L型ブラケットは、部品の取り付けや構造体の補強に使われる「L字型の支持金具」です。
その製作方法によって、強度・コスト・加工性に大きな違いがあります。
本記事では代表的な5つの製作方法を紹介し、それぞれのメリット・デメリット・注意点を初心者でもわかるように解説します。
✅ 溶接で作成
✅ 曲げ加工で作成
✅ 削り出し加工で作成(切削)
✅ 山形鋼(アングル)で作成
✅ ボルト締結で作成(部品を組み立て)
溶接で製作
▶ 特徴
L字に切り出した2枚の鋼板などを溶接で接合して作る方法です。
✅ メリット
- 強度が高く、がっちり固定できる
- 大型・重量物にも対応しやすい
- 材料の制約が少ない
🚫 デメリット
- 歪みや変形が出やすい(特に薄板)
- 美観が悪くなりがち(研磨が必要な場合も)
- 作業者の技術が必要
- コストや工数がやや高め
溶接でL型ブラケットを製作する際の注意点とは?
L型ブラケットを溶接で製作する方法は、高い強度を確保できるため、多くの機械構造物や装置フレームなどに使われます。
しかし、正確な直角や十分な強度が必要な場合は注意が必要です。
本項では、設計段階で必ず押さえておきたい「溶接製作時の注意点」を、わかりやすく解説します。
注意点①:直角度が必要な場合は追加工を前提とする
✅ 溶接だけでは「直角精度」が出にくい!
溶接では、熱による歪みがどうしても発生し、
L字の角度(90°)が微妙にずれることがあります。
🔍 たとえば…
- 加工前は90°だったが、溶接後に91°になっていた
- 溶接部が引っ張られて「ハの字」になってしまった
✅ 設計上の対策
✔ 追加工(フライス・研磨)を前提に設計する
👉 溶接後に基準面を仕上げる加工代を残しておく
✔ 直角度が重要な面には基準マークや注記を入れる
🔍例:「溶接後、B面90°±0.1加工仕上げ」
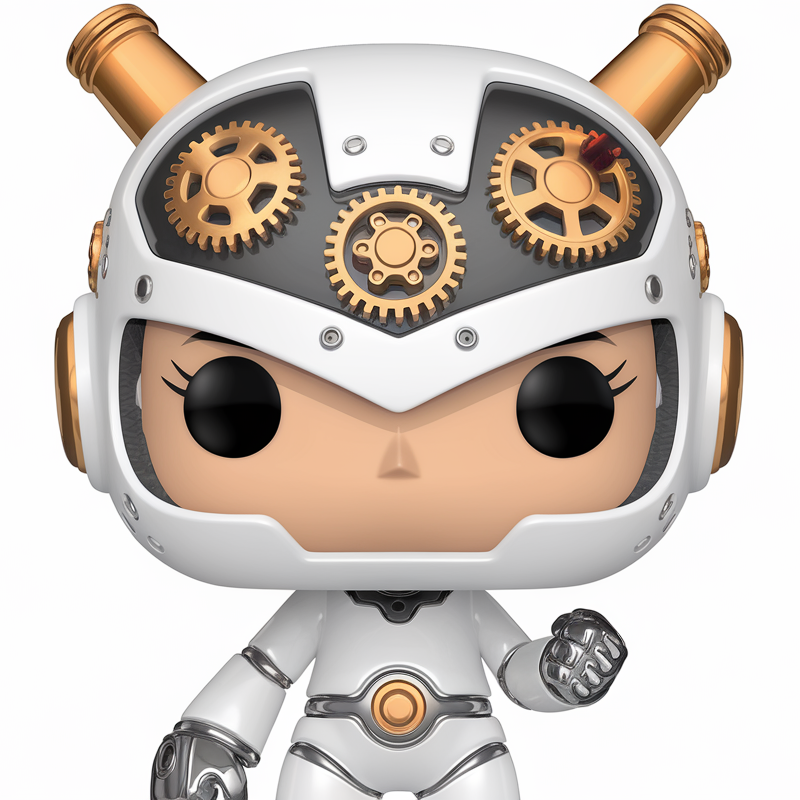
直角が重要なブラケットほど、溶接後の追加工を想定した設計が必要です!
注意点②:必要強度に応じて溶接指示を正しく行う
✅ 強度不足は事故のもと!
