部品の特定の線がどれだけ理想的な直線からズレているかを示す形状公差です。
特に軸やガイドレールなど、精度が求められる部品に設定されます。
🔍例: 直径20mm、長さ100mmのシャフトがある場合、直線度公差0.01mmが設定されたとします。
シャフトの軸線は長さ100mmに対して、0.01mm以内の誤差で直線であることが求められます。
📌測定方法
シャフトを固定し、表面に設置したダイヤルゲージまっすぐに移動させて軸線のズレを測定します。
誤差が0.01mm以下であれば、直線度が満たされていることになります。

平面度(Flatness)
平面度は、ある面が理想的な平面からどれだけズレているかを示す形状公差です。
ベースプレートや接触面などに使用され、部品の安定した設置や他部品との密着性を保証します。
🔍例: 100mm × 50mmのプレートに対して、平面度公差0.05mmが設定されたとします。
プレートの表面は、理想的な平面から上下0.05mm以内の範囲で凹凸が許容されます。
📌測定方法
平面度を測定する際には、3次元測定機やダイヤルゲージを使用して、全体の高さの変動を確認します。
測定範囲内に収まっているかどうかで合否が判断されます。

真円度(Roundness)
真円度は、円形の断面が理想的な円形からどれだけズレているかを示す形状公差です。
回転体や軸受けの設計において重要な公差であり、滑らかで正確な回転動作を保証するために設定されます。
🔍例: 直径25mmの円筒形部品の真円度公差が0.01mmと指定されている場合。
この場合、円筒の断面は、理想的な円から半径方向に±0.01mm以内のズレであることが求められます。
📌測定方法
部品を回転させてダイヤルゲージで表面を測定し、ズレが0.01mm以内かどうかを確認します。

4. 円筒度(Cylindricity)
円筒度は、部品の円筒形状が理想的な円筒からどれだけズレているかを示す公差です。
軸やベアリングなど、回転運動が関わる部品の精度管理において重要です。
🔍例: 直径30mm、長さ1000mmの円筒形シャフトに対して、円筒度公差0.05mmが設定された場合。
円筒の外周は、理想的な円筒形から半径方向に±0.05mm以内のズレであることが求められます。
📌測定方法
3次元測定機や専用の測定器を用いて、シャフト全体の表面のズレを確認します。
表面が理想的な円筒形からどれだけ外れているかを計測し、0.05mm以内であれば合格となります。

