空圧機器の基礎知識
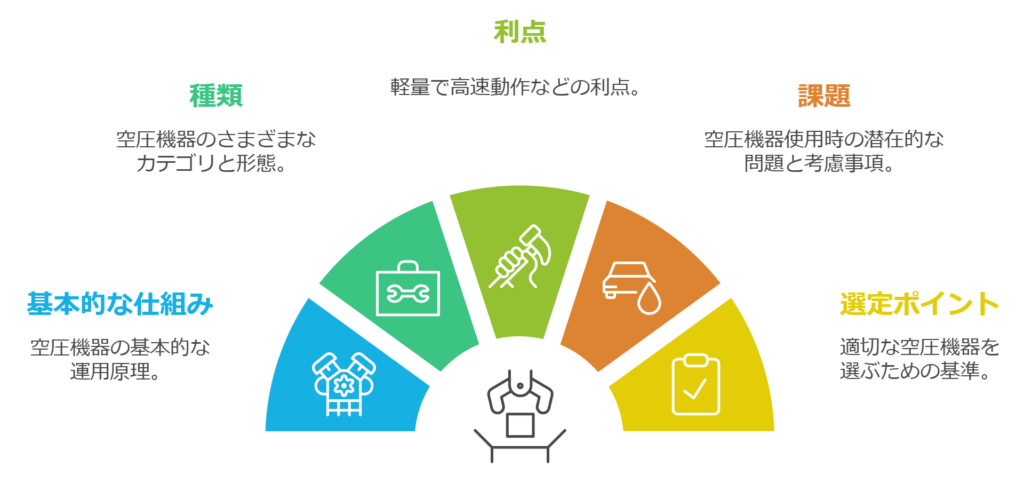
空圧機器(エア機器)は、圧縮空気をエネルギー源として動作する機械部品です。産業用機械や自動化設備で広く使用されており、軽量で高速動作が可能なため、様々な分野で活躍しています。空圧機器の基本的な仕組みや種類、利点と課題、選定ポイントについて解説します。
空圧機器の仕組み
空圧機器は、圧縮空気を使用して動力を伝達します。通常、コンプレッサーによって空気を圧縮し、その圧力を利用して機械部品を動かします。圧縮空気は、シリンダー、モーター、バルブなどを介して動力として利用されます。
エアシリンダーの基礎知識
エアシリンダーの基本構造と動作原理
エアシリンダーは、空圧機器の中で最も広く使用される部品の一つであり、圧縮空気を利用して直線的な運動を生み出すための重要な要素です。
エアシリンダーの基本構造
エアシリンダーは、圧縮空気のエネルギーを直線運動に変換する装置で、シンプルな構造ながらも多くの産業で利用されています。
エアシリンダーの動作原理
エアシリンダーの動作原理は非常にシンプルですが、圧縮空気の力を効率的に活用しています。エアシリンダーの動作は、空気圧を利用してピストンを前後に動かすことで、直線運動を生成します。
✅ 単動シリンダー:片側のみに空気を供給し、スプリングで戻る構造。
✅ 複動シリンダー:両側に空気を供給し、前進・後退を制御可能。
エアシリンダーの選定手順
エアシリンダーを適切に選定するためには、以下の手順が重要です。
✅ ストロークの決定:必要な移動距離を算出。
✅ 推力計算:負荷に応じたシリンダー径を決定。
✅ 使用環境の考慮:温度、湿度、粉塵などの影響をチェック。
✅ 取付方法の選定:フランジ取付、クレビス取付など用途に適した方法を選ぶ。
✅ クッション方式の選定:ラバークッション、エアクッションなど用途に適した方式を選定。
エアシリンダーの推力計算
エアシリンダーの推力は以下の式で求められます。
\( \displaystyle F=P×A\)
- F:推力(N、ニュートン)
- P:空気圧(Pa、パスカルまたはMPa)
- A:ピストン面積(m²、平方メートル)
✅ 大きな負荷には大径シリンダーを選定
✅ 摩擦損失や圧力低下を考慮する
✅ エア圧の安定供給が必要
エアシリンダーの種類とメーカーの特徴
エアシリンダーにはさまざまな種類があり、用途によって使い分ける必要があります。
✅ 標準シリンダー:一般的な直線運動を行う。
✅ コンパクトシリンダー:省スペースで設置可能。
✅ ロータリーアクチュエータ:直線ではなく回転運動を発生させる。
✅ ロータリークランプシリンダー:ワークや部品を固定するためのシリンダー。
✅ エアチャック:エアの供給により爪を開閉し、ワークを保持させる。
✅ 耐環境シリンダー:防塵・防水・耐熱・耐寒仕様。
✅ メーカーの特徴:SMC、コガネイ、CKDなど各社が独自技術を提供。
直動ガイドとフローティングジョイントの併用
エアシリンダの動作精度と耐久性を向上させるためには、直動ガイドとフローティングジョイントの適切な組み合わせが重要です。それぞれの役割は以下のとおりです。
✅ 直動ガイド:シリンダのロッドのブレを抑え、直線運動の精度を向上
✅ フローティングジョイント:わずかな芯ずれを吸収し、シリンダロッドや機械部品への負荷を軽減