溶接と一口に言っても、溶接方法・ビードの長さや形状によって、
得られる強度は大きく変わります。
🚫 強度が不足すると…
- 応力集中部からクラックや破断が発生
- 荷重を支えきれず変形・脱落する危険性も
✅ 設計上の対策
✔ 使用条件に応じて溶接方法を指定する
🔍例:アーク溶接/TIG溶接など
✔ 必要に応じてJIS溶接記号や指示を図面に明記
🔍例:全周溶接、長さ〇〇mmの断続溶接など
✔ 荷重方向を考慮した接合部の配置
必要に応じてリブ(補強)を追加する
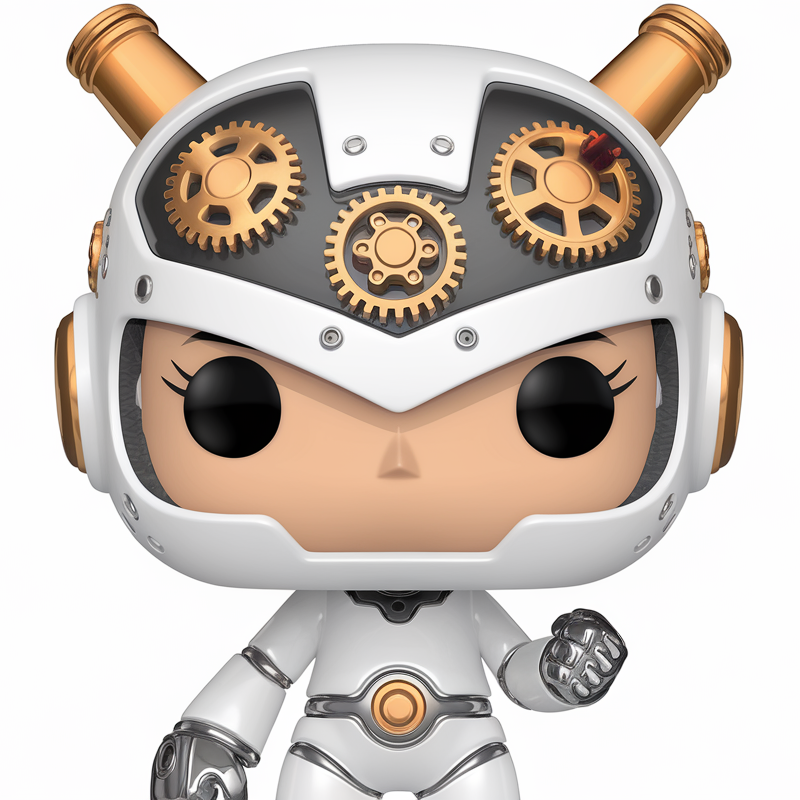
「見た目がくっついていればOK」ではなく、必要な荷重条件をクリアできる溶接条件を設計段階で明確にしておきましょう。
設計者として意識したいこと
チェック項目 | 内容 |
---|---|
直角精度が必要か? | 必要なら溶接後の追加加工を想定 |
加工代を設計に盛り込んでいるか? | 溶接歪み対策のための「余裕寸法」が設計にあるか |
溶接指示は図面に明記しているか? | 強度に関わる溶接の種類・範囲・形状を指示しているか |
荷重方向は考慮されているか? | 溶接部が主要荷重に耐えられる構造になっているか |
溶接でL型ブラケットを製作する際には、「精度」と「強度」の2つの観点から注意が必要です。
✅ 直角度が必要な場合は追加工を前提とした設計にする
✅ 必要な強度が出るように溶接方法・範囲を的確に指示する
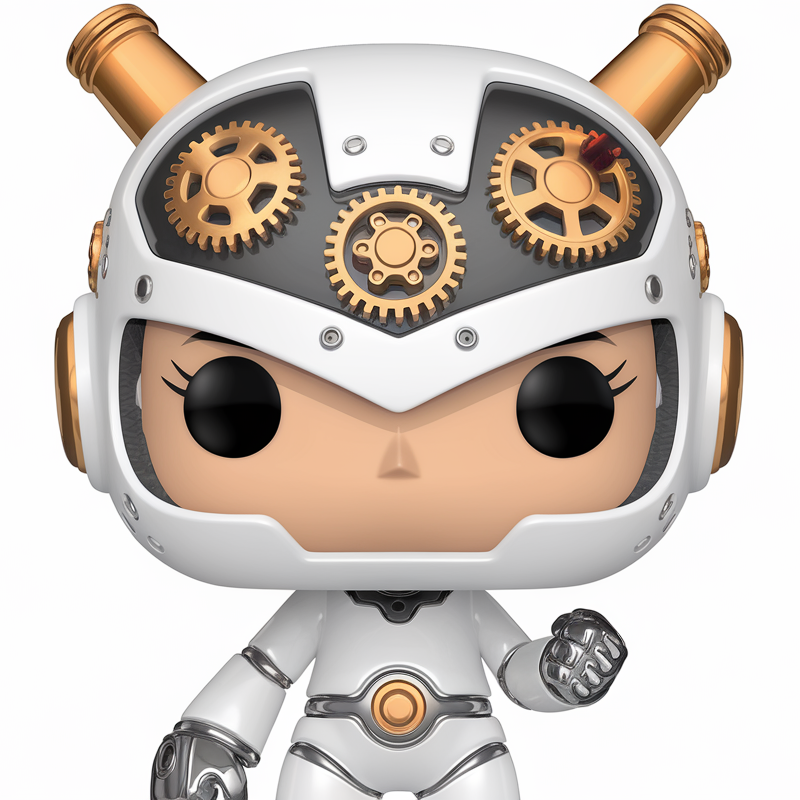
溶接は汎用性が高い一方で、設計・加工・仕上げすべての工程に配慮が必要です。
現場任せにせず、設計段階での配慮が高品質な製品づくりのカギとなります!
