機械設計においてセンサーは、自動化・安全対策・品質向上に欠かせない重要な要素です。
このページでは、センサーに関する基礎から、各種類の特徴・選定ポイント・設計の注意点まで、体系的にまとめています。
各項目には詳しい個別記事へのリンクもありますので、必要な情報をすぐにチェックできます!
センサーの基礎知識
設備設計におけるセンサー配置とその重要性
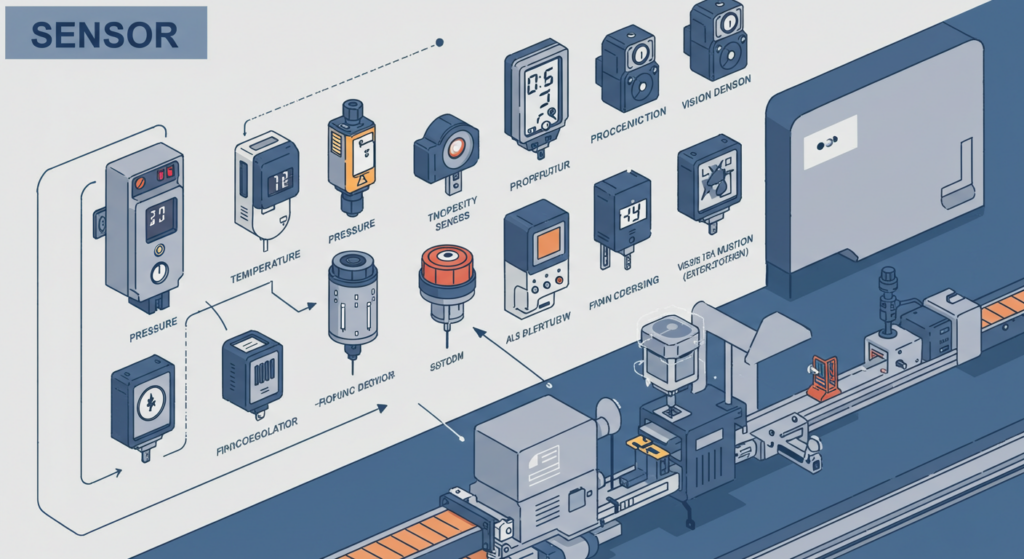
現代の機械設計において、センサーは設備の精度・効率・安全性を支える欠かせない要素です。特に設備設計においては、「どの動作を、どのタイミングで、どこで検知すべきか」という視点で、センサーの配置計画を行うことが非常に重要です。
✅ 動作イメージの具体化と可視化
センサー配置を最適化する第一歩は、設備全体の動作を把握し、それを図やフローチャートで「見える化」することです。たとえば、ワークの位置確認や作業開始・終了タイミングの把握、安全の確保など、各工程ごとの目的を整理し、必要な検知ポイントを洗い出します。
✅ 動作ごとのセンサーの役割定義
動作に応じて必要な情報を収集するため、以下のようなセンサーを適材適所に配置します。
- 光電センサー:ワークの有無や通過確認に。
- 近接センサー:金属部品の有無や取り付け確認に。
- エリアセンサー:作業エリアへの人の侵入を検知し、安全確保。
- ロードセルや圧力センサー:荷重や圧力の異常検出。
✅ 動作イメージが設計に与えるメリット
動作を具体的にイメージすることで、以下のような効果が得られます。
- センサー設置位置の最適化:検出精度が高く、誤作動の少ない位置に配置可能。
- 誤動作の予防:センサーの死角や干渉リスクを事前に排除。
- 設備効率の向上:センサーとアクチュエータが連携し、無駄のない動作を実現。
✅ 設置計画の進め方
- 必要な情報のリスト化
工程ごとに必要な検知情報を洗い出します。 - センサーの種類選定
対象物や環境条件(材質、距離、温度、粉塵など)に応じて適したセンサーを選定します。 - センサー配置の検討とシミュレーション
動作イメージをもとに最適な位置へ設置し、設計段階で動作確認・調整を行います。
✅ センサー活用の主な目的と例
- 動作制御:光電・近接センサーで位置や有無を検知。
- 異常検出:圧力・温度センサーで装置異常を早期発見。
- 自動化:リミットスイッチやレーザーセンサーでロボットの動作制御。
- 安全管理:エリアセンサーで作業者を検知し機械を停止。
- データ収集・分析:流量・荷重データを収集し、保守予知や効率改善に活用。
このように、機械設計におけるセンサー配置は、設備の品質・効率・安全を大きく左右します。
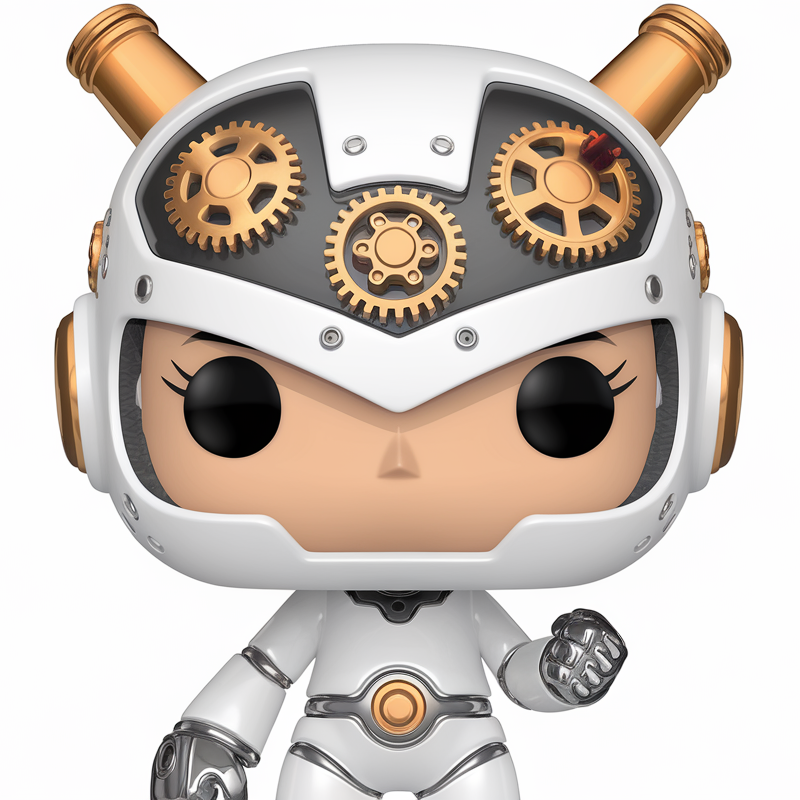
設計の初期段階から動作の具体化を行い、最適なセンサー選定と配置を行うことで、高信頼・高性能な設備設計が実現できます。
機械設計におけるセンサーの役割と種類
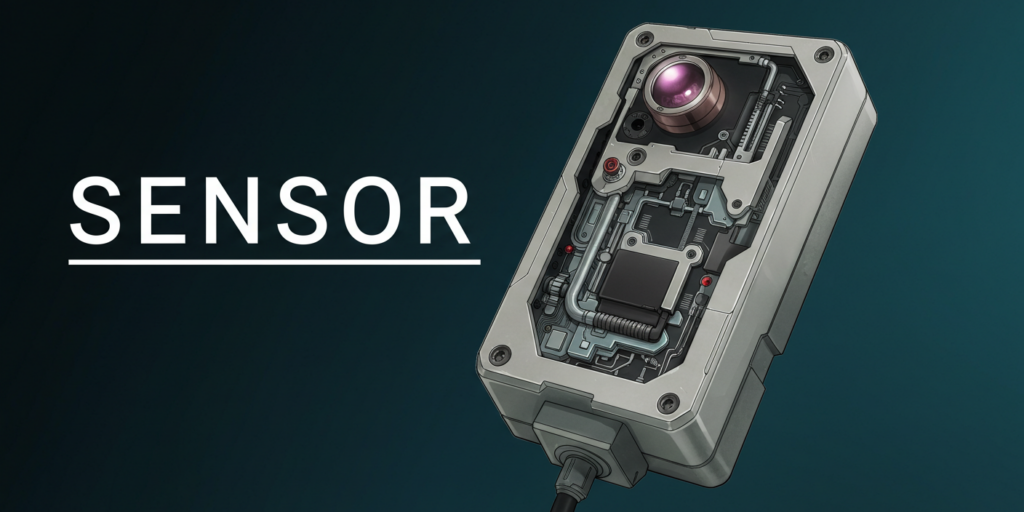
✅ センサーの役割と重要性
センサーは「位置・速度・温度・荷重」などの物理量を電気信号に変換する装置で、機械の監視・制御・安全・効率化に欠かせない要素。IoTやAIとの連携で、設計の高度化にも貢献。
✅ センサーの主な役割
- 状態監視:異常・過熱・負荷をリアルタイム検知(例:温度・圧力センサー)
- 動作制御:精密な制御(例:位置センサー)
- 安全性の確保:異常時の停止や警報(例:距離センサー)
- 効率向上:データを基に最適運転(例:流量センサー)
✅ 機械設計で使われる主要センサーと用途
センサー名 | 特徴・用途例 |
---|---|
光電センサー | 光で対象物を検知。部品の有無や位置決めに使用。 例:コンベアでの検出、カウント作業。 |
近接センサー | 一定距離内に近づいた物体を非接触で検出。 例:ロボットアームの停止制御、安全カバー制御。 |
オートスイッチ | エアシリンダのピストン位置を磁石で検知。 例:組立工程での動作確認、シーケンス制御。 |
リミットスイッチ | 機械的接触で検出。 例:テーブル終端検出、搬送停止位置確認、安全装置。 |
レーザー距離センサー | 高精度な距離測定。 例:AGVの障害物検知、建築距離測定。 |
ロードセル | 荷重を電気信号化。 例:重量計、プレス機の圧力監視。 |
エア圧力センサー | 圧縮空気の圧力検出。 例:エア漏れ検知、安全監視。 |
流量センサー | 液体や気体の流量測定。 例:冷却水・薬液の供給管理。 |
✅ センサーの活用で得られるメリット
- 安全対策 → 人や装置を守る設計に
- 高精度な動作制御 → 品質・生産性の向上
- 異常の早期発見 → 故障予防と信頼性向上
- 効率運転 → 省エネとコスト削減
センサー選定は“動作の見える化”から始めよう!
