機械設計において、公差とはめあいを適切に設定することは、製品の性能や寿命に大きく影響します。ただし、公差とはめあいの設計には多くの注意点があり、それを無視すると思わぬ問題を引き起こすことがあります。本記事では、「温度変化による影響」、「加工法の制約」、「製造と検査のコスト」という3つの観点から、公差設計時の注意点について詳しく解説します。
温度変化による影響
温度の変化による材料の膨張と収縮
すべての材料は、温度が上昇すると膨張し、下降すると収縮します。この性質を考慮しないと、以下のような問題が発生する可能性があります。
🚫嵌合の変化
- 熱膨張によって部品間のすきまが狭くなり、動作不良や過大な応力が発生する。
🚫動作の不安定化
- 極端な温度環境では、設計上の意図から外れた寸法変化が生じる。
🔍具体例
- 高温環境下で使用されるシャフトとベアリングのすきまばめでは、シャフトが膨張してベアリング内で固着するリスクがある。
- 金属部品と樹脂部品を組み合わせた場合、異なる膨張率による歪みや隙間が生じる。
対策
✅使用環境の温度範囲を考慮して、公差やはめあいを設定する。
✅温度変化に強い材料や、熱膨張率の低い材料を選択する。
✅部品の動作をシミュレーションし、温度変化を反映した設計を行う。
熱膨張率が高いプラスチックにおける公差設定のポイント
プラスチック材料は、軽量で加工性に優れる一方、金属に比べて熱膨張率が高い特性があります。この特性を考慮せずに公差を設定すると、温度変化による寸法変化が製品の性能に影響を与える可能性があります。本項では、熱膨張率が高いプラスチックを使用する際の公差設定の注意点とポイントについて解説します。
📌プラスチックの熱膨張率の特性
プラスチックは金属と比べて熱膨張率が数倍から数十倍になることが一般的です。
以下の例で比較してみましょう。
✅金属(SS400)
- 熱膨張率 約11.7 × 10⁻⁶/℃
✅プラスチック(POM、ポリアセタール)
- 熱膨張率 約100 × 10⁻⁶/℃
この差により同じ温度変化があった場合、樹脂部品は金属部品よりも大きく膨張または収縮します。
公差設定における温度変化の考慮
🔍使用環境の温度範囲を把握する
プラスチック部品の寸法は、環境温度が変化するたびに影響を受けます。そのため、以下のように使用環境を分析することが重要です。
📌使用する機械や装置の通常動作温度(例:20~60°C)。
📌保管中や輸送中に予想される極端な温度範囲(例:-20~80°C)。
🔍許容できる寸法変化の計算
熱膨張による寸法変化を事前に計算し、その範囲内で機能を維持できる公差を設定します。