曲げ加工で製作
▶ 特徴
1枚の板金をL字に曲げて作る方法です。最も一般的な製作方法です。
✅ メリット
- 安価で量産しやすい
- 溶接不要で見た目がキレイ
- 軽量で扱いやすい
🚫 デメリット
- 曲げ部に応力集中しやすい(荷重が集中すると割れやすい)
- 厚板や高強度材には不向き
- 大型・高負荷用途には向かないことも
曲げ加工でL型ブラケットを製作する際の注意点とは?
L型ブラケットを「曲げ加工」で製作する方法は、溶接や削り出しに比べて工程がシンプルでコストを抑えやすいのが特徴です。
しかし、曲げ加工ならではの注意点を理解していないと、割れや変形といった不具合が起こることもあります。
本項では、曲げ加工で失敗しないための設計のポイントをわかりやすく解説します!
注意点①:板厚が厚い材料は「割れ」に注意!
✅ 曲げ加工は、外側に引張、内側に圧縮応力がかかる
曲げ加工では、材料の外側は引っ張られて伸びる方向に、内側は圧縮されて縮む方向に力がかかります。
📌 特に板厚が厚い場合は…
- 外側の伸びに材料が耐えきれず、クラック(割れ)が入る
- 曲げ角がきついと、さらに破損リスクが高まる
✅ 設計上の対策
✔ 最小曲げR(曲げ半径)を材料厚みに応じて確保する
🔍 例:SPCCなら、曲げR ≧ 板厚 × 1.0 ~ 1.5 が目安
✔ 延性(ねばり)の高い材料を選ぶ
👉 SS400やアルミ系材などは比較的曲げに強い
✔ 曲げ方向を素材の圧延方向に対して適切に設定する
👉 圧延方向と直交して曲げると割れにくい
注意点②:曲げ部の近くに穴や切欠きがあると変形しやすい
✅ 曲げ時に応力集中が起こり、変形・割れの原因に!
曲げ加工の近くに穴や切り欠きがあると、そこに応力が集中して、
- 穴の形状が変形して楕円になる
- 亀裂やクラックの起点になる
- 精度の高い部品にならない
というトラブルが発生します。
✅ 設計上の対策
- 穴・切り欠きは曲げ中心から十分に離す
👉 目安:板厚の3倍以上は離すのが安全 - どうしても近くに穴が必要な場合は、後加工で穴あけ
👉 曲げ後にドリルやレーザーで穴を空ける
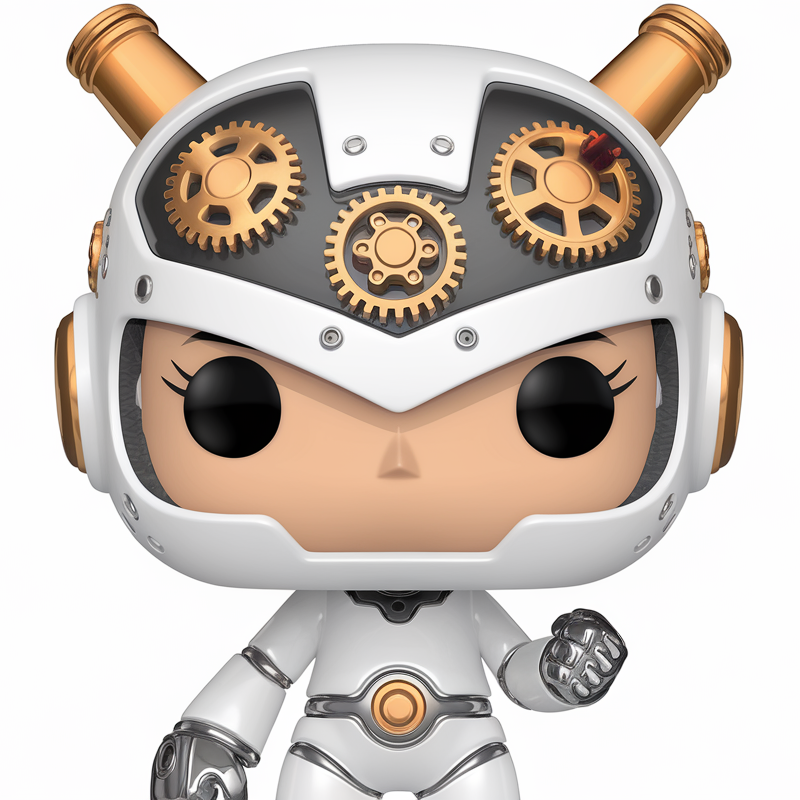
曲げ部に近い穴は変形するだけでなく、製品の強度低下にもつながるため要注意です!
