機械設計において「精度が高い=良いもの」というイメージはよくあります。しかし、実際には高精度を追求することで加工費や納期が大幅に増えることもあり、常に最善とは限りません。
この記事では、高精度を求めることによるコスト・納期への影響、そして設計者が考えるべき「バランス」について、初心者にもわかりやすく解説します。
高精度って何を意味する?
機械設計における「精度」とは、部品の寸法や位置が設計通りにどれだけ正確に作れるかを示すものです。
💡 たとえば、、、
✔ 寸法公差(±0.01mmなど)
✔ 平行度、直角度、同心度などの幾何公差
✔ 表面粗さ(Ra 1.6 など)
これらの数値が小さければ小さいほど、精度が高い部品とされます。
高精度が必要な場面
もちろん、高精度が必要な設計もあります。
💡 たとえば、、、
- ベアリングが入る穴(H7やH6などの厳しいはめあい)
- 精密位置決めをする装置(±0.01mm単位での制御)
- 光学系や電子部品の取り付け部(ズレが性能に直結)
このような場合には、高い精度は性能を左右する重要な要素となります。
高精度=高コストの理由
では、なぜ精度を上げるとコストや納期が上がってしまうのでしょうか?
主な理由は次のとおりです。
加工工数が増える
- 高精度にするには、高価な精密加工機械が必要
- 荒加工 → 中仕上げ → 仕上げ と工程が多段階になる
- 加工後の検査や測定も高度な機器や熟練作業者が必要
不良率が上がる
- 許容範囲が狭いため、少しのズレでもNG品になる
- 歪みや反りが許されないため、加工条件が非常にシビア
納期が延びやすい
- 高精度部品は特別な加工設備や外注が必要になることも多く、
- 小ロットでも時間がかかる傾向があります
精度指定のやりすぎは要注意!
初心者がやりがちなミスとして、「とりあえず全部H7で!」「0.01mm単位で揃えよう!」と、過剰な精度を指定してしまうケースがあります。
たとえば、こんなことが起こります。
ケース | 問題点 |
---|---|
取付穴を全部H7公差にした | 穴あけの精度が必要→ボーリング加工が必要→加工費UP |
±0.01mmの寸法公差を多用 | 通常のNC加工機では対応できない→研削工程が必要 |
表面粗さRa 0.4の面を多く指定 | 鏡面仕上げが必要→時間も費用も大幅増 |
必要以上の加工費と納期が発生し、設計自体が非現実的になることも。
どこまで精度を求めるべきか?判断のコツ
設計者が考えるべきは、「必要な機能を満たす最低限の精度」です。以下のような観点で判断しましょう:
重要な部位には必要な精度を
- 軸と穴の嵌合部、ベアリング取付部などははめあい公差をしっかり指定
- 位置決め用の穴や基準面は高精度な幾何公差が必要
影響が少ない部分は緩めてOK
- 外観だけのカバーや取手など → 広めの公差で十分
- 他部品と干渉しない内部空間など → ±0.1mmでも問題なし
加工しやすい設計を心がける
- 可能であれば一般公差を使う
- 面取りや逃げ形状などで加工性を向上させる
精度とコストのトレードオフ事例
事例 | 高精度設計 | コスト・納期への影響 |
---|---|---|
軸穴にH7/g6を指定 | 高精度な研削が必要 | 工数・加工費UP |
±0.01mmの板金加工 | 難易度が非常に高い | 外注+納期長期化 |
精密加工部品を多数使用 | 部品単価が高くなる | 製品コスト増 |
高精度を求めるなら軸加工の方が有利?〜穴加工との違いとコストの関係〜
機械設計をしていると、よく「高精度なはめあい」が求められる部品があります。特に軸と穴の組み合わせは、モーターやベアリング、ギアの取り付けなど、多くの場所で登場します。
ところが、同じ精度を要求しても、「穴加工よりも軸加工の方が安くて早い」という事実は、意外と知られていません。
この記事では、軸加工と穴加工の違いを初心者にもわかりやすく解説しながら、高精度加工におけるコストと納期のトレードオフについて説明します。
軸と穴、どちらもはめあいが必要な部品
まず、はめあいとは何か簡単におさらいしましょう。
はめあいとは、軸と穴を一定のすき間や圧力で組み合わせるために、公差(寸法の許容範囲)を決めて設計することです。
🔍 たとえば、、、
- すきまばめ:軸が穴より小さく、スムーズに入る(例:回転軸)
- しまりばめ:軸が穴より少し大きく、圧入される(例:ギアの圧入)
- 中間ばめ:ほぼ同じサイズで、軽く圧入(例:ピンの挿入)
ここで重要になるのが、「軸側を精度良く仕上げるか、穴側を精度良く仕上げるか」という選択です。
なぜ穴の高精度加工はコストが高くなりやすいのか?
