機械設計において、軽量化は装置の性能や効率に大きく関わる重要な要素です。特に、可動部や搬送装置などでは、部品の「重さ」が装置の加減速性能、消費電力、そして耐久性にまで影響します。
そこでよく使われるのが「アルミ合金」と「樹脂(プラスチック)」です。この2つはどちらも軽量素材として知られていますが、特性や適した用途は大きく異なります。
この記事では、アルミ合金と樹脂の違いと使い分けのポイントを初心者の方にもわかりやすく解説します。
アルミ合金とは?
アルミ合金は、アルミニウムに他の金属(銅、マグネシウム、シリコンなど)を加えて、強度や耐久性を向上させた金属材料です。代表的なものに「A5052」や「A7075」などがあります。
アルミ合金の特長
✅ 軽い(比重:約2.7)
✅ 強度が高い(特にA7075などの高強度合金)
✅ 耐食性がある(錆びにくい)
✅ 加工性がよい(切削、曲げ、穴あけなど)
✅ 見た目がきれい(アルマイト処理で美観UP)
アルミ合金の注意点
🚫 鉄と比べてコストが高い
🚫 溶接には工夫が必要(材質により溶接性に差がある)
🚫 高温環境には不向き(熱伝導率は高いが、強度が下がる)
樹脂とは?
樹脂とは一般的にプラスチック素材のことを指し、種類も多く、特性も幅広いです。代表的なものに「POM(ポリアセタール)」「MCナイロン」「ABS」などがあります。
樹脂の特長
✅ 非常に軽い(比重:1.0〜1.5程度)
✅ 加工が容易(切削、射出成形が可能)
✅ 電気絶縁性が高い(電気部品に最適)
✅ 摺動性がよい(摩耗しにくい)
✅ 腐食しない
✅ 自己潤滑性がある(潤滑油なしでも滑る)
✅ 静音性に優れる
✅ 耐摩耗性に優れる種類も多い(POM、MCナイロンなど)
樹脂の注意点
🚫 強度が低い(金属と比較して)
🚫 熱に弱い(種類によって耐熱温度は異なるが、100℃以上で変形することも)
🚫 紫外線や薬品に弱い素材もある
🚫 寸法安定性が低い(湿気や温度で膨張・収縮することがある)
比較表:アルミ合金 vs 樹脂
特性 | アルミ合金 | 樹脂 |
---|---|---|
比重 | 約2.7 | 約1.0〜1.5 |
強度 | 高い | 低い(種類により差) |
加工性 | 良い | 良い |
耐食性 | 良い | 良い(ただし薬品に注意) |
耐熱性 | △(中程度) | ×〜△(低〜中程度) |
コスト | 中〜高 | 中程度 |
寸法安定性 | 良い | 種類によっては不安定 |
見た目仕上げ | 美しい(アルマイト可) | 普通 |
使い分けの考え方
では、どのようにアルミ合金と樹脂を使い分ければ良いのでしょうか?
アルミ合金が適しているケースとは?
一定の強度と耐久性が求められる部品への最適な選択
機械設計において材料を選ぶ際、「軽いからアルミ」「安いから鉄」といった漠然とした選び方をしていませんか?
実際には、材料の特性を理解し、設計の目的に応じた選定をすることが非常に重要です。
本項では、「アルミ合金が適しているケース」として、特に以下の2つの用途に注目して解説します。
✅ 一定の強度が必要な部品
✅ 耐久性が必要な可動部品
アルミ合金は軽さだけでなく、高い比強度(強度/重量)や耐腐食性など、鉄とは異なる優れた特性を持っています。それぞれのケースについて、具体例とともにわかりやすく説明します。
一定の強度が必要な部品に最適
装置のフレーム、ブラケット、アームなど、自重や外力を支える構造部品には、一定以上の強度が求められます。鉄(SS400)は強度はありますが重く、可動部に使うと負荷が大きくなります。
アルミ合金であれば、強度を保ちながら重量を大幅に削減でき、装置全体の軽量化と省エネ化につながります。
例1:検査装置や自動機のフレーム
- アルミフレーム(ミスミなど)は軽量かつ強固
- ボルト締結が容易で、組み換えや調整も簡単
- ステンレスに比べてコスト・加工性のバランスが良好
例2:ロボットアームのベースプレート
- 重量を抑えることでアクチュエータの負荷が低減
- 振動特性も良く、高速動作に対応
耐久性が必要な可動部品にも適している
可動部には、繰り返し応力や摩耗、疲労破壊への耐性が必要です。アルミ合金は種類にもよりますが、適切に選定すれば鉄に劣らない耐久性を発揮します。
特に、A7075のような超々ジュラルミン系合金は、強度や疲労特性が非常に高く、航空機や高精度部品にも使われます。
例1:リニアアクチュエータの移動ステージ
- 可動部をアルミ化することで、駆動力の低減や応答性の向上が可能
- 表面をアルマイト処理することで耐摩耗性・潤滑性を向上
例2:ガイドレールのスライダー部
- 高精度な加工が可能で、組立精度も高い
- 腐食による摺動不良やメンテナンスコストを低減
アルミを使う際の注意点
🚫 高温環境には弱い
- 150℃を超えるような環境では強度が低下するため、要検討
🚫 材質によっては溶接が難しい
- A5052は比較的溶接性が良いが、A7075などは溶接に不向き
🚫 表面処理(アルマイトなど)が必要な場合あり
- 耐摩耗性や絶縁性が必要な場合は、アルマイト処理を検討
アルミ合金は「強さ×軽さ」のバランスが決め手!
