機械設計において、部品形状をいかにシンプルに保てるかは、製品のコスト・納期・品質に直結する重要なポイントです。特に「切削加工」を用いる部品では、複雑な形状や無理な構造は加工の難易度とコストを一気に引き上げる要因になります。
この記事では、「なぜシンプルな形状が重要なのか」「どのようにシンプル化を意識すべきか」を初心者にもわかりやすく解説します。
シンプルな形状が大切な理由とは?
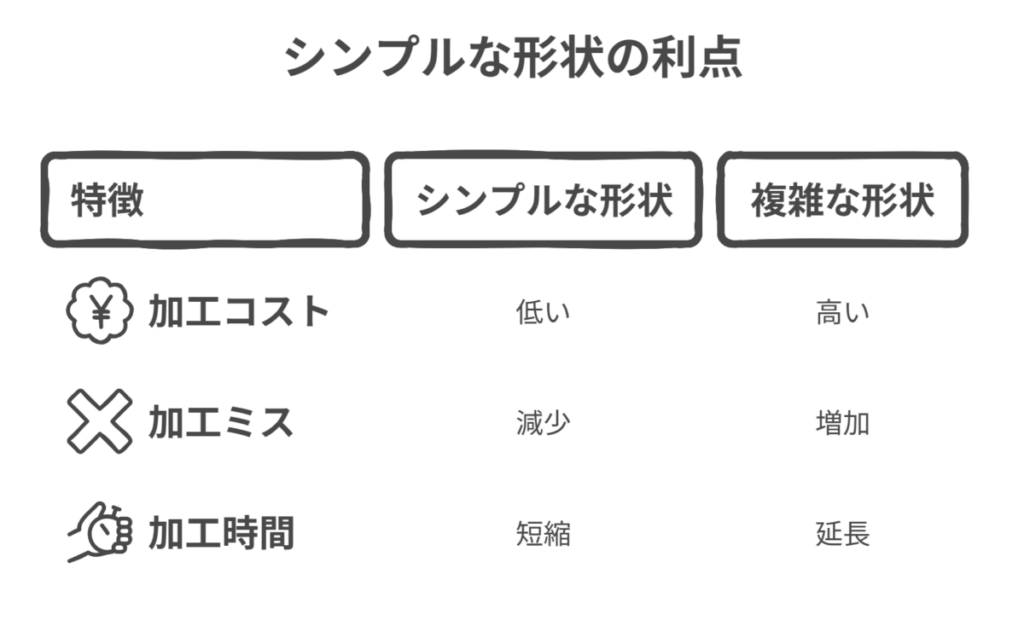
加工コストが安くなる
多軸複雑な形状は、特殊な工具や多軸加工、追加工程が必要になります。
逆に、平面・穴・直線的な溝などの基本的な形状だけで構成された部品は、汎用設備で短時間に加工できるため、コストが抑えられます。
加工ミスが減る
加工がシンプルなら、プログラムや段取りも簡単になり、加工ミスやバラつきのリスクも下がります。
結果として品質が安定しやすくなります。
加工時間が短縮される
複雑な段取りや工具交換が減ることで、加工時間が短縮され、生産効率が向上します。
これは納期短縮にもつながります。
シンプルな形状を設計するための工夫ポイント
「段差」「凹凸」「突起」をなるべく避ける
段差や高さ違いは追加の加工が必要です。可能な限り、フラットな面構成にできないかを検討しましょう。
四角いポケットは隅R(コーナーR)を設ける
エンドミルは直角を削れないため、四隅にはRをつける設計が望ましいです。
直角にしたい場合は追加工が必要になります。
複雑な3D形状は避ける
斜面や曲面、傾斜付きポケットなどは3次元加工(3D CAM)が必要で、手間もコストもアップします。
できるだけ2.5次元の加工で済むように工夫しましょう。
加工しやすい形状の代表例
形 | 加工性 | 備考 |
---|---|---|
直線的な平面 | ◎ | フライス加工で簡単 |
丸穴 | ◎ | ドリル1本で完了 |
隅Rつきポケット | ○ | 標準的な |
傾斜面や曲面 | △ | 多軸加工 |
設計者が意識したいこと
- その形状、本当に必要? → 機能・強度・位置決めの観点から見直してみましょう。
- 加工者の立場で考える → 図面を見て「これは一発で削れそう」と思える形が理想です。
- 簡単な形が“かっこ悪い”とは限らない! → 精度や品質、コスト面での美しさも大切です。
切削加工で複雑形状はなぜNG?~精度・コスト・ひずみのリスク~
機械部品を設計するとき、「かっこよく」「無駄なく」と考えるあまり、ついつい複雑な形状にしてしまうことはありませんか?
