機械設計では、回転運動を基準にして動作を制御する機構が多く使われます。その中で、「1回転シャフト」は、機械の動作サイクルを確実に管理し、正確な制御を行うための重要な要素です。
本記事では、1回転シャフトの基本的な特徴と、その活用方法について詳しく解説します。
1回転シャフトとは?
1回転シャフトとは、機械の動作サイクルを1回転(360°)を基準として管理するために設定する回転軸のことです。
通常、機械の動作は一定の周期で繰り返されます。そのため、回転軸を基準にして動作のON/OFFや制御タイミングを決めることが一般的です。
例えば、次のような機械に1回転シャフトが活用されます:
- 包装機械 → 1回転ごとに1つの製品を包装
- プレス機 → 1回転ごとに1回の成形動作を実行
- 充填機 → 1回転ごとに1つの容器へ充填
このように、機械の動作を360°単位で管理することで、精度の高い動作が可能になります。
1回転シャフトの特徴
動作サイクルの基準となる
1回転シャフトは、機械の各工程が正しく動作するための「基準」となります。
例えば、カムポジショナーやエンコーダを使って回転角度を測定する場合、1回転(360°)を基準にすることで、以下のメリットがあります:
✅ 回転軸の位置を常に一定の範囲(0°〜360°)で管理できる
✅ 動作のズレを防ぐことができる
1回転が基準となることで、異常が発生した場合でも、どの角度で問題が起きたのか特定しやすくなります。
カム機構やセンサー制御に適している
カム機構やカムポジショナーでは、1回転シャフトを基準にすることで、ON/OFFのタイミングを正確に設定できます。
例えば、包装機械で「カッターを180°でON、240°でOFF」と設定すると、常に正確なタイミングで包装が完了します。
また、エンコーダやレゾルバと組み合わせることで、高精度な制御が可能になります。
タイミング制御をシンプルにできる
機械の動作を1回転(360°)で区切ることで、制御ロジックをシンプルにできます。
例えば、1回転ごとにON/OFFを制御する場合、カムプログラムを設定しやすくなります。
✅ 90°で開始
✅ 180°でON
✅ 270°でOFF
このように、回転角度を基準に動作を設定することで、設定ミスを防ぐことができます。
1回転シャフトの活用方法
カムポジショナーと組み合わせた精密制御
カムポジショナーを使用すると、1回転シャフトの角度データをもとに、特定の位置で機械の動作をON/OFFできます。
📌 活用例:食品包装機械
✅ 0°~120°:フィルム送り
✅ 120°~180°:カット
✅ 180°~360°:待機
このように、カムポジショナーと1回転シャフトを組み合わせることで、正確なタイミング制御が可能になります。
エンコーダと連携して動作のズレを防ぐ
エンコーダを1回転シャフトに取り付けることで、回転角度をデジタル信号として取得できます。
📌 活用例:プレス機のストローク制御
✅ エンコーダで回転角度を測定
✅ 180°でストローク開始
✅ 360°で終了
エンコーダを使用することで、動作のズレをリアルタイムで補正でき、安定した制御が可能になります。
センサーと組み合わせて位置決めを正確にする
1回転シャフトの回転角度に応じて、リミットスイッチや光電センサを配置すると、正確な位置決めが可能になります。
📌 活用例:充填機のタイミング制御
✅ 90°:容器搬送
✅ 180°:充填開始
✅ 270°:充填終了
センサーと1回転シャフトを組み合わせることで、動作のズレを防ぎ、安定した生産が可能になります。
機械設計における1回転シャフトを活用した設備間の同期方法
製造ラインや自動機では、複数の設備が連携して動作することが一般的です。例えば、コンベアで部品を搬送し、加工機で成形し、検査機で品質をチェックするなど、各設備が正確なタイミングで同期する必要があります。