計算式は以下の通りです。
\( \displaystyle ΔL=α⋅L0⋅ΔT\)
- ΔL:変化する長さ(膨張量)
- α:線膨張係数(単位:1/°C または 1/K)
- L₀:元の長さ(膨張前の長さ)
- ΔT:温度変化(最初の温度と最終温度の差)
▼例:100mmのPOM部品が40°C温度上昇する場合
\( \displaystyle ΔL=100×10^-6⋅100⋅40\)
\( \displaystyle ΔL=0.4mm\)
この場合、温度変化による寸法増加が0.4mmとなり、公差設定に影響を与えます。
組み合わせ部品との適合性
✅動作する部品とのはめあいの緩衝
プラスチック部品と金属部品を組み合わせる場合、温度変化により膨張率の違いが顕著に現れるため、次のような工夫が必要です。
- クリアランスの調整:嵌合部に余裕を持たせる設計。
- フローティング構造:寸法変化を吸収するための可動性を持たせる。
✅固定部分の変形防止
熱膨張による応力集中を防ぐために、以下の工夫が有効です。
- スリットやリブを追加して、熱膨張による変形を分散。
- クランプ位置を限定して、膨張方向を制御。
公差設定とコストのバランス
プラスチック部品では、熱膨張を考慮した公差設定が必要ですが、厳しすぎる公差は製造コストを大幅に上昇させます。そのため、以下のポイントを意識してバランスを取ることが重要です。
- 精度が重要な部分(嵌合部や動作に影響する部分)にのみ厳しい公差を適用。
- 他の部分では緩やかな公差を設定し、コストを削減。
- 必要に応じて、材料選定段階で熱膨張率の低いエンジニアリングプラスチック(例:PEEKやPPS)を採用する。
熱膨張対策の具体例
- 歯車の設計
- 熱膨張率の高いプラスチック製歯車では、バックラッシュ(歯車間の隙間)を適切に設定して、動作不良を防止します。
- スライドガイド
- 摺動部にクリアランスを設けることで、熱膨張による摩擦増加を回避します。
- 筒形部品の固定
- プラスチックの内径や外径が膨張しても機能を維持できる設計を採用します。
熱膨張率が高いプラスチック部品を設計する際は、使用環境の温度変化と材料特性を考慮して公差を設定することが不可欠です。
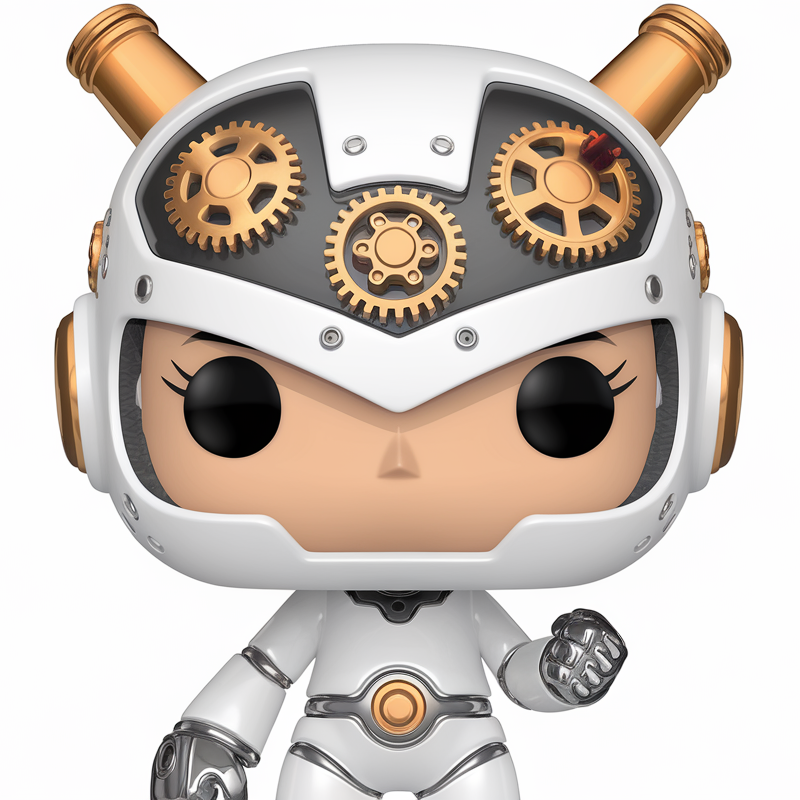
温度変化による寸法変化を計算し、組み合わせ部品との適合性やコストとのバランスを取りながら設計を進めましょう。
これにより、プラスチックの利点を最大限に活用しながら、信頼性の高い製品を実現できます。
加工法の制約
加工方法による公差の実現可能性
