機械設計では、ただ図面どおりに形を描くだけでは足りません。
「この部品は、どう加工されるか」を考えることが、良い設計の第一歩です。
この記事では、切削加工における「工程分離」と「製造フロー設計」の工夫を、初心者にもわかりやすく解説します。
加工現場の流れを理解すれば、コストダウン・納期短縮・品質安定につながること間違いなしです!
なぜ“工程分離”が重要なのか?
工程分離とは、複数の加工工程を意図的に段階ごとに分けて設計・管理することです。
🔍 例)
- 荒加工(大まかに削る)
- 中仕上げ加工
- 精密加工(公差や面粗さを厳密に仕上げる)
- 穴加工(ドリルやタップ)
- 表面処理・検査
これを無計画に行うと、以下のような問題が起こります。
- 不要な段取り替えが発生
- 公差が出せず、再加工が必要に
- 他工程との干渉で不良発生
初心者が知っておきたい「工程分離の工夫」7選
1. 荒加工と仕上げ加工を分ける
最初に材料全体を削る「荒加工」と、公差や面粗さを出す「仕上げ加工」は、工具・回転数・送り速度が異なります。
これを明確に分けることで、工具寿命も延び、品質も安定します。
✅設計時の工夫
- 仕上げ面は加工図面に「仕上げ加工必要」と注記
- 公差部位を明確に分けておく(必要な面だけに寸法公差を付ける)
2. 回転対称部品は旋盤加工に分離する
例えばシャフト形状の部品は、旋盤での円筒加工が効率的。
フライス加工と併用するよりも、円形部と角部を部品分割して、得意な加工方法で分けると良いです。
✅設計時の工夫
- 回転対称形状を別部品として設計
- ねじ止めや圧入で組み合わせる
3. 穴加工は工程の後半に行う
部品の削り出し前に穴を開けてしまうと、変形や加工ズレの原因になります。
特に高精度な合わせ穴やピン穴は、最後に行うのが原則です。
✅設計時の工夫
- 図面に「後加工指定」や「仕上げ後穴加工」などを明記
4. 基準面を最初に加工しておく
すべての寸法・穴位置の基準となる面(基準面)は、真っ先に加工しておくことで後工程が安定します。
✅設計時の工夫
- 図面で基準面を明示
- 加工順序を考慮し、基準から寸法を配置
5. 反りや歪みを防ぐために中間焼鈍を考慮する
大物部品や薄肉部品では、途中で「焼鈍(しょうどん)」と呼ばれる応力除去処理を行うことがあります。
これも工程分離の一つで、加工途中で素材の歪みを取るために重要です。
✅設計時の工夫
- 図面や指示書に「焼鈍材使用」などを記載
- 薄肉・非対称部品は、歪み対策を工程内で考慮
6. 前加工と後加工の境界を明確に
溶接・焼入れ・表面処理を行ったあとで追加工が必要な場合、どの工程までが前加工かをはっきり決めておきましょう。
✅設計時の工夫
- 後加工が必要な部位に明示を入れる
- できれば、後加工不要な形状に工夫する(例:穴を前もって開けておく)
7. 製品の組立順を意識した設計にする
加工順序と同様に、組立てやすさ・検査のしやすさも設計段階から考慮しましょう。
後工程の干渉や手間を防ぎます。
✅設計時の工夫
- 組立の基準部位から加工順を考える
- 検査や仕上げがしやすい部品構造にする
製造フロー設計とは?
製造フローとは、素材→加工→表面処理→検査→組立→出荷といった製品完成までの流れのことです。
この流れを無視した設計は、次のような問題を招きます。
- 工場内での運搬回数が多くなる
- 工程間で不具合や手戻りが増える
- 工期やコストが読みにくくなる
製造フローを考慮した設計の具体例
製造フロー | 配慮すべき設計ポイント |
---|---|
素材 | 入手しやすい規格サイズを使用する(例:50×50×100など) |
加工 | 片面から加工できる形状、段取りを減らす設計に |
表面処理 | メッキやアルマイト後に再加工が不要なように仕上げ面を調整 |
組立 | 締めやすい位置にねじや穴を配置する |
検査 | 基準面や基準穴を使って測定しやすい設計にする |
■ まとめ:工程と流れを意識した設計でトラブル激減!
切削加工の設計は、ただ形を決めるだけではありません。
「どんな工程で、どの順番で、どう仕上げるか?」をあらかじめ考えておくことで、加工工数の削減・品質の安定・納期短縮につながります。
✅設計時に自問してみると良い質問
- この部品、何工程で加工することになる?
- 最初にどこを基準面として加工する?
- 穴は前?後?どこで加工する?
- 公差は本当にこの精度が必要?
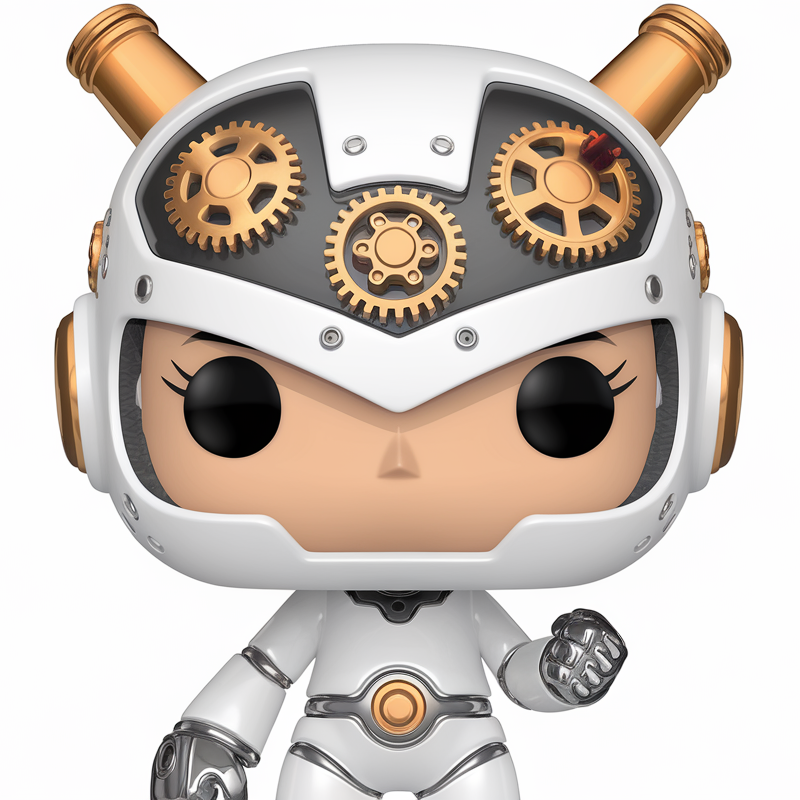
こうした問いを意識しながら設計を進めるだけで、現場から喜ばれる設計者になれます。
コメント