溶接は、機械設計における接合方法のひとつで、金属同士を強固に一体化する加工技術です。ボルトやリベットと違い、継ぎ目のない構造を作ることができるため、高強度・高剛性な構造体を実現できます。
設計者として溶接の特性や注意点を理解しておくことは、適切な構造設計や製造コストの最適化につながります。
ここでは初心者の方にもわかりやすく、溶接の基礎知識と設計のポイントを紹介します。
溶接の主な種類
アーク溶接(手溶接)
▶ 最も一般的な方法。電気アークの熱で母材と溶接棒を溶かして接合。
✅ 利点:設備が簡易で対応範囲が広い。
🚫 欠点:熟練工による品質差が出やすい。
半自動溶接(CO₂/MAG溶接)
▶ 溶接ワイヤが自動供給されるため作業効率が良い。
✅ 利点:大量生産に向いており、均一な品質が得られる。
🚫 欠点:屋外作業には不向き(風でシールドガスが流れる)。
TIG溶接(アルゴン溶接)
▶ 非消耗電極と不活性ガスを使用し、高精度な溶接が可能。
✅ 利点:ステンレスやアルミなど非鉄金属に適しており、美しい仕上がり。
🚫 欠点:作業速度が遅く、熟練が必要。
スポット溶接
▶ 主に薄板同士を圧力と電流で接合。
✅ 利点:自動化しやすく、量産向け。
🚫 欠点:厚板や広範囲の溶接には不向き。
溶接のメリットとデメリット
項目 | メリット | デメリット |
---|---|---|
構造 | 継ぎ目がないため、軽量かつ高剛性 | 溶接部に歪みや残留応力が発生 |
コスト | ボルトやリベットが不要で部品点数を削減 | 熟練工や溶接治具が必要になる場合も |
設計の自由度 | 複雑形状でも接合可能 | 溶接後の修正が難しい |
強度 | 高強度な接合が可能 | 衝撃や疲労に弱い場合がある |
設計時の注意ポイント
✅ 溶接方法を考慮した設計
- 板厚、材料、接合部の形状により適切な溶接方法を選定。
- 例:ステンレス板であればTIG溶接、構造用鋼板にはCO₂溶接が一般的。
✅ 溶接後の歪み対策
- 溶接熱による変形や反りを考慮し、溶接順序や治具設計を工夫。
- 事前の「歪み見込み」設計や対称溶接が有効。
✅ 強度設計と溶接部の配置
- 応力集中を避けるために、曲げ部や高応力部に溶接線を入れない。
- 溶接部には「応力緩和」のための逃げ加工やフィレット処理を行う。
✅ 材料の溶接性
- 材質により溶接性が異なる(※後述)。
- 炭素鋼(SS400など)は溶接性が良好、ステンレスやアルミは技術を要する。
✅ 検査方法の検討
- 目視検査、浸透探傷検査(PT)、超音波探傷検査(UT)などを使って品質を担保。
- 設計段階で検査方法と精度基準を定めておく。
溶接後に加工が必要な理由とは?
溶接は、部品同士をしっかりと接合できる非常に便利な加工方法です。しかし、溶接しただけでは寸法が正確にならないことが多く、図面通りの精度を実現するためには「溶接後の加工」が必要になるケースがあります。
本項では、なぜ溶接後に加工が必要なのか、どのような場所に加工が必要になるのかについて、わかりやすく解説します。
溶接すると、なぜ寸法が狂うの?
