機械設計において、部品の正確な寸法は非常に重要です。
しかし、実際の製造では、寸法にわずかな誤差が生じることが避けられません。
そのため、設計者はこの誤差を考慮しながら、製品が意図通りに機能するように設計を行う必要があります。この誤差の範囲を定義するのが「公差」であり、さらに部品同士の適切な接合や動作を保証するための基準が「はめあい」です。
この記事では、公差とはめあいの基本的な概念とその重要性について解説します。
公差とは
公差とは、設計上の目標寸法に対して許容される誤差の範囲を示すものです。どんなに精密な製造技術を用いたとしても、完全に設計寸法通りに部品を製作することは難しいため、この公差を設定して、寸法のばらつきが許容される範囲を規定します。公差は、部品が互いに正しく機能するために必要な余裕を持たせるためのものです。
公差の主な目的は、次の通りです。
機能の保証
公差を適切に設定することで、部品同士の正しい組み合わせや動作が確保されます。
▶ 適切なはめあいを実現
🔍例:軸と穴のはめあい(すきまばめ・しまりばめ)
▶ 摺動部の動作性を確保
🔍例:リニアガイドやベアリングのスムーズな動き
▶ 密閉性やシール性能の確保
🔍例:Oリングやオイルシールの効果を維持
適切な公差を設定しないと、部品がうまく組み合わない、摩耗が早まるなどの問題が発生します。
コストの最適化
過剰な精度を要求すると、製造コストが大幅に上がります。公差設計では、必要十分な精度を見極めることが重要です。
▶ 高精度加工にはコストがかかる
🔍例:±0.01mm以下の加工 → 追加工や測定費用が増加
▶ 公差を緩めるとコストダウン
🔍例:±0.1mmの公差に変更 → 通常の加工方法で対応可能
▶ 製造と品質管理のバランスを取る
🔍例:量産品は公差を広めに、精密機械は厳しく設定
公差を適切に調整することで、品質を維持しつつコストを抑えることができます。
製品の信頼性の向上
製品が長期間にわたり安定して機能するためには、公差の設定が不可欠です。
▶ 寸法のばらつきを抑えて品質を一定に
🔍例:量産部品の品質を均一化 → 製品の安定性向上
▶ 部品の互換性を確保
🔍例:交換部品がスムーズに適合する設計 → メンテナンス性向上
▶ 疲労や摩耗を考慮した公差設計
🔍例:高負荷部分はクリアランスを最適化し、摩耗を防ぐ
適切な公差設定により、製品寿命が延び、ユーザーの信頼を獲得できます。
公差の適切な設定は、下記項目に大きく貢献します。
✅ 機能の保証(正しく動作する)
✅ コストの最適化(無駄な精度をなくす)
✅ 製品の信頼性向上(品質の安定化)
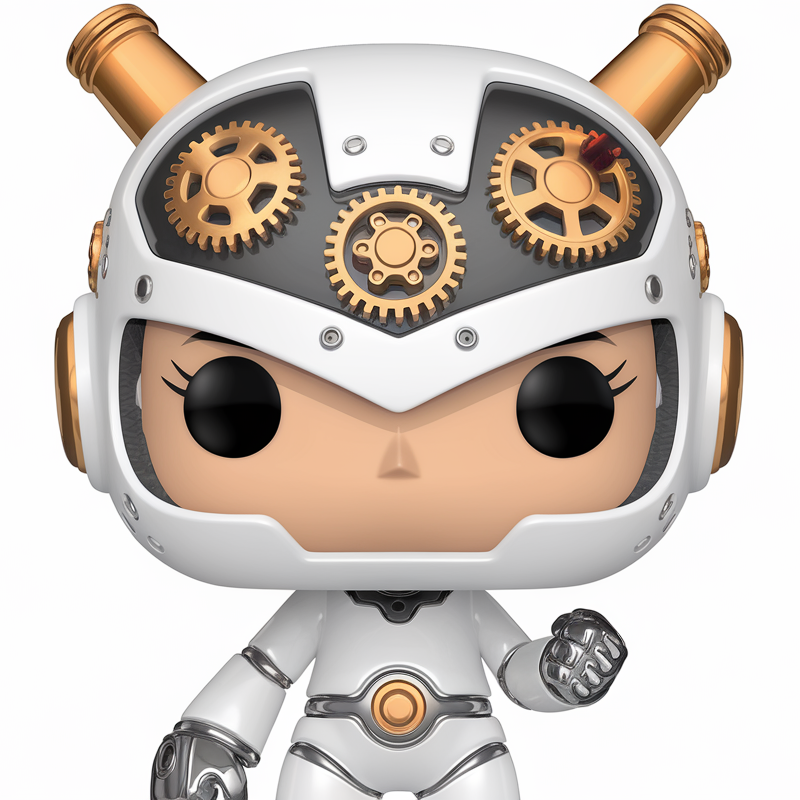
機械設計では、必要最小限の公差を設定し、性能とコストのバランスを取ることが重要です!