直動ガイドで精度を確保しつつ、フローティングジョイントで芯ずれを吸収することで、エアシリンダの寿命延長とスムーズな動作が可能になります。
電磁弁の役割と選定ポイント
電磁弁は、エアシリンダーの動作を制御する重要なバルブです。
📌選定時は以下のポイントを考慮します。
✅ 2ポート、3ポート、5ポートの種類
✅ シングルソレノイド or ダブルソレノイド
✅ 動作圧力範囲と応答速度
エア供給の基礎知識
エア配管の基本と設計ポイント
エア配管は、システムの効率やメンテナンス性を左右する重要な要素です。
✅ 適切な配管ルート:圧損を抑えるため、直線的な配管を心がける。
✅ 適切な配管サイズ:圧縮空気の流量や配管の長さに大きく影響します。
✅ 適切な継手の選定:異なるホース径や角度に対応できるものを選ぶ。
✅ マニホールド配管:一括管理しやすい
✅ 配管の色分け:誤接続を防ぐために、用途ごとに色を分ける。
✅ タグ付け:保守・点検時の識別用
✅ シール処理:エア漏れ防止のために適切なシール材を使用。
適切な配管設計により、エア漏れを防ぎ、省エネ効果を高められます。
エア配管の継手の種類と選定ポイント
エア配管の継手は、空圧機器を効率的に接続し、エア漏れを防ぐために重要な役割を果たします。継手の種類によって、適用できるチューブの材質や使用環境が異なります。一般的に以下のような種類があります。
✅ ワンタッチ継手:工具不要で簡単にチューブを接続・取り外しできる
✅ ネジ込み継手:ねじ接続で高い密閉性を確保し、振動にも強い
✅ カプラ:空圧機器や配管をワンタッチで着脱できるようにする接続部品
✅ ロータリージョイントの選定:圧縮空気を回転する機械部品に供給するための回転継手
適切な継手を選定することで、エア配管の効率向上とトラブル防止が可能になります。
エア回路図の基礎と読解
エア回路図は、空圧システムの構成を理解し、適切に設計・メンテナンスするために不可欠です。基本的な記号や流れを把握することが重要です。
✅ シリンダーのシンボル:エアシリンダーの動作方向や種類を示す記号。
✅ バルブの記号:2ポジション・3ポジションなどの動作パターンを表現。
✅ 圧力源・フィルターの記号:エア供給元や空気清浄機構を示す。
✅ 流れの方向:回路内での空気の流れを矢印で表示。
読解のポイント
- 回路の流れを意識する → 空気の供給から排気までの流れを確認。
- シンボルの意味を理解する → 各機器の役割を把握し、動作のイメージをつかむ。
- 設計ソフトの活用 → SMCの回路図作成ツールを利用すると便利。
エア回路図を理解することで、トラブル時の原因特定や効率的なシステム設計が可能になります。
コンプレッサーの種類と選定ポイント
コンプレッサーは圧縮空気を供給する重要な機器です。
✅ レシプロコンプレッサー:小規模な用途に適する。
✅ スクリューコンプレッサー:大規模な工場向け。
✅ オイルフリーコンプレッサー:クリーンな空気供給が必要な場合に最適。
✅ エアタンクとの組み合わせ:安定した空気供給を実現。
エアー3点セットの概要と選定ポイント
エアー3点セットは、空圧機器の性能を最適化し、長寿命化を図るために不可欠な機器です。
一般的に以下の3つの要素で構成されます。
✅ フィルター:圧縮空気内の水分や異物を除去し、清浄なエアを供給
✅ レギュレーター:圧縮空気の圧力を調整し、安定した動作を確保
✅ ルブリケーター:空圧機器の潤滑を行い、摩耗を防ぐ
適切なエアー3点セットを選定することで、エア機器の性能向上とトラブルの防止が可能になります。