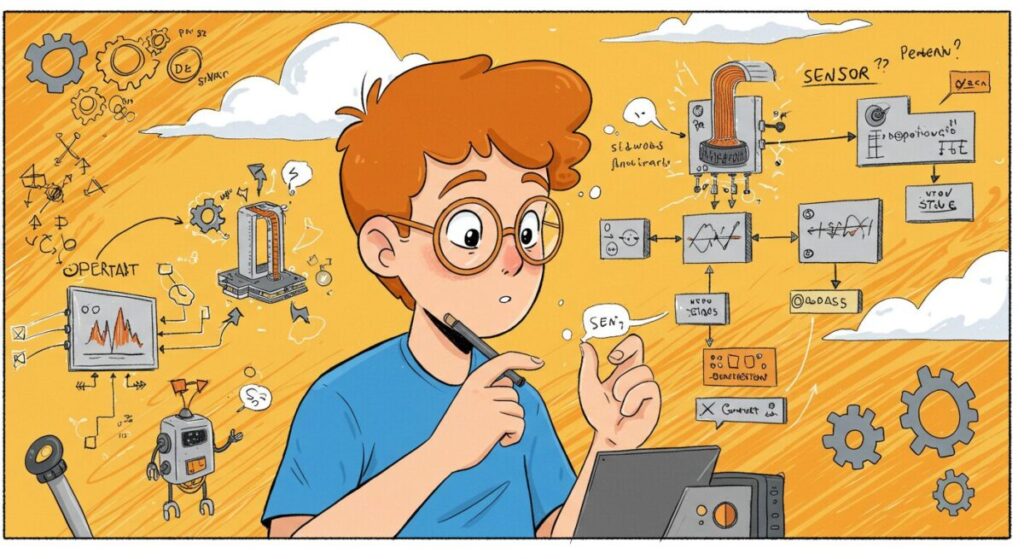
センサーの選定を考える際、いきなり「どのセンサーを使うか?」を検討するのは早すぎます。
まず重要なのは 設備全体の動作フローを見える化すること です。
✅ なぜ「見える化」が必要なのか?
- センサーは「どこで・何を・どう検知するか」が明確でないと効果を発揮しません。
- 動作の流れを整理することで、センサーが必要な箇所が自然と見えてきます。
✅ 見える化のポイント
- 作業のスタート/完了の把握
- 例:ワーク搬入 → 光電センサー、処理完了 → オートスイッチ
- ワークの位置・状態の確認
- 例:所定位置 → 近接センサー、向きや有無 → 画像・レーザーセンサー
- 安全性の確保
- 例:作業者接近 → エリアセンサー、カバー未閉 → リミットスイッチ
✅ フローチャートが鍵!
✔ フローチャートを使うメリット
- 動作の順番、条件、判断基準が明確になる
- 電気設計(PLCやラダー)との共通言語になる
- 設計ミスや漏れを防止できる
✔ フローチャートに含めるべき内容
- スタート/ストップ条件
- 各動作(センサーON、シリンダー動作など)
- 各タイミングの条件分岐(例:「センサーAがONなら次へ」)
✅ 構想段階でのフローチャート作成が重要!
✔ フローチャートを描くことで…
- センサーの数・位置・役割が明確に
- 設計変更を回避しやすくなる
- 電気設計とのスムーズな連携が可能に
- 設置スペースや干渉の問題も早期発見できる
「とりあえず設計して、あとでセンサーを追加」では遅い!
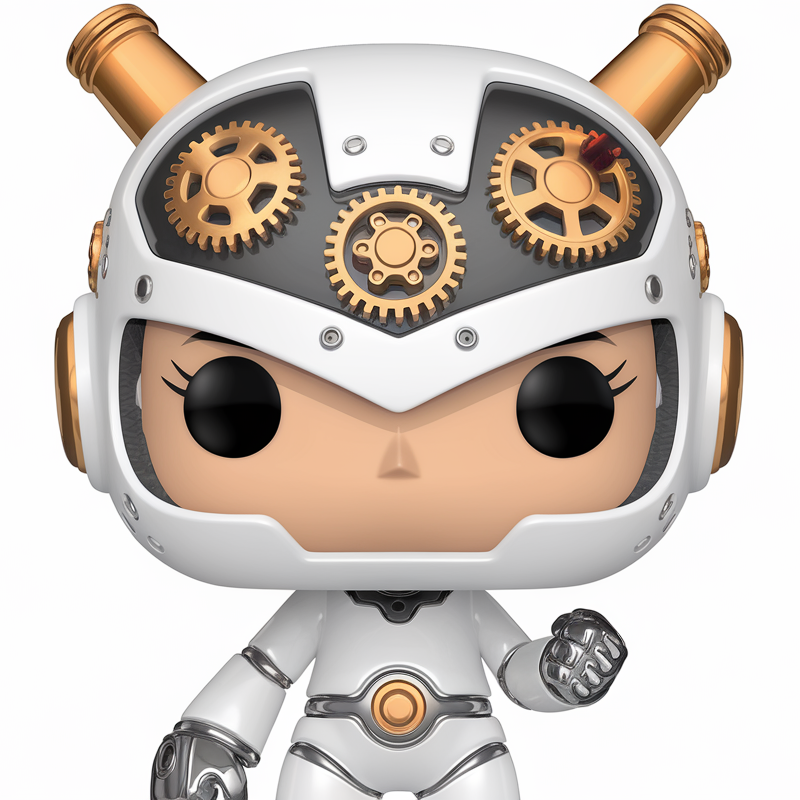
センサー選定の第一歩は、「設備の動作を可視化すること」。
フローチャートを活用して、設計段階からセンサー配置を計画することで、安全で効率的な設備設計が実現します。
センサーの種類と特性・選定ポイント
光電センサー
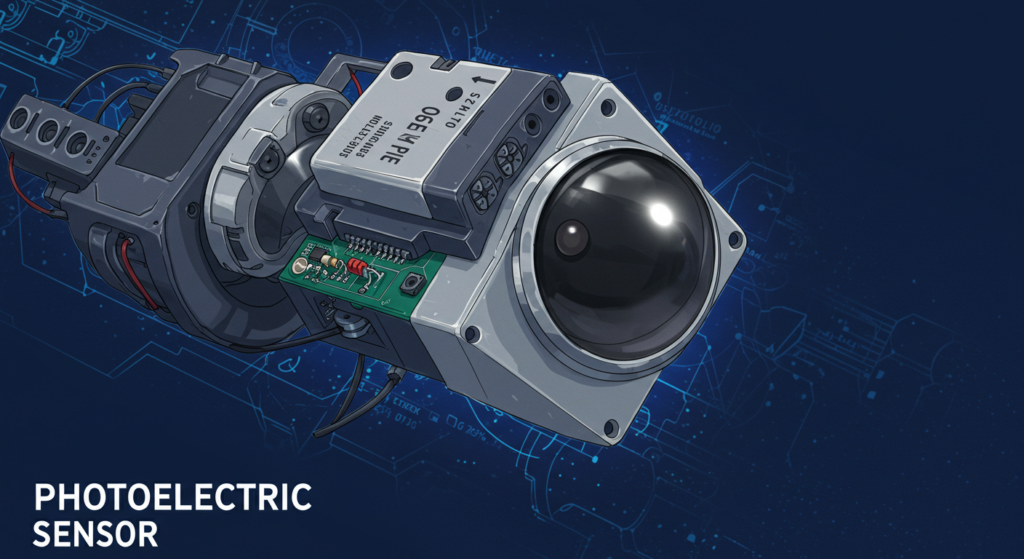
✅概要
- 光を利用して対象物を検知するセンサー。
- 透過型、反射型、回帰反射型などの方式があります。
🔍用途
- コンベア上の部品検出。
- 箱詰めラインでの有無検知。
- カウント作業や位置決め。
📌光電センサーの活用例
- 部品検出(コンベアライン)
- 自動車部品工場のコンベア上で、光電センサーを使って部品の有無を検知。
