機械設計の現場では、「性能」や「強度」、「安全性」など多くの要素を考慮して部品を設計します。
しかし、忘れてはならないのが「コスト」です。
特に量産品を扱う製造業では、部品1個あたりのわずかなコスト差が、
企業の利益に大きな影響を与えます。
今回は、機械設計における「部品コスト」の重要性について、初心者の方にも分かりやすく解説します。
部品のコストが企業の利益に直結する理由
製造業における利益は非常にシンプルな式で表すことができます。
利益 = 売上 − コスト
この「コスト」の中には、原材料費、人件費、設備費、そして部品の製造・調達費などが含まれます。
つまり、設計段階でコストの高い部品構成を選んでしまうと、それだけで企業の利益を圧迫する可能性があるのです。
特に量産製品の場合は、1個あたりのコストが10円違えば、
年間1万台で10万円の差、10万台で100万円の差になります。
小さなコスト意識が、企業の収益や競争力に直結するのです。
設計者がコスト意識を持つべき3つの理由
~なぜコストを意識した設計が企業にとって重要なのか?~
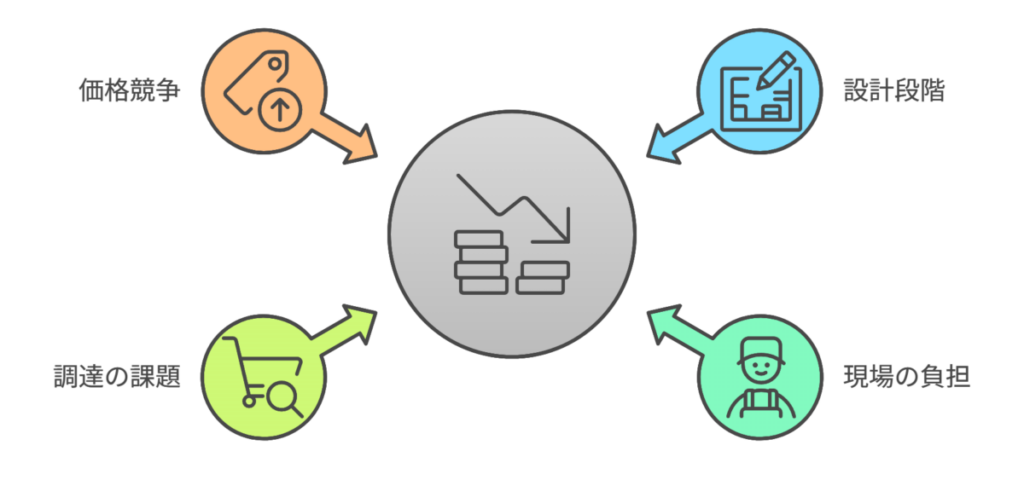
機械設計において、「強度」や「性能」「安全性」を確保することは、設計者の重要な役割です。
しかし、それだけでは設計として不十分なことがあります。
もうひとつ、非常に大切な視点が「コスト意識」です。
「設計者は技術のことだけを考えていればいい」と思われがちですが、実は設計の段階で製品コストの大部分が決まってしまうため、企業の利益に大きく影響する立場でもあるのです。
今回は、設計者がコストを意識すべき「3つの理由」について、初心者の方にもわかりやすく解説します。
理由①:設計で8割のコストが決まる
製造業における一般的な考え方として、製品のコストのうち70〜80%は設計段階で決定すると言われています。
なぜ設計でコストが決まるのか?