公差の表示方法
公差は、設計図上で通常以下のように表記されます。
📌 ±公差
例として、寸法が50 ± 0.1 mmと指定された場合、寸法は49.9 mmから50.1 mmまで許容されます。
📌 上限・下限公差
例えば、寸法が50 +0.2/-0.1 mmと指定された場合、寸法は50.2 mmから49.9 mmまで許容されます。
公差の累積
公差の累積とは、複数の部品や寸法が組み合わさったとき、それぞれの公差が積み重なることで、最終的な寸法や位置が大きくずれてしまう現象を指します。図面上では問題なさそうに見えても、“最悪の組み合わせ”が起きると、組み立て不良や機能不全を引き起こす原因になります。
最悪のパターンを想定しよう
設計で大切なのは、すべての寸法が“理想値”になるとは限らないという点です。
最悪の組み合わせ(すべてが公差の下限または上限)になっても部品が干渉せず、正常に動作・組み立てできるかを事前に検討しておくことが重要です。
✅ 想定しておくべき「最悪の組み合わせ」
🔍 例)
複数部品のズレが蓄積 ⇒ センサー位置がずれる
穴が最小寸法、軸が最大寸法 ⇒ 圧入不可
ガイド部品がすべて最大寸法 ⇒ 取り付けできない
公差の累積は、目に見えにくい落とし穴ですが、設計初期に意識しておくことで回避できます。
特に重要なのは、最悪のパターンを想定し、「これでも問題が起きないか?」という視点で寸法設計を行うこと。
これを意識するだけで、現場でのトラブル・コスト増・納期遅れを大きく減らすことができます。
一般公差について
機械設計では、すべての寸法に厳密な公差を指定するのは非効率です。
そこで活用されるのが 「一般公差」 です。
一般公差を適用することで、図面の記載を簡素化し、設計や加工の効率を向上させることができます。
一般寸法公差(JIS B 0405-1 / ISO 2768-1)
長さ寸法や角度寸法の公差を統一的に定めたものです。
部品のサイズに応じて 「精級」「中級」「粗級」「極粗級」 の4段階に分かれます。
公差等級 | 特徴 |
---|---|
精級(f) | 高精度な加工が必要な部品 |
中級(m) | 一般的な機械加工品 |
粗級(c) | 溶接品や鋳造品など、粗い仕上げ |
極粗級(v) | 精度が厳しくない部品 |
📌 設計例:「一般公差 ISO 2768-m」
→ 特に公差が指示されていない寸法は、中級(m)の公差を適用する
一般公差を使うメリット
✔ 図面の記載が簡潔になり、作図ミスを減らせる
✔ 標準化されているため、製造・検査がスムーズ
✔ 必要な部分だけ厳しい公差を設定でき、コストを最適化
