機械設計では、部品や構造物の性能を確保するために適切な材料を選定することが不可欠です。その中で見落とされがちなのが「残留応力」の問題です。残留応力を十分に考慮しないと、設計通りの性能が発揮できなかったり、予期せぬトラブルが発生することがあります。この記事では、残留応力の基本や、設計および材料選定時に重要なポイントについて解説します。
残留応力とは?
残留応力とは、外部からの力が加わっていない状態でも材料内部に存在する応力のことです。この応力は、製造プロセス(圧延、鍛造、溶接、熱処理など)や機械加工の過程で発生します。
代表的な残留応力の原因
✅ 加工応力:切削や圧延などの機械加工によるもの。
✅ 熱応力:溶接や熱処理での急激な温度変化によるもの。
✅ 構造応力:複雑な形状の部品で、均一に応力が分散しない場合に発生。
残留応力が引き起こす問題
残留応力が材料や部品に与える影響は大きく、以下のような問題を引き起こします。
🚫寸法変化
- 加工後や熱処理後に材料が変形することがあります。
- これにより、設計した寸法公差を逸脱してしまう場合があります。
🚫疲労強度の低下
- 残留応力があると、繰り返し荷重に対する耐性が低下し、部品の寿命が短くなることがあります。
🚫応力腐食割れのリスク増加
- 残留応力があると、材料が腐食環境下で割れやすくなることがあります。
🚫組立不良
- 残留応力による寸法変化や歪みにより、部品の組立精度が悪化する場合があります。
機械設計における残留応力とその影響 〜変形・割れのリスクとは〜
機械設計において、材料の強度や剛性を考慮することは非常に重要ですが、それと同じくらい「残留応力」にも注意を払う必要があります。残留応力を適切に管理しないと、加工後の変形や割れの原因となり、設計通りの性能を発揮できなくなる可能性があります。
残留応力による変形・割れの問題点
変形(寸法の狂い)
残留応力が材料内部に不均一に分布していると、時間の経過や追加加工(切削・研削など)によって応力が解放され、部品が反る・ねじれる・縮む といった変形が発生します。
📌 具体例
- 精密加工後に歪みが発生 → 平面度や直角度が狂い、組み立て時に不具合が発生
- 溶接後の歪み → 長尺部品がそり上がる
🔍 対策
✅ 応力除去焼鈍(ストレスリリーフ) を行い、加工後の応力を緩和する
✅ 交互加工(切削→焼鈍→仕上げ加工)を取り入れる
✅ 材料の選定(内部応力の少ない鋳造材や熱処理済みの材料を使用)
割れ(破壊)
残留応力が蓄積すると、外部からの荷重がなくても材料が破壊する ことがあります。特に、引張の残留応力が大きいと、微細なクラック(ひび)が成長し、最終的に破壊に至ります。
📌 具体例
- 焼入れ処理後の割れ → 急冷時の内部応力差により、割れが発生
- 溶接部の割れ → 熱膨張と収縮の影響で引張応力が生じ、微細なひび割れが発生
🔍 対策
✅ 焼入れ後に焼戻し処理を行い、内部応力を低減する
✅ 溶接時に徐冷(ゆっくり冷やす)して、急激な温度変化を避ける
✅ ショットピーニング処理などで表面に圧縮応力を与え、引張応力を抑える
残留応力を適切に管理することで、設計通りの精度や強度を確保し、長期的に安定した機械部品の性能を発揮 させることができます。ぜひ、設計や加工の際に意識してみてください!
残留応力を考慮した材料選定のポイント
材料選定の際には、以下の点を考慮することで残留応力の影響を最小限に抑えることができます。
残留応力の少ない材料を選ぶ
✅黒皮材
熱間圧延状態の材料で内部応力が少ない。荒加工に適しています。
✅焼鈍材
焼鈍処理によって内部応力を解放した材料。高い寸法安定性が求められる場合に適しています。
✅6F材
さらに精密な用途向けに処理された材料で、加工後の変形が少ない。
適切な熱処理を行う
熱処理(焼鈍、時効処理、応力除去焼き戻しなど)を施すことで、材料内部の応力を緩和することができます。
加工プロセスを見直す
加工の手順や条件を最適化し、応力が偏在しないようにすることが重要です。例えば、対称的な加工や、切削量を均一にすることで歪みを抑えることができます。
材料形状を工夫する
加工変形を防ぐには、材料の選定だけでなく、加工形状や設計の工夫も必要です。以下に具体的な方法を示します。
対称形状を設計する
部品形状が非対称だと、加工時の応力が一方向に集中しやすくなります。その結果、材料が偏った方向に変形する可能性が高くなります。
🔍対策
- 対称形状に設計することで、加工時の応力を均等に分散する。
