製品の設計において、ねじの選定は意外と軽視されがちです。機能を果たせばいいとばかりに、部品ごとに異なる長さのねじや、呼び径の異なるねじを多用してしまうと、思わぬところで組立ミスや手間の原因になってしまいます。
特に量産現場や出荷前の検査工程では、「ねじの使い分け」が非常に面倒な作業になります。使用する工具も増え、ねじの長さを間違えて取り付けてしまうリスクも高まります。
本記事では、初心者の方にもわかりやすく「ねじや工具サイズを統一することのメリット」と「設計時に気を付けたいポイント」について解説します。
なぜねじや工具サイズを統一する必要があるのか?

まずは、ねじや工具サイズを統一することでどんなメリットがあるのかを見ていきましょう。
ねじの取り違えミスを防げる
部品ごとに「M4×12」「M4×16」「M5×20」などバラバラなサイズのねじを使っていると、組立作業者がねじを取り間違えるリスクが高まります。
実際の現場では、ねじの長さ違いを目視で区別するのは間違いの原因になり、工具で締め込んだ後に「届いていない」「飛び出している」といった不具合が発生することもあります。
工具の交換が減り、作業効率が向上
ねじの呼び径がバラバラだと、それぞれに対応するドライバーや六角レンチ、トルク管理工具を用意しなければなりません。工具交換のたびに手が止まり、作業効率が低下します。
特に多品種少量生産やセル生産方式では、作業の簡素化・標準化が重要になります。同一サイズのねじを使うことで、工具は一種類で済み、手間も減らせます。
在庫管理がラクになる
ねじサイズが統一されていれば、部品の在庫管理も簡単になります。発注や補充、数量チェックなども一括で行えるため、部品切れや発注ミスの防止にもつながります。
設計時に気をつけたい“ねじサイズ統一”のコツ
では、具体的にどのような工夫をすれば、ねじの統一ができるのでしょうか?
設計段階で意識しておきたいポイントを紹介します。
可能な限り、同一サイズのねじを使用する
- 呼び径(M4、M5など)と長さ(10mm、15mmなど)をなるべく統一します。
- 特に小型機器ではM3やM4などのサイズに絞ると良いでしょう。
- 強度的に問題がなければ、使用するねじサイズを絞ることを優先しましょう。
規格長さ(例:L=10、15、20)にそろえる
- ねじの長さは、JIS規格などで標準化されているもの(例:10mm、12mm、16mm、20mmなど)から選ぶようにします。
- 中途半端な長さ(13mm、18mmなど)は避けた方がよく、調達性も悪くなります。
- 既存のねじラインナップから選ぶことを心がけると、コストダウンにもつながります。
座ぐりやタップ深さは統一しておく
- どの部品でも「ねじ深さ12mm」などと決めておけば、設計時に毎回計算する手間が省けます。
- ねじが底突きしないよう、タップ深さとねじ長さの関係には余裕を持たせておくことも重要です。
必要な締結力に応じて例外を設ける
もちろん、すべてのねじを同一サイズにするのは難しい場合もあります。たとえば、トルクが高くかかる部分や構造上強度が必要な部分には、太いねじや長めのねじを使う必要があります。
しかし、それでも「できるだけ同じサイズを使い、それ以外は必要最小限にする」という方針を守ることで、現場の負担を大きく減らすことができます。
組立現場での具体的なトラブル事例
ここでは、ねじや工具サイズが統一されていなかったことによって発生した、実際の現場でのトラブル例を紹介します。
事例①:ねじ長さの取り違えで貫通ミス