溶接は高温の熱で金属を一体化させるため、以下のような影響が出ます。
✅ 熱による歪み
- 溶接部に集中して加熱
- 急冷される過程で金属が収縮
- 部材が引っ張られるように「歪み」が発生します。
✅ 熱膨張と収縮
溶接時に金属が一時的に膨張し、冷めると収縮します。このとき、元の寸法とズレが生じることがあります。
✅ ビード(盛り上がり)の影響
- 溶接した部分には「ビード」と呼ばれる盛り上がりができます。
- そのままでは他の部品と干渉することがあります。
寸法確保が必要な代表的な例
ベース面や取り付け面
✅フレームやブラケットなど、他部品と接触する面は、溶接後に反ったり膨れたりする可能性があります。
👉 溶接後にフライス加工などで「面出し」をして、平面度や寸法精度を確保する必要があります。
ボルト穴・軸穴
✅溶接熱で部材がわずかに変形すると、穴の位置がズレることがあります。
👉 溶接後に正確な位置に穴あけ加工やリーマ加工を行って仕上げます。
ガイドレールの取付面
✅リニアガイドやボールねじなど、精密な位置決めが必要な部品は特に注意。
👉 寸法だけでなく直角度や平行度も重要なため、溶接後に精密な機械加工が必須です。
溶接後加工の方法と注意点
加工方法 | 内容 | 使用例 |
---|---|---|
フライス加工 | 平面を削って精度を出す | ベース面の仕上げなど |
旋盤加工 | 丸物の内外径を仕上げる | パイプ溶接後の端面仕上げ |
ボーリング加工 | 溶接後の穴仕上げ | 軸受け部や取付穴 |
グラインダー仕上げ | ビード除去や仕上げ | 表面の干渉対策 |
🚫注意:溶接後は材料が硬化していることもあるため、切削条件の調整や工具選定も重要です。
図面での設計ポイント
▶ 加工基準を明記する
どこを基準にして寸法を出すかを図面で指示
▶ 後加工のマークをつける
例)溶接後フライス仕上げ「▽」などを記載
▶ 溶接順序と加工順序を考慮
なるべく後加工がしやすい形状に設計する
溶接は便利な接合手段ですが、「溶接すれば完成!」というわけではありません。
寸法精度を求められる部位は、溶接後に加工が必要になるケースが多くあります。
初心者の方は次のポイントを押さえておきましょう。
✅ 溶接すると歪みや熱収縮で寸法が狂う
✅ 寸法精度が必要な面や穴は、溶接後に加工するのが基本
✅ 設計段階で「後加工ありき」で図面を描くと、現場との連携がスムーズになる
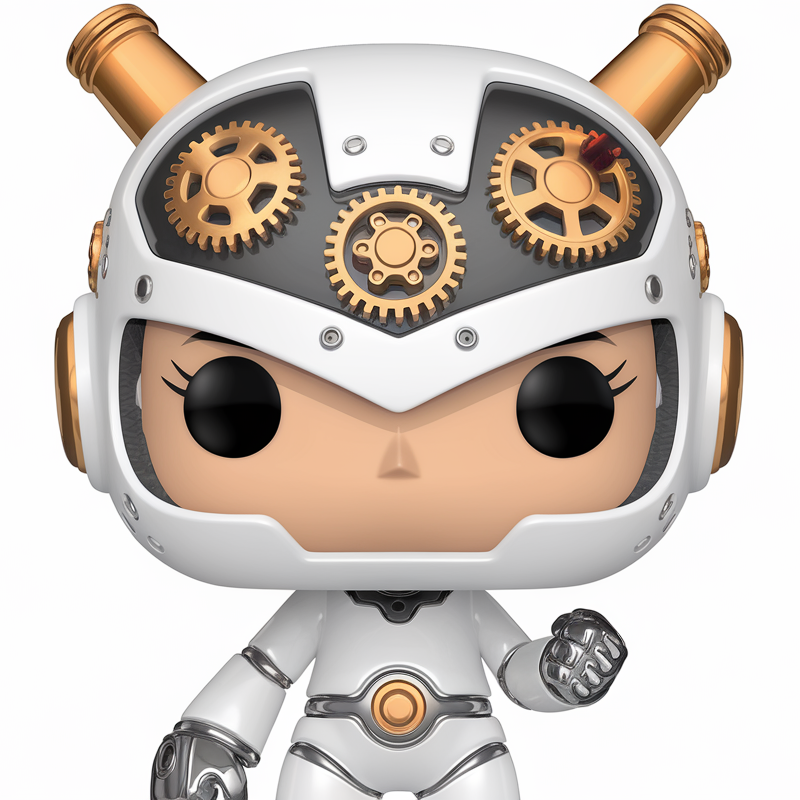
しっかりと寸法精度を確保することで、製品の組立性や信頼性が大きく向上します。
設計と製造をつなぐ大切な考え方として、ぜひ覚えておきましょう!
材料ごとの溶接性のポイント
材料 | 溶接性 | 特徴・注意点 |
---|---|---|
SS400(一般構造用鋼) | ◎ 良好 | 一般的な構造材として使用される |
S45C(炭素鋼) | △ 条件次第 | 前後熱処理や予熱が必要になる場合あり |
SUS304(ステンレス鋼) | ○ 難易度中 | 熱歪み・クラックに注意。TIG溶接が主流 |
アルミ合金 | △ 難易度高 | 酸化皮膜を除去しながら溶接が必要。専門技術が必要 |
溶接を取り入れる設計例
- 架台設計
- 角パイプやチャンネル材のフレームを溶接で接合し、軽量・高剛性を実現。
- ブラケット部品
- L字の部品を板金+溶接で構成し、ボルトレス化。
- 筐体・カバー
- 薄板同士をスポット溶接で簡易に組立。
溶接の図面指示のポイントと注意点
なぜ溶接の図面指示が重要なのか?
