機械や設備にセンサーを組み込むとき、いきなり「どのセンサーを使おうか?」と考えるのは少し早い段階です。
まず重要なのは、「設備全体の動作の流れを可視化すること」です。
センサーは“ただ取り付けるだけ”では意味がなく、どこで・なにを・どのように検知すべきかを明確にする必要があります。
そのためには、動作の流れを整理して、「センサーが必要なポイント」を洗い出すことが欠かせません。
可視化のポイント:ここを押さえよう!
作業開始や終了のタイミングを把握
設備がいつスタートし、どこで処理が完了するか。
この流れを時系列で整理することで、「スタート検知」や「完了検知」に必要なセンサーが見えてきます。
🔍 例
▶ ワークが搬入されたら処理を開始する
→ 光電センサーでワーク検知
▶ 処理が終わったら次工程へ搬送
→ シリンダーのエンド確認オートスイッチなど
ワークの位置や状態の確認
動作中にワークが所定の位置にあるか、異常がないかをチェックすることは非常に重要です。
その確認にセンサーが大きな役割を果たします。
🔍 例
▶ ワークが所定の位置まで来ていない
→ リミットスイッチや近接センサーで検知
▶ ワークの向きや有無を判別
→ 画像センサーやレーザー距離センサー
安全性を確保する条件の整理
機械を安全に動作させるためには、オペレーターや周辺環境を確認するためのセンサーが必要です。
🔍 例
▶ 作業者が機械に近づいたら動作を停止
→ エリアセンサー・光電センサー
▶ カバーが閉じていないと動作しない
→ 近接センサやリミットスイッチなどでインターロック設計
図やフローチャートで見える化!
紙やホワイトボードで構いません。
「1. ワークが来る → 2. センサーで検知 → 3. シリンダーが動作 → 4. 処理開始」といった流れをフローチャートやタイムチャートで描くことで、センサーの配置場所や種類が自然と見えてきます。
全体の流れを視覚的に整理することで、設計ミスや抜けも防止できます。
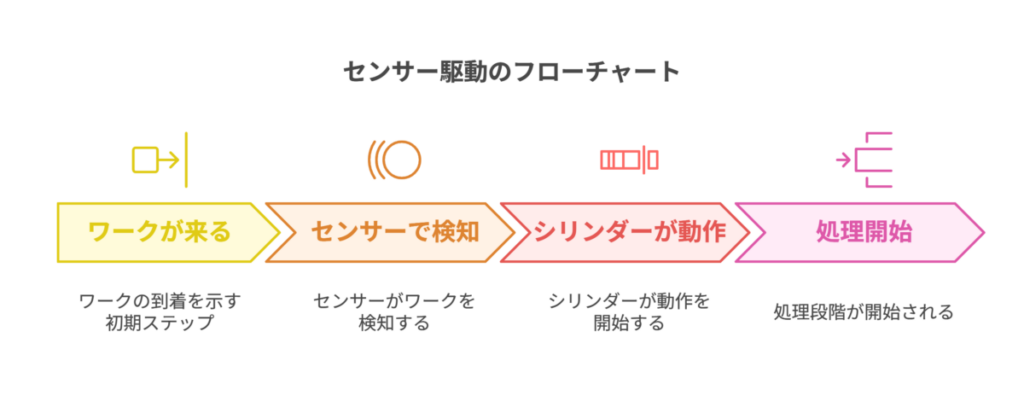
フローチャートは電気設計との橋渡し!
機械設計でも欠かせない“見える化”
機械の動作を設計するとき、フローチャートを描くことは単なる手間ではありません。
それは、機械設計と電気設計をつなぐ“共通言語*とも言える重要な工程です。
設備が「どう動くか」を機械側だけでなく、電気制御側も正しく理解していることが、トラブルのない設計の第一歩となります。
なぜフローチャートが必要なの?
