機械設計の現場では、「できるだけ早く完成させてほしい!」という要求がよくあります。
一方で設計者としては、「できるだけ完成度を高めたい」とも考えるものです。
この両者はしばしばトレードオフ(相反関係)になります。
今回は、設計期間(納期)と完成度(品質・最適性)のトレードオフについて、初心者にもわかりやすく解説します。
なぜ設計に時間をかけたいのか?
機械設計では、短期間で完成させるよりも、以下のような完成度を上げるための検討に時間が必要です。
- 材料の強度やコストを最適化
- 荷重分布に応じた構造設計
- 加工や組立のしやすさを考慮
- 適切な公差設定やはめあい設計
- 耐久性や振動、熱などの検証
これらを丁寧に行えば、より安全で信頼性が高く、コスト効率の良い製品になります。
納期を優先すると起きること
一方、製品をできるだけ早くリリースしたいという要望も多くあります。
この場合、設計にかけられる時間はどうしても限られ、次のような状況になります。
納期優先でありがちな設計判断
項目 | 時間があれば… | 納期優先だと… |
---|---|---|
材料選定 | 強度・価格・加工性を最適化 | とりあえず手配しやすい材料で決める |
構造設計 | 軽量化・剛性バランスを検討 | 既存モデルを流用して最小限の変更 |
公差設計 | 組立性・加工費を見ながら設定 | ざっくりした一般公差で済ませる |
つまり、「とりあえず動くものを早く出す」という設計になりやすく、
後々の手戻りや品質問題のリスクが高まります。
試作・検証工程の省略リスク
短納期の設計では、試作・評価・検証のプロセスも圧縮されがちです。
省略されやすい検証内容
- 耐久試験:繰り返し荷重や振動の影響を見る
- クリアランス評価:動作時の干渉やバックラッシュの確認
- 熱変形・材料疲労のチェック
これらを省略すると、たとえ設計図面上は問題がなくても、実機でトラブルが出る可能性が高くなります。
設計期間と完成度のバランスをどう取るか?
現実には、「納期も守りたいし、完成度も下げたくない」という矛盾した要求が多いです。
このときに重要なのは、優先順位を整理してリスクを見極めることです。
バランスの取り方の例
優先度 | 判断ポイント | 見極め方 |
---|---|---|
高 | 人命や安全にかかわる要素(強度・破損) | どんなに短納期でも十分検討が必要 |
中 | 性能や信頼性(振動、摩耗、精度) | できる限り検証するが簡略化も視野 |
低 | 美観や利便性(見た目・分解性) | 初期は妥協し、後で改良する計画も可 |
設計フェーズごとの判断ポイント
フェーズ | 時間をかけたい項目 | 急ぎのときの妥協案 |
---|---|---|
初期構想 | 使用材料、荷重計算 | 既存設計の流用を前提に考える |
詳細設計 | 公差、締結方法、干渉チェック | 基本形状と機能だけを決めておく |
試作・検証 | 耐久・振動・熱試験 | 初回は基本機能だけに絞って評価 |
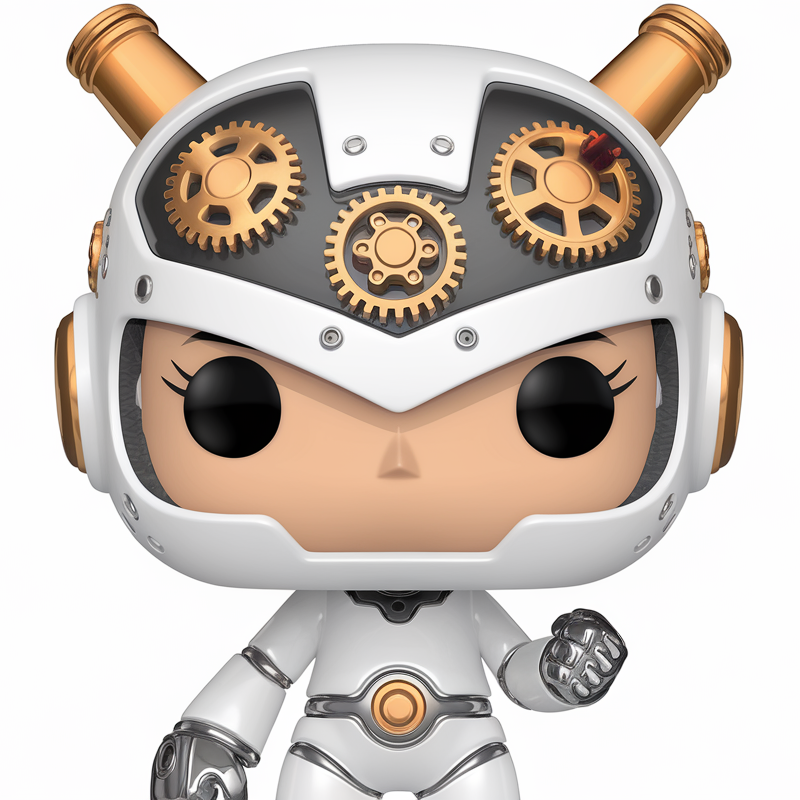
「必要なところには時間をかけ、妥協できる部分は簡略化」という視点が大切です。
設計者として注意すべきこと
短納期を受けた場合でも、以下の意識を持ちましょう
- 致命的なリスクは見逃さない(安全性・強度)
- 不明点は早めに周囲と相談する
- 仕様変更の余地を残した設計にする
- 「今は暫定」と明示しておく
これにより、後工程や量産時の手戻りを防げる可能性が高まります。