真円度と円筒度の違い
真円度と円筒度は、どちらも円形や円筒形の部品の精度を測定する形状公差ですが、対象とする部分や評価する範囲に違いがあります。
以下では、真円度と円筒度の違いについて詳しく説明します。
真円度(Roundness)
✅真円度は、円形の断面が理想的な円形からどれだけズレているかを評価します。
✅つまり、ある断面における円の形状がどれだけ正確であるかを確認するものです。
✅真円度は円筒形状の軸やボア(穴)などの断面に対して設定されます。
円筒度(Cylindricity)
✅円筒度は、部品全体が理想的な円筒形からどれだけズレているかを評価します。
✅部品の全長にわたる外周や内径のズレを測定し、部品全体が均一な円筒形状であるかどうかを確認するための公差です。
✅円筒度は真円度と異なり、部品全体に対しての形状を評価します。
真円度と円筒度の比較まとめ
項目 | 真円度 | 円筒度 |
---|---|---|
評価範囲 | 特定の断面のみ | 部品全体の円筒形状 |
対象部位 | 部品の任意の断面の円 | 部品全体の外周または内径 |
主な使用場面 | 回転体の断面精度確認や軸の精度評価 | 軸や穴の全体的な円筒形状の精度評価 |
測定方法 | 断面の形状をダイヤルゲージなどで測定 | 3次元測定機などを使用して全体を測定 |
形状公差の精度が悪いと起こり得る不具合
幾何公差は、製品や部品の形状や寸法の精度を規定する設計上の重要な要素です。その中でも形状公差は、部品の幾何学的な形状そのものの正確さを管理するために使用されます。
形状公差の精度が悪い、または適切に管理されていない場合、製品や部品の機能や信頼性に重大な影響を及ぼす可能性があります。
本項では、形状公差が不適切な場合に起こり得る不具合と、それを防ぐ方法について解説します。
形状公差の精度が悪いと起こり得る不具合
🚫 組み立て不良
形状の誤差により、部品が正確にフィットせず、組み立てが困難になる。
🔍例
- 直線度の不良により、シャフトが穴にうまく挿入できない。
- 平面度の不良により、取り付け面が傾き、ねじれや隙間が生じる。
🚫 動作の不良
可動部品の場合、形状の不正確さが運動性能に悪影響を及ぼします。
🔍例
- 円筒度が悪いローラーは、回転時に振動や騒音を引き起こす。
- 真円度が悪いピストンは、シリンダー内で摩擦や漏れを引き起こす。
🚫 例摩耗や損傷の増加
形状公差の不良は、部品の接触面積や圧力分布を変化させ、摩耗や損傷を早めます。
🔍例
- 平面度が不良な部品が他の部品と接触すると、部分的な圧力集中が発生し、摩耗が進行する。
🚫 シール性能の低下
シール部品が形状公差により正確に接触できない場合、漏れが発生します。
🔍例
- Oリングやガスケットが不適切な面に接触し、液体やガスが漏れる。
🚫 外観品質の低下
製品の形状が不正確だと、外観上の品質が損なわれ、市場での評価が低下します。
🔍例
- 真円度の悪い部品が目視で歪んで見える。
🚫 精度や測定結果の不一致
形状公差が設計意図と異なると、測定基準がずれ、製造工程全体に悪影響を及ぼします。
🔍例
- 平面度の不良で治具が不安定になり、測定値が正確でなくなる。
形状公差の不具合の原因
形状公差が悪い精度で製造される原因には、以下が挙げられます。
⛔ 加工精度の不足:工作機械や工具の劣化。
⛔ 設計ミス:現実的でない形状公差の指定。
⛔ 材料の変形:加工後の熱膨張や応力による変形。
⛔ 検査不足:製造工程での形状検査が不十分。
形状公差を守るための対策
✅設計段階での適切な公差設定
- 公差値は必要最低限に設定し、コストと加工可能性のバランスを取る。
- 設計意図を正確に製造者へ伝えるため、図面に明確な公差を記載する。
✅加工精度の向上
- 高精度な工作機械や加工工具を選定する。
- 加工後の残留応力を最小限にする熱処理や応力除去を行う。
✅測定と品質管理
- 三次元測定機や表面粗さ測定器など、適切な検査機器を使用する。
- 定期的な検査と工程管理を徹底する。
✅製造プロセスの見直し
- 部品の形状精度を保証するために、治具やクランプの配置を工夫する。
- 成形後に機械加工を追加し、最終形状を整える。
形状公差の不良が与える実例
搬送装置のガイドレール
産業用コンベアや搬送装置のガイドレールは、直線度や平面度が重要です。
形状公差が悪い場合、以下のような問題が発生します。
🚫不具合
搬送されるワークがレールに引っかかり、スムーズに移動できない。
📌影響
搬送の遅延や生産ラインの停止が発生し、生産効率が低下する。
🔍対策
ガイドレールの加工精度を高め、精密な測定で直線度を確認する。
ロボットアームの取り付け部品
産業用ロボットの関節部分や取り付け部品では、平面度や真円度が重要です。
形状公差が悪いと以下のような問題が起こります:
🚫不具合
取り付け部の傾きや歪みにより、ロボットアームの動作が不正確になる。
📌影響
位置決め精度が低下し、加工や組み立て工程でのミスが増える。
🔍対策
加工後の形状検査を徹底し、必要に応じて仕上げ加工を追加する。
形状公差の精度が悪い場合、組み立てや動作不良、摩耗の増加、外観品質の低下など、製品全体の性能や信頼性に悪影響を及ぼします。これを防ぐためには、設計段階での適切な公差設定と加工精度の向上、そして検査の徹底が必要です。
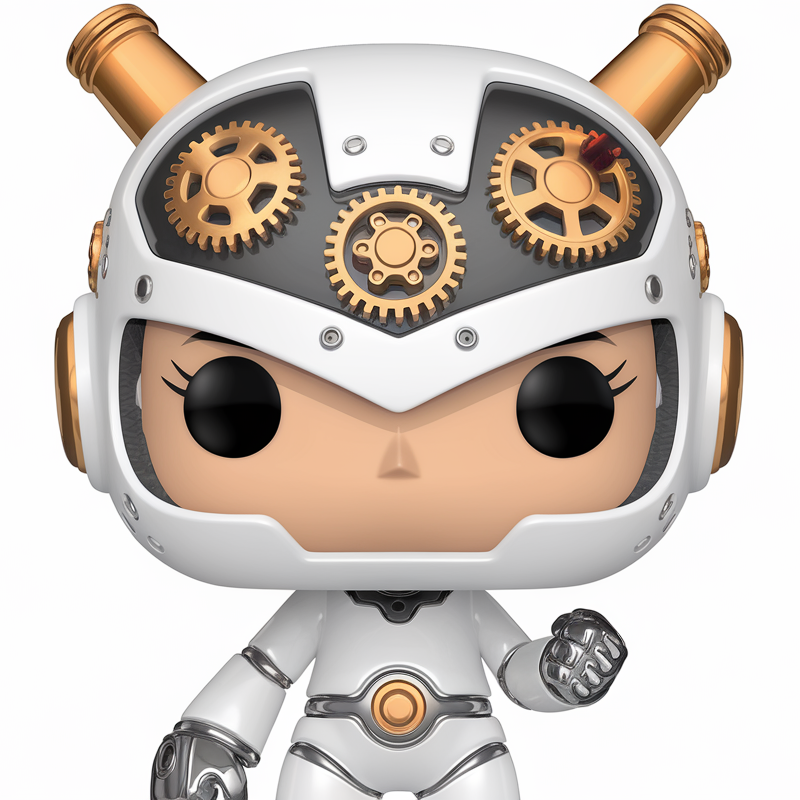
形状公差を適切に管理することで、製品品質の向上とコスト削減を両立させることができます。
まとめ
機械設計における形状公差は、部品の製作精度を保証するための非常に重要な要素です。形状公差を適切に設定することで、機械部品同士が正確に組み合わさり、スムーズな動作や長寿命を実現します。直線度、平面度、真円度、円筒度といった各種公差は、それぞれが異なる形状の誤差を評価するものであり、設計者が意図する製品の機能や品質を維持するための基準となります。
形状公差は、機械の精度や性能を直接的に左右するため、特に重要な設計要素です。真円度と円筒度の違いに見られるように、適用範囲や評価方法が異なるため、設計段階での適切な判断が必要となります。さらに、公差の設定によって加工コストや生産性にも大きな影響を与えるため、過剰な精度要求を避けつつ、必要な精度を確保することがコストパフォーマンスの最適化にもつながります。
コメント