バルブの種類と選定ポイント
エアーバルブは、空圧機器の制御に不可欠な要素であり、用途に応じた適切な選定が求められます。主な種類は以下の通りです。
✅ 手動バルブ:レバーやダイヤルで手動操作が可能
✅ ボールバルブ:圧縮空気のON/OFF制御
✅ チェックバルブ:空気の逆流を防ぐために使用
✅ スピコン:空気の流量を調整し、シリンダーの速度制御に活用
適切なエアーバルブを選定することで、空圧システムの効率化や制御の最適化が可能になります。
排気処理の種類と選定ポイント
エア機器の排気処理には、騒音対策や異物除去のためにサイレンサーやエキゾーストクリーナーが使用されます。それぞれの特徴は以下の通りです。
✅ サイレンサー
- 排気時の騒音を低減するための装置。
- 多孔質材やメッシュ構造を用い、音のエネルギーを吸収。
✅ エキゾーストクリーナー
- 排気中の油分や異物を除去し、周囲の環境をクリーンに保つ。
- 排気の勢いを抑えて、排気音の発生を低減
使い分けのポイント
- 騒音対策が必要な場合 → サイレンサー を選定
- オイルミストや異物が多い環境 → エキゾーストクリーナー を採用
適切な排気処理を行うことで、作業環境の向上や機器の長寿命化が期待できます。
冷却と埃飛ばしの基礎知識
ブロワー・送風機の特徴と選定ポイント
ブロワー・送風機は、機械や設備の冷却や作業環境の清掃に活用されます。適切な風量と風圧を選定することで、効率的な冷却や埃飛ばしが可能になります。
✅ 冷却用途:電子機器やモーター、工作機械などの発熱を抑えるために使用。
✅ 埃飛ばし用途:製造現場や木工加工、印刷工程などで、粉塵や切削くずを除去。
✅ 携帯型ブロワー:作業現場での局所的な冷却や埃除去に便利。
✅ 据置型送風機:広範囲の冷却や集塵装置と組み合わせた粉塵管理に活用。
選定のポイント
- 冷却対象の発熱量 → 必要な風量と風速を計算し、適切な機種を選定。
- 埃の種類と飛ばし方 → 吸引と組み合わせるか、局所的に風を当てるかを決定。
- 騒音と省エネ性能 → 長時間使用する場合、静音設計や高効率モーターを検討。
適切なブロワー・送風機を選定することで、設備の熱負荷を軽減し、作業環境の清潔さを維持できます。
イオナイザーの活用方法と選定ポイント
イオナイザーは、静電気の除去や異物の付着防止に役立つ空圧機器です。製造現場や電子機器の組立工程で活用され、品質向上に貢献します。
✅ 静電気除去:樹脂部品やフィルムなどの帯電を防ぎ、異物付着を抑制。
✅ ホコリの除去:静電気によるホコリの吸着を防ぎ、クリーンな作業環境を維持。
✅ エアブロータイプ:圧縮空気と組み合わせて、広範囲の除電や異物除去が可能。
✅ バータイプ:生産ラインでのシート状材料や基板の除電に適用。
✅ スポットタイプ:精密部品や特定エリアの局所的な除電に活用。
選定のポイント
- 対象物の大きさと形状 → 広範囲ならバータイプ、局所的ならスポットタイプを選定。
- 必要な除電能力 → 高速なラインでは応答速度の速いイオナイザーを選ぶ。
- 作業環境 → クリーンルーム対応の機種や、省エネ設計のものを検討。
- メンテナンス性 → 電極の清掃が容易なモデルを選定し、定期的な保守を実施。
適切なイオナイザーを選定することで、製品の品質向上と生産効率の向上が期待できます。
真空機器の基礎知識
真空ポンプの特徴と選定ポイント
