レーザー加工(レーザーカット)は、高エネルギーのレーザー光を照射して金属や樹脂を精密に切断・加工する方法です。板金加工において特に多く使われ、高速・高精度な加工が可能なため、自動車部品・精密機器・建築資材など幅広い分野で活用されています。
この記事では、レーザー加工の特徴や、設計時に考慮すべきポイントをわかりやすく解説します!
レーザー加工の特徴
✅ 高精度な切断が可能
👉 ±0.1mm以下の精度で加工できるため、精密な部品に最適!
✅ 複雑な形状も容易に加工
👉 NCデータに基づき、穴あけや細かいカットも自由自在!
✅ 型が不要で短納期対応が可能
👉 プレス加工と違い、金型を作る必要がないため、小ロット生産や試作にも適している!
✅ 熱影響が少ないが、歪みに注意
👉 材料の熱影響による歪みが発生することがあるため、厚板の場合は要検討!
✅ 材料の選択肢が広い
👉 鉄(SPCC、SS400)・ステンレス(SUS304)・アルミなど、さまざまな材料に対応!
設計時のポイント
✅ 最小切断幅(スリット幅)を考慮する
👉 一般的に0.1〜0.3mmのスリット幅ができるため、細かい形状では影響を考慮する
✅ 角部のR処理を検討する
👉 レーザー加工ではシャープな角を作ることも可能だが、応力集中を防ぐためにR処理を推奨
✅ 切断面の仕上げを考慮する
👉 一部の材料ではレーザー加工後のバリ(小さな突起)の、後処理が必要になる場合があります。
✅ 材質と板厚の適正な組み合わせを選ぶ
👉 薄板(1.0〜3.0mm)の加工が得意だが、厚板(6mm以上)では加工時間が長くなりコスト増加
✅ 加工コストを最適化
👉 細かいカットを指定するとコスト増につながるため、加工のしやすさを考慮した設計が重要!
レーザー加工における材料の厚みの注意点
レーザー加工を行う際、材料の厚みは加工精度や仕上がり、コストに大きく影響します。適切な板厚を選定しないと、加工不良やコスト増につながることがあるため、注意が必要です。
本項では、レーザー加工で板厚を考慮する際の重要なポイントを解説します!
材料の厚みが加工に与える影響
✅ 切断精度と仕上がりが変わる
▶ 薄い材料(1~3mm)は高精度な加工が可能で、切断面もきれいに仕上がる
▶ 厚い材料(6mm以上)になると、切断面が粗くなり、バリが発生しやすい
✅ レーザー出力と加工速度のバランス
▶ 薄い板: 高速で加工可能で、変形しにくい
▶ 厚い板: 加工速度が遅くなり、熱影響で歪みが出やすい
✅ 加工可能な最大板厚を超えない
▶ 一般的なCO2レーザーでは鉄は10~20mm、ステンレスは10mm程度が加工限界
▶ ファイバーレーザーでは、より厚い材料(鉄25mm以上)も加工可能
✅ 熱影響による歪みに注意
▶ 厚板を加工すると、熱による歪みや反りが発生しやすく、精度が低下することがある
▶ 特にSUS304は熱膨張しやすいため、歪みに注意!
✅ コストとのバランスを考慮
▶ 厚板の加工は加工時間が長くなり、コストが増加するため、必要最小限の厚みに抑えるのがポイント!
設計時に考慮すべきポイント
✅ 用途に応じた板厚を選ぶ
👉 精密な部品なら1~3mm程度の薄板が適している
👉 強度が必要なら6mm以上の厚板を検討
✅ 熱影響を考慮した設計
👉 大きなサイズの厚板を加工すると歪みが発生するため、熱影響を抑える工夫が必要
👉 スリット(細い切れ込み)や補強リブを設けると変形を軽減できる
✅ 加工時間とコストを意識する
👉 厚板は加工時間が長く、コスト増につながるため、できるだけ薄く設計するのが理想
✅ 後工程も考慮する
👉 厚板ではバリ取りや仕上げ処理が必要になることもあるため、後工程を考えた設計が重要
レーザー加工では、材料の厚みによって加工精度・仕上がり・コストが大きく変わります。
適切な板厚を選定することで、精度の高い加工とコストの最適化が可能になります。
設計時のポイントは以下の通りです。
✅ 精密加工なら薄板(1~3mm)、強度が必要なら厚板(6mm以上)
✅ 熱による歪みを考慮し、スリットや補強を設計する
✅ 厚板は加工時間が長く、コスト増になるため最適な厚みにする
✅ 後工程(バリ取り・仕上げ処理)も考慮する
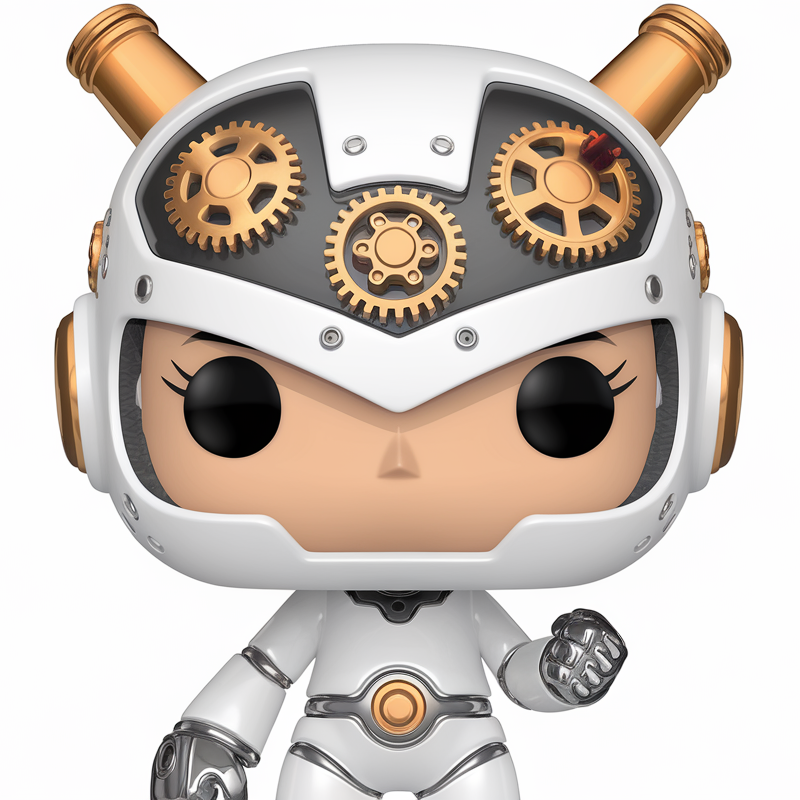
これらのポイントを押さえて、効率的なレーザー加工設計を目指しましょう!
まとめ
レーザー加工は、高精度・短納期・多様な形状に対応できる便利な加工方法です。しかし、設計時にスリット幅や熱影響、仕上げ処理を考慮しないと、思わぬ問題が発生することもあります。
設計時には、
✔ 最小切断幅を考慮する
✔ 角部のR処理を検討する
✔ 材料と板厚のバランスを取る
✔ コスト面も考慮する
といった点を意識することで、レーザー加工をより効果的に活用できます!ぜひ、実際の設計に取り入れてみてください。
コメント