電気と機械は別の設計領域
- 機械設計者は、シリンダーやアクチュエーター、構造部品を担当。
- 電気設計者は、センサーやPLC、リレー回路などの動作制御を担当。
お互いの領域が違うからこそ、「設備はこう動く」という共通のイメージを明確に伝える手段が必要になります。
それが フローチャート です。
フローチャートに含めるべき内容
以下のポイントを押さえてフローチャートを作ると、電気設計との連携がスムーズになります。
✅ スタート・ストップ条件
- 設備がどういう条件でスタートするか
- 完了や異常でどこでストップするか
✅ 各動作の順番
- シリンダーの動作
- センサーのON/OFF
- モーターの回転など
✅ 各タイミングの条件
- 「このセンサーがONなら次の動作へ進む」
- 「このエラーが出たら待機状態に戻る」
電気設計とスムーズに連携するには?
曖昧な言葉は避ける!
🚫 「だいたいこのへんで動く」
✅ 「センサーAがONになったら、バルブBを開く」
フローチャートにすることで、誰が見ても同じ理解ができ、電気設計者はPLCのラダー設計がしやすくなります。
実際のフローチャート例(簡易)
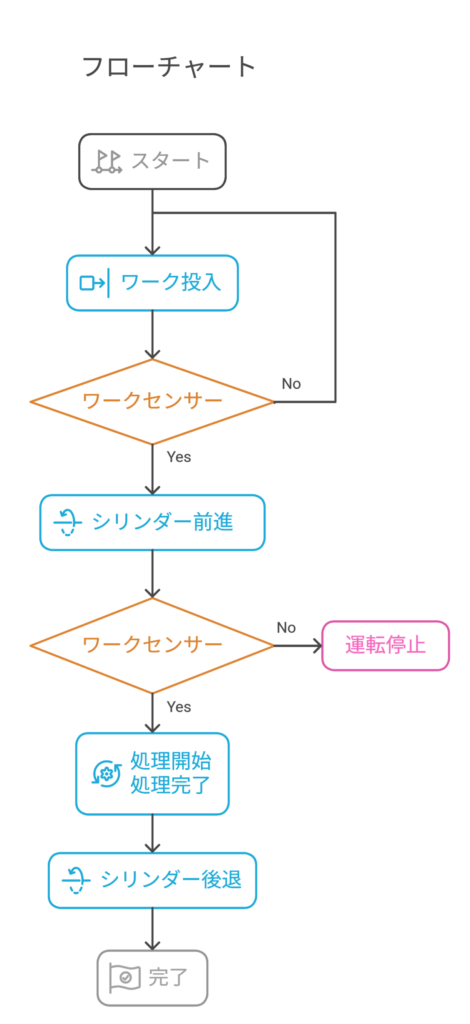
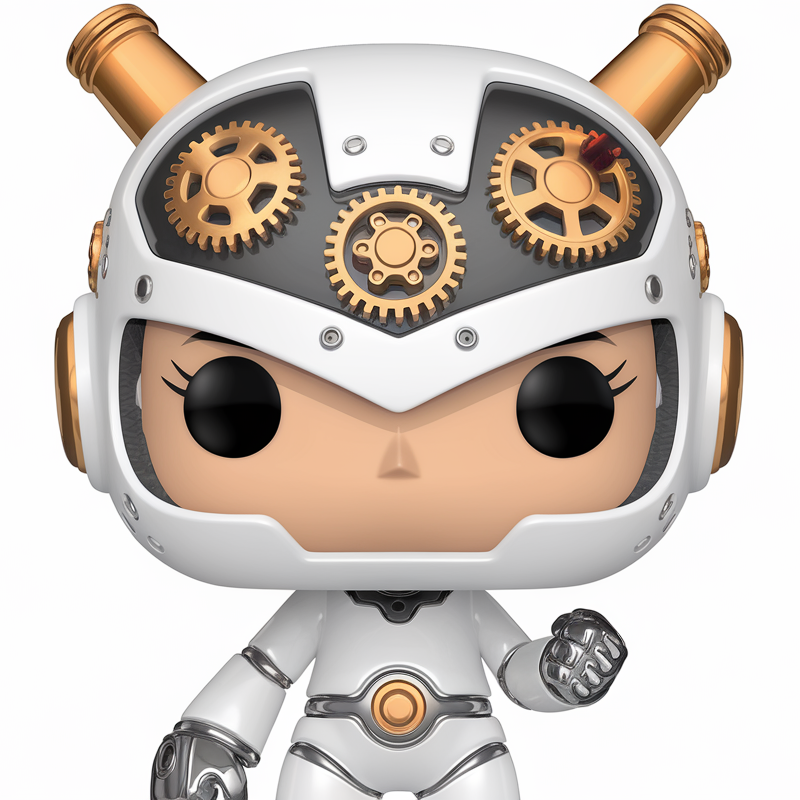
こういったシンプルな図でOKです。
ポイントは「動作順・条件・判断」を誰でも見てわかる形にすること。
フローチャートは設計の共通図面!