その理由はシンプルで、次のような重要な要素をすべて設計者が決定するからです。
✅ 使用する材料の種類(鋼材、アルミ、樹脂など)
✅ 加工方法(切削加工、板金、鋳造、溶接など)
✅ 形状や寸法(シンプルか複雑か、加工しやすいかどうか)
✅ 使用する部品(市販品か特注品か)
✅ 組立方法(手作業か自動化か)
たとえば、同じ性能を持つ部品でも、材料をステンレス(SUS304)にするのか、普通鋼(SS400)にするのかで材料費が2倍以上違うこともあります。
また、複雑な3次元形状をした部品は加工に手間がかかり、工賃が大幅に上がる可能性もあります。
つまり、設計者の選択ひとつで、部品単価や加工費が大きく変わるのです。
一方、製造現場での改善や購買部門での値引き交渉などによってコストを下げることはできますが、設計によって決まってしまったベースのコストには限界があります。
したがって、最も効果的なコスト削減策は「設計段階での工夫」なのです。
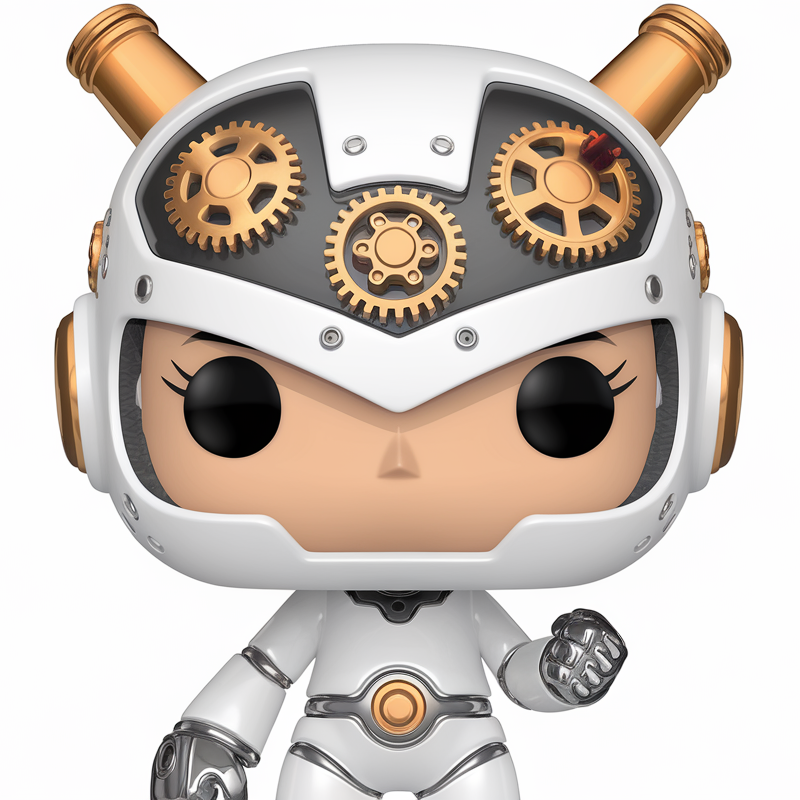
下記に、コスト削減に役立つ記事のリンクを張っているの
ぜひ、参考にしてください。
🔍材料選定
🔗機械設計における「材料選定」の基礎知識を徹底解説
🔗【コスト比較表】よく使う材料のコスト徹底比較【材料価格】
🔍加工方法
🔗【加工者との連携】材料の加工方法の知識が重要な理由【加工可否】
🔗【初心者向け】切削加工のコストを下げる!工具と加工方法の工夫ポイント10選
🔍形状について
🔗切削加工のコストダウンは形状設計から!初心者でもできる8つの工夫
🔗切削加工では“シンプルな形状”が最強!~機械設計でムダを減らすコツ~【分割設計のススメ】
🔍市販品(標準部品)について
🔗部品選定における標準品と特注品の違いと設計のポイント
🔗なぜ標準部品を使うとメリットがあるの? -コスト削減と納期短縮のカギ-
🔗【保存版】機械設計に役立つ!よく使うWEBカタログ・CADダウンロードリンク集【要素別まとめ】
🔍組立方法について
🔗加工後の「組立・検査」を考慮した設計で、失敗とムダを防ごう!