一般公差を適用することで、無駄な公差を減らし、コストと精度のバランスを最適化できます。
📌 設計時のポイント
✅ 重要な寸法には個別に公差を設定し、その他は一般公差を適用
✅ 「ISO 2768-mK」のように、適用する一般公差を明確に指示
✅ 適用基準を決めることで、社内ルールを統一
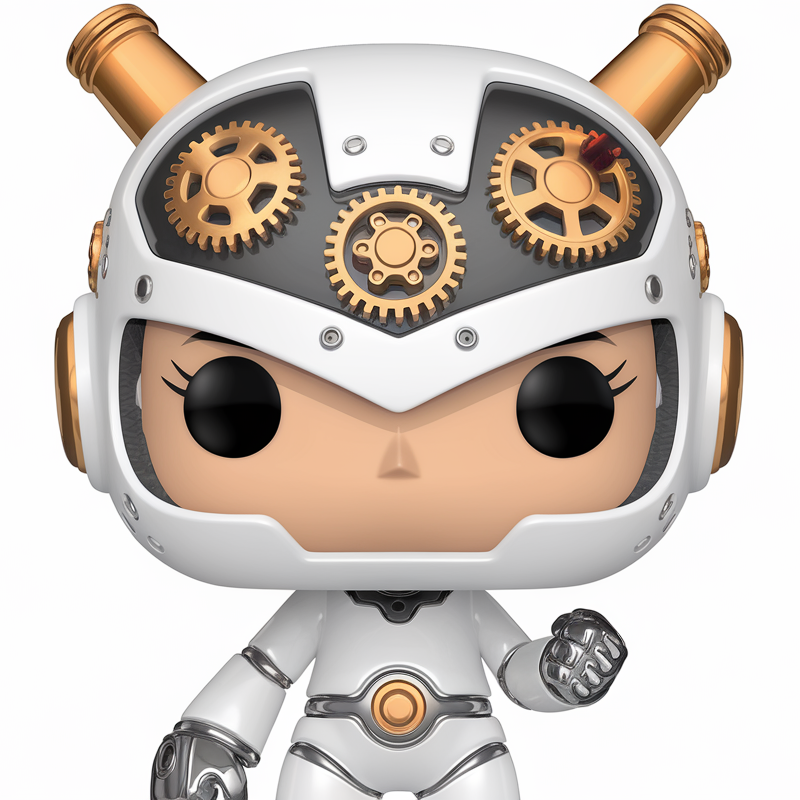
適切な公差設定が、製造コスト削減と品質向上の鍵となります!
幾何公差について
✅幾何公差は、形状・位置・姿勢・振れなどの精度を規定する公差のことです。
✅JIS(ISO)では、以下の4つのカテゴリに分類されます。
形状公差(形が正しく作られているか?)
▶ 真直度(まっすぐか)
▶ 平面度(平らか)
▶ 円筒度(円柱が歪んでいないか)
▶ 真円度(円が正確か)
🔍例)シャフトの軸径が指定寸法内でも、曲がっていると機能しないため、真直度公差を指定する。
姿勢公差(基準に対して正しい角度か?)
▶ 平行度(基準面と平行か)
▶ 直角度(基準面と垂直か)
▶ 傾斜度(基準面と指定角度になっているか)
🔍例)直角度公差を指定することで、ボルト穴が正しく垂直に加工されるようにする。
位置公差(正しい位置にあるか?)
▶ 同心度(中心がズレていないか)
▶ 対称度(形状が左右対称か)
▶ 位置度(基準点から正しく配置されているか)
🔍例)ベアリングの穴位置がずれていると、軸がスムーズに回転しなくなるため、位置度公差を指定する。
振れ公差(回転部品のブレを制御)
▶ 円周振れ(回転時にブレないか)
▶ 全振れ(すべての方向でブレないか)
🔍例)モーターの回転軸がブレると、騒音や振動の原因になるため、円周振れ公差を指定する。
幾何公差を使うメリット
✔ 機能を保証しつつ、製造コストを最適化
✔ 寸法公差だけでは制御できない要素を管理
✔ 組立や交換時の互換性を確保
例えば、寸法公差を厳しくするより、幾何公差で必要な精度だけを確保するほうが、無駄なコストを抑えつつ、必要な精度を確保できます。
幾何公差を適切に設定することで、
✅ 機械の性能を保証し、
✅ 加工コストを最適化し、
✅ 部品の互換性を向上させることができます。
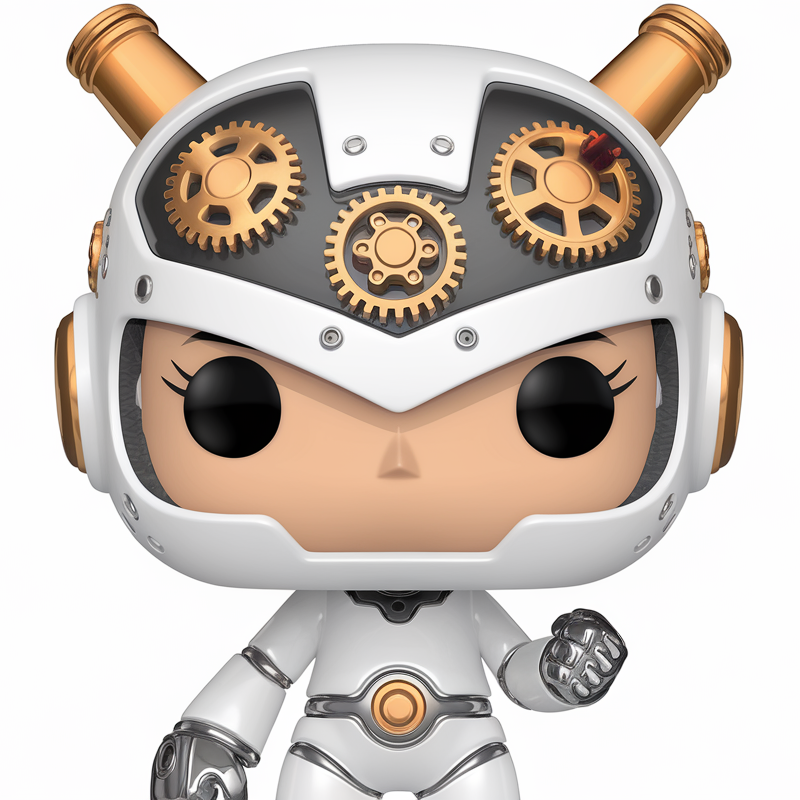
機械設計において、寸法公差だけでなく幾何公差をうまく活用することが、精度とコストのバランスを取る鍵となります!
表面粗さについて
表面粗さとは、部品の表面にある微小な凹凸の度合いを表す指標です。
加工方法によって、この粗さが変わり、摩擦や摩耗、密閉性に影響します。
📌 表面粗さが影響する要素
✔ 摺動部の摩擦(軸受・ガイドなど)
