真空焼入れは、機械部品の性能を向上させる熱処理の一種で、「焼き入れの中でも高精度・高品質」が求められる分野で広く使われています。
この記事では、初心者の方にも理解しやすいように、「真空焼入れとは何か」「どんな特徴があるのか」「他の焼入れとの違い」や「適した用途・注意点」などをわかりやすく解説します。
真空焼入れとは?
真空焼入れは、その名の通り真空状態で行う焼入れ処理です。
基本の流れ
- 真空炉の中で部品を加熱(通常800~1200℃程度)
- 冷却媒体(高圧ガス)で急冷
- 窒素やアルゴンガスなどの不活性ガスを使って冷却
通常の焼入れでは大気中で加熱するため、表面が酸化して黒くなる(スケールが出る)のが一般的ですが、真空焼入れでは酸素が無いため、表面が変色しないのが大きな特長です。
真空焼入れのメリット
表面が酸化しない(無酸化処理)
真空中で加熱するため、部品表面が変色せず光沢を保てるのが最大の利点です。
✅ 見た目がきれいなまま仕上がる
✅ 表面仕上げの再研磨が不要な場合も
寸法変化や歪みが少ない
真空炉では加熱がゆっくり・均一に行われ、急激な温度差が少ないため、寸法変化や熱歪みを抑えることができます。
✅ 精密部品・高精度加工品に最適
脱炭がない
通常の焼入れでは、表面が酸素と反応し、炭素が抜けて(脱炭)硬さが落ちることがありますが、真空ではそれが起きません。
✅ 表面の硬度保持に有利
真空焼入れのデメリット・注意点
コストが高い
真空炉は設備も運転コストも高いため、通常の焼入れよりも割高です。
🚫 コスト重視の部品には不向き
大きな部品には制限がある
真空炉にはサイズ制限があるため、大型部品の処理が難しい場合があります。
🚫 大型シャフトや構造材には不向きなケースも
冷却速度に制限がある
水や油と違い、ガス冷却は冷却能力がやや弱め。冷却速度が必要な材料には不向きなことも。
🚫 材料との相性に注意が必要
真空焼入れに適した用途・部品
以下のような高精度・高表面品質が要求される部品に適しています。
部品 | 特徴・理由 |
---|---|
金型(精密金型) | 表面の光沢・精度を保ちやすい |
精密シャフト | 寸法変化が少なく高硬度 |
医療機器部品 | クリーンな仕上がりが必要 |
工具部品(バイト、パンチ) | 高硬度と美しい仕上がり両立 |
真空焼入れに適した材質
一般的に、以下のような材料が真空焼入れによく使われます。
材料 | 備考 |
---|---|
S45C | 中炭素鋼であり、強度や耐摩耗性に優れている |
SKD11、SKD61 | 金型用工具鋼の定番材料 |
SKH(高速度鋼) | 高硬度・耐摩耗性の確保に最適 |
SUS系(マルテンサイト系) | 例:SUS440など。ステンレスでも焼入れ可能な鋼種 |
SCM440Cなど合金鋼 | 精密機械部品に向く |
SUJ2(高炭素クロム軸受鋼) | 高硬度・高耐摩耗性に優れた鋼材 |
他の焼入れとの違い
焼入れ方法 | 特徴 | 表面状態 | 精度変化 | コスト |
---|---|---|---|---|
通常の焼入れ (油焼入れ) | 広く使われる汎用処理 | 黒皮が出る | 歪みやすい | 安い |
浸炭焼入れ | 表面を硬化 内部は靱性あり | スケールあり | 歪みが出やすい | 中程度 |
高周波焼入れ | 表面だけ選択的に硬化 | 多少のスケール | 比較的小さい | 中程度 |
真空焼入れ | 高品質・高精度 | 無酸化・光沢あり | 歪みが少ない | 高い |
真空焼入れと通常の焼入れの違いと使い分け
機械設計において、部品の強度や耐久性を高めるために欠かせないのが「焼入れ(やきいれ)」という熱処理です。
しかし、一口に焼入れといっても「通常の焼入れ」と「真空焼入れ」では、処理方法や仕上がりに大きな違いがあります。
本項では、初心者の方でも理解しやすいように、真空焼入れと通常の焼入れの違い・それぞれのメリットと使い分けのポイントをわかりやすく解説します。
焼入れとは何か?
焼入れとは、鋼材を高温に加熱してから急冷することで硬さ(硬度)を高める熱処理のことです。
硬化によって耐摩耗性や強度が向上するため、機械部品や工具に広く使われています。
通常の焼入れとは?