設計期間と完成度のトレードオフには「効率化」がカギ!
機械設計では、「早く仕上げたい」と「完成度を高めたい」という、相反する要求に向き合うことがよくあります。
これはまさに「設計期間と完成度のトレードオフ」です。
どちらかを優先すれば、もう一方に影響が出てしまいます。
しかし、両立に近づける工夫もあります。
そのカギが、「設計効率の向上」です。
本項では、トレードオフの考え方と、効率化によってその影響を抑える方法について、初心者向けにわかりやすく解説します。
設計期間と完成度はなぜトレードオフになる?
設計には、「じっくり時間をかけて作りこむ」ほど高い完成度が期待できます。
しかし実際には…
- 「納期が迫っている」
- 「今すぐ製品を立ち上げたい」
- 「先行試作を急ぎたい」
…といった事情から、設計期間が限られることも多いです。
その結果、
- 材料の選定が大ざっぱになったり
- 公差や組立性の検討が浅くなったり
- 耐久評価が簡略化されたり
といったリスクが生じやすくなります。
設計の効率化が重要になる理由
こうした状況で「完成度を維持しながら、設計期間を短縮したい」とき、頼りになるのが設計の効率化です。
効率化とは、単に「早く図面を引く」ことではありません。
ムダな検討を減らし、再利用可能な設計を活かすことで、品質を保ちつつスピーディに設計を進めることを指します。
設計効率を高める5つの方法
① 標準化設計の活用
よく使う部品や構造、モジュールは、テンプレート化・標準化しておきます。
🔍 例)
- 汎用ブラケット、取付プレートの穴ピッチ設計
- モーター取付部の標準寸法化
- 規格フレームに合わせた設計
➡ 都度ゼロから設計せず、流用でスピードアップできます。
② 過去図面・成功事例の活用
過去の設計図や似た製品の構成は、効率化の宝庫です。
前回の設計で何に苦労し、どこを改善したかを活かしましょう。
➡ 一から仕様検討する時間を大幅にカットできます。
③ モジュール設計で再利用性を高める
一体設計ではなく、「機能ブロックごとに分割」して設計すると、再利用や検討分担がしやすくなります。
🔍 例)
- 制御部、搬送部、固定部などのモジュール化
- ボルト締結ユニット、シャフト支持ユニットを使い回す
➡ ユニット単位で検討できるため、効率的で手戻りも減らせます。
④ 3D CADの活用と自動化
3Dモデルから図面生成、自動干渉チェック、部品表出力などのCAD機能をフル活用します。
マクロやスクリプトで繰り返し作業を自動化するのも有効です。
➡ 手作業によるミスや検討漏れを防げ、設計時間を短縮できます。
⑤ 検討の優先順位を見極める
全てを完璧にしようとせず、「重要な部分に注力し、そうでない部分は割り切る」判断も効率化の一つです。
🔍 例)
- 安全性や構造強度には時間をかける
- 非重要部品の選定や詳細形状は標準品で済ませる
➡ 重要なポイントを逃さずに、無駄な時間を省けます。
トレードオフは「知識」と「工夫」で乗り越えられる
「納期か完成度か」ではなく、「両方にできるだけ近づく設計」を目指すには、日頃からの準備と工夫が不可欠です。
設計者として意識しておきたいのは以下のポイントです:
対策 | 内容 |
---|---|
標準化 | 汎用設計はテンプレート化しておく |
ナレッジ蓄積 | 成功・失敗事例を社内で共有する |
設計分担 | 検討項目をモジュール単位で分担 |
設計ツールの活用 | CAD、CAE、PDMの機能を使いこなす |
優先度の明確化 | 重要なところに時間をかける判断力 |
時間がないときほど効率的に!