組立作業中に、M4×20とM4×16のねじを間違えて取り付けてしまい、奥側に突き抜けて基板を破損してしまった。
🚫 原因
同じ径で長さが異なるねじを混在させていたため、作業者が混乱した。
🔍 対策
全体をできるだけM4×16で統一し、貫通が必要な箇所のみ目印付きで別梱包。
事例②:工具交換の手間で作業時間が倍に
小さな筐体の組立作業で、M3、M4、M5のねじをそれぞれ使用していたため、3種類のドライバーを使い分ける必要があり、作業時間が予定の2倍になった。
🚫 原因
機能ごとに細かくねじサイズを変えていた。
🔍 対策
一部強度を見直し、全体をM4に統一。
工具サイズの統一も重要なポイント
ねじと同じく、工具のサイズも設計段階で気を配るべきです。
✅ 六角穴付きボルトを使う場合は、六角レンチのサイズを統一することで工具の本数が減ります。
✅ トルクドライバーを使用する場合は、締め付けトルクの規格化も大切です。
✅ 工具が1本で済めば、作業スピードが格段に上がります。
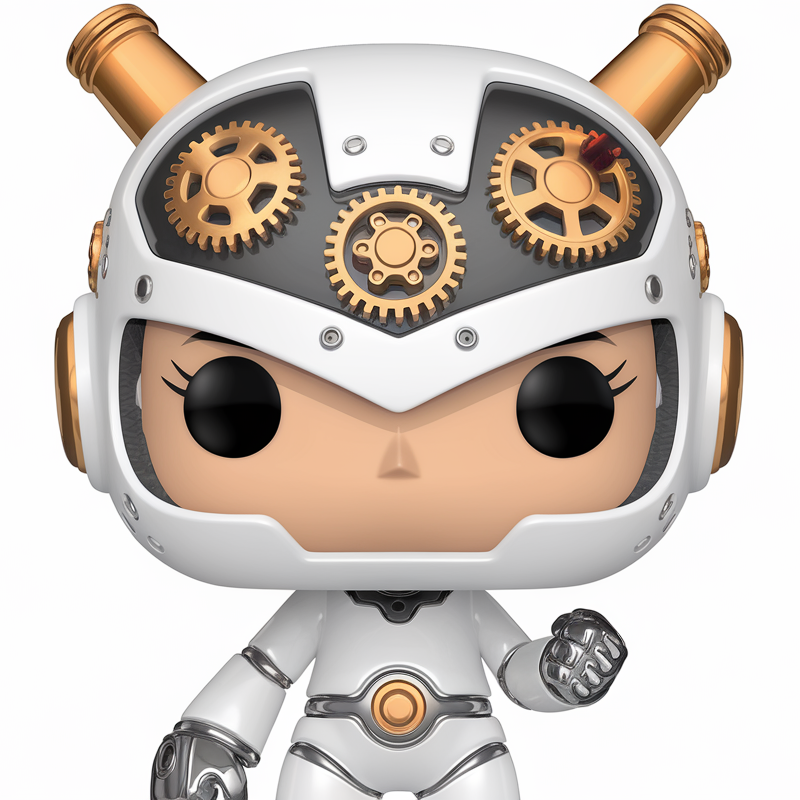
また、工具サイズが統一されていれば、自動化・省人化を進めやすいというメリットもあります。たとえば自動ねじ締め機などは、ねじサイズがバラバラだと適応が難しくなります。
ねじサイズを統一すると「タップ加工」も効率アップ!
製品や部品の設計で使う「ねじ」。
組立や分解がしやすく、再利用も可能なねじは、あらゆる機械・構造物で使われています。
しかし設計初心者がやってしまいがちなミスのひとつに、「ねじサイズを部品ごとに変えてしまう」ということがあります。
たとえば、
✅ M3、M4、M5のねじが混在
✅ 同じ呼び径でも長さがバラバラ
✅ 部品によってピッチやタップ深さが異なる
といった設計になると、組立現場だけでなく「加工現場」にも大きな負担をかけることになります。
本項では、ねじサイズを統一することで「タップ加工」がどれだけ効率的になるか、初心者にもわかりやすく解説します。
そもそも「タップ加工」とは?
タップ加工とは、ねじ穴(メネジ)をあける加工のことです。
ドリルで下穴を開けたあと、タップという工具でねじ山を切ることで、ボルトやねじが入る穴が完成します。
機械加工において非常によく使われる工程で、以下のような作業が必要です。
- 下穴径に合ったドリルで穴を開ける
- 指定されたねじサイズに合ったタップを準備する
- 旋盤やフライス、ハンドタップなどででタップ加工を行う
- 加工後、タップが折れていないか検査する
このとき、ねじサイズがバラバラだと「タップの段取り替え」や「工具交換の手間」が増えてしまいます。
タップサイズが多いと現場はどう困る?
工具の段取り替えが多くなる
たとえば、M3・M4・M5と複数サイズのタップが必要な場合、加工するたびに工具ホルダーを交換したり、切削条件を再設定したりする必要があります。
これは、マシニングセンタでのNCプログラム作成の手間も増えるということです。
さらに、タップごとに推奨の回転数や切削油条件が異なるため、設定ミスによる不良や工具破損のリスクも高まります。
タップの在庫や管理が複雑になる
工具の種類が増えるということは、それだけ在庫管理の手間が増えるということです。
- 在庫切れによる納期遅れ
- タップの使い分けミスによる不良品発生
- 保守用タップの過剰在庫によるコスト増
など、設計側が気づきにくい「加工側の負担」が蓄積します。
ねじサイズを統一すると、タップ加工がこう変わる!