🔗組立ミスを未然に防ぐ“ポカヨケ設計”とは?初心者にもわかる実践事例
理由②:現場や調達部門の負担を軽減できる
設計者がコストや加工性を考慮しないまま設計を行うと、次のようなトラブルが起きる可能性があります。
製造現場での手間が増える
- 加工しにくい形状や、特殊な工具が必要な設計をしてしまうと、製造時間が長くなり、加工コストが上がります。
- 精密加工や手仕上げが必要になると、作業者の技能や時間が大きく影響し、不良率も上がるおそれがあります。
調達部門の負担が増える
- 市販されていない部品や特殊な材料を使用すると、調達に時間がかかり、納期が遅れる可能性があります。
- 海外からの輸入が必要な部品を指定した場合、為替や通関、物流のリスクが増加します。
こういった問題は、結果的に「納期遅延」「コスト増加」「不良発生」「顧客クレーム」などの企業全体への悪影響につながります。
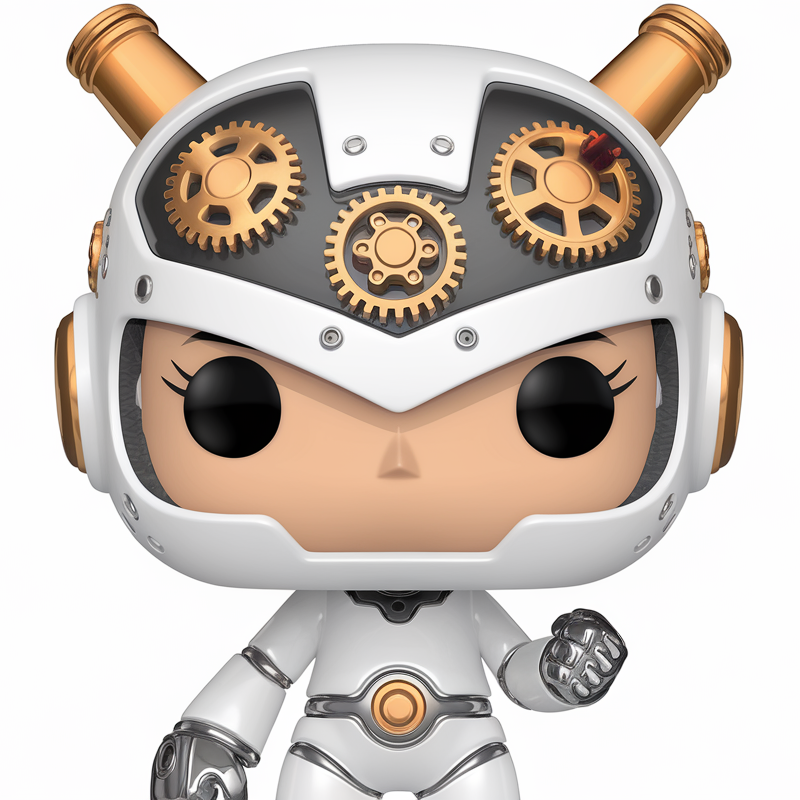
つまり、設計者がコスト意識を持つことで、製造・調達部門との連携がスムーズになり、
トラブルの少ない設計が可能になります。
理由③:他社との価格競争に勝つため
現代のモノづくりは、価格競争が非常に激しい世界です。
どれだけ性能の高い製品を作っても、価格が高すぎれば売れません。
お客様が求めているのは、「必要な性能を満たし、なおかつ価格が合理的な製品」です。
たとえば、ある製品がA社とB社で同じ機能・性能だった場合、価格が安い方を選ぶのは当然です。
このような競争に打ち勝つためには、設計の段階からコスト意識を持つことが必須です。