その他のポイント:精度とばらつきに注意!
曲げ加工は ±0.2mm~0.5mm 程度のばらつきが出やすい
👉 高精度を要求する場合は追加工や冶具で補正が必要
角度ばらつきにも注意(±1°以上になることも)
👉 曲げ型の管理、材料バッチ差などに留意する
曲げ加工は手軽でコスト効率の良い方法ですが、材料の性質や形状に応じた適切な設計が不可欠です。
注意点 | 対策 |
---|---|
厚板での割れ | 材料に応じた最小曲げRを確保し、延性の高い材料を選ぶ |
穴や切り欠きの変形 | 曲げ部から十分に離す、または後加工を検討 |
精度のばらつき | 許容精度を確認し、必要に応じて補正設計を行う |
曲げ加工に慣れてくると、設計の自由度が広がります。
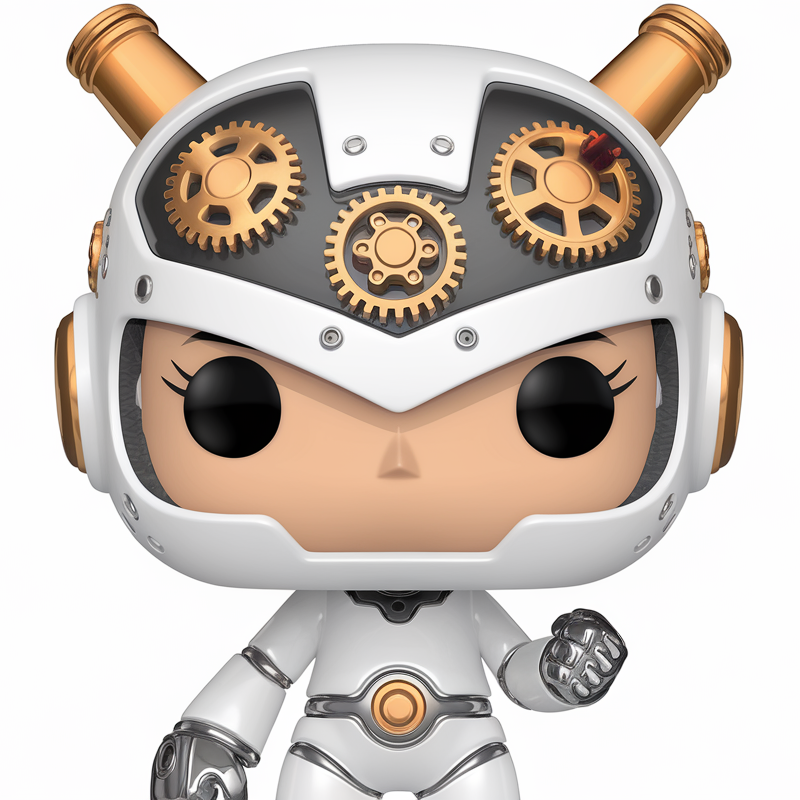
最初はこれらの注意点を押さえながら、「割れない・変形しない・組みやすい」L型ブラケットを目指しましょう!
削り出し加工で製作(切削)
▶ 特徴
金属の塊からL型形状を削って作る方法です。CNC加工などを使います。
✅ メリット
- 高精度な製品が得られる
- 応力集中が少なく、強度に優れる
- 美観も良好(表面仕上げしやすい)
🚫 デメリット
- 加工時間が長く、コストが高い
- 材料歩留まりが悪い(削る部分が多い)
- 小ロット・高機能向け
削り出し加工でL型ブラケットを製作する際の注意点とは?
L型ブラケットを作る方法のひとつに「削り出し加工(マシニング加工)」があります。
これは一枚の材料(丸棒や角材)から切削して形を作る方法です。
見た目も精度もキレイに仕上がりますが、設計の段階でよく検討しておかないと、驚くほどコストがかかるケースもあります。
本項では、「削り出しで作るL型ブラケット」の設計上の注意点をわかりやすく解説します!
削り出し加工の特徴のまとめ
削り出し加工とは、NCフライスやマシニングセンタなどの切削機械を使って、材料を少しずつ削りながら目的の形に仕上げていく方法です。
特徴 | 内容 |
---|---|
高精度 | 寸法や直角度が高精度で出せる(±0.01mm~可能) |
高剛性 | 一体構造になるため、溶接や曲げよりも剛性が高い |
高コスト | 材料費+加工費が非常に高くなることがある |
注意点①:とにかくコストが高い!