真空ポンプは、空気を排出して圧力を低下させる装置で、吸着搬送や脱泡、真空成形などに活用されます。用途に応じて適切な種類を選ぶことが重要です。
✅ 油回転式真空ポンプ:高い真空度を実現し、密閉容器の脱気や成形に適用。
✅ ドライポンプ:オイルを使用せず、クリーンな環境での使用に最適。
選定のポイント
- 必要な真空度 → 使用する環境や用途に応じて、到達真空度を確認。
- ランニングコスト → 真空ポンプはモーターを駆動して空気を排出するため、電気を消費します。
- 使用環境 → オイルミストの発生を避けるならドライポンプやエジェクタ式を検討。
- メンテナンス性 → 長期間安定稼働させるために、フィルターやオイル管理が容易なタイプを選択。
- 騒音・振動 → 静音性が求められる環境では、防振・防音対策が施されたモデルを選ぶ。
用途に応じた真空ポンプを選定することで、作業の効率化と安定した真空環境を実現できます。
真空エジェクタの特徴と選定ポイント
真空エジェクタは、圧縮空気を利用して真空を発生させる装置で、吸着搬送や真空固定などの用途に使用されます。電源が不要で小型なため、省スペース設計にも適しています。
✅ ベンチュリ効果:圧縮空気を利用して真空を作り出す装置
✅ 軽量・コンパクトな設計:エジェクタは電動式の真空ポンプと比べて非常に小型で軽量。
✅ 高速な真空応答:圧縮空気の供給・遮断によって瞬時に真空を発生・解除できます。
選定のポイント
- 真空度(吸着力)の確認 → 真空度(-kPa)が高いほど、より強力な吸着が可能
- 圧縮空気の使用量 → 省エア設計が求められる場合、低消費エアタイプのエジェクタを検討。
- 設置スペース → コンパクトな単体エジェクタか、機能を一体化したユニットを選択。
- 真空破壊機能の有無 → ブロー機能付きのエジェクタを選ぶと、吸着解除が素早く行えます。
用途に応じた真空エジェクタを選定することで、省エネと作業効率の向上を両立できます。
真空パッドの特徴と選定ポイント
真空パッドは、真空エジェクタや真空ポンプと組み合わせて使用し、ワークを吸着・搬送するための重要な機械要素です。ワークの材質や形状に応じて適切なタイプを選定することで、安定した吸着性能を確保できます。
✅ 平型:平らなワークに最適。
✅ベローズ型:柔軟性があり、多少の高さ違いがあるワークにも対応可能。
✅ 深型:凹凸のあるワークや曲面のワークに対応。
✅ スポンジ型:ワークに傷をつけず、吸着面が不均一でも対応可能。
選定のポイント
- ワークの材質・形状 → 平面、曲面、凹凸の有無に応じて適切なパッド形状を選択。
- 吸着力 → 真空源の性能と組み合わせて、必要な吸着力を確保できるサイズを選ぶ。
- 使用環境 → 高温環境では耐熱パッド、粉塵が多い環境ではフィルター付きタイプを選択。
- 跡の付きにくさ → 吸着跡が問題になる場合は、ウレタンやスポンジ型を検討
ワークの特性や使用条件に適した真空パッドを選定することで、安定した吸着搬送を実現できます。
エアツールの基礎知識
エアツールの種類と活用方法
エアツールは、圧縮空気を動力源として動作する工具であり、軽量かつ高出力で、幅広い作業に活用されています。用途に応じたエアツールを選定することで、作業の効率化と品質向上が可能になります。
✅ エアインパクトレンチ:ボルト・ナットの締め付け&取り外し
✅ エアドライバー:ルク管理が容易で、組み立て作業に最適。電動ドリルに比べて高耐久。
✅ エアリューター:精密研削・彫刻・バリ取り.
