機械設計において、2つの部品を高精度に位置合わせして組み付けるためには、適切な「位置決め方法」を選定することが重要です。その中でも特に多用されるのが、“インロー”による位置決めです。
この記事では、インローとは何か、その仕組みや目的、メリット・デメリット、そして設計上の注意点までを、初心者にもわかりやすく解説していきます。
インローとは?
インローの定義
「インロー」とは、一方の部品に設けた凸部(ボス)を、もう一方の部品の凹部(穴)に差し込んで位置決めをする構造のことです。
いわば、“はめ合わせ”による位置決めです。円筒形が多く、ピッタリとはまるように設計されることで、部品同士のずれを防ぎます。
なぜインローを使うのか?
インローは以下のような目的で使用されます。
✅ 部品同士の位置決め精度を確保
✅ 組み付け作業時のズレを防止
✅ ねじ位置や軸の芯合わせの補助
✅ 溶接・接着・ねじ止めの際のガイド機能
✅ 応力の分散(広い面で接触させることで応力集中を抑える)
簡単に言えば、“ズレずに正しい場所に部品を組み付ける”ための設計手法の一つです。
インローの構造と種類
インローの構造は基本的に「ボス+穴」ですが、目的や設計方針によっていくつかのバリエーションがあります。
円筒インロー
- 丸いボスと穴で構成
- 位置決め精度が高く、組み付けやすい
- 通常はH7/h6やH7/g6などのはめあい公差で設計
段付きインロー
- 段付き形状にすることで、プレートの側面と溝の側面で面接触
- 垂直方向の位置決めも同時に可能(高さ方向のガタを抑える)
キー溝付きインロー
- 位置決めの自由度を一方向に限定したい場合に使用
- 応力を逃がしたいときや、差し込み方向を限定したいときに有効
インローは位置決めだけじゃない!せん断荷重やトルクも受け持つ設計ポイントを解説
機械設計において「インロー」と聞くと、真っ先に部品同士の位置決めを連想する方が多いでしょう。確かにそれが基本的な用途ですが、実はインローはせん断荷重やトルクを受ける構造設計にも有効です。
本項では、インローの基本機能を押さえつつ、力を受け持つ構造要素としての活用方法、設計上の注意点、他の要素との役割分担など、初心者にもわかりやすく解説します。
インローとは?基本の再確認
インローとは、一方の部品に設けた凸形状を、もう一方の部品の凹形状に差し込むことで、部品同士を正確な位置関係で組み合わせる構造です。
代表的な用途は以下の通り。
✔ 部品同士の位置決め
✔ 組立作業のガイド
✔ ネジ位置の確保・芯ずれ防止
ここまでは位置決め部品としての役割ですが、設計の工夫次第でせん断荷重やトルクの伝達手段としても活用できます。
インローが受け持てる力の種類とは?