削り出し加工の最大のデメリットは「コストが高い」こと。
▶ 原因は主に以下の2点
- 材料ロスが多い
→ L型にするために大きな材料からガッツリ削り出す必要があり、削りカスの量が多い。
→ 特にアルミやステンレスなど高価な材料ではロスも高コストに直結。 - 加工時間が長い
→ L型は凹形状になるため、段取りや多面加工が必要。
→ 工数が多く、加工機の稼働時間が長くなり、コストアップ。
✅ 設計上の対策
- 本当に削り出しでなければならないのか?を見極める
👉 曲げや溶接で代替できないかを検討 - 不要な部分を省いた形状にする
👉 軽量化設計で加工時間・材料コストを削減 - 数量が多い場合は、アルミダイキャストなど別工法も検討
注意点②:加工制約と段取りに注意!
削り出しでは、3軸・5軸などの加工機を使って複雑な形状に対応できますが、段取り(加工方向の切替)や工具干渉の制限が出ることもあります。
🚫 具体的な注意点
- 奥まった内角部の加工が難しい(刃物が届かない)
- 工具長さが必要になり、加工剛性が低下する
- 加工方向ごとに治具や段取り替えが発生
これらが加わると、追加の加工費や治具費がかかります。
削り出しが適しているケースとは?
高コストにも関わらず、削り出しが選ばれるケースもあります。
以下のような条件なら、削り出し加工が有効です。
✔ 強度・剛性が重要で、一体構造が必要な場合
✔ 製品の精度が非常にシビアな場合(位置精度、直角度など)
✔ 少量製作で、他工法の金型コストが見合わない場合
✔ デザイン性や見た目が重視されるプロトタイプ用途
コスト・目的をよく見極めよう!
削り出し加工は高精度で高剛性な部品が作れる魅力的な加工方法です。
しかしその分、コストや加工時間が非常に大きくなるという大きなデメリットもあります。
項目 | 内容 |
---|---|
メリット | 高精度・高剛性・美観に優れる |
デメリット | 材料ロス・加工工数・コストが高い |
設計の工夫 | 他工法との比較・軽量化設計・形状の簡略化を検討 |
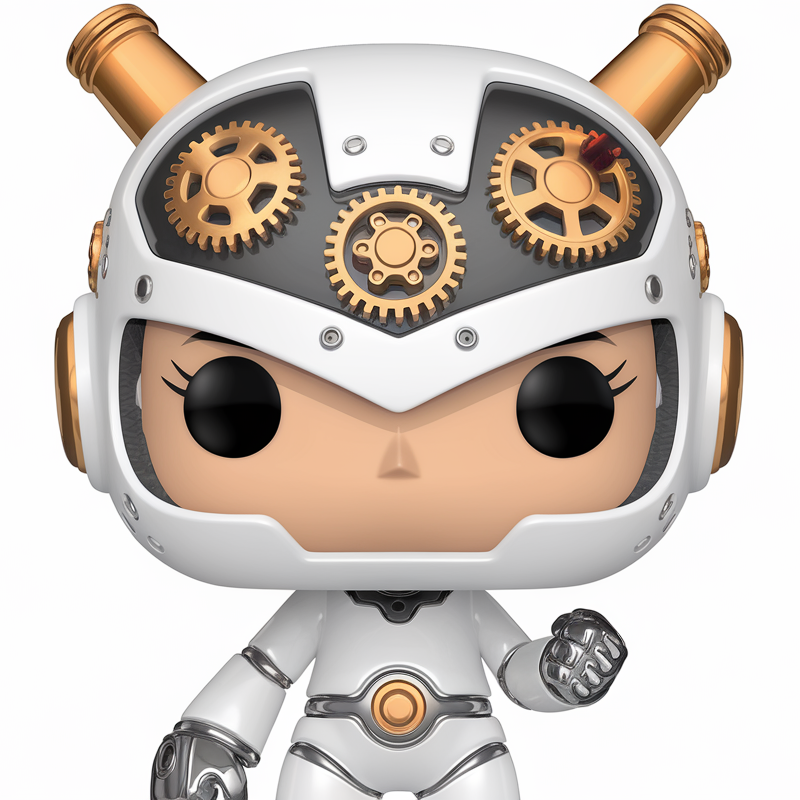
削り出しを選ぶときは、「他の製造方法では目的を満たせないか?」を一度立ち止まって見直すのがポイントです!
山形鋼(アングル)で製作
▶ 特徴
既製品の山形鋼(L型鋼材)をカットして使う方法です。建築や機械構造に多用されます。
✅ メリット
- 既製品を使えるため安価・手軽
- 材料入手が容易(ミスミ・ホームセンターなど)
- 頑丈で加工もしやすい(穴あけ・溶接可)
🚫 デメリット
- 直角精度があまり良くない(必要なら追加加工)
- 外観や寸法の自由度が低い
- 曲げや特殊形状には対応できない
山形鋼でL型ブラケットを作るときの注意点とは?
L型ブラケットの製作方法にはいくつか種類がありますが、コストパフォーマンス重視で手軽に作れるのが「山形鋼(アングル)」を使った方法です。
ホームセンターなどでも手に入りやすく、溶接やボルト締結などで簡単にL型部材を構成できます。
しかし、安価で便利な反面、注意すべきポイントもあります。この記事では、山形鋼でL型ブラケットを設計・製作する際の注意点をわかりやすく紹介します。
山形鋼(アングル)とは?