✅ エアブローガン:圧縮空気で粉塵や切りくずを吹き飛ばす。機械や部品の清掃に最適。
活用方法
- 生産ラインの効率化 → インパクトレンチやドリルを用いることで、組立作業のスピードを向上。
- メンテナンス作業 → ブローガンを使用して機械内部の粉塵や切りくずを除去し、故障を防止。
- 負荷の少ない作業 → 軽量で振動が少ないため、長時間使用しても作業者の負担を軽減。
- 防爆環境での活用 → 電動工具に比べて火花が発生しにくいため、危険物を扱う現場での使用も可能。
用途に適したエアツールを選定し、適切に活用することで、安全かつ効率的な作業が実現できます。
空圧機器の利点と課題
利点
✅ 可搬性と柔軟性
空圧システムは軽量で設置が簡単なため、作業現場のレイアウト変更にも対応しやすいです。
✅ コストの低さ
空圧機器はシンプルな構造であるため、比較的安価に導入・維持できます。
課題
❌ 圧縮効率の問題
圧縮空気を作る際のエネルギー消費が高く、全体の効率が低下することがあります。
❌ 安定性の課題
温度や湿度による圧力変動があるため、システムの安定性が他の動力源に比べて劣ることがあります。
空圧機器の選定ポイント
空圧機器を選定する際には、以下のポイントを考慮することが重要です。
使用圧力
各機器が対応できる圧力範囲を確認し、適切な圧力で使用することが重要です。
流量の確保
シリンダーやモーターが必要とする空気の流量を確保し、圧縮空気の供給が安定するように配管サイズやコンプレッサーの容量を選定します。
作動環境
温度や湿度、粉塵などの環境要因に対応できる機器を選定し、フィルタや潤滑システムを適切に設置します。
空圧機器の物語 ~風の力に導かれた機械設計の歴史~
1章. はじまりの風:古代の知恵と空気の力
それは紀元前300年ごろ、古代ギリシャの天才ヘロンがアレクサンドリアで風を操り、文明の新たな扉を開いたときのことでした。ヘロンは空気と水を利用して、簡易的な蒸気エンジン「アイオロスの球」を作り出しました。これこそが、人類が初めて「流体の力」で何かを動かした瞬間です。
ヘロンの発明は、「空気には力がある」という概念を広めました。しかし、当時はただの「おもしろいおもちゃ」として扱われ、実用化の道はまだ遠いものでした。
2章. 中世の停滞と意外な進展
中世ヨーロッパでは科学が停滞し、空気の力に注目する人々はほとんどいませんでした。しかし、この時期にも空気の力を活用する技術がひそかに進化していました。その主役は鍛冶場です。
鍛冶屋が使用した「ふいご」は、空気を送り込むことで炉の温度を上げる仕組みを持っていました。この簡単な装置が、空圧技術の基盤となる「圧縮空気」のアイデアを形作ります。中世の鍛冶屋たちは知らぬ間に、未来の空圧機器の可能性を広げていたのです。
3章. 産業革命と空気の大躍進
18世紀、産業革命がイギリスで始まりました。蒸気機関が大いに発展したこの時代、空気の力も再び注目を浴びます。
ジョセフ・ブラックという科学者が、「空気は圧縮して保存できる」という概念を広め、これが後の「エアタンク」につながります。そして19世紀になると、産業革命の花形である炭鉱に空気圧縮機が導入されます。炭鉱の作業員が深い坑道でハンマーを使う代わりに、空圧機器を使って作業効率が向上したのです。
この頃、フランスの技術者ジョルジュ・ポンセレが発明した「空圧式ドリル」が話題となります。「空気でこれほどの力が出せるのか!」と驚いた人々は、空圧技術に未来を感じ始めました。
4. モダンエアーの誕生:20世紀の技術革新
20世紀初頭、空圧技術はついに産業界の主役の座を射止めます。この時期に登場したのが、空圧機器の心臓とも言える「コンプレッサー」です。圧縮空気を貯める技術が進化し、製造業や建設業、そして医療分野まで幅広く活用されるようになりました。
さらに、空気圧を利用した動作の制御装置「空圧シリンダー」も誕生します。これにより、ライン作業が自動化され、生産性が劇的に向上しました。戦後の高度経済成長期には、日本でも空圧機器が広く普及し、工場には空圧式ロボットが導入されるようになります。
5. 空気が未来を動かす:現代とこれから
21世紀に入り、空圧機器はさらに進化を遂げています。特に注目されるのが「省エネルギー化」と「精密制御」です。空圧シリンダーやバルブが電子制御と組み合わさり、高速かつ正確な動作が可能になりました。
さらに、空気という無尽蔵の資源を使うことで、環境負荷を減らすことができるという点で、空圧機器は再び脚光を浴びています。現代では、工場だけでなく、医療分野や自動車分野、さらにはロボティクスや宇宙開発にまで応用が広がっています。
物語の教訓:風を味方にする設計者たち
空圧機器の歴史は、「目に見えない空気に力がある」というシンプルな気づきから始まりました。その力を理解し、工夫を凝らした設計者たちが、機械設計の新たな可能性を次々に切り開いてきたのです。
現代のエンジニアもまた、この歴史を背負いながら、空圧技術を進化させ続けています。目に見えない空気の力は、これからも私たちの生活を支える重要なエネルギー源であり続けるでしょう。
まとめ
空圧機器はその柔軟性とクリーンなエネルギー源として、幅広い産業分野で重要な役割を果たしています。適切な機器選定とメンテナンスを行うことで、空圧システムのパフォーマンスを最大化し、効率的な動力伝達を実現できます。
コメント