しかし、切削加工において“複雑形状”は多くのデメリットを生みます。
本項では、複雑な形状を切削で加工する際に起こりやすい問題と、その理由をやさしく解説します。
複雑形状による主なデメリット
加工に時間がかかる
曲面や段差、ポケットが複雑な形になるほど、加工パスが増え、工具交換や段取りも多くなり、作業に時間がかかります。
🔍 例)
- 直線1本の加工は数秒
- 複雑な3Dポケット形状は数分~十数分
加工コストが高くなる
加工時間が長くなれば、それだけ機械の稼働費や人件費も上がり、製品コストが跳ね上がります。
また、専用治具や特殊工具が必要になることもあり、コスト増の要因になります。
加工ひずみが出やすい
複雑な形を削ることで、材料の内部応力がバランスを崩し、反りや歪みが発生しやすくなります。
内部応力(残留応力)とは?
材料の中には、加工前から目に見えない“力”が残っていることがあります。これを「内部応力もしくは残留応力」と呼び、特に大きく削ると応力バランスが崩れて変形してしまうことがあります。
🔍 例)
- 一方向から大量に削る
- 偏った肉抜き形状
🚫 加工後に反りや歪みが発生!
品質のばらつきが大きくなる
複雑形状は、加工プログラムが複雑化し、オペレーターの技量によって仕上がりが変わることも多くなります。これにより、ロットごとのばらつきが発生するリスクが増します。
検査や組立も難しくなる
形状が入り組んでいると、寸法検査がしづらくなったり、組み立て時に干渉やズレが起きたりすることもあります。
設計者ができる対策
- 部品の役割をよく見直す
- 本当にその凹みや段差は必要ですか?
- できるだけ“2.5次元”で完結する設計に
- フラットな面と丸穴中心で構成すると◎
- 対称形状や均等な肉抜きにする
- 応力バランスが取りやすくなります
- 必要があれば2部品に分けて構成する
- 加工が楽になり、品質も安定します
設計と加工のギャップに注意!
設計者は3D CAD上で形を簡単に作れますが、それが現場で簡単に加工できるとは限りません。
複雑な形状を思いついたら一度、「この形、加工しやすいだろうか?」と加工者目線で見直す習慣をつけましょう。
切削加工における複雑形状の設計は、コスト・精度・品質に多くのデメリットをもたらします。
特に、材料の内部応力によるひずみや、加工時間の増大は見逃せないリスクです。