概要
「通常の焼入れ」とは、大気中で鋼材を加熱し、その後に油や水で急冷する方法です。
もっとも一般的な焼入れ方法で、多くの鋼材に適用されています。
特徴
- 加熱時に空気中の酸素と反応し、表面が酸化(スケールが発生)
- 処理コストが安価
- 工場内の汎用設備で対応可能
真空焼入れとズブ焼入れ(全体焼入れ)の比較表
項目 | ズブ焼入れ | 真空焼入れ |
---|---|---|
加熱雰囲気 | 大気中 | 真空中 |
冷却方法 | 油や水 | 高圧ガス(窒素など) |
表面の状態 | 黒皮・スケールが出る | 酸化なし・光沢のまま |
寸法精度 | 歪みや変形が出やすい | 歪みが小さい |
設備コスト | 安価 | 高価 |
処理コスト | 低い | 高い |
適した部品 | 一般部品・構造材 | 精密部品・美観が必要な部品 |
使い分けのポイント
では、実際の設計や部品選定において、どちらを選べば良いのでしょうか?
以下に目的別の使い分けポイントを紹介します。
ズブ焼入れを選ぶべき場合
- コスト重視の量産部品
- 表面仕上げを重視しない構造部品
- 加工後に再研磨がある場合
🔍 例:汎用機械部品、フレーム部品、建設機器部材
真空焼入れを選ぶべき場合
- 表面を黒くしたくない(美観重視)
- 寸法精度が重要(歪みNG)
- 脱炭による性能低下を避けたい
- 仕上げ研磨なしで使いたい精密部品
🔍 例:金型、精密シャフト、光学機器部品、医療機器部品
注意点
真空焼入れは材料の種類によっては適さない場合も
- 冷却速度が水や油に比べて遅いため、焼入れ性が低い鋼種には不向きな場合あり
- 対象の材料が真空焼入れに適しているか、メーカーの仕様確認やテストが必要
真空焼入れと通常の焼入れは、それぞれ特性や仕上がりが大きく異なる熱処理方法です。
目的 | 推奨処理 |
---|---|
コスト重視・量産品 | ズブ焼入れ |
表面の美観・精度を重視したい | 真空焼入れ |
精密機器部品に使いたい | 真空焼入れ |
鋼材の表面が酸化しても問題ない | ズブ焼入れ |
焼入れ方法の選定は、「見た目」「寸法精度」「硬さ」「コスト」といった複数の観点から判断する必要があります。
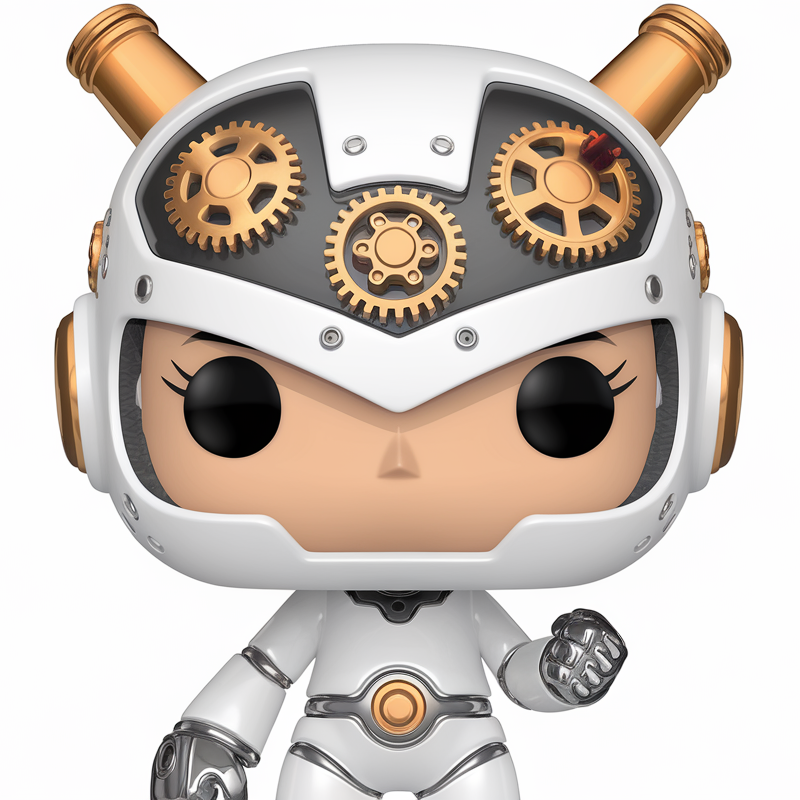
適切な処理を選ぶことで、製品の寿命や信頼性を大きく左右する重要なポイントとなります。
まとめ:真空焼入れは「高精度・美観」が求められる場面で選ぶ
真空焼入れは、以下のような設計ニーズがある場合に最適です。
✔ 精密部品で寸法変化を最小限にしたい
✔ 美観・クリーンな表面仕上がりが必要
✔ 再研磨なしで使いたい・再加工が難しい部品
✔ 高硬度と耐摩耗性を両立したい
反面、コストやサイズ制限があるため、すべての部品に適しているわけではありません。
目的や用途に応じて、焼入れ方法を正しく選定することが、機械設計において重要なポイントです。
コメント