✔ シール性(密閉性)(Oリング、パッキン部)
✔ 疲労強度(応力集中を防ぐ)
✔ 接触面の密着度(溶接・接着部)
✔ 見た目の仕上がり(美観・塗装の仕上げ)
表面粗さの指標(Ra、Rz など)
表面粗さは、JIS(JIS B 0601)やISO(ISO 4287)規格で定義されており、主に以下の指標が使われます。
記号 | 名称 | 特徴 |
---|---|---|
Ra | 算術平均粗さ | 一般的に最もよく使われる指標 |
Rz | 最大高さ粗さ | 最高点と最低点の差で評価 |
Ry | 最大高さ | ある区間内の最大凹凸の高さ |
Rq | 二乗平均平方根粗さ | Raに似ているが、より精密な評価 |
📌 よく使われるのは「Ra」と「Rz」
Raは全体的な平均、Rzは局所的な最大凹凸を見るときに使います。
表面粗さRaと従来仕上げ記号▽の関係
機械設計の図面において、表面粗さを指定する際によく使用されるのが▽記号です。この記号は、表面の仕上げの度合いを視覚的に示し、加工業界で一般的に使われています。通常、▽の数が多いほど、表面が滑らかであることを意味し、表面粗さの値(Ra)も低くなります。
Ra(算術平均粗さ) | 従来仕上げ記号 |
50a , 100a | ~ |
12.5a , 25a | ▽ (1発) |
3.2a . 6.3a | ▽▽ (2発) |
0.4a . 0.8a , 1.6a | ▽▽▽ (3発) |
0.012a , 0.025a , 0.05a , 0.1a , 0.2a | ▽▽▽▽ (4発) |
表面粗さの基準値(JIS B 0601-2001)
表面粗さは「μm(マイクロメートル)」単位で表され、加工方法ごとに異なります。
加工方法 | Ra(μm) | Rz(μm) |
---|---|---|
研磨仕上げ | 0.05 ~ 0.2 | 0.1 ~ 1.0 |
ラッピング | 0.01 ~ 0.05 | 0.05 ~ 0.2 |
フライス加工 | 1.6 ~ 6.3 | 6 ~ 25 |
旋盤加工 | 0.8 ~ 3.2 | 3 ~ 15 |
鋳造 | 12.5 ~ 50 | 50 ~ 200 |
📌 用途に応じた表面粗さの目安
✔ 軸受や摺動部 → Ra 0.1~0.4 μm(研磨仕上げ)
✔ シール部品 → Ra 0.2~0.8 μm
✔ 一般機械部品 → Ra 1.6~6.3 μm(旋盤・フライス加工)
✔ 鋳造品・鋳物 → Ra 12.5 μm以上(粗い仕上げ)
表面粗さの設計における注意点
🚫 過剰な表面仕上げはコスト増
✔ 必要以上に滑らかな表面にすると、加工コストが高くなる!