- 部品が検出されない場合、自動的にラインを停止してミスを防止します。
- パッケージング工程でのカウント
- 飲料の自動箱詰めラインで、光電センサーにより所定の本数が詰められているかを確認し、不足があればアラームを鳴らします。
近接センサー
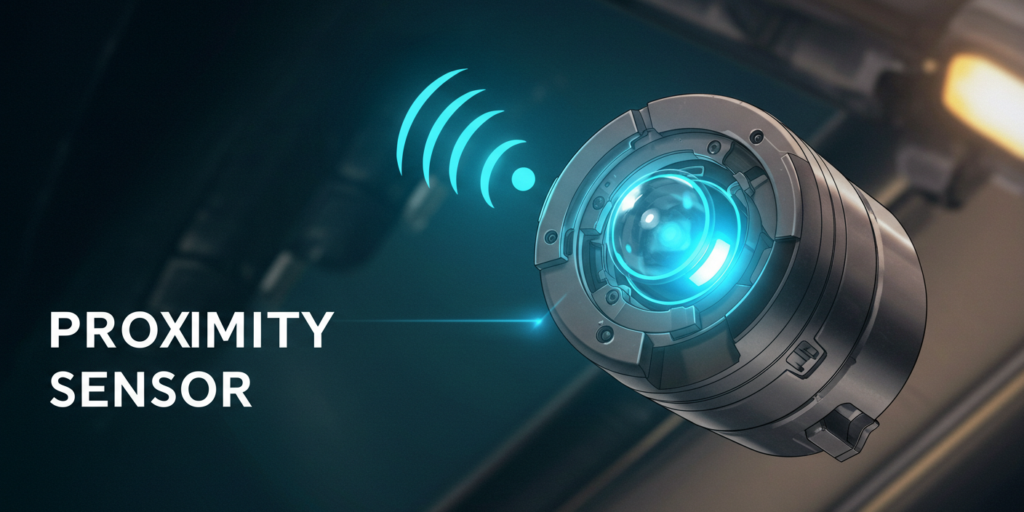
✅概要
- 対象物が一定距離内に近づいた際に反応するセンサー。
- 非接触で動作するため、耐久性が高い。
🔍用途
- 機械の位置決め。
- 回転体やスライド機構のエンド検出。
- 金属製品の有無検知。
📌近接センサーの活用例
- ロボットアームの停止位置制御
- 工場内のロボットアームが動作範囲内で確実に停止するように、近接センサーを設置。
- センサーが対象物を検出した時点でアームの動作を制御します。
- 安全カバーのインターロック制御
- 近接センサーが安全カバーを感知し、取り外されていれば設備の動作を停止。
- 耐久性が高いため、長期間にわたって安定して動作します。
レーザー距離センサー
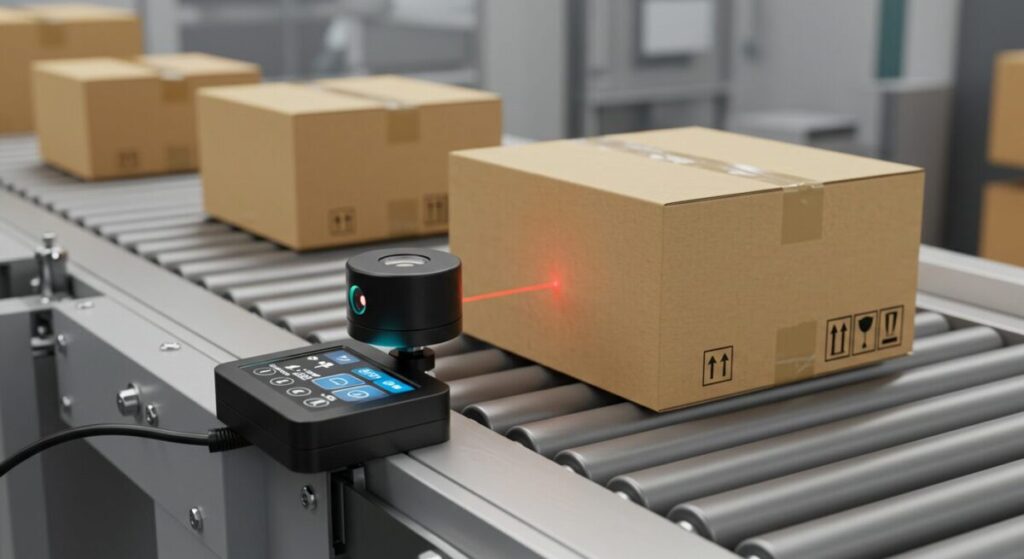
✅概要
レーザー光を使用して対象物との距離を高精度に測定するセンサー。
🔍用途
- 自動車の衝突防止システム。
- 設備間距離の測定。
- 部品の厚さ測定や位置確認。
📌レーザー距離センサーの活用例
- 倉庫の自動搬送ロボット(AGV)のルート制御
- レーザー距離センサーを搭載したAGVが、障害物を検知して衝突を回避。
- スムーズな自動搬送を実現します。
- 建築現場での距離測定
- 高精度なレーザー距離センサーを使用して建築資材間の距離を測定。施工精度を向上させます。
ファイバーセンサー
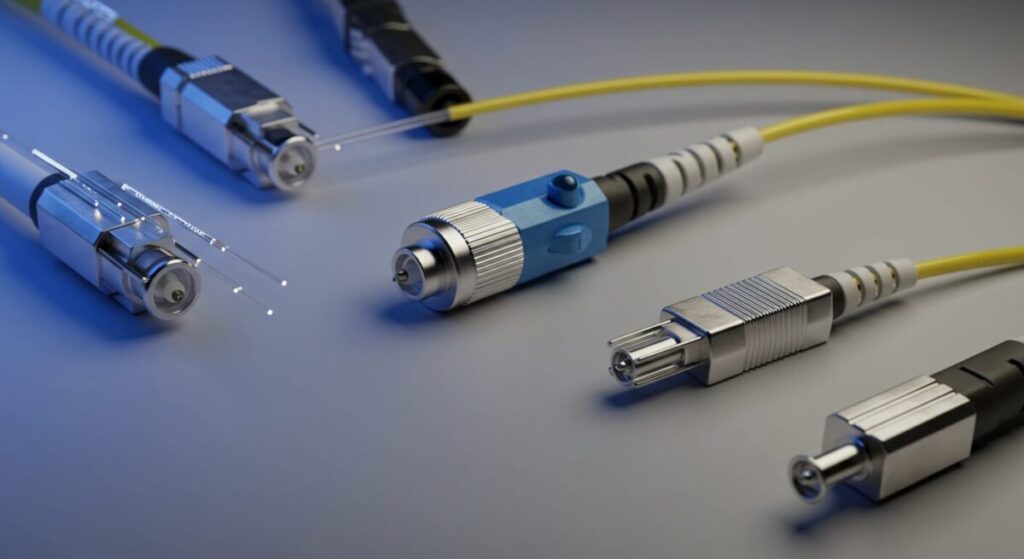
✅概要
- ファイバーケーブルを用いて光信号を送受信するセンサー。
- 狭い場所や小型機器に適用可能。
🔍用途
- 微小部品の検出。
- 狭い空間での物体検知。
- 高速ラインの安定検出。
📌ファイバーセンサーの活用例
- 電子部品の有無確認
- 小型基板上の微小な部品の有無を確認。
- 狭いスペースに対応可能なため、精密機器の生産に適しています。
- 高速ラインでの物体検知
- 高速で流れるライン上の製品を正確に検出し、不良品を素早く排除します。
マイクロフォトセンサ
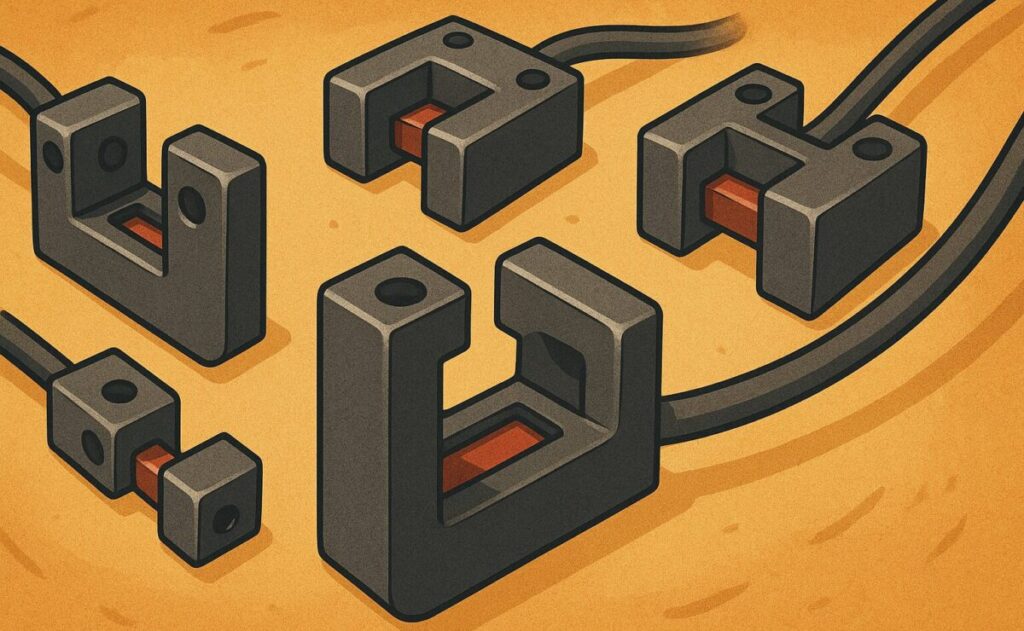