山形鋼(アングル)は、断面が「L字型」になっている鋼材です。
「等辺山形鋼(両辺が同じ長さ)」と「不等辺山形鋼(片方が長い)」の2種類があります。
主に以下のような場面で使われます。
✅ フレームの補強部材
✅ 簡易的なブラケット
✅ 鋼構造物の接合部 など
注意点①:規格寸法に合う材料を見つける必要がある
山形鋼は規格サイズがあらかじめ決まっている材料です。
つまり、設計時に自由な寸法で設計できるわけではないため、以下の点に注意が必要です。
🔧 規格に合わせた設計を心がけよう
✔ 市販されているサイズの一覧を確認してから設計する
✔ 必要寸法と規格寸法が合わない場合は、他の製作方法(曲げ・溶接)も検討
✔ 寸法に余裕がある場合は、「加工代(切断や穴あけスペース)」を考慮する
注意点②:直角度を必要とする場合は追加工が必要
山形鋼は製造時に「熱間圧延」によってL字形状が作られているため、精密な直角が出ていないことがよくあります。
一般的には90°±1~2°の範囲で誤差があるため、精密な位置決めや、装置のフレームなどで直角度が重要な場合にはそのまま使えません。
🔧 解決方法
✅ フライス加工や面取り加工で直角を出す
✅ 加工前提で、余長(加工代)を確保して設計する
✅ 位置決めには治具やピンを併用することも検討
山形鋼のメリット・デメリットまとめ
項目 | 内容 |
---|---|
メリット | 安価・入手性が高い・軽量・加工が比較的簡単 |
デメリット | 寸法の自由度が低い・直角度や平面度が不正確・精密部品には不向き |
📌 コストと精度のバランスがカギ
山形鋼を使ったL型ブラケット製作は、コストを抑えたいときや、強度がそこまで求められない補強部材としては非常に有効です。
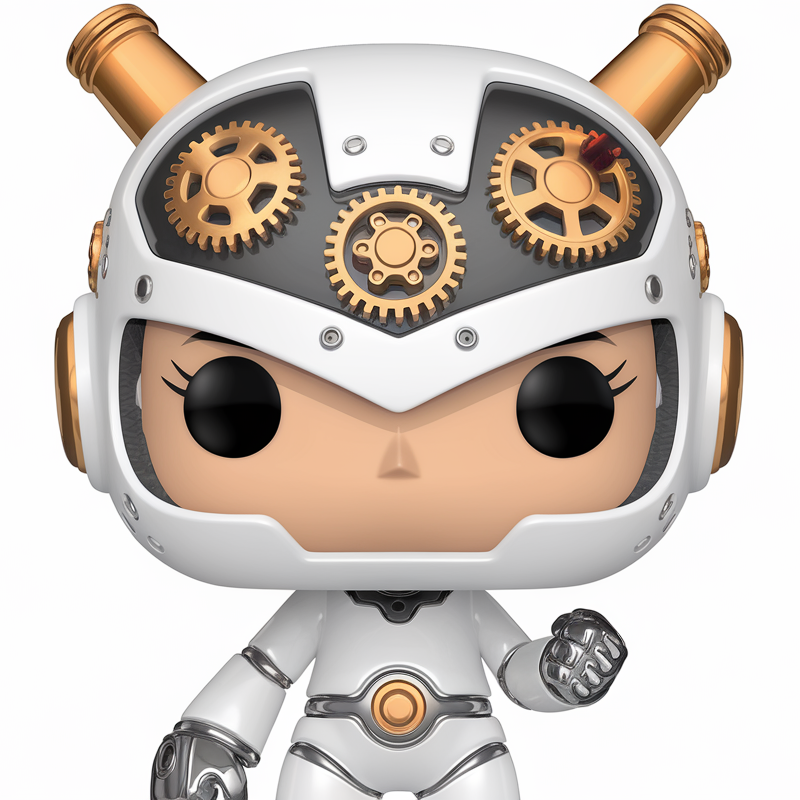
精密な直角や寸法精度が求められる場面では追加工が必須になるため、設計段階で「どこまで精度が必要なのか?」をしっかり見極めましょう。
ボルト締結で製作(部品を組み立て)
▶ 特徴
2枚の板やアングル材などをボルトでL型に締結して作る方法です。
✅ メリット
- 組み立てが簡単で、後からの調整も可能
- 分解・再利用できる
- 加工なしで既成部品を組み合わせ可能
🚫 デメリット
- 剛性がやや低く、緩みのリスクがある
- ボルト・ナットが必要で部品点数が多い
- 外観がゴツくなりがち
ボルト締結でL型ブラケットを製作する際の注意点とは?