✔ 摺動部や密閉部以外は、適切な粗さを選定するのが重要!
🚫 加工方法によって粗さが異なる
✔ 研削や研磨は滑らか、フライスや旋盤はやや粗い
✔ 鋳造や鋳物は表面が粗いので、後加工が必要になる場合も
🚫 摩耗や疲労強度を考慮する
✔ 粗すぎると摩擦や摩耗が増加
✔ 細かすぎると潤滑油の保持力が低下し、かえって摩耗が進むこともある
表面粗さは、機械の性能・寿命・コストに大きく影響します!
📌 設計時のポイント
✅ 用途に応じた適切な粗さを選ぶ(過剰な仕上げはコスト増)
✅ Ra と Rz を使い分ける(一般的には Ra を指定)
✅ 図面に表面粗さを明記する(明確な指示で加工ミス防止)
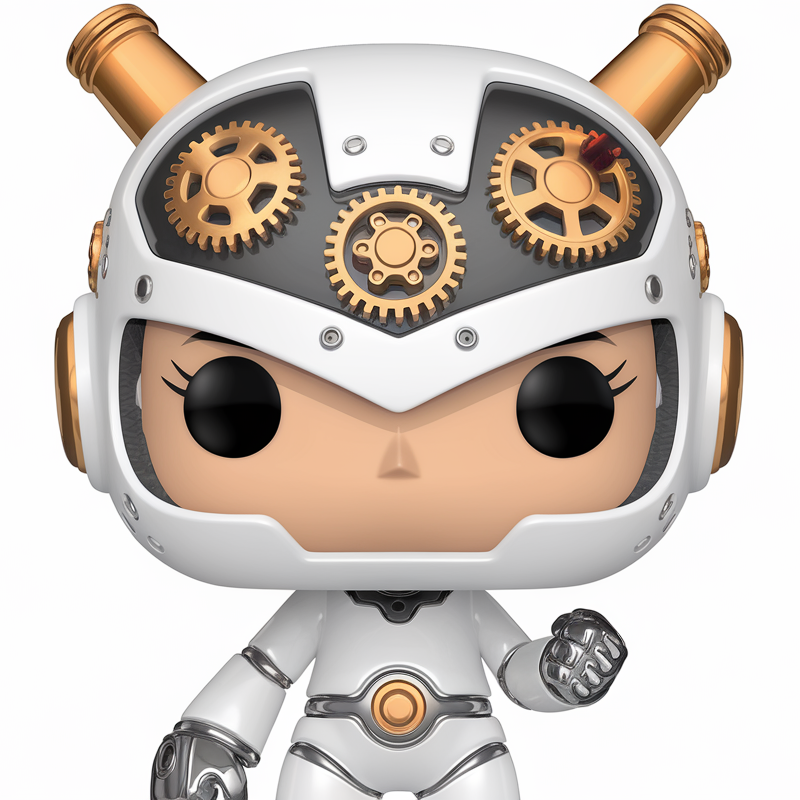
適切な表面粗さの設定が、品質向上とコスト最適化の鍵になります!
研磨指示について
研磨(grinding・polishing)とは、砥石や研磨材を用いて部品の表面を削り、仕上げ精度を高める加工方法です。
表面の凹凸を減らし、滑らかにすることで、寸法精度や機能性を向上させます。
研磨の目的
研磨は、次のような目的で行われます。
🔹 寸法精度の向上(高精度のはめあい、公差管理)
🔹 摺動抵抗の低減(軸受・ガイド・シール部品の性能向上)
🔹 密閉性の向上(Oリング・パッキン・シール部)
🔹 摩耗の抑制(研削加工による表面硬化)
🔹 美観の向上(外観品質の改善)
研磨の種類と特徴
機械設計において、よく使われる研磨方法を紹介します。
研磨方法 | 特徴 | 主な用途 |
---|---|---|
円筒研削 | 回転する部品の外径・内径を研磨 | シャフト、ベアリング、ブッシュ |
平面研削 | 平らな面を精密に仕上げる | 金型プレート、摺動部 |
ラッピング | 超精密研磨で高い平滑度を得る | シール面、光学部品 |
ホーニング | 円筒内面の仕上げ | シリンダー、油圧部品 |
バフ研磨 | 表面を滑らかにし、光沢を出す | 外観部品、装飾品 |
📌 用途に応じた研磨方法の選定が重要!