✅概要
非常に小型の光電センサーで、狭い空間や微細な対象物を検出可能。
🔍用途
- 精密機械内での部品検出。
- 電子部品の位置確認。
- ロボットアームの細部制御。
📌マイクロフォトセンサの活用例
- 精密部品の位置決め
- 小型機械内でマイクロフォトセンサを使い、細かい部品の位置を正確に確認。
- 作業の精度が向上します。
- ロボットの指先検出
- ロボットアームの指先に設置して、部品の把持を高精度に制御。
- 組立作業の効率を向上させます。
エリアセンサ・ライトカーテン
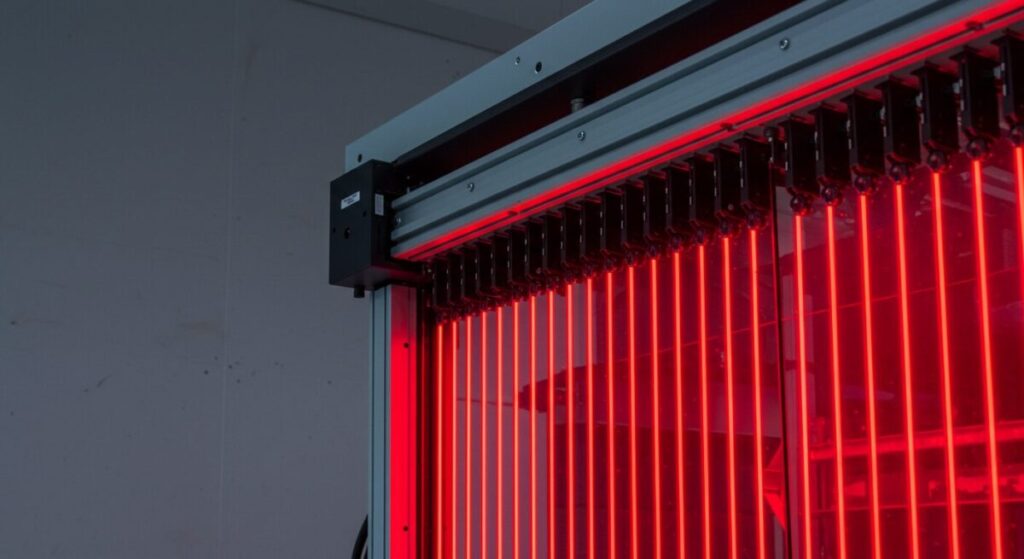
✅概要
複数の光電センサーを並べたもので、広い範囲を一括して監視可能。
🔍用途
- セーフティガードとしての人員検出。
- 製品ラインの異常検出。
- 高速移動体の位置検知。
📌エリアセンサの活用例
- 機械安全対策
- 工作機械の危険ゾーンにエリアセンサを配置。
- 作業者が手をかけた瞬間に機械の動作を停止させ、事故を防ぎます。
- 物流ラインでの欠品検知
- 物流ラインに置かれた製品が規定のエリア内に正しく配置されているかをエリアセンサで確認。
- 不良品や欠品を即座に検出します。
リミットスイッチ
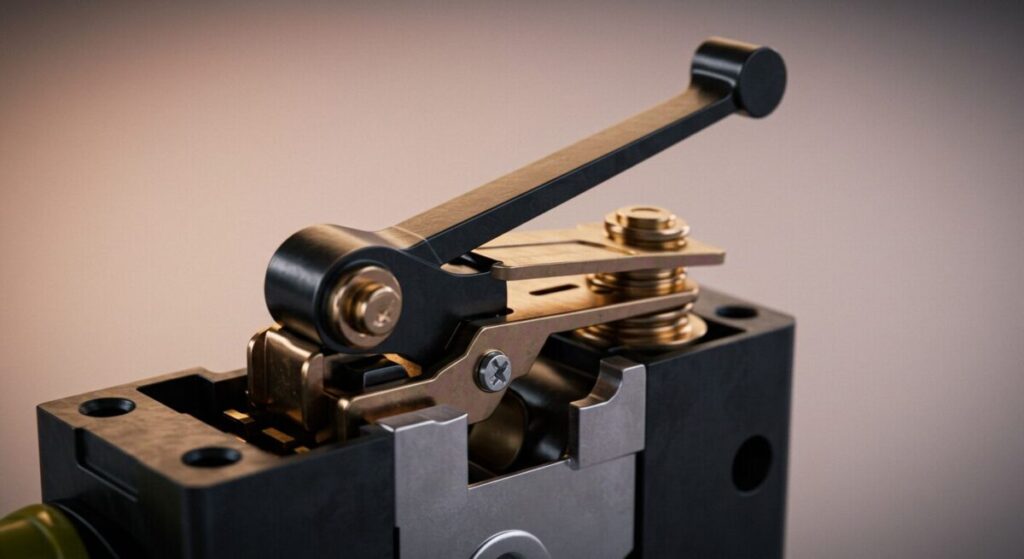
✅概要
機械的な接触によって対象物を検出するスイッチ型センサー。
🔍用途
- スライドテーブルの終端位置の検出。
- 工作機械の安全装置。
- 搬送機の停止位置の確認。
オートスイッチ(エアシリンダ)
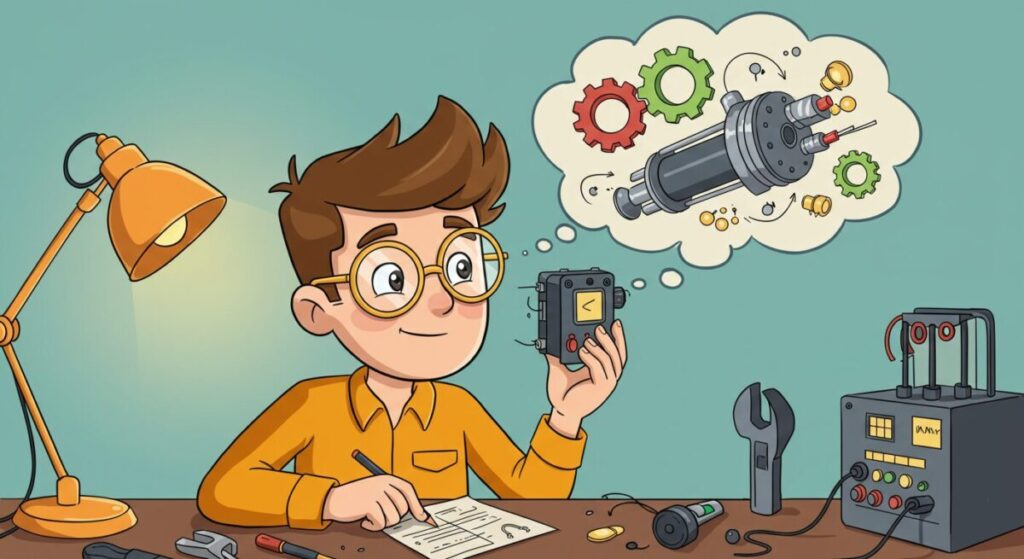
✅ 概要
- エアシリンダーのピストン位置を磁石で検出するセンサー。
- シリンダー本体に取り付け、ピストンに内蔵された磁石の位置を検出します。
- 有接点タイプと非接点タイプがあり、検出方法や応答性、耐久性が異なります。
🔍 用途
- エアシリンダーの動作確認
- ストローク端の検知による制御信号出力
- 自動装置におけるタイミング制御や安全確認
📌 オートスイッチの活用例
- 自動組立ラインでの位置検出
- 部品挿入工程で、前進端にオートスイッチを取付けて、ピストンが正しく動作したかを確認。
- 検出信号がなければ装置を一時停止し、不具合を防止します。
- 多軸装置のシーケンス制御
- 複数のシリンダーを使う自動装置において、オートスイッチを使って順序制御を実現。