この同期を取るために重要なのが1回転シャフトの活用です。1回転シャフトを基準にすれば、設備間の動作タイミングを揃え、無駄な待機時間を削減し、生産効率を向上させることができます。
本項では、1回転シャフトを活用した設備間同期の方法について詳しく解説します。
1回転シャフトを同期基準として活用するメリット
1回転シャフトを設備の動作サイクルの基準とすることで、次のようなメリットがあります。
✅ 設備間のズレを防ぎ、確実な同期が可能
✅ 制御がシンプルになり、トラブルシューティングが容易
✅ 回転角度を基準にON/OFF制御できるため、タイミング調整が簡単
✅ サーボモーターやエンコーダと組み合わせることで、微調整が可能
このように、1回転シャフトを基準にすることで、設備全体の動作を一貫して制御しやすくなります。
設備間の同期方法
設備の同期を取るためには、以下のような方法があります。
メカニカルな連結による同期
機械式のシャフトやギア、チェーンを使って設備を直接連結する方法です。
📌 活用例:カム駆動の包装機
- メインの1回転シャフトを基準に、各部品の動作タイミングを調整
- ギアやチェーンを用いて複数のシャフトを同期
- 動作が直接機械的に連結されるため、ズレが発生しにくい
⚠ 注意点
- 機械的な調整が必要で、変更が難しい
- 機械要素の摩耗による誤差が蓄積する
エンコーダやカムポジショナーを使った同期
エンコーダやカムポジショナーを使用し、電子的に設備を同期させる方法です。
📌 活用例:サーボモーターを使った搬送装置とプレス機の同期
- 基準となる1回転シャフトにエンコーダを取り付け、角度情報を取得
- カムポジショナーやセンサーでON/OFF信号を出力し、他の設備に同期信号を送る
- サーボモーターを使って補正制御を行い、ズレを自動修正
⚠ 注意点
- 制御ソフトウェアの設定が必要
- 初期設定に時間がかかることがある
PLCを用いたタイミング制御
PLCを活用し、タイミングをソフトウェア的に制御する方法です。
📌 活用例:食品包装機とラベル貼り機の同期
- 基準となる1回転シャフトの角度データをPLCで取得
- ラベル貼り機の動作タイミングをPLCで調整し、同期を取る
- ズレが生じた場合、センサーとフィードバック制御で補正
⚠ 注意点
- 制御プログラムの開発が必要
- 設備ごとに微調整が必要
1回転シャフトを基準に設備を同期させることで、安定した生産ラインの運用が可能になります。
✅ メカニカルな連結(ギア・チェーン)を活用すれば、シンプルな同期が可能
✅ エンコーダ+カムポジショナーで電子的に同期させると、精度が向上する
✅ PLCを活用したカム制御により、複数の設備をソフトウェアで連携できる
✅ マスター・スレーブ方式を使えば、負荷変動がある装置でもリアルタイムに同期が取れる
機械設計において、1回転シャフトを活用することで、設備間の動作を高精度に同期させ、生産効率を向上させることが可能です。
アタッチメントチェーンの1ピッチを1回転に合わせる有用性
機械設計において、1回転シャフトの回転に対してアタッチメントチェーンの1ピッチを正確に同期させることは、搬送機構の安定性と精度向上に大きく貢献します。特に一定ピッチでワークを搬送する設備やタイミングを重視する自動機では、この手法が非常に有効です。
本項では、1回転シャフトの回転とアタッチメントチェーンの1ピッチを同期させることのメリットや具体的な活用例、設計のポイントについて詳しく解説します。
1回転シャフトとアタッチメントチェーンの同期とは?
アタッチメントチェーンとは?
アタッチメントチェーンとは、チェーンのリンク部分に取り付けられたアタッチメント(取付具)を利用して、ワークを搬送する機械要素です。
アタッチメントには以下のような種類があります:
✅ 角アタッチメント:部品を引っ掛けたり、押したりする用途
✅ フラットアタッチメント:ワークを安定して載せる用途