インローは、設計次第で以下のような機械的な力に耐えることができます。
せん断荷重
せん断荷重とは、接触面に対して平行方向に加わる力のことです。
🔍 例)
- 上プレートに水平荷重がかかり、下プレートとずれようとする
- ボルトでは支えきれない場合、インローがせん断ストッパーとして機能
👉 この場合、インローが「ストッパー」として滑り防止の役割を果たします。
トルク(回転方向の力)
トルクとは、軸を中心に部品が回転しようとする力のこと。
🔍 例)
- モーターやギヤボックスのハウジング
- ネジだけで回転を防ぐには限界がある
👉 インローによって、凸と凹が干渉して回転を阻止することで、トルク伝達が可能になります。
インローがせん断・トルクを受け持つ場面の例
以下のような設計で、インローは重要な役割を果たします。
✅ モーターの取付ベース
- 高トルクを発生するモーターの取付では、取付ねじだけではトルクに対して弱い
- インローによって、「回転方向のズレ」を抑え、ねじの負荷を軽減
✅ 精密プレートの重ね構造
- 上下プレート間で水平方向にずれる力(せん断)を受ける場合、インローがストッパーの役割
- 特に、ねじ緩みや微振動でズレるリスクがある場合に有効
✅ ギヤボックスや減速機のフランジ取付部
- 回転力の伝達を「ねじの摩擦力」だけに依存すると危険
- インローで回転力を直接受け、ねじを「固定だけ」に分離できる
インローで力を受け持たせる設計のポイント
材料の強度に注意
インローが力を受ける場合、その接触面が応力集中するため、使用する材料の強度が非常に重要です。
- 軟質材料(アルミや樹脂)ではへたりや摩耗が起こりやすい
- 鋼材(S45C、SCMなど)で、表面焼入れを検討するのも有効
面接触を意識する
- 接触面が小さいと、局所的に高応力となり変形やかじりの原因に
- 可能であれば「面接触」や「段付きボス」で接触長さを確保すると良い
公差設定とガタの管理
- インローがトルクやせん断力を受け持つ場合、ガタがあっては意味がない
- 中間ばめ(m6/H7など)~圧入(p6/H7)を選択し、ガタなし+着脱性のバランスを検討
熱膨張の考慮
- 異種材同士(例:アルミ+鋼)のインロー構成では、温度変化によるすきまの変化に注意
- 高温時のガタ発生や、低温時のかじり・割れなどのリスクあり
インロー vs 位置決めピン:どちらが力に強い?
比較項目 | インロー(ボス) | 位置決めピン |
---|---|---|
位置決め精度 | 中〜高 | 非常に高 |
せん断荷重耐性 | 面接触で分散される | 線接触のため局所応力大 |
トルク伝達 | 可(特に円筒で有効) | 基本的に不可 |
脱着のしやすさ | 設計次第(すきまあり) | 基本的にやや固め |
位置決めピンは高精度な位置決めに適すが、大きな力を受ける用途にはインローの方が有利です。
インローでの力の分担:ねじやピンとの併用がベスト
インロー単体で全荷重を受けるのではなく、ねじ・ピンとの併用設計がベストです。
🔍 例)
- トルクをインローで受け、ねじは位置維持と締結のみ
- せん断荷重をインローとピンで分担
このように、役割を分離することで、設計の信頼性と保守性が向上します。
インローは「力の設計」にも使える!
インローは単なる位置決めのための構造に留まらず、以下のような構造強度を支える重要な要素としても活用できます。