- 前工程のシリンダーが所定位置に達したことを検出してから、次の動作に進めるようにします。
ロードセル
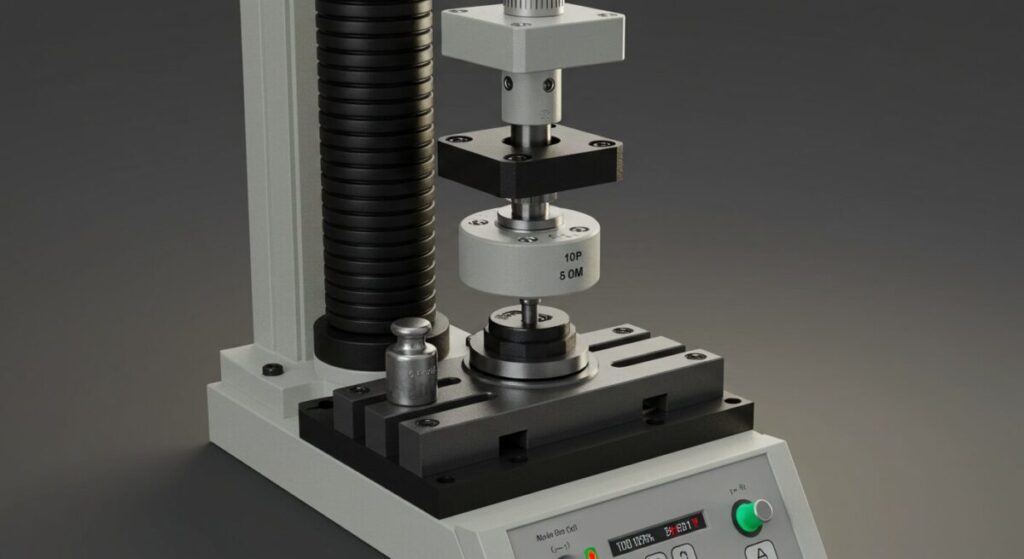
✅概要
- 荷重や力を検出するためのセンサー。
- ひずみゲージを利用して力を電気信号に変換。
🔍用途
- 産業用の計量装置。
- 機械の締付力の監視。
- 圧縮や引張試験機。
📌ロードセルの活用例
- 重量計の計量システム
- 食品工場でロードセルを使い、原材料の正確な計量を実現。
- 一定の重量以上になると自動的にラインを停止して材料を補充します。
- プレス機の力制御
- 金属加工のプレス機にロードセルを設置し、加工時の圧力をリアルタイムで監視。
- 過剰な圧力がかかった場合、自動的に動作を停止します。
エア圧力センサー
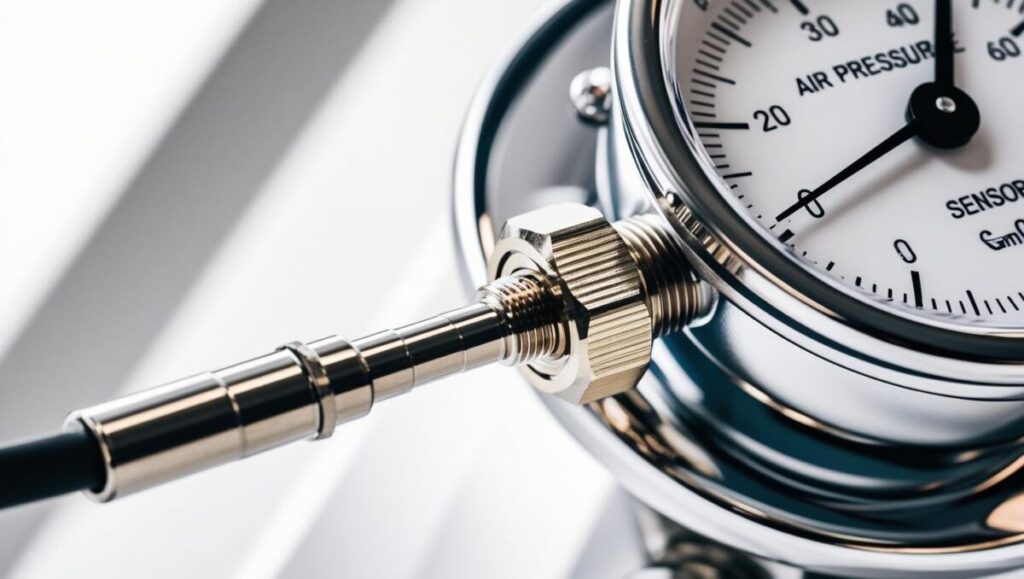
✅概要
- 圧縮空気の圧力を検出するセンサー。
- 圧力範囲の設定やモニタリングに使用。
🔍用途
- 空気圧システムの状態監視。
- 生産ラインのエア漏れ検出。
- 空気圧駆動装置の安全管理。
📌エア圧力センサーの活用例
- エア供給ラインの漏れ検知
- 製造ラインでエア圧力センサーを用いて圧力を監視。
- 漏れが発生した場合に異常を検知して、早期に修理対応を行います。
- 空気圧駆動装置の安全監視
- 空気圧シリンダーの動作状態をセンサーでモニタリングし、圧力の低下等以上があった場合はシステムを停止させます。
流量センサー
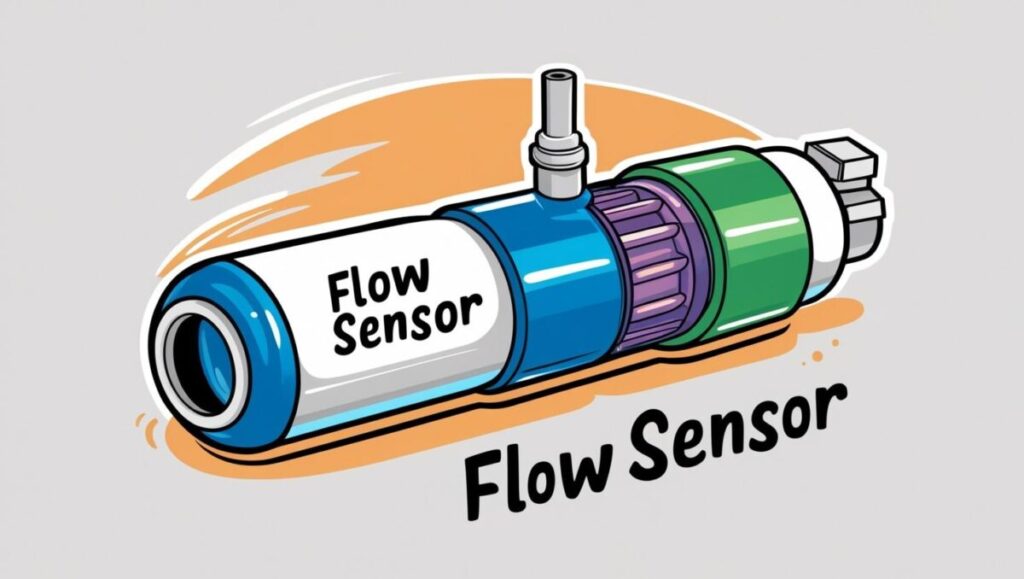
✅概要
- 液体や気体の流量を測定するセンサー。
- 熱式や超音波式などの方式があります。
🔍用途
- 工業プラントでの流量管理。
- 冷却水や潤滑油の供給量測定。
- ガス供給システムのモニタリング。
📌流量センサーの活用例
- 冷却装置の水流監視
- 機械設備の冷却装置において、流量センサーを使って冷却水の流れを監視。
- 水流が不足した場合、警告を出して機器の過熱を防ぎます。
- 薬液の供給量管理
- 化学工場で流量センサーを使用して、薬液の正確な供給量を管理。誤差を最小限に抑えます。
センサーの出力・仕様の理解
「A接点・B接点」センサー接点動作の違いと選定ポイント
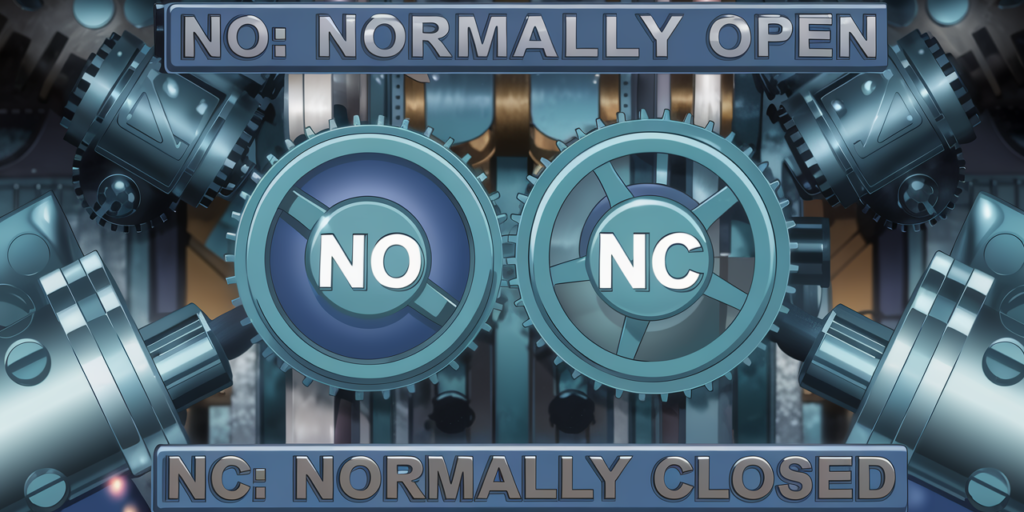
✅ A接点(常開)とB接点(常閉)とは?