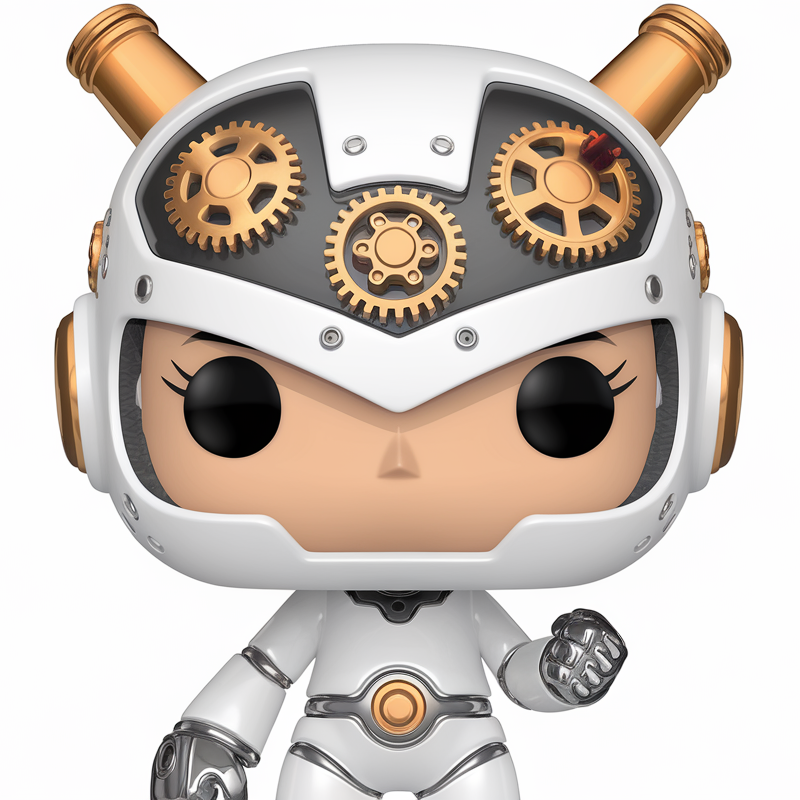
まずは“シンプルな形状で目的を果たす”ことを第一に考え、必要があれば段階的な改善や工程分割を取り入れることで、設計と加工のバランスが取れた高品質な製品に近づけることができます。
部品は“あえて分ける”ことで加工も品質も良くなる!
機械部品の設計をしていると、「一体型の方がスマートだし、ネジや組立の手間も減ってよさそう」と考えて、できるだけ1個の部品にまとめようとすることがあります。
しかし、あえて2部品に分けることで、加工や品質面で多くのメリットが生まれることもあるのです。
本項では、「なぜ分けることが有効なのか?」を初心者にもわかりやすく紹介します。
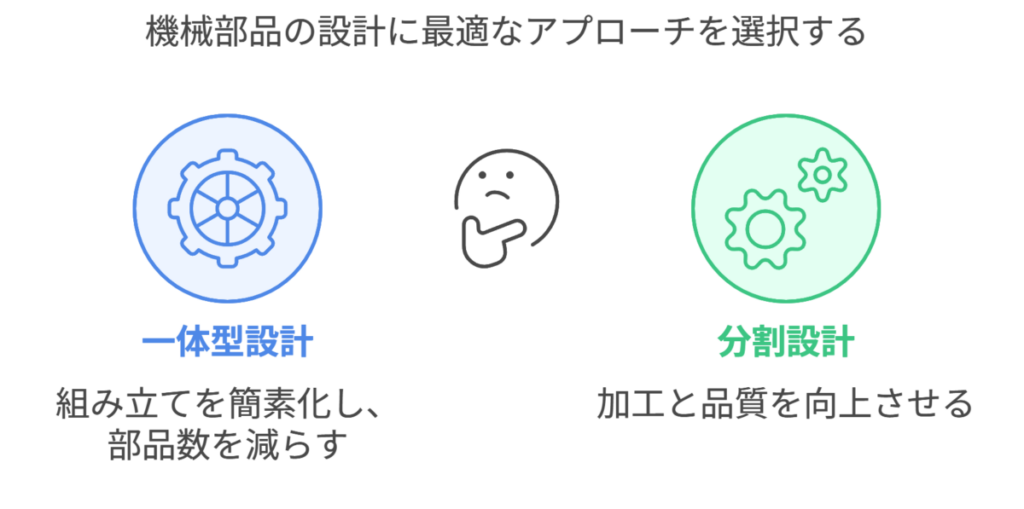
一体形状は加工が難しくなりがち
部品を一体に設計すると、以下のような問題が出ることがあります。
🚫 加工が難しく、加工時間が長くなる
🚫 複雑な形のため、専用治具や特殊工具が必要
🚫 加工ひずみや反りが発生しやすくなる
🚫 加工公差が厳しくなり、不良リスクが増える
特に、内部に段差やポケットがある形状や、複雑な3D形状は一体で作るとコストも手間もかかってしまいます。
部品を分割するメリット
加工しやすくなる
複雑な形を分けることで、シンプルな形状ごとに加工ができるようになります。
それぞれの部品が簡単な形なら、標準工具・少ない段取りで加工できるため、効率的です。
品質が安定する
一体成形では難しかった精度管理や仕上げ加工も、分ければ個別に対応できるため、高精度で安定した品質が得られます。
組立後に調整ができる
例えば、スライド部や角度が絡む部品などは、分けて組立時に位置を調整できる構成にすれば、調整の自由度が広がります。
分割設計のコツ
分けるタイミングの例 | 説明 |
---|---|
内部の加工が届きにくい場合 | ポケットや段差が深い場合は上下で分ける |
一部だけ高精度が必要な場合 | 精度が必要な部分だけ別加工して組み合わせる |
材質が異なる部分がある場合 | 耐摩耗性 |
🔍 例)
ベースプレートにL型ブラケットが一体成形されている構造
👉 ベースとブラケットを別部品+ボルト締結に変更すれば、加工は簡単になり、変形も減る!