✅ ローラアタッチメント:回転動作と組み合わせて搬送する用途
このアタッチメントの1ピッチ分の動作を、1回転シャフトの1回転と一致させることで、同期を取ることができます。
1回転シャフトとアタッチメントチェーンの1ピッチを同期させるメリット
ワークの搬送位置が常に一定になる
1回転シャフトの回転とアタッチメントチェーンのピッチを完全に同期させることで、ワークの停止位置や投入位置のズレがなくなります。
例えば、
- 包装機で袋詰めをする際に、袋の位置が常に一定になる
- 塗装ラインでワークが一定の間隔で供給される
- 加工機でワークを正確な位置にセットできる
といった利点があります。
タイミング制御が容易になる
1回転シャフトの回転角度とチェーンのピッチが一致することで、カムポジショナーやPLCを用いた制御が簡単になります。
✅ 0°~90°:ワークの搬送
✅ 90°~180°:ワークの停止・加工
✅ 180°~360°:次のワーク搬送準備
のように、角度ごとの動作を明確に設定できるため、制御ロジックがシンプルになります。
加工・組立精度が向上する
ワークの位置が常に一定になるため、
- 穴あけ・切削などの加工精度が向上する
- ロボットやアクチュエーターによる組立作業のズレが少なくなる
- 搬送中の衝撃や振動を抑えられる
といったメリットが得られます。
設備のメンテナンスがしやすくなる
タイミングがズレる原因として多いのは、チェーンの伸びや摩耗によるピッチズレです。しかし、1回転シャフトと1ピッチが同期していれば、
✅ ズレが発生した際の補正が容易
✅ 摩耗が進んだ場合でもチェーン交換時の再調整が簡単
といった利点があります。
1回転シャフトとチェーンの同期設計のポイント
適切なスプロケット選定
アタッチメントチェーンのピッチ(P)とスプロケットの歯数(T)を考慮し、1回転で1ピッチ進むように設計します。
✅ 設計例
- チェーンのピッチ:P = 12.7 mm(#40)
- スプロケット歯数:T = 20
- 1回転あたりの搬送距離 = T × Z = 12.7 mm × 20 = 254 mm
このように、スプロケットの歯数とチェーンのピッチを適切に選定することで、1回転シャフトの1回転ごとに1ピッチ分の搬送が可能になります。
テンショナーでチェーンの張力を一定に保つ
チェーンが緩んでしまうと、同期精度が低下するため、テンショナーを設置し張力を一定に保つことが重要です。
✅ スプリング式テンショナー(自動で張力を調整)
✅ ねじ式テンショナー(細かい張力調整が可能)
これらを活用することで、チェーンのスムーズな動作と高精度な同期を維持できます。
1回転シャフトとアタッチメントチェーンの1ピッチを同期させることで、搬送精度・制御性・メンテナンス性が向上します。
✅ ワークの位置精度が向上し、加工・組立の精度も向上
✅ タイミング制御が容易になり、設備の動作が安定する
✅ 摩耗やズレを簡単に補正でき、メンテナンスがしやすい
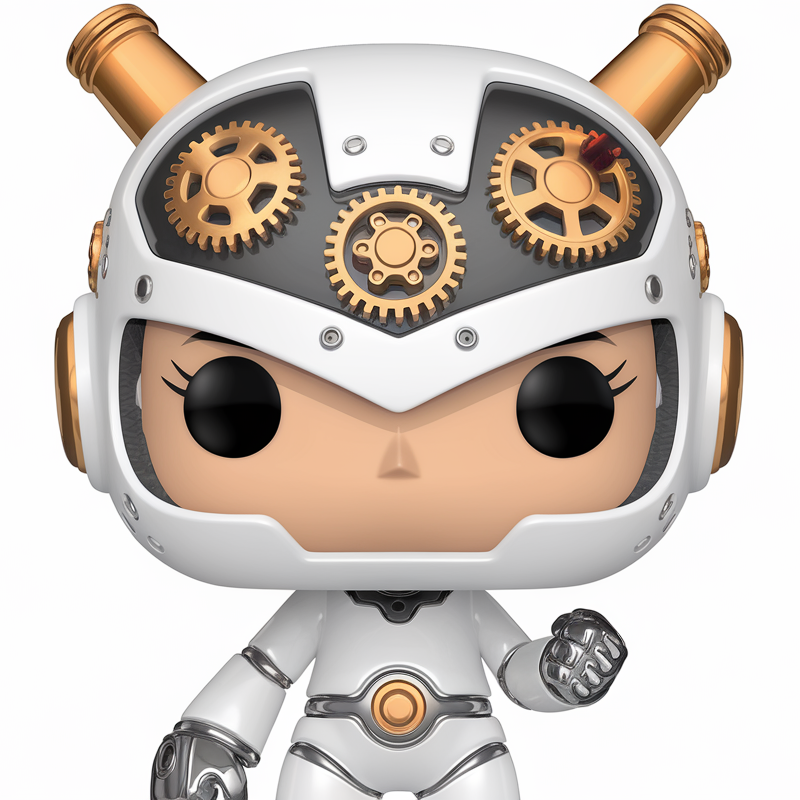
設計の際には、スプロケットの歯数、エンコーダによる制御、テンショナーの適用といったポイントを考慮することで、より高精度な搬送システムを構築できます。
この手法を活用することで、高精度・高効率な生産ラインを実現し、設備全体のパフォーマンスを向上させることが可能です。
まとめ
1回転シャフトは、機械の動作サイクルを360°単位で管理するための重要な要素です。
これを適切に活用することで、高精度な制御と安定した動作が可能になります。
✅ 1回転を基準にすることで、動作サイクルの基準が明確になる
✅ カムポジショナーやエンコーダと組み合わせることで、高精度な制御が可能
✅ センサーと連携することで、動作のズレを防ぎ、正確な位置決めができる
機械設計において、1回転シャフトを活用することで、効率的で正確な制御が実現できます。
コメント