アルミ合金は単に軽いだけでなく、設計に必要な強度や耐久性を保ちながら軽量化できる優秀な材料です。
- 構造部品で強度が必要な場合
- 繰り返し動く可動部で耐久性が必要な場合
このような場面では、鉄ではなくアルミ合金の採用を積極的に検討する価値があります。
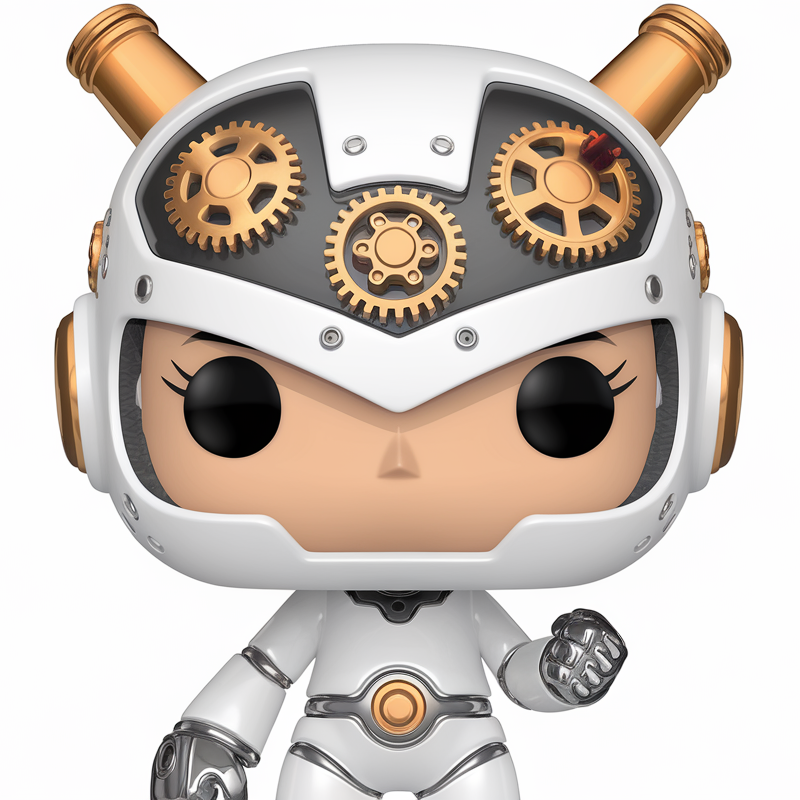
設計の初期段階で材料の特性を把握し、部品ごとに最適な選定を行うことが、コスト・性能・耐久性をバランスよく満たすカギとなります。
樹脂が適しているケースとは?
摺動部品における摩耗・潤滑の課題を解決する材料選定
機械設計において、つい「強度が必要だから金属一択」と考えてしまいがちですが、実際には用途に応じて“樹脂”がベストな選択肢になる場面も多くあります。
本項では、特に以下のようなケースで樹脂材料が非常に有効であることを解説します。
✅ 摩耗や潤滑の問題を軽減したい場合
✅ 金属同士の摩耗を避けたい場合(摺動部のブッシュやスペーサー)
摩耗や潤滑の問題を軽減したい場合
回転やスライドが繰り返される機構では、金属同士が直接当たると摩耗や焼き付きが発生しやすくなります。こうした場合に、潤滑不要で低摩擦な樹脂を使うことで、摩耗や潤滑の問題を軽減できます。
代表的な材料例
- POM(ポリアセタール)
- 非常に滑りやすく、摺動性・寸法安定性が高い
- MCナイロン
- 高強度で摩耗にも強く、軸受やギアに最適
具体例
- 摺動ガイドのスライダー
- 回転部のカラーやスペーサー
- 歯車(静音性と潤滑性を両立)
樹脂を使用するメリット
- 潤滑油不要 → メンテナンス性向上
- 摩耗粉が少ない → 清浄性が必要な装置に最適
- 無音に近い動作音 → 医療・検査装置などにも◎
金属同士の摩耗を避けたい場合(ブッシュ・スペーサー)
金属部品同士が直接接触すると、以下のような問題が起きがちです。
🚫 摩耗・変形・かじりつき
🚫 異音発生(チリチリ音やガタつき音)
🚫 部品寿命の低下
これを回避するために、あえて接触面の一方を樹脂化することが非常に有効です。
特に「樹脂ブッシュ」や「樹脂スペーサー」はその典型例です。
具体例
- アルミ製リンク機構に挿入する樹脂ブッシュ
- ボルトと筐体の間に入れる樹脂スペーサー
- カムフォロワの摺動部に使う樹脂パッド
これにより、金属表面の損傷や焼き付き、異音発生を抑えることが可能になります。
注意点と推奨ポイント
温度環境に注意
- 樹脂は高温(100〜150℃以上)で軟化・変形する可能性があります。
- 高温環境では耐熱樹脂(PEEK、PPSなど)を選定する必要あり。
強度の過信は禁物
- 金属の代わりに使えるとはいえ、過剰荷重をかけると割れ・変形が発生します。
- 力のかかり方・取付方法も含めて検討が必要です。
静電気が発生する場合あり
- 電子部品や粉体搬送系では帯電防止グレードの樹脂を選ぶのが安全です。
摺動や摩耗に悩むなら、金属から“樹脂”への置き換えを検討!