図面で適切に溶接指示がされていないと、以下のような問題が発生します。
✅ 作業者によって解釈が異なり、溶接品質がバラつく
✅ 強度不足や過剰な溶接が起こり、不具合やコスト増加
✅ 組立性や後加工との干渉が生じ、手戻りが発生
つまり、誰が見ても同じ品質で作れるようにするのが図面指示の目的です。
図面での溶接指示のポイント
📌 明確な位置と向きを示す
- 矢線がどちらの面を示しているかを意識しましょう。
- 表側・裏側で異なる溶接を行う場合は、基準線の上下の違いで指示します。
📌 サイズや長さは省略しない
- 脚長や溶接長を数値で明記しましょう。
- 曖昧な「一部溶接」「適宜」は極力避け、具体的に記載します。
📌 特殊な溶接条件は備考に記載
- 必要なら溶接記号とは別に表形式で一覧化してもよいです。
- 例:「隅肉溶接脚長6mm、連続溶接、仕上げ不要」
溶接指示でよくある注意点
NG例 | 問題点 |
---|---|
指示のない箇所が溶接されていた | 明確な指示不足。誰が見てもわかるように記載を。 |
必要な溶接が見落とされていた | 組立工程や構造を考慮して全て記載。 |
過剰な全周溶接を指示 | 強度過剰&コスト増。必要な箇所だけに絞る。 |
溶接指示は「設計者の意思表示」
溶接の図面指示は、単に線や記号を書く作業ではなく、設計意図を正確に伝える重要な工程です。
初心者の方はまず次のポイントを意識しましょう。
▶ JISなどの標準的な溶接記号を覚える
▶ 寸法・溶接箇所・向きなど、誰が見ても迷わないように指示
▶ 図面上で表しにくい内容は、備考欄や別表で補足
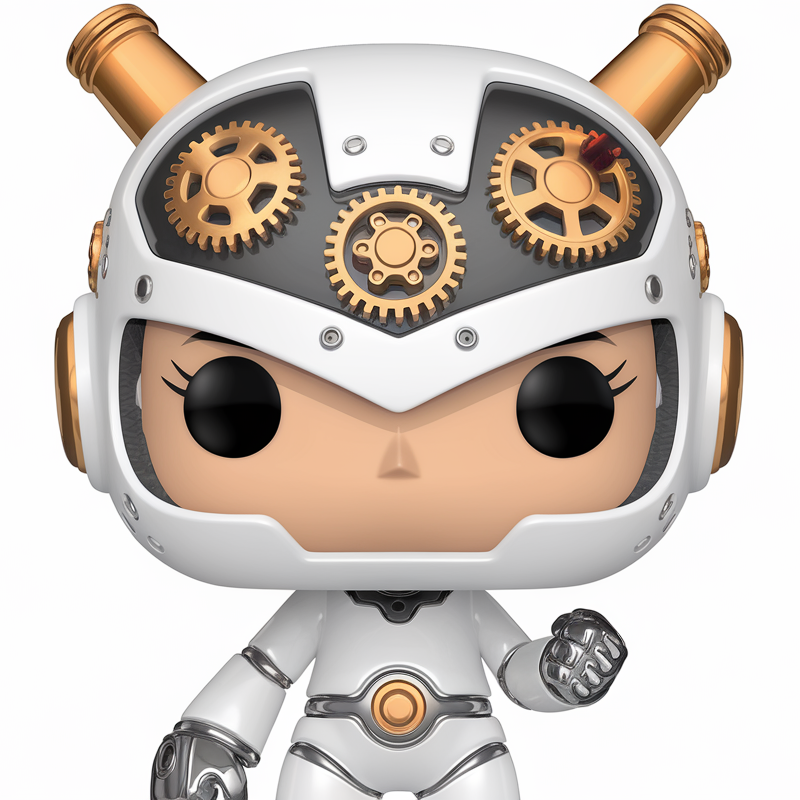
溶接構造は強度・コスト・加工性に大きく関わるため、図面での適切な指示は非常に重要です。
実際の製造現場とのコミュニケーションを意識して、より伝わる図面を目指しましょう!
図面での溶接指示の記載例
- 溶接記号(JIS Z 3021)を使って接合方法を記載
例:フィレット溶接、突合せ溶接、全周溶接など - 必要に応じて「連続長さ」「間隔」「溶接サイズ(脚長など)」も指示
- 溶接後処理(グラインダー仕上げ、ビード残し、非破壊検査)も記載すること
まとめ
溶接は、部品同士を一体化する強力な接合手段であり、機械設計の中で非常に多用されます。
ただし、熱による歪み、応力、材料特性への影響など、設計時に考慮すべき点も多くあります。
設計者としては以下を押さえることが重要です。
✔ 使用する溶接方法と材料の適性
✔ 熱による影響(歪みやクラック)
✔ 強度や検査方法の確保
✔ 図面での明確な溶接指示
これらを意識することで、現場との連携が取りやすくなり、信頼性の高い製品設計につながります。
コメント