✔ せん断荷重のストッパー
✔ トルクの伝達経路
✔ ねじやピンの負担軽減
✔ 位置決めと力の両立
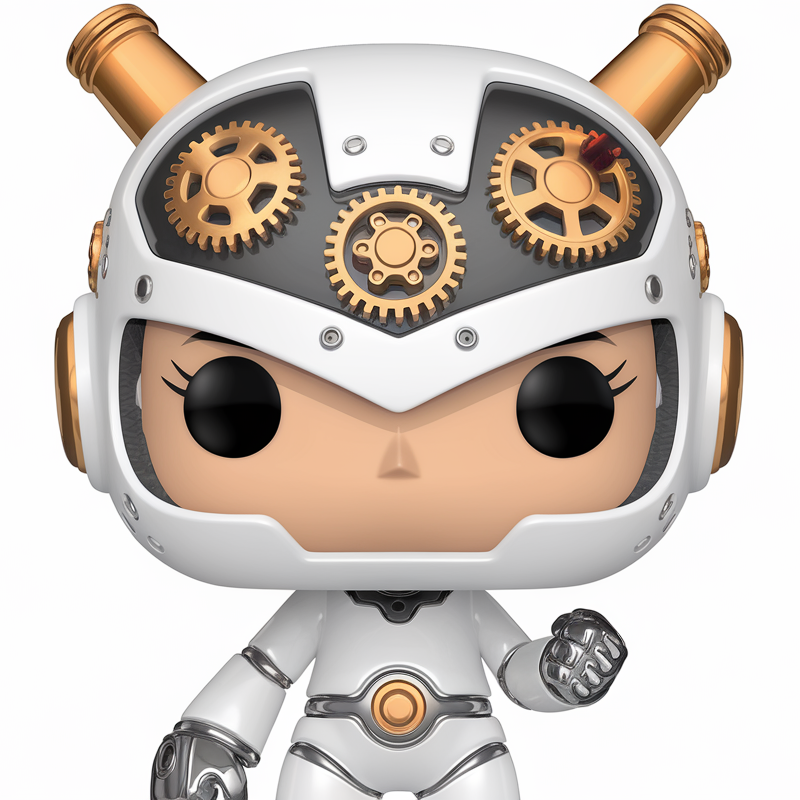
設計においては、「インローはただの穴とボスではなく、力の流れを考えた設計の一部である」と捉えることが重要です。
精度・強度・作業性のバランスを見極めながら、最適なインロー設計を行っていきましょう。
はめあい公差とクリアランス
インロー設計で非常に重要なのが「はめあい」の設定です。
クリアランスを持たせる(すきまばめ)
- g6/H7やh7/H7などが代表例
- 組み立てやすく、脱着も簡単
- 位置決め精度はそこそこ
中間ばめ
- m6/H7やn6/H7などを用いる
- 手では入らず、軽くたたいて入れる感じ
- 高精度かつガタが出にくい
圧入(強めのしまりばめ)
- p6/H7やs6/H7など
- 取り外し不可なほどしっかり固定される
- 高剛性を要する箇所や回転防止などに利用
組立性を考慮し、片側は位置決め、もう片側はクリアランスを設けると、歪みを防げて組み付けもスムーズです。
インロー位置決めの実用例
🔍 モーターと取付板の組み付け
- モーターのボス部分を取付板に設けた穴に差し込み、ねじ止め
- 回転中心の芯ずれを防止できる
🔍 精密筐体の組み合わせ
- 位置合わせ用にインロー形状を設けることで、ねじを締める前からピタリと位置決め
- 製品の組み立て作業を簡便化・標準化できる
🔍 溶接や接着の前処理
- 接合部品のガイドとしてインロー形状を活用
- 組み立てジグの簡略化にもつながる
設計上の注意点
インローは便利な機構ですが、設計時には以下のような点に注意しましょう。
精度管理と加工公差の設定
- インロー部ははめあい公差の影響を強く受ける
- 特に位置決め精度が重要な場合は、研削仕上げや仕上げ公差の指定が必要
熱膨張の考慮
- 材料の組み合わせによっては、使用環境の温度変化でクリアランスが変化
- 高温環境では「しまりばめ」が「きつすぎる」状態になることもある
組立工程との整合性
- 現場作業者が正しくインローにはめ込める構造かを検討
- 面取り・リード角・案内面の設計で、作業性を高めることが可能
位置決めと固定の分離
- インローはあくまで「位置決め」であり、「固定」はねじやピンで行う
- 固定と位置決めを一体化すると、作業性や信頼性の低下につながる
インローと他の位置決め手法との比較
位置決め方法 | 精度 | 脱着性 | 使用頻度 |
---|---|---|---|
インロー | 高い | 良い | 非常に多い |
位置決めピン | 非常に高い | 中程度 | 多い |
ダボ・ガイド | 中程度 | 良い | 一部用途で使用 |
加工合わせ | 低い | - | 非推奨 |
インローは、精度と作業性のバランスに優れた方法であり、特に量産品の組み立てなどで重宝されます。
まとめ
インローは、機械設計における代表的な位置決め手法であり、
✅ 加工精度の確保
✅ 組み付け作業の安定
✅ ワークの芯合わせやズレ防止
といった多くのメリットがあります。設計時にははめあい公差・組立性・熱変形・固定手段などにも注意を払い、信頼性の高い機構を目指しましょう。
「インローはただの穴とボスではなく、設計の工夫と精度管理の結晶」と言っても過言ではありません。ぜひ、設計に活用してみてください!
コメント