金属では難しい「潤滑なしで滑らかに動く」「摩耗粉を出さない」「静かに動く」といった要求には、樹脂材料が非常に有効です。
特に以下のような用途では、樹脂の採用をおすすめします:
✅ 潤滑が難しい摺動部品
✅ 軽量化したい摩耗部品
✅ 金属接触で異音や摩耗が発生している部品
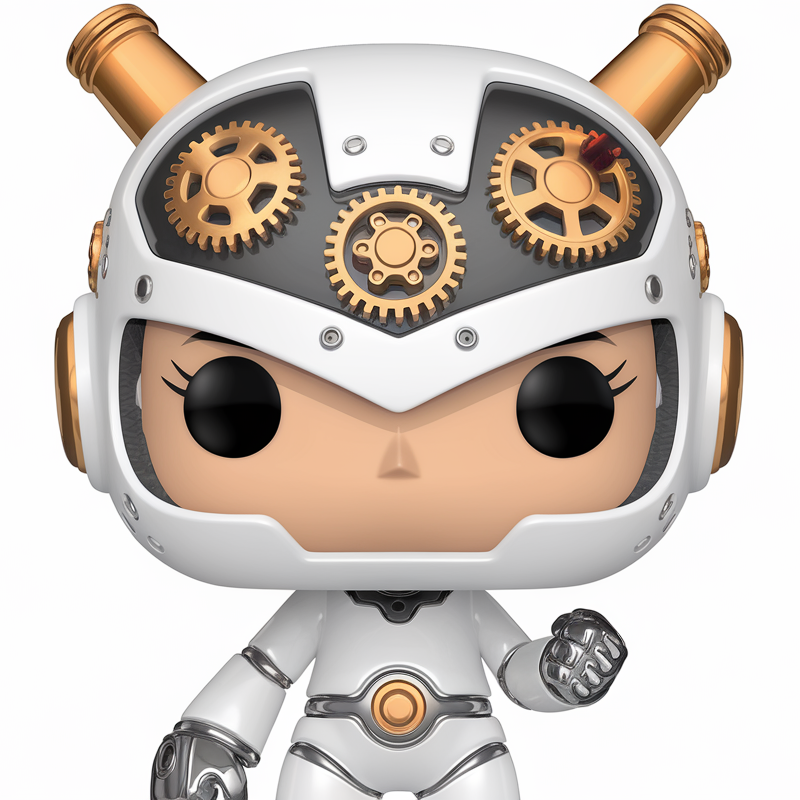
設計初期で「なぜ金属なのか?」「本当に金属でなければならないか?」を考えることで、トラブルの予防や寿命延長、保守性の向上につながります。
実際の活用例
ケース1:装置のフレーム → アルミ合金
アルミフレーム(例:ミスミのアルミプロファイル)は、軽量かつ高強度で、組立もしやすいため自動機や検査装置で多用されます。
ケース2:搬送用の部品トレイ → 樹脂
軽くて加工しやすい樹脂(POMやMCナイロンなど)で作ることで、搬送装置の負荷を下げ、省エネや高速化に貢献できます。
まとめ
目的に応じて、材料の特性を活かした選定を行うことが、設計品質と効率の向上に直結します。材料選定は「なんとなく」ではなく、「機能・性能・コスト」のバランスを見極めて行いましょう。
アルミ合金と樹脂は、どちらも軽量化に適した材料ですが、それぞれ特性と得意な用途が異なります。
アルミ合金は金属としての強度・剛性・耐久性に優れ、強度が必要な構造部品や可動部品に適しています。一方、樹脂は摩耗や潤滑の課題を軽減でき、摺動部やスペーサー、軽負荷のカバー部品などに有効です。
材料選定では、「力のかかり方」「温度環境」「摩耗や潤滑の有無」「精度や加工性」といった観点をバランスよく考慮することが重要です。
安易に「金属→樹脂」へ置き換えるのではなく、機能・コスト・加工性・耐久性のトータルバランスを見て、最適な材料を選ぶようにしましょう。
コメント