たとえば次のような取り組みが、価格競争力のある製品を生み出します。
✅ 既製品(規格品)を積極的に使うことで部品単価を抑える
✅ 加工しやすい設計を行って製造コストを下げる
✅ 共通部品化して在庫管理や流通コストを軽減する
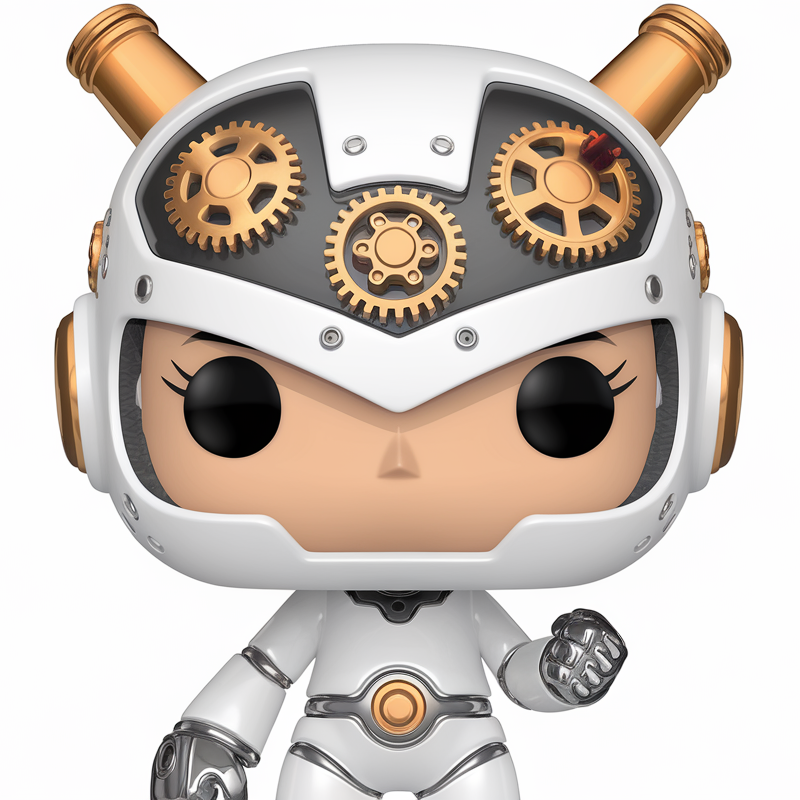
価格競争に勝つことは企業の利益だけでなく、
自分の設計が市場で評価されるチャンスにもつながります。
設計者は“企業の利益を守る番人”
機械設計者の仕事は、単に図面を描くだけではありません。
製品の品質、コスト、納期、安全性すべてに責任を持つ、非常に重要な立場です。
コスト意識を持つことで、
- 企業全体の利益向上
- 製造・調達部門との連携強化
- 市場での競争力向上
といった多くのメリットを生み出すことができます。
初心者のうちは、性能や機能ばかりに目が向きがちですが、
「この設計は高くつきすぎていないか?」「現場で作りやすいか?」という視点を持つだけで、
設計者として一歩レベルアップできるはずです。
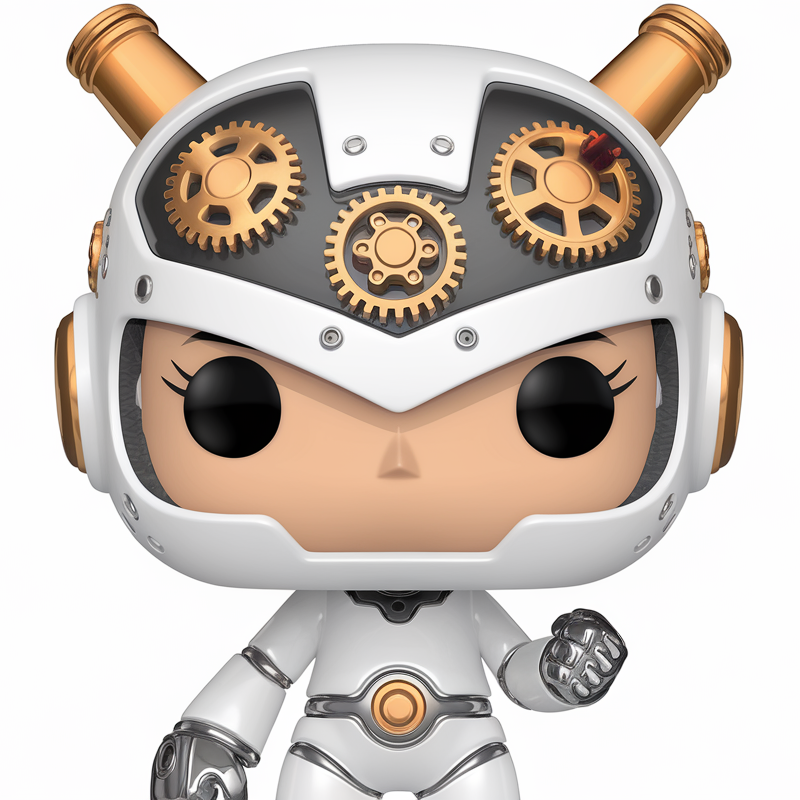
良い設計とは、機能だけでなくコストまで最適化された設計。
設計の引き出しを増やしながら、コスト感覚を鍛えていきましょう!
設計時にコストを意識する具体的なポイント
① 材料の選定
高性能な材料=高コストになりがちです。
たとえば、一般構造用鋼(SS400)と高強度鋼(SCM440)では材料単価が大きく異なります。
必要以上に高級な材料を使わず、「必要十分な性能」を満たす材料を選ぶことが重要です。
▼推奨ポイント
