機械部品を設計する際、「この形を削って作ってください」と図面を描くことになります。
でも、どんな刃物で加工するか? を意識せずに設計すると、「この形は削れません」や「追加工が必要です」といった問題が起きてしまいます。
切削加工では、工具(刃物)の形状がそのまま加工形状に転写されるという特徴があります。
この記事では、「工具の形を理解することがなぜ大切か?」を、初心者にもわかりやすく解説します。
切削工具とは?
切削工具とは、「材料を削るための刃物」のことです。
代表的なものには以下のような種類があります。
工具の種類 | 主な用途 | 特徴 |
---|---|---|
エンドミル | フライス盤やマシニング加工に使用 | 円柱状で、端と側面に刃がある |
ドリル | 穴あけ加工 | 先端で穴を開ける |
バイト | 旋盤加工(回転する材料を削る) | 単刃で、材料の外側や内側を削る |
加工形状は「刃物の形」がそのまま出る!
たとえば、四角いポケットや直角の内コーナーを設計したとします。
しかし、エンドミル(切削工具)は先端が完全な角ではなく、丸み(隅R)があります。
つまり、加工された形状も隅が少し丸くなるのです。
「刃物の限界=加工の限界」
処理ツール | 加工結果の例 |
---|---|
エンドミル | コーナーに Rが残る(直角にならない) |
バイト | 小さなRが必ず残る(0.4mm、0.8mmなど) |
隅R(すみアール)を設計に反映しよう
特にエンドミルで加工する「ポケット」「溝」「くり抜き形状」などでは、内角に「隅R(コーナーR)」が出るのが当たり前です。
工夫ポイント
- 内コーナーは直角ではなく、R形状で設計する
- できるだけ大きなR寸法(例:R3)を指定すると、加工が楽になる
- どうしても直角が必要なときは、放電加工や角出し加工が必要になる(コストアップ)
バイトの削れる形に注意!
バイトで削ると、角には必ず小さなR(丸み)が付きます。
なぜなら、バイトの先端にもわずかな丸み(隅R)があるからです(通常はR0.2~0.4mm程度)。
設計での注意点
- 完全な直角や鋭角は削れない → 放電加工などが必要になる
- バイトの刃形に応じた形状設計が必要
バイトとは?
バイトは、旋盤(せんばん)という工作機械で使う工具です。
材料を回転させて、バイトを当てることで外形や内径を削ります。
バイトの特徴
「外径加工」「内径加工」「突切り」「ねじ切り」など、さまざまな用途のバイトがある
先端に1本の刃がついたシンプルな工具
刃の角度や形によって、削る方向や仕上がりが変わる
バイト加工のメリットと限界
メリット | 限界・注意点 |
---|---|
シンプルな構造で汎用性が高い | 内部の複雑な形状は苦手 |
外径・内径・ねじ切りなど対応可能 | 鋭角や細かい隅までは削れない |
刃先の形状を自由に調整できる | 加工者の技量によって仕上がり差あり |
設計者が知っておくと良いこと
- 加工方法に応じた形状を意識する
- バイトで加工する場合は、丸みや直線的な動きを考慮しましょう。
- 細かすぎる形状は避ける
- 細い溝や鋭角な切り欠きなどは、別加工や工具変更が必要になることも。
- 隅Rや面取りの配慮
- 加工しやすさと強度確保のため、隅RやC面取りを設けるのが基本です。
バイトを理解すれば設計がうまくいく!
切削加工において「どんな刃物で削るのか?」を知ることは、設計ミスを減らす第一歩です。
バイトは旋盤で使う基本的な工具ですが、その形や動きを理解していないと、図面通りに加工できない部品を作ってしまう可能性があります。
✅ バイトはシンプルだが万能ではない
✅ 加工できる形状には制限がある
✅ 設計段階でバイトの形や動きを想定することが大切
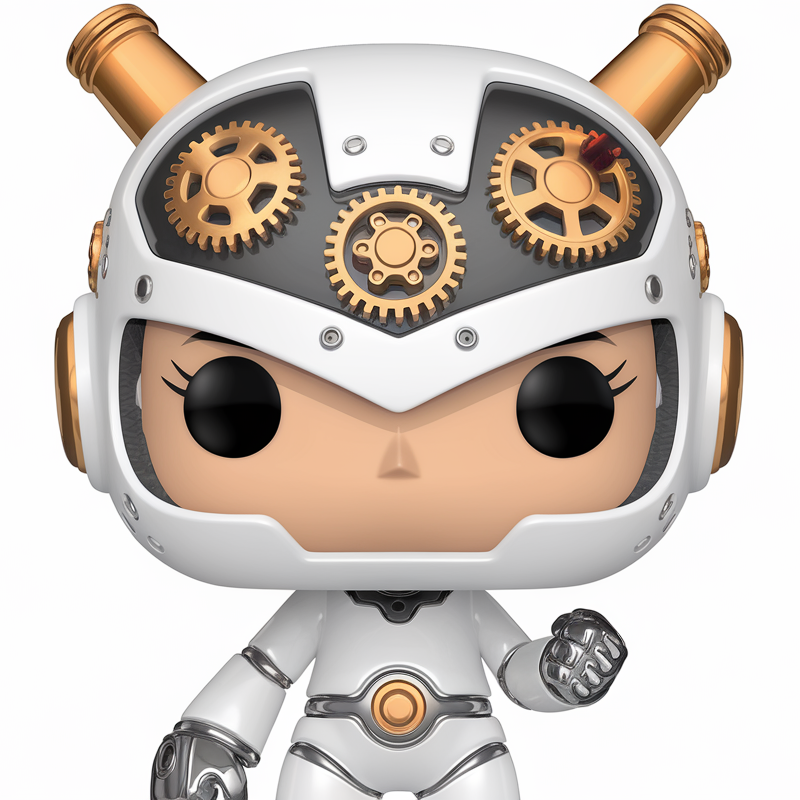
切削加工を学ぶ上で、工具の理解は欠かせません。
次回から図面を描くときは、「この形、バイトで削れるかな?」と考えてみましょう!