- A接点(NO):通常は開回路。検出時に閉じて出力ON。
→ 用途:動作検知、機械停止、アラーム用など - B接点(NC):通常は閉回路。検出時に開いて出力OFF。
→ 用途:安全監視、異常検知、非常停止ボタン
✅ 選定ポイント
- 通常はOFFで、動作時のみONにしたい → A接点
- 断線検出や安全監視をしたい → B接点
光電センサー:ライトオンとダークオンの違い
✅ 【ライトオン】
- 光が当たっているときに出力ON
- 例:
- 透過型:物体がないときにON
- リフレクタ型:反射光を受けてON
- 拡散反射型:物体に反射してON
✅ 【ダークオン】
- 光が当たっていないときに出力ON
- 例:
- 透過型:物体が光を遮るとON
- リフレクタ型:光が遮られるとON
- 拡散反射型:背景の反射がなくなるとON
✅ 選定ポイント
- 光を受けてONにしたい → ライトオン
- 光を遮ってONにしたい → ダークオン
→ 検出対象の有無・設置環境に応じて選ぶことが重要。
近接センサー:NO(ノーマリーオープン)とNC(ノーマリークローズ)
✅ NO(A接点と同等)
- 通常:OFF
- 検出時:ON
→ 動作の検知用途
✅ NC(B接点と同等)
- 通常:ON
- 検出時:OFF
→ 異常検知・断線検出
総合的な選定ポイント
項目 | NO / A接点 / ライトオン | NC / B接点 / ダークオン |
---|---|---|
通常状態 | OFF(開) | ON(閉) |
動作時 | ON(閉) | OFF(開) |
安全性 | 低め(断線検知しにくい) | 高め(断線検知しやすい) |
主な用途 | 検出による動作トリガー | 異常監視・非常停止 |
NPN出力とPNP出力の基礎と配線ミスの注意点
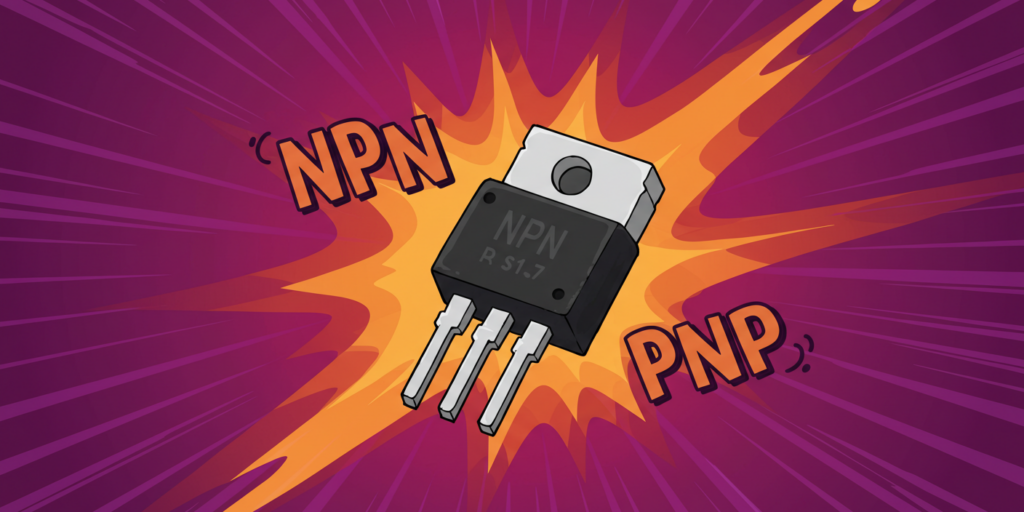
NPN出力とは
- 方式:出力端子が0V(GND)に接続される「シンク出力(電流を吸い込む)」。
- 動作:検出時に0Vを出力。
- 特徴
- シンプルな回路設計が可能。
- 日本では主流(既存設備との互換性・歴史的背景)。
PNP出力とは
- 方式:出力端子が+電源に接続される「ソース出力(電流を供給する)」。
- 動作:検出時に+電源を出力。
- 特徴
- 欧州規格に適合。
- 電圧出力で直感的に扱いやすい。
NPNとPNPの比較表
項目 | NPN出力 | PNP出力 |
---|---|---|
動作方式 | シンク(電流を吸い込む) | ソース(電流を供給する) |
検出時の出力 | 0V(負極) | +電源(正極) |
外部回路の抵抗 | プルアップが必要 | プルダウンが必要 |
主流地域 | 日本・アメリカ | 欧州・アジアの一部 |
⚠️ NPN/PNPを間違えて接続すると?
- 動作不良:期待する信号が得られず、センサーや装置が正常動作しない。
- 故障リスク:短絡や過電流により、センサー・入力機器が損傷する可能性あり。
- トラブル例
- センサーやPLCが異常発熱。
- 意図しないタイミングでON/OFF。
- 生産ラインの停止など大きな損害も。
✅ 正しい接続・配線をするための対策
- 設計段階で仕様確認:センサーやPLCの仕様を図面に明記。
- 現場での確認手順:配線作業前にセンサーの型番・出力方式を再確認。
- ミス防止の工夫
- 出力方式で配線色を分ける。
- センサーにNPN/PNPのラベルを貼付。
- 設備全体で出力方式を統一する(標準化)。
🔍 選定時のポイント
- 接続機器の仕様を確認(NPN or PNP対応か)
- 設備の地域性(日本はNPNが基本)
- ノイズ耐性など環境条件も考慮
NPNとPNPはセンサー出力方式の基本であり、配線ミスが大きなトラブルに直結します。
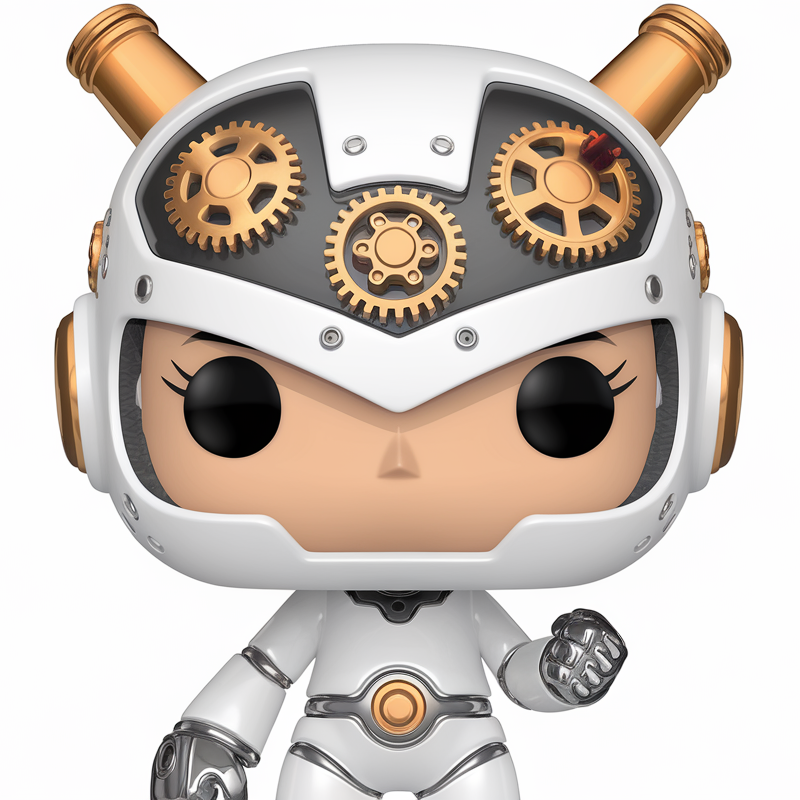
選定時は制御機器の仕様を確認し、仕様に適合した出力方式を選ぶことが重要です。
センサーの応答速度と応答周波数
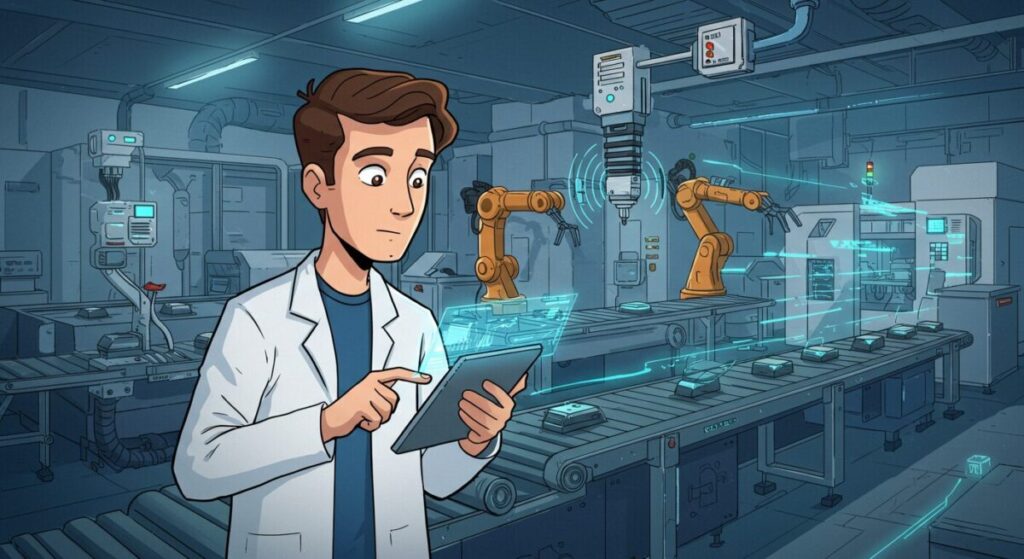
応答速度とは?