ねじの呼び径(Mサイズ)をできるだけ統一しておくことで、タップ加工は驚くほど効率化します。
加工工程が標準化される
たとえば、部品ごとにM4のねじを使うと決めておけば、
- 下穴はφ3.3mmドリルで統一
- タップはM4×0.7を使用
- 回転数や切削条件も一括設定可能
となり、プログラム、工具、加工条件が共通化できます。
段取り替えが減れば、加工時間も短縮でき、生産性が向上します。
タップ工具の使い分けが不要になる
現場では、工具の使い間違いが思わぬ不良を生むことがあります。
たとえば、M5の下穴にうっかりM4のタップを使ってしまうと、ねじが全く締まらない不良穴になります。
ねじサイズが統一されていれば、タップの使い間違いが起きにくくなるため、現場の安心感も向上します。
タップ折れ・不良のリスクも低減
タップ加工でよくあるトラブルが「タップの折損」です。
サイズが異なるタップを頻繁に交換していると、正しい条件設定が難しくなり、破損のリスクが高まります。
また、タップ折れはその後の除去や再加工に大きなコストと手間がかかるため、極力避けたいトラブルです。
ねじサイズを絞って統一することで、条件設定も安定し、タップ破損のリスクも減少します。
設計者ができる「ねじ統一」の工夫ポイント
呼び径を1〜2種類に絞る
🔍 例)
小型部品ではM3・M4、中型以上ではM4・M5など、用途に応じてサイズを決めておくと◎。
長さも規格寸法で統一する
L=10、15、20mmなど、JIS規格の標準長さから選ぶと、入手性も良く在庫管理も簡単です。
高トルク箇所のみ例外として使い分ける
どうしても大きな力が必要な部分(軸受け部、回転部など)では、M8やM10などを使う必要がある場合もあります。
その場合は「例外」として使い、必要最小限の種類にとどめることが大切です。
ねじサイズの統一は加工現場への“思いやり”
ねじサイズを統一することで、
- 組立効率アップ
- 工具管理が簡素化
- タップ加工の段取り削減
- 不良率の低下
- 加工コストの削減
といったメリットが得られます。
タップ加工は、地味ながらも部品品質を左右する重要な工程です。
加工現場の負担を減らす設計は、製品の信頼性を上げる近道です。
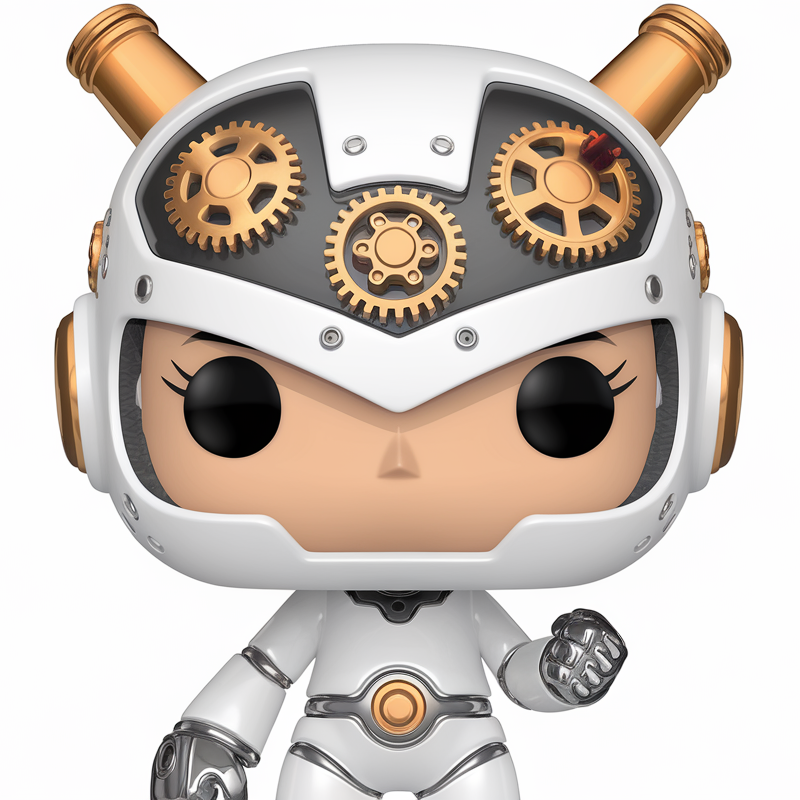
設計者が「現場目線」を持つことで、製品全体の品質と生産性が向上します。
ぜひ次の設計から、ねじサイズの統一を意識してみてください!
まとめ:ねじサイズと工具の統一でミスゼロ&効率UP!
ねじの長さや呼び径、使用工具をなるべく統一することで、
✔ 組立ミスを防止
✔ 工具交換の手間を削減
✔ 作業時間の短縮
✔ 在庫管理の簡素化
といった多くのメリットが得られます。
すべてを統一するのは難しくても、「できるだけ少ない種類にまとめる」ことを意識するだけで、設計品質と作業性が大きく向上します。
現場の使い勝手に配慮した設計は、信頼される設計者への第一歩です。ぜひ今日から、ねじと工具の「統一」を意識してみてください。
コメント