L型ブラケットを製作する方法の中でも、溶接や曲げ加工を使わずに、プレートとプレートをボルトで組み合わせて作るというのは非常に手軽な方法です。
特に、設備の組み替えや調整が多い機械設計では、分解・再利用がしやすいというメリットがあります。
しかし、ボルト締結には特有のデメリットや注意点もあるため、用途に応じた使い分けが重要です。
注意点①:剛性がやや低く、緩みのリスクがある
ボルト締結は部品同士を「面で固定する」のではなく、「点で締め付ける」方法です。
そのため、以下のような問題が起こりやすくなります。
問題 | 内容 | 対策例 |
---|---|---|
剛性不足 | 曲げや衝撃荷重に対してたわみやすい | 座金を増やす、補強プレートを追加 |
緩み | 繰り返し振動でボルトが緩む | スプリングワッシャー、ねじロック剤の使用 |
面圧過大 | 締めすぎると部材が変形 | 適切な締結トルク管理、座面の設計工夫 |
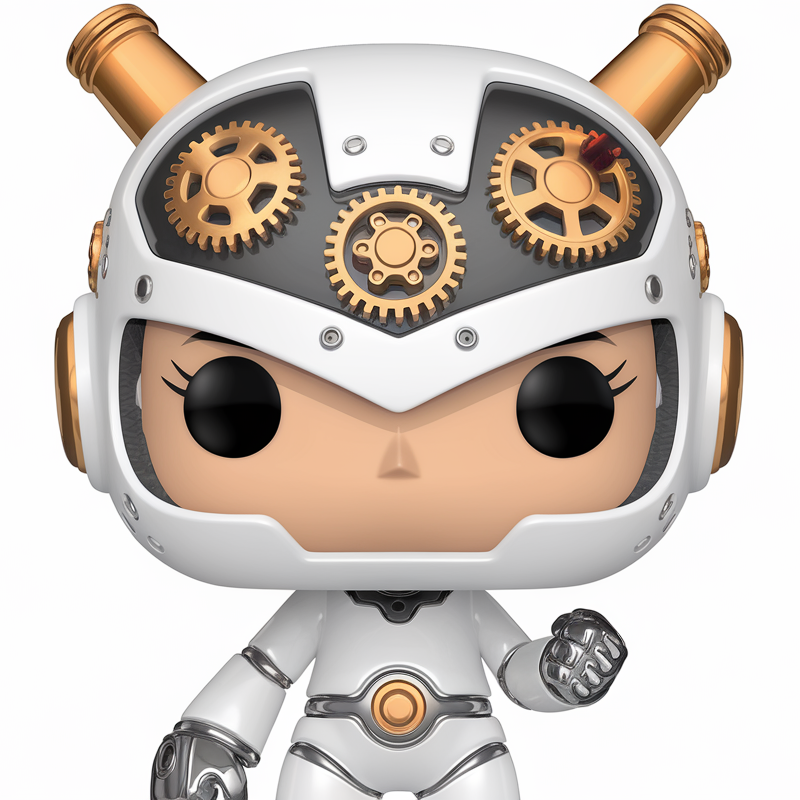
特に振動や衝撃が加わる部位では、緩み防止対策は必須です。
注意点②:部品点数が多く、ごつくなりがち
ボルト締結はナット、ワッシャー、ボルト、L字プレート(またはスペーサ)など、複数部品が必要です。
そのため、以下のような点に注意しましょう。
🔧 設計時の注意ポイント
✅ 部品点数が多くなると組立・メンテが面倒
✅ ボルトの頭部やナット分、外形寸法が大きくなるため干渉リスクに注意
✅ ごつくて重くなることがあるので、軽量化したい用途には不向き
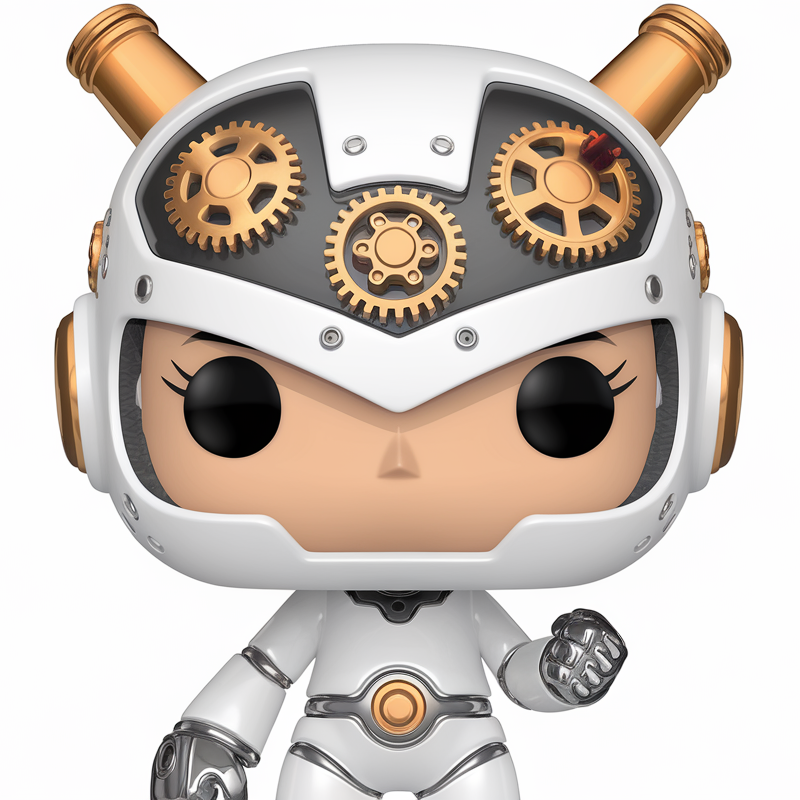
装置の「見た目」や「寸法制限」に関わるなら、できるだけスマートな構造を意識!