- 定義:検出対象が変化してから、センサーが反応するまでの時間。
- 単位:ms(ミリ秒)やμs(マイクロ秒)で表される。
- 重要性:応答が遅いと、ワークの見逃し・誤動作・装置クラッシュなどの原因になる。
✅ 応答速度の具体例
- 搬送ライン:部品が高速で流れる場合、応答が遅いと誤検出や見逃しが起こる。
- シリンダー制御:タイミングズレで機械が誤動作することも。
✅ センサーの応答速度目安
センサー種別 | 応答速度目安 | 用途例 |
---|---|---|
近接センサー(高性能) | 約1〜5ms | 金属部品検出など |
光電センサー | 約0.5〜1ms | 高速カウント |
オートスイッチ(有接点) | 約2〜5ms | エアシリンダー制御 |
オートスイッチ(非接点) | 約0.5〜1ms | 高速応答が必要な場合 |
応答周波数とは?
- 定義:センサーが1秒間に何回オン・オフを検出できるか(単位:Hz)。
- 目安:
- 一般近接センサー:200〜500Hz
- 高速タイプ:1kHz〜5kHz
- 静電容量式:10〜100Hz(遅い)
✅ 応答時間との違い
指標 | 応答周波数 | 応答時間 |
---|---|---|
意味 | 1秒間の検出回数 | 1回の検出にかかる時間 |
単位 | Hz | ms |
応答周波数が重要な場面
- 高速コンベアでのワーク検出
- 回転体の回転数検出(シャフトやローラーなど)
✅ 設計時のチェックポイント
- 1秒間のワーク通過数を見積もる
- センサ仕様書で「応答周波数」確認
- 実運用より2〜3倍の余裕を持つのが理想
✅ 応答遅延によるリスク
- 検出ミスや見逃し
- タイミングずれやカウントミス
- 安全機構の遅れや装置不良
✅ 応答速度を考慮した設計のポイント
- センサー仕様(応答時間・応答周波数)の確認
- 実際の動作速度とのバランス調整
- ノイズ対策(デジタルフィルタ等)も考慮
センサー選定では、検出対象の速度に応じた応答性能(応答時間・応答周波数)を意識することがトラブル防止のカギ。
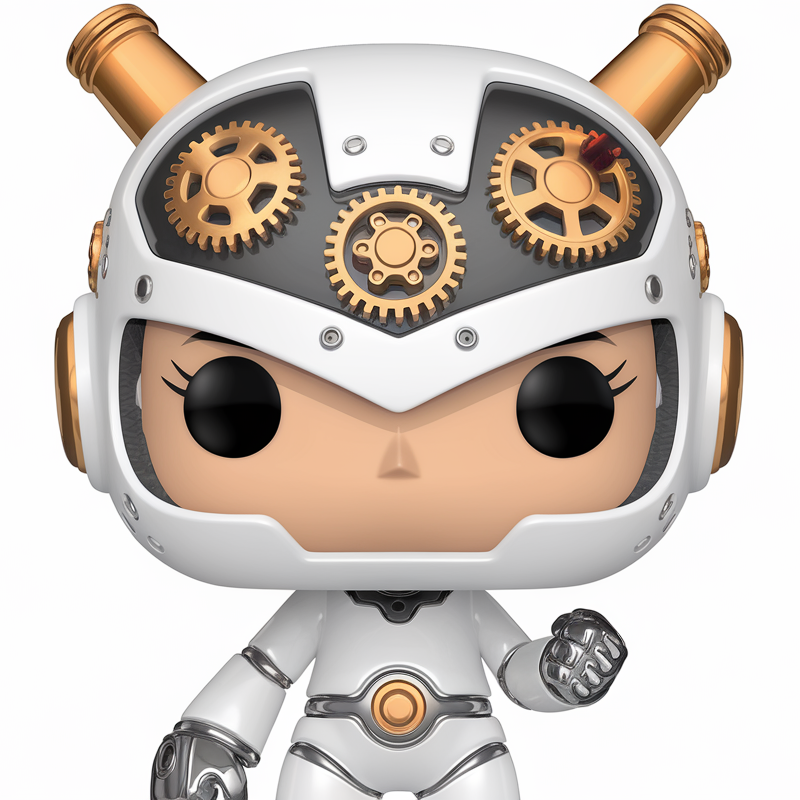
「何を・どれだけの速さで検出したいか」を明確にし、余裕を持ったセンサーを選定しましょう。
設計・実装時の注意点
センサー実装における注意点
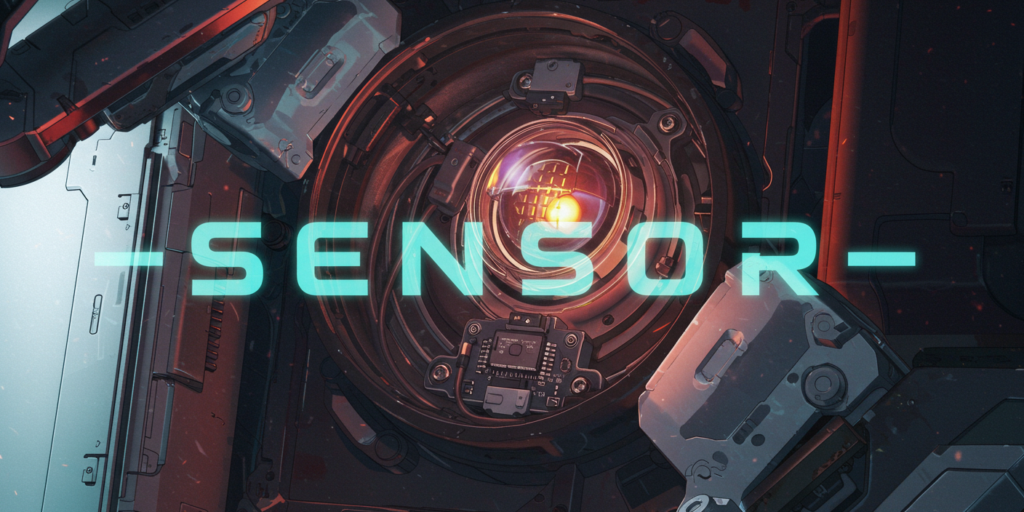
設置場所の選定
- 感度の最適化
センサーは対象物との距離や角度により感度が変化するため、取扱説明書に準拠した適正な距離と向きで設置する必要がある。
例:光電センサーは近すぎると誤検出、遠すぎると感度低下。近接センサーは金属の影響を受けやすいため、スペーサー等の工夫が必要。 - 環境条件の考慮
温度、湿度、振動、汚れなどが性能や寿命に影響するため、IP規格を考慮し、防水・防塵対応製品を選定。
電磁波干渉(ノイズ)対策
- 影響と不具合例
電磁波干渉により、ノイズ混入・誤動作・信号途切れ・感度低下が発生する。 - 主な発生源
Wi-Fi機器、インバーター、モーター、高電圧機器、雷など。 - 対策例
1. シールドケーブルの使用と正しい接地
2. 接地(アース)の徹底
3. フィルタ回路(フェライトコア等)の挿入
4. 配線方法の工夫(電源線と信号線を分離、直角交差)
5. 干渉源からの距離を取る、金属シールドを追加
6. ノイズ対策機器(ラインフィルタ等)の活用 - 設計段階での工夫
ノイズ耐性のあるセンサー選定、現場での電磁波試験の実施により信頼性を確保。
メンテナンス性の確保
- 交換しやすい設置
工具が届きやすく、位置調整が簡単なようにガイドや目盛付き固定具を活用。 - 定期点検と清掃
センサーの種類や使用環境に応じて、検出面の清掃や校正をスケジュール化。
センサーの校正
- 校正の目的
正確な測定と品質保証、規格対応のために定期的な校正が必須。 - ロードセルの校正例
標準分銅などを用いて、無負荷→段階的荷重→出力測定→校正曲線作成の流れで実施。
センサーの性能を最大限に発揮するには、適切な設置環境・ノイズ対策・メンテナンス性・定期的な校正が不可欠。
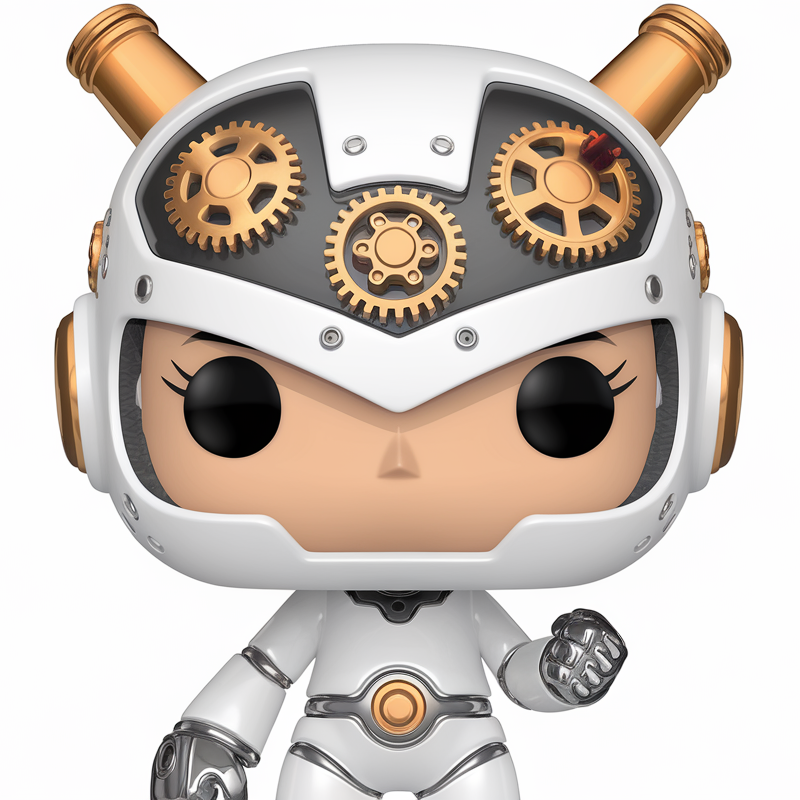
信頼性の高いシステム構築のためには、設計段階からこれらを考慮することが重要です。
センサーにおけるチャタリングとは?