✔ 設計には時間がかかるが、すべてを時間で解決するのは現実的ではない
✔ 完成度を維持したまま設計期間を短縮するには、「効率化」が不可欠
✔ 標準化、再利用、モジュール化、ツール活用などの工夫で、両立に近づける
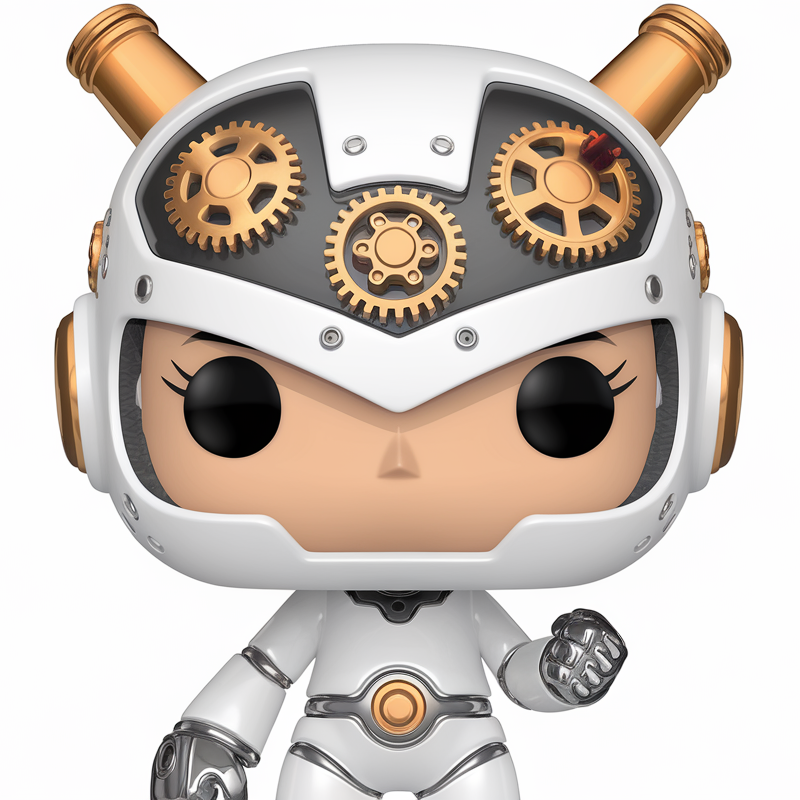
短納期でも品質を妥協しない設計をするには、日頃の準備と設計スキルの積み上げがカギです。
まとめ:トレードオフを理解して賢く設計しよう
観点 | 短納期設計 | 時間をかけた設計 |
---|---|---|
スピード | ◎ | △ |
完成度 | △ | ◎ |
品質リスク | 高め | 低め |
市場投入タイミング | 早い | 遅いが安定 |
機械設計では、いつも「時間」と「品質」の両立が求められます。
設計者としては、どこで妥協するか、どこは譲れないかをしっかり見極める目が必要です。
機械設計では、「早く仕上げる」ことと「完成度を高める」ことの両立が求められますが、両者はトレードオフの関係にあります。
納期を優先すれば最適設計や十分な検証が難しくなり、完成度を重視すれば設計期間やコストが増える可能性があります。
こうしたジレンマを乗り越えるには、設計の効率化が不可欠です。
標準部品の活用、過去設計の流用、モジュール化、CADの自動化機能などを活用することで、短期間でも品質を維持した設計が可能になります。
重要なのは、「どこに時間と手間をかけるべきか」を見極め、設計全体のバランスを意識することです。
トレードオフを理解し、効率的に対応できる設計者を目指しましょう。
コメント