分ける=悪ではない!
一体型にこだわりすぎると、加工や調整が難しくなり、コスト増・品質低下につながることもあります。
「組み立てる手間が増える」と心配になるかもしれませんが、トータルで見れば分割の方が合理的になるケースは多いです。
切削加工において、部品をあえて分けて設計することは、“手間を減らし、品質を上げる”ための有効な手段です。
✔ 加工が楽になる
✔ 変形しにくくなる
✔ 精度管理もしやすくなる
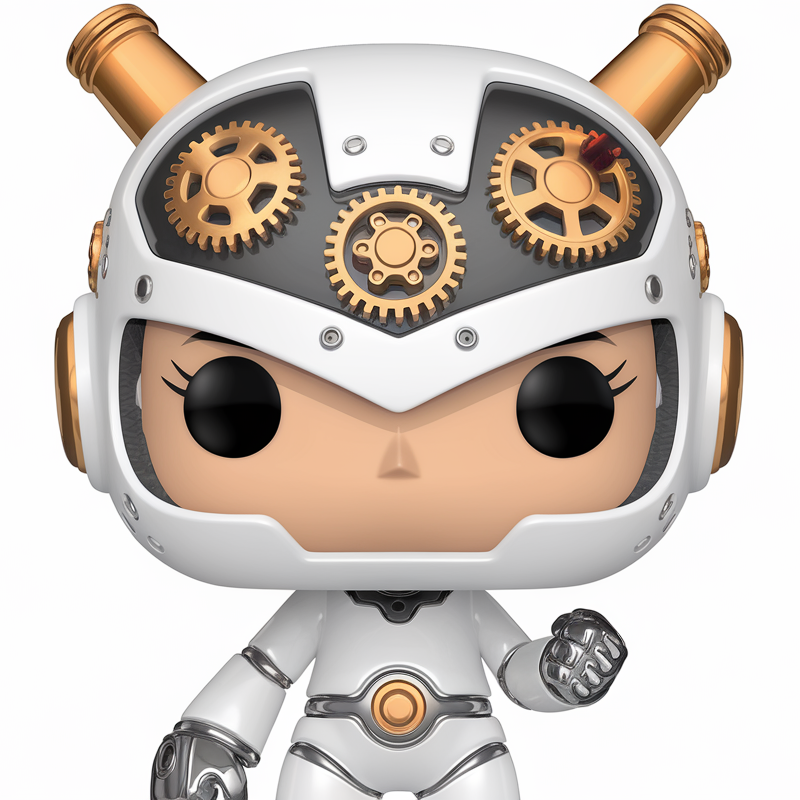
そんな利点があるからこそ、設計段階で「本当に一体化が必要か?」を見直す視点がとても大切です。
まとめ
切削加工では、シンプルな形状こそが最も合理的です。余分な段差や曲面、複雑な穴を減らし、誰が見てもわかりやすく、誰が削っても安定して加工できる形状にすることが、よい機械設計者の条件のひとつです。
設計の段階で「この形、本当に必要か?」と一度立ち止まり、加工現場をイメージする視点を持つことで、製造全体がスムーズになります。シンプルは正義、それが切削加工設計の鉄則です。
コメント