製造する部品の形状や公差は、選択した加工方法によって制約を受けます。たとえば、以下のような特性があります。
- 切削加工
- 高精度な寸法が可能だが、加工コストが高い。
- 研削加工
- ミクロン単位の精度が必要な場合に適用。ただし、生産速度が遅くなる。
- 成形加工(プレスや鋳造など)
- 低コストで大量生産可能だが、公差が大きくなる傾向がある。
🔍具体例
- プラスチック成形品は収縮が発生しやすく、正確な寸法を出すのが難しい。
- 切削加工で非常に厳しい公差を指定すると、加工時間が増え、コストが急増する。
対策
✅使用する加工方法に適した公差を設定する。
✅精度が必要な箇所だけに厳しい公差を適用し、それ以外は緩める。
✅初期試作で実際の加工限界を確認し、設計にフィードバックする。
製造と検査のコスト
厳しい公差がもたらすコスト増加
公差が厳しいほど、加工工程が増え、検査にも手間がかかります。以下の問題が発生することがあります。
▶ 高精度な加工には、専用の高価な設備や工具が必要。
▶ 検査において、すべての部品を詳細に確認する時間とコストがかかる。
▶ 廃棄率の増加:厳しい公差を達成できない部品が多くなる可能性。
🔍具体例
- ±0.01mmの公差が必要な部品を大量生産する場合、特殊な加工機械が必要となり、コストが著しく上がる。
- 高精度を要求する製品では、三次元測定機を用いた検査が必要になるため、検査コストが増加。
対策
✅設計時に、部品ごとの機能と必要な精度を明確化する。
✅部品全体ではなく、重要な部分にのみ厳しい公差を設定する。
✅実績のある加工業者と相談し、コストと精度の最適なバランスを見つける。
部品の形状や公差は加工方法による制約を受けるため、適切な選定が重要です。例えば、切削加工は高精度だがコストが高く、成形加工は低コストだが公差が大きくなるといった特性があります。そのため、必要な精度に応じた加工方法の選択が求められます。
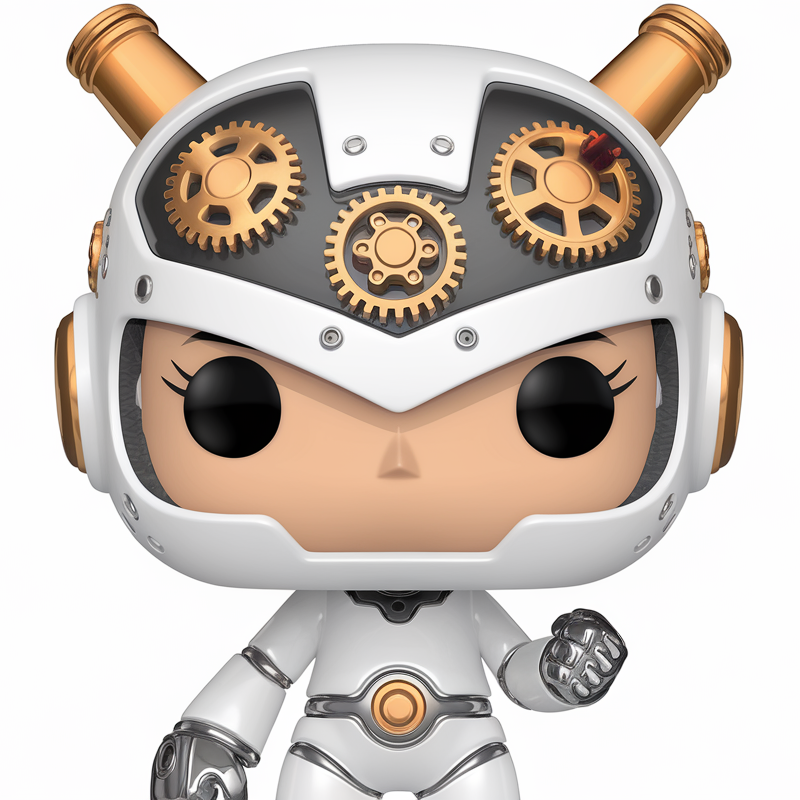
公差が厳しくなると加工・検査のコストが増加し、廃棄率も上昇するため、重要な部分のみに厳しい公差を設定することが有効です。
設計段階で加工業者と相談し、コストと精度の最適なバランスを見極めることが、効率的な製造につながります。
まとめ
公差とはめあいの設計では、温度変化、加工法、コストの3つの要因を慎重に考慮する必要があります。これらを無視すると、部品の機能不良や大幅なコスト増加につながります。設計者は、部品の使用環境や製造条件を正確に把握し、最適な公差とはめあいを設定することで、信頼性が高くコスト効率の良い製品を実現できます。
コメント