- 部品の負荷や使用環境を正しく評価して、適切な材料を選ぶ。
- 同等性能で安価な代替材(例:S45C → S35C)を検討する。
② 加工方法の工夫
切削加工が多い形状や、複雑な3D形状は加工費が高くなります。
溶接・組立・研磨などの手間がかかる工程もコストアップの要因です。
▼推奨ポイント
- 標準的な寸法や加工方法を使う(例:直角、φ10、M6など)。
- フライスや旋盤で加工しやすい形状にする。
- 板金や押出材など、量産向きの加工法も検討する。
🔍工作機械について
🔗旋盤加工の特徴と設計時のポイント
🔗フライス加工の特徴と設計時のポイント
🔗放電加工の基本原理と設計時のポイント
🔗板金加工の特徴と設計時のポイント
🔗レーザー加工の特徴と設計時のポイント
🔗溶接の基礎と設計時のポイント
🔍加工方法の基礎知識について
🔗L型ブラケットの設計方法を徹底解説 5選 【溶接・曲げ】
🔗【切削加工の工夫】ポケットの角は丸くするのが正解!~隅Rの基本と加工性への影響~
🔗切削加工は「刃物の形」がそのまま形状になる!【ピン角と逃がし加工】
🔗【初心者向け】C面取りとRの違いとは?角部の加工設計の基本と使い分けのコツ【糸面取り】
🔗深い溝・深穴はなるべく避けよう!~切削加工で大事な工具の限界~【穴精度・直角度の確保】
🔗切削加工は「片側から加工できる形状」が理想!【段取り替え削減】
🔗切削加工で「左右対称」と「非対称」どっちがいいの?【加工性と組立性】
🔗なぜ部品は左右対称が多いの?設計の効率化と応力バランスの理由をやさしく解説
🔗【切削加工の基礎知識】肉抜き・中空形状は“バランスよく”が大切!