完全なピン角はNG?切削加工では「逃がし加工」がオススメ!
機械設計において「角はシャープにしたい」「ぴったりはめ込みたい」と思うこと、ありますよね。
でも、切削加工では“完全な直角(ピン角)”を削るのはとても難しいということをご存じでしょうか?
本項では、なぜピン角が加工しにくいのか、どう工夫すればいいのかをやさしく解説します。
ピン角ってなに?
「ピン角」とは、直角で鋭くとがった角のこと。
設計上、部品のポケット(凹み)の四隅などにピン角があると、見た目はきれいでスッキリします。
でも実はこれ、切削加工では非常にやっかいなんです。
切削加工ではなぜピン角ができない?
切削加工では、主にエンドミルやバイトという先端がわずかに丸い刃物を使って削ります。
そのため…
- 角まで削るとき、どうしても丸み(隅R)が残ってしまう
- 完全な直角は、物理的に作れない
無理にピン角にしようとすると…
ピン角を実現しようとして無理な設計をすると…
- 特殊加工(放電加工やワイヤーカット)が必要になりコストアップ
- ワイヤーカットでも厳密なピン角は不可能(ワイヤー径によるもの)
- 工数が増えて納期が長くなる
- 工具に無理がかかって工具寿命が短くなる
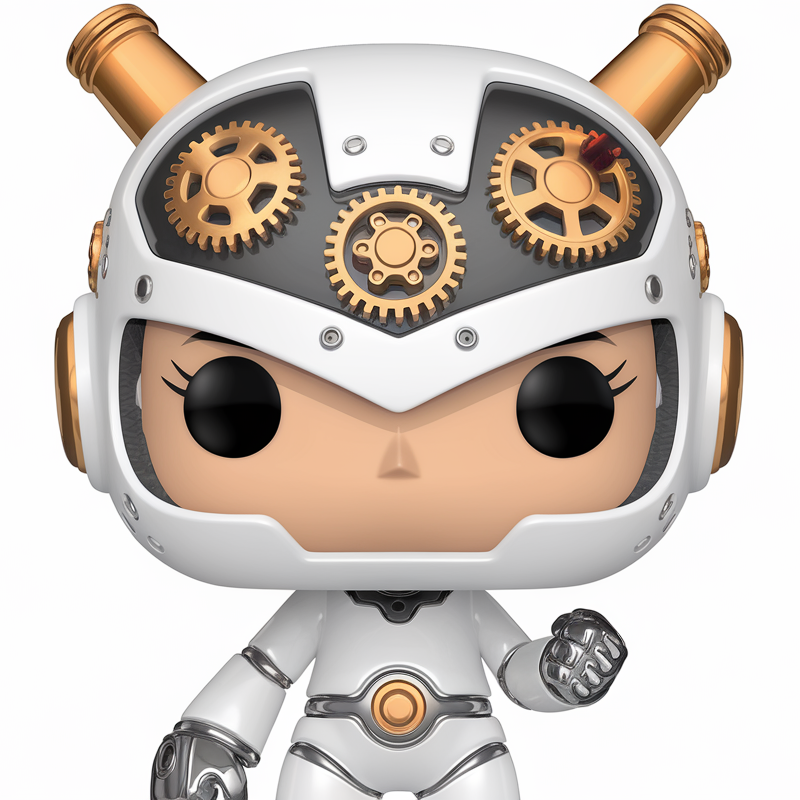
つまり、加工も高くつき、設計者にも製造者にもメリットがありません。
解決策①:逃がし加工を使おう!