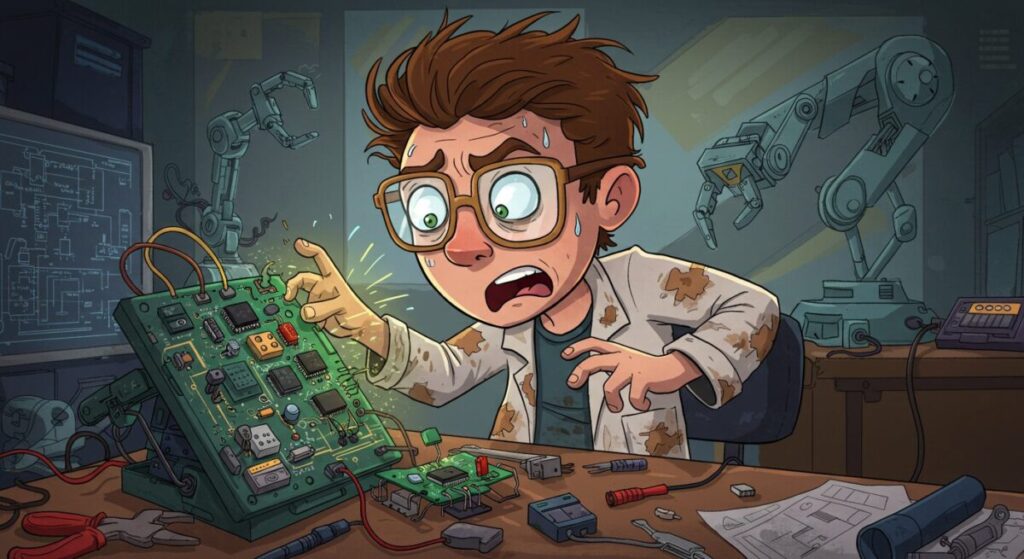
チャタリングとは?
センサーやスイッチがオン/オフを切り替える際に、一瞬の間に信号が何度も変化する現象のこと。
この“信号のバタつき”が原因で誤作動や誤カウントを引き起こす。
✅ 主な発生原因
- 機械的要因:スイッチの接点が跳ねる、可動部がバウンドする
- 電気的要因:ノイズ、電源の揺らぎ
- 環境要因:振動、金属粉や油の付着
✅ チャタリングが起こるセンサー
センサー種類 | チャタリングの可能性 |
---|---|
機械式スイッチ | 非常に高い |
近接センサ | 低いが発生可能 |
光電センサ | 反射具合によってはあり得る |
オートスイッチ(有接点) | 発生する可能性あり |
オートスイッチ(非接点) | 基本的に少ない(内部で処理済) |
✅ チャタリングによるトラブル
- 誤カウント(1つを2回カウント)
- PLCが誤信号を処理
- モーターやシリンダーの誤作動
- 安全機能の誤動作リスク
✅ 対策方法
🔧 ハード的対策
- 非接点センサーの使用
- コンデンサやバッファ回路で信号平滑化
- 感度・取付位置の調整
💻 ソフト的対策(PLC・マイコン)
- ON時間のフィルタ処理(例:20ms以上で有効)
- デバウンス処理(一定時間変化がなければ信号確定)
- 信号一致のロジックでフリッカ除去
✅ 実例と効果
- 問題:1つのワークが2回カウントされる
- 対策:非接点センサーに変更し、PLC側で0.05秒未満の信号を無視
- 効果:誤カウント解消!
✅ 初心者向けポイント
- チャタリング=“信号のガタつき”と覚える
- 初めての設計では「非接点+タイマ処理」が安心
- トラブル時は「チャタリングかも?」と疑ってみよう
チャタリングはセンサー誤動作の大きな要因。
非接点センサーの選定、取り付け工夫、ソフトでの信号処理などの対策が重要。
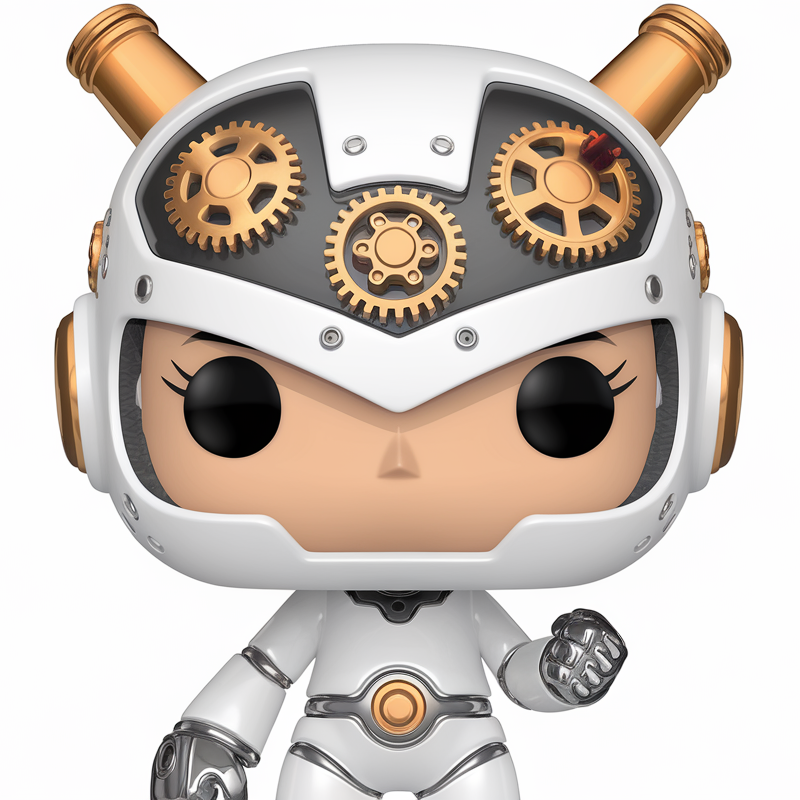
問題が起きたときは「チャタリングを疑う」ことが解決の第一歩。
まとめ|センサーを理解して、より精密で安全な設計を!
センサーは単なる部品ではなく、制御・安全・品質管理を支える神経のような存在です。
種類や原理だけでなく、配線方式・応答性・設置位置・干渉対策なども理解しておくことで、トラブルを防ぎ、信頼性の高い設計が実現できます。
本まとめページをブックマークして、いつでもセンサー設計に役立ててください!
コメント