研磨指示をする際の注意点
🚫 研磨が不要な部分に指示しない!
👉 過剰な研磨はコスト増加の原因に!
🚫 適切な粗さを指定する!
👉 用途に合わせた適切な Ra 値を選定!
🚫 加工方法と寸法公差をセットで指定!
👉 加工指示が曖昧だと、仕上げ精度にバラつきが出る!
研磨は、部品の精度・摺動性・密閉性を向上させる重要な加工!
📌 図面で明確な指示をすることが品質向上のカギ!
✅ 研磨方法を明記(円筒研削、平面研削など)
✅ 仕上げ粗さ(Ra)を指定(適切な仕上げを得るため)
✅ 寸法公差と併記(精密加工が必要な場合)
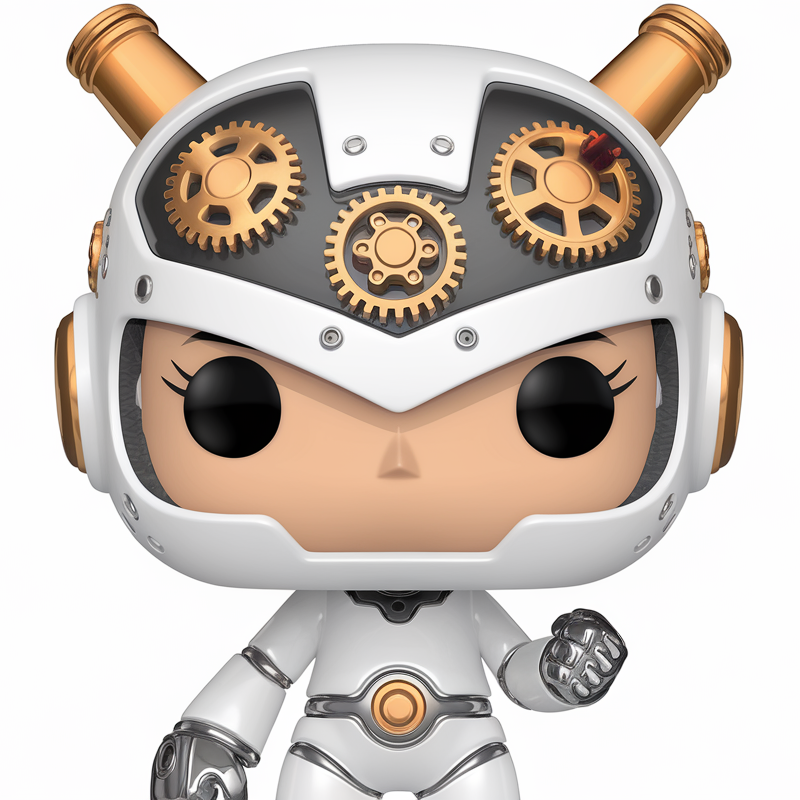
適切な研磨指示を行うことで、高品質な部品の設計とコスト削減につながります!