- 機械加工が必要な部分を対象として均一に肉厚を確保する。
板材や長尺部品の肉厚を均一化する
板材や長尺部品を加工する際、肉厚が不均一だと応力が集中し、反りやねじれが発生しやすくなります。
🔍対策
- 肉厚が均一になるよう設計する。
- 必要以上に薄肉化しない。
内部応力を軽減するための予備加工
仕上げ加工前に材料内部の応力を均等化するために予備加工を行います。
🔍具体例
- 粗加工後に自然時効を設ける(加工後に時間を置いて内部応力を緩和)。
- 粗加工後に焼鈍(ストレスリリーフ)を実施し、応力を軽減する。
開口部やコーナー形状の工夫
大きな穴や急なコーナー形状は応力集中を引き起こしやすく、加工後の歪みにつながります。
🔍対策
- 開口部の角を丸くする(R加工を適用)。
- 不要な開口部や穴加工を避けるか、必要最小限に設計する。
加工順序を最適化
切削加工時の残留応力は、加工順序によっても影響を受けます。先に加工する部分の応力が後の加工部分に影響を与えることがあります。
🔍対策
- 応力を均等に分散する加工順序を計画する。
- 大きな切削を伴う加工を後回しにせず、前半で行う。
黒皮材や焼鈍材の活用
- 材料選定の段階で、加工変形を抑える材料を選ぶことも効果的です。
- 黒皮材や焼鈍材は内部応力が少なく、加工変形を低減できます。
🔍設計段階での考慮
残留応力の影響を完全に取り除くことは難しいですが、設計段階で以下を意識することで、加工変形を最小限に抑えることが可能です。
✅材料の選定時に応力が少ない材料を選ぶ(例: 焼鈍材や熱処理済み材料)。
✅応力集中が起きない形状設計を行う(肉厚の均一化、R加工)。
✅加工後の変形を考慮した公差設計を行う。
残留応力は加工時に避けられない課題の一つですが、設計段階で適切な形状や材料を選び、加工方法を工夫することで影響を大幅に軽減できます。また、予備加工や焼鈍処理を適切に組み合わせることで、最終的な製品の精度を確保できます。
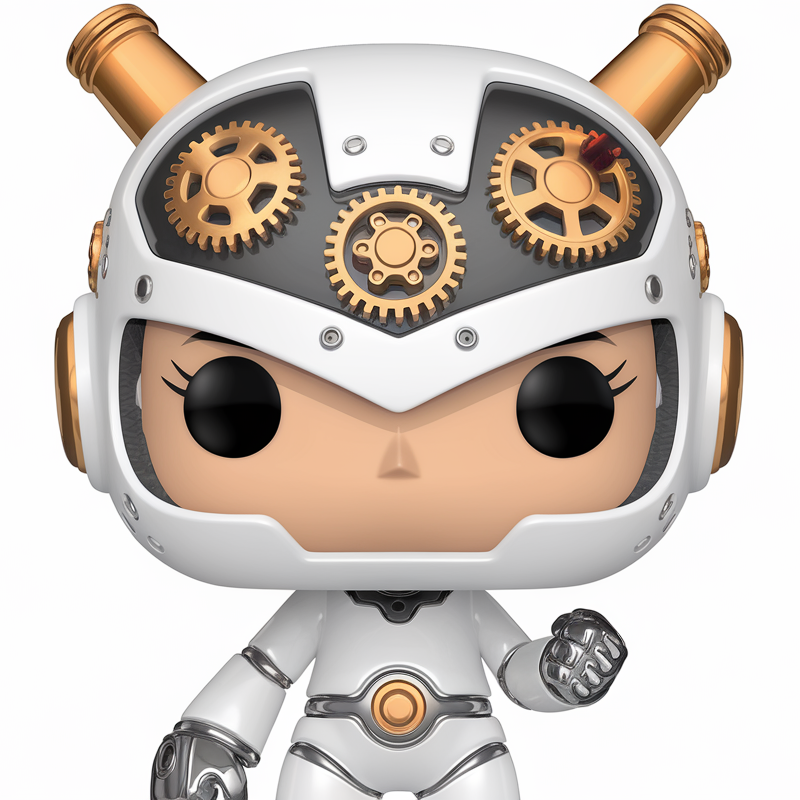
材料選定と設計の段階で残留応力を考慮することが、高品質な製品を効率的に作る鍵となります。
まとめ
機械設計において、残留応力を正しく理解し、適切に対策を講じることは、設計者としての重要な責務の一つです。残留応力は、材料内部に見えない形で蓄積し、設計意図に反した部品の変形や性能低下を引き起こす要因となるため、設計段階からその存在を考慮する必要があります。例えば、加工後の変形や疲労強度の低下、応力腐食割れといった問題を未然に防ぐには、材料の選定や加工方法、さらに熱処理プロセスを緻密に計画することが求められます。
材料選定においては、残留応力の少ない黒皮材や焼鈍材、6F材などの使用を検討し、目的や使用環境に応じて適切な材料を選ぶことが重要です。また、加工段階での工夫も大きな効果を発揮します。たとえば、対称的な切削を行う、切削深さを均一に保つ、加工部の形状を工夫するなど、残留応力の偏在を防ぐ手法は多岐にわたります。
さらに、熱処理を利用して残留応力を解放することも有効な方法です。焼鈍や応力除去焼き戻しを適切に活用することで、部品の寸法安定性や性能が向上し、最終的な製品の信頼性が大きく高まります。これらの手法は短期的には追加のコストや時間が発生するかもしれませんが、長期的にはトラブルを防ぎ、製品寿命を延ばすことで結果的にコスト削減にもつながるでしょう。
また、残留応力の測定技術も積極的に活用すべきです。X線回折法や穴あけ法、ストレインゲージ法など、状況に応じた適切な測定手法を用いることで、部品内部の応力状態を把握し、設計や製造プロセスの改善に役立てることができます。
残留応力は、適切に対策を講じなければ設計や製造工程で思わぬ問題を引き起こす一方、事前に十分な考慮を払うことで、トラブルを防ぐだけでなく、製品のパフォーマンス向上にも寄与する大きなポイントです。機械設計において、単に強度や加工性だけを重視するのではなく、残留応力の影響まで考慮した材料選定や設計を行うことで、より高品質な部品や製品を実現することが可能になります。
最終的に、設計者としての役割は、信頼性の高い製品を効率的に作り上げることです。そのためには、残留応力という目に見えない要因を軽視せず、材料選定から加工、熱処理、測定に至るまでの各プロセスを慎重に検討し、製品の信頼性と寿命を確保することが大切です。この意識を持つことで、トラブルのリスクを軽減し、設計の精度を高めることができるでしょう。
コメント