軸と穴のどちらに高精度を持たせるかで、加工の難易度とコストが大きく変わります。
穴加工の高精度が難しい理由
🚫 内側は工具が制限される
- 穴の中は狭くて見えにくく、工具も限られるため、加工・測定の難易度が高い。
- 高精度な穴には、リーマ加工やボーリング加工が必要。
- これらは時間がかかり、コストも高め。
🚫 測定に専用ゲージが必要
- 穴径の正確な測定は難しく、プラグゲージやエアマイクロなど専用測定器具が必要。
- 測定作業自体に時間と技術が必要。
🚫 仕上げミスのリスクが高い
- 穴の深さ・材質・形状によっては芯ズレやテーパー形状になりやすく、不良リスクが上がる。
- 再加工が難しいため、一発勝負で精度が必要。
軸加工は高精度でも比較的容易
一方で、軸の外径加工は比較的コストがかかりにくい理由があります。
軸加工のメリット
✅ 加工機械が豊富
- 旋盤やNC旋盤など、高精度な外径加工に特化した設備が整っている。
- 精密旋削や研削加工により、0.001mm単位の加工も比較的容易。
✅ 測定がしやすい
- 軸の直径はノギスやマイクロメータなどで手軽に測定できる。
- 測定値が読みやすく、作業者のミスも少ない。
✅ 工程が安定しやすい
- 外周加工は形状や素材の変動に影響されにくく、安定した精度が出しやすい。
設計時のおすすめ:穴は広め、軸を精度管理
多くの設計現場では、次のような方針がよく採用されます。
穴は広めの公差(H7など)にし、軸で精度調整(g6、h6など)する。
このようにすると
- 穴側は汎用的な加工方法(リーマ加工など)で済む。
- 軸側で旋盤加工や研削により寸法を細かく制御できる。
- 結果として、全体の加工費と納期が抑えられる。
具体的なコスト比較(参考例)
項目 | 穴(高精度) | 軸(高精度) |
---|---|---|
加工方法 | ボーリング、リーマ仕上げ | 旋削、外径研削 |
加工コスト | 高い(工具代、工数) | 比較的安い |
測定難易度 | 高い(専用ゲージ必要) | 低い(汎用測定器でOK) |
納期への影響 | 長くなる傾向 | 比較的短い |
安定性 | やや不安定(芯ズレ等) | 安定しやすい |
設計者としての注意点
もちろん、すべての場面で軸精度の方が良いとは限りません。以下のようなケースでは注意が必要です。
- 軸を交換する機会が多い:交換用軸の加工精度が重要。
- 量産品で穴側が成形される(例:金型品):穴寸法が固定になるため、軸側の制御が必要。
- 材質が非常に硬い:軸の加工も難しくなる。
→ こうした条件も含めて、加工性・測定性・コストを総合的に判断することが大切です。
高精度なら「穴より軸」が原則
初心者が高精度な部品設計をする際には、以下のポイントを意識しましょう。
✅ ポイントまとめ
✔ 穴の高精度加工はコスト・納期ともに不利
✔ 軸の高精度加工は加工・測定がしやすく、コストを抑えやすい
✔ 設計では「穴は広め、軸で調整」が基本
✔ 実際の使い方や組立条件も考慮して判断する
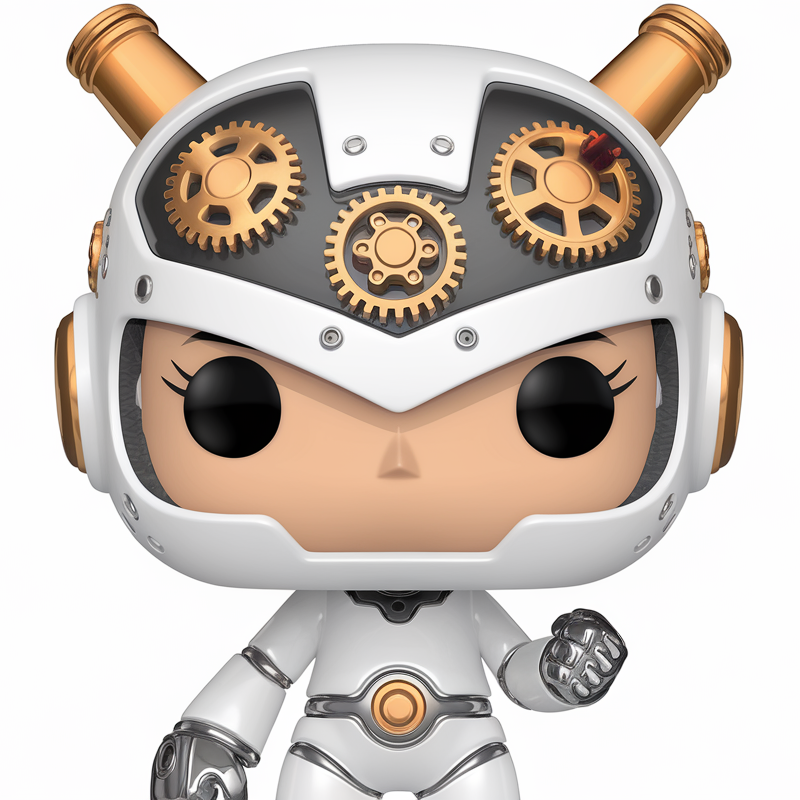
高精度な設計には必ず「加工とのバランス」が求められます。
コスト・納期・精度のすべてを見ながら、加工者にも優しい設計を心がけましょう。
まとめ:精度とコストはトレードオフ!最適なバランスを探そう
機械設計では、「精度を上げれば良い」という単純な発想ではなく、「目的に必要な精度だけを確保する」ことが重要です。
覚えておきたいポイント
✔ 高精度ほどコストも納期も大きくなる
✔ 精度指定のやりすぎはNG
✔ 「必要な精度」と「許容できるズレ」を見極めよう
設計のゴールは「図面通りに作ること」ではなく、「機能・性能を満たす部品を効率的に作ること」です。精度と加工性・コストのバランスを意識して、ムダのないスマートな設計を心がけましょう!
コメント