🔗溶接って強度的に大丈夫なの?溶接部の強度評価と注意点
③ 標準部品の活用
ねじやベアリング、ブラケットなど、市販の標準部品を使えば、コストも調達も効率化されます。
逆に、オリジナル形状の部品を多用すると、製作費・図面作成・組立すべてがコストアップにつながります。
▼推奨ポイント
- ミスミやTHK、NBなどの規格品を活用する。
- ボルトやナットは種類・サイズを統一して管理しやすくする。
④ モジュール化・共通化
部品を複数の製品で使い回す「共通設計」は、製造コストや在庫管理の効率化に効果的です。
▼推奨ポイント
- 他製品と共通で使える寸法・取付け方法にする。
- モジュールごとにユニット化して再利用性を高める。
コストダウンを意識しすぎると起きる落とし穴
設計者がコストを意識するのは良いことですが、「安さ」だけを追求しすぎると、
逆効果になることもあります。
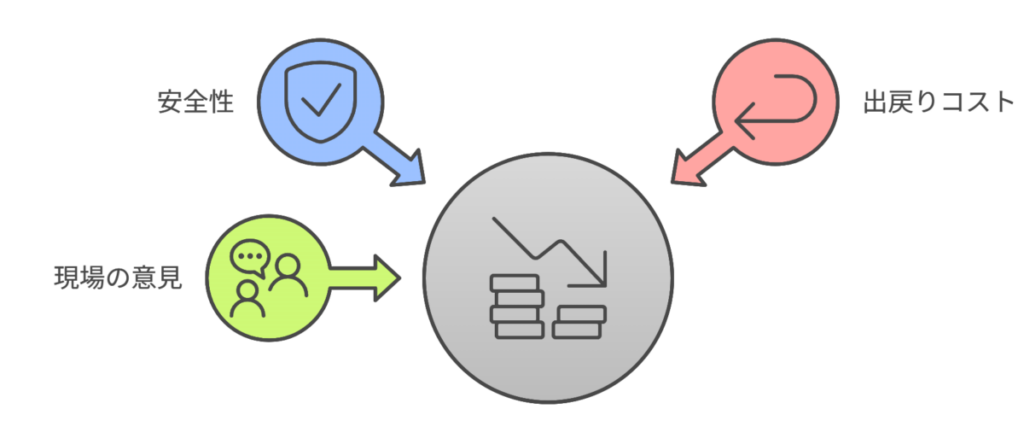
⚠️注意点①:安全性を犠牲にしない
コストダウンのために強度不足や信頼性の低い設計をしてしまうと、最終的に不良や事故につながり、結果的にコスト増となります。
⚠️注意点②:手戻りコストの方が高い
安価な部品を使ったが性能不足で設計変更になった…
そうなれば図面の修正・試作やり直し・評価試験など、多くの「見えないコスト」が発生します。
⚠️注意点③:現場の声を無視しない
加工者や組立担当者の意見を無視して「理想の設計」を突き通すと、現場が苦労してコストも上がる結果に。
現場と設計のコミュニケーションも、コストダウンの大事な要素です。
設計者に求められる“コスト感覚”
初心者のうちは「設計=強度や性能を満たすこと」と考えがちですが、それだけでは不十分です。
「コスト」「納期」「品質」など、全体最適を考える視点が設計者には求められます。
では、どうやってその“コスト感覚”を養えばよいのでしょうか?
▼実践的なコスト意識の養い方
- 材料費や加工費の目安を覚える(例:SUS304はSS400の約2〜3倍)
- 他の設計者や購買部門に相談してコスト相場を知る
- 自社の不良事例・クレーム事例を学ぶ
- 設計変更が発生した際に「なぜそうなったのか」を振り返る
まとめ:良い設計は「安くて使える」
機械設計において、性能や安全性はもちろん大切ですが、コストを意識することも同じくらい重要です。
部品1個あたりの数円、数十円の違いが、年間・全社で見れば何百万円ものインパクトになります。
企業の利益や製品の競争力を左右するのは、まさに設計者の判断次第なのです。
「高性能で高価な部品」ではなく、「必要な性能を満たし、合理的なコストの設計」を意識して、
“企業に貢献する設計者”を目指していきましょう。
コメント