はめあいとは
はめあいは、軸と穴のように、二つの部品がどのように組み合わさるかを示す基準です。はめあいは、主に以下の3種類に分類されます。
はめあいの種類
✅すきまばめ
- 部品が容易に組み立てられたり分解できる状態を維持するはめあいです。
- 例として軸と穴の間に隙間がある場合。
✅中間ばめ
- 部品が組み立てる際に軽く押し込まれる必要のあるはめあい。
- クリアランスとインターフェイスの中間的な状態。
✅しまりばめ
- 部品が強い力で組み込まれ、外れにくい状態を維持します。
- 通常は高摩擦の場合に使用。
はめあいの公差記号の見方
はめあいは 「軸の公差」と「穴の公差」 を組み合わせて表します。
JIS規格では、公差記号(例:H7/g6) を用いて表記します。
公差記号の基本
- 穴の公差(大文字:H, G, F など)
- 軸の公差(小文字:h, g, f など)
- 数字(精度等級)(6, 7, 8 など)→ 小さいほど精密
🔍 例:H7/g6
🔹 H7(穴) → 基準寸法より大きくならず、小さくなる範囲が決まる
🔹 g6(軸) → 基準寸法より小さくならず、大きくなる範囲が決まる
この組み合わせによって、「すきまばめ・しまりばめ・中間ばめ」が決まります。
はめあいの適切な選定
✅ 機械設計においては、どのはめあいを選定するかが非常に重要です。
✅ 選定が適切でないと、部品の摩耗や故障の原因となる可能性があります。
✅ 設計の段階で、各部品の役割や使用条件に応じたはめあいを選ぶことが求められます。
使用用途を明確にする
はめあいを選ぶ際には、以下のポイントを考慮します。
✔ 軸と穴が動くか、固定するか?
✔ 摩耗や熱膨張を考慮する必要があるか?
✔ 組立や分解のしやすさは?
コストと加工精度を考慮する
適切なはめあいを選ぶ際には、加工コスト も重要です。
✔ 高精度のはめあい(h6, H6 など) → 加工コストが高い!
✔ 適度なすきまばめ(H7/g6 など) → コストを抑えられる!
📌 過剰な精度を求めると、加工コストが上がるためバランスを考える!
公差とはめあいの関係性
公差とはめあいは、互いに密接に関係しています。公差が適切に設定されていないと、はめあいの意図が正しく実現されません。例えば、すきまばめを設定する場合、軸と穴の公差が狭すぎると、意図したすきまが確保されず、可動性が失われる可能性があります。また、しまりばめの場合は、逆にすきまが大きすぎると、強度が不足し、部品が緩んでしまうことがあります。
公差とはめあいを組み合わせる際は、以下のポイントを考慮します。
✅ 寸法のばらつきが機能にどのような影響を与えるかを分析する。
✅ 組み立てやすさと製造コストのバランスを取る。
✅ 許容されるすきまやしまりの範囲を明確に定義する。
公差とはめあいの重要性
機械の精度と寿命に直結
✅機械の精度や耐久性は、各部品がどれほど正確に組み合わされるかに大きく依存します。
✅適切な公差とはめあいを考慮することで、摩耗や故障を防ぎ、機械の寿命を延ばすことが可能です。
例えば、軸受けとシャフトの間に適切なすきまばめが設定されていなければ、過度な摩擦が生じ、早期の摩耗や故障を引き起こします。
製造コストと品質のバランス
✅過度に厳しい公差を設定すると、製造コストが大幅に上昇します。
✅適切な公差を設定すれば、品質を維持しつつコストを抑えることができます。
設計者は、必要な精度と製造可能性のバランスを考慮し、公差を決定する必要があります。
組み立ての容易さ
✅部品同士が適切にはまり合うことは、組み立て作業の効率にも影響を与えます。
✅特に、大量生産においては、迅速かつ正確に組み立てが行えることが重要です。
はめあいが適切に設定されていると、作業者はスムーズに部品を組み合わせることができ、生産効率が向上します。
公差とはめあいの設定時に考慮すべきポイント
公差とはめあいを設定する際には、いくつかの重要なポイントを考慮する必要があります。
✅機能要求
部品がどのような役割を果たすかを明確にし、その機能に必要な精度やすきまを設定します。
✅材料の特性
使用する材料の伸縮や熱膨張を考慮して、適切な公差やはめあいを設定します。
✅使用環境
温度変化や振動など、使用環境が部品に与える影響を考慮します。
たとえば、温度変化による膨張を見越して公差を設定することが必要です。
✅製造精度
現実的に製造可能な精度と、必要な公差を比較し、無理のない範囲で設計を行います。
まとめ
機械設計における公差とはめあいは、部品同士が適切に機能するための基礎的な要素です。これらを正しく設定することで、機械の性能や寿命、さらには製造コストや生産性にも大きな影響を与えます。設計者は、公差とはめあいを適切に考慮し、各部品が最適な状態で組み合わされるように設計することが求められます。
公差とはめあいを理解し、適切に適用することで、高性能で信頼性のある機械を設計できるだけでなく、コスト効率の良い製造プロセスも実現できます。