どうしても角まで部品をぴったり入れたい場合は、「逃がし加工」を使いましょう。
逃がし加工とは?
ポケットの四隅に、小さな削り込み(逃がし)を設けることで、部品の角が干渉しないようにする工夫です。
メリット
- 工具で削れる形状だけで済むため加工が楽になる
- 工具選択の自由度が増える(例:φ6エンドミルで逃がし寸法をφ6.5にする等)
- 部品の組付け性が向上する
解決策②:相手部品側に逃がしを設ける
もうひとつの選択肢は、差し込まれる側の部品(オス側)にRや面取りを設けておくことです。
例えば・・・
- 入り込む角部にC面取り(C1など)を施す
- 小さなR(R0.5など)を設けることで干渉を防止
メリット
- 組付け時の「引っかかり」や「キズ」を防げる
- 加工側に大きな逃がしを設けずに済む場合がある
- 全体としてスマートな設計になる
ピン角は避けて逃がそう!
NGな考え | OKな考え |
---|---|
ピン角でかっちり合わせたい | 逃がしで干渉を避ける |
シャープな角がかっこいい | 加工しやすくて組付けやすい形に |
切削加工では、工具の形が加工形状にそのまま影響します。
無理なピン角指定はトラブルのもと。逃がし加工を上手に使って、設計も加工もスマートに進めましょう!
逃がし寸法の設定ポイント
✔ 使う工具(エンドミル)より少し大きめの半径で設計する
✔ 「以下」や「最大」といったゆるめの寸法公差を使うと、加工しやすい
🔍 例)
使う工具:φ6エンドミル → 逃がしRはR3以上で「R3.5以下」と指定するのがベター
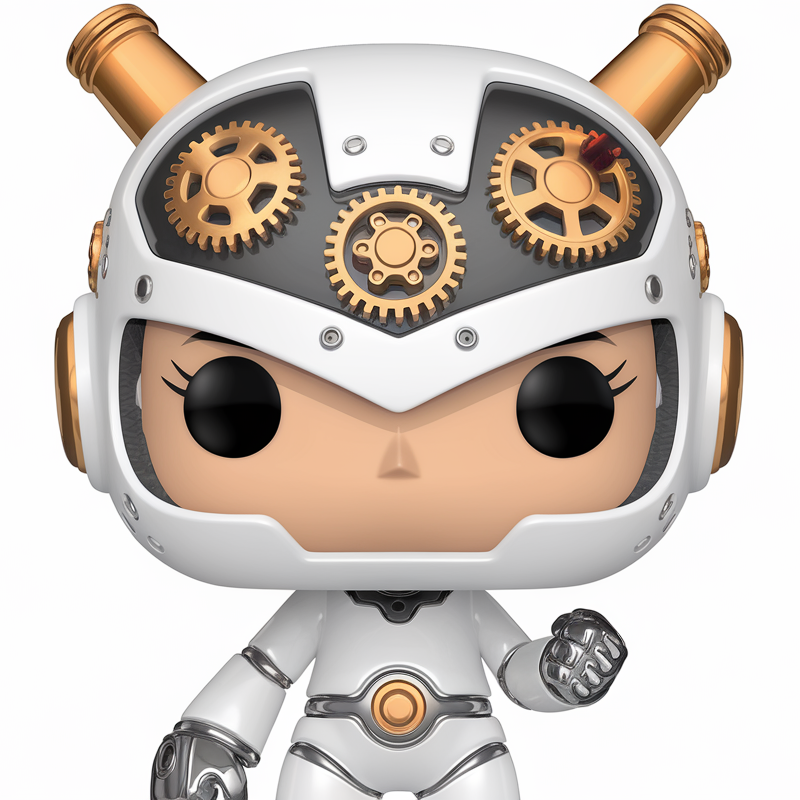
このように、加工側か、相手側か、または両方に工夫を入れることで、ピン角によるトラブルを防ぎつつ、組付けしやすい設計が可能になります。
設計者が知っておきたいこと
ポイント | コンテンツ |
---|---|
工具の形を理解する | エンドミルは丸く削れる/直角はできない |
バイトの先端Rを前提に設計する | 最小でもR0.4程度あると加工しやすい |
どうしても直角が必要なら | 放電加工や逃がし加工で対応(コストアップ) |
まとめ:加工形状は刃物形状の“写し鏡”
切削加工では、「こう削れるだろう」と設計者が思っていても、実際は工具の形に大きく影響されるのが現実です。
✔ 工具の形状を知れば、無理な設計が減る
✔ 隅Rを意識すると、加工がスムーズになる
✔ 加工現場との連携も良くなる
設計段階で刃物(工具)の特性を理解しておくことが、トラブル回避とスムーズな製造の第一歩です!
コメント