ボルト締結L型ブラケットの活用に向いているケース
- 小型装置のプロトタイプ
- 構造変更が頻繁にある試験装置や治具
- 溶接や曲げ加工ができない素材(アルミや樹脂)
手軽さと引き換えに“設計の工夫”が必要
ボルト締結によるL型ブラケットは、簡単で加工レスな構造として便利な反面、剛性・緩み・寸法のごつさなど、注意点も多い構造です。
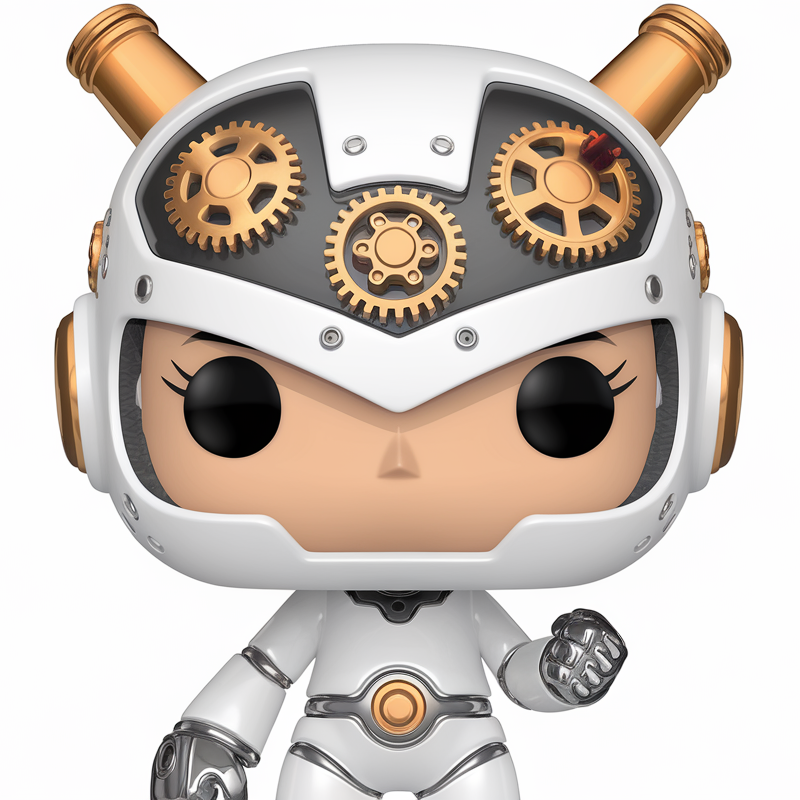
しっかりとした設計を行えば、組立や分解のしやすさを最大限に活かせるので、現場の用途に応じた使い分けを心がけましょう。
各工法のざっくり比較表
製作方法 | 強度 | コスト | 加工性 | 精度 | コメント |
---|---|---|---|---|---|
溶接 | ◎ | ○ | △ | △ | 高強度が欲しいときに |
曲げ加工 | ○ | ◎ | ◎ | △ | 軽量&コスト重視なら |
削り出し | ◎ | × | △ | ◎ | 高精度・高強度向け |
山形鋼 | ○ | ◎ | ○ | △ | 手軽&安価で頑丈 |
ボルト締結 | △ | ○ | ◎ | ○ | 可変性・再利用向け |
まとめ
L型ブラケットは、その用途や必要な強度・コスト・見た目などによって、最適な製作方法が異なります。
▶ 強度最優先:溶接 or 削り出し
▶ コスト&軽量重視:曲げ加工
▶ 手軽に作りたい:山形鋼 or ボルト締結
用途や数量、必要な精度に応じてベストな工法を選定することが、良い設計への第一歩です!
L型ブラケットは単純な形状ながらも、使用環境や用途に応じて最適な製作方法を選ぶことが非常に重要です。
それぞれの加工法の特性を理解し、図面設計の段階から「加工性」や「後工程の手間」を見越した設計を行うことで、トラブルの少ない安定した構造が実現できます。
コメント