フローチャートを作成することは、機械と電気の設計のズレを防ぐために必須です。
▶ 設備の動きを整理できる
▶ 誤動作・仕様漏れの防止になる
▶ 電気設計との意思疎通が円滑になる
つまり、「よい機械は、よいフローチャートから生まれる」と言っても過言ではありません。
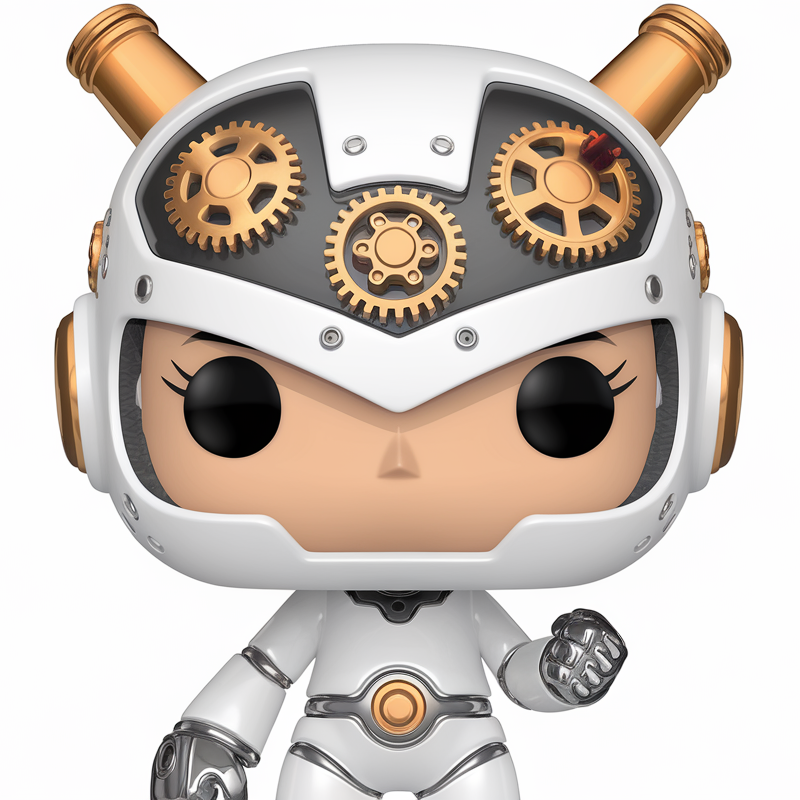
ぜひ、機械設計の段階からフローチャートを取り入れて、チームで同じ動作イメージを共有していきましょう!
構想段階のカギはフローチャート
センサー配置は“あとから”じゃ遅い!
機械を設計するうえで、センサーの種類・数・設置場所をいつ決めるか?
実はこれ、機械構想の初期段階でフローチャートを描くことでかなり明確になります。
「最後に電気設計で何とかなるでしょ」と思っていると、
後になって「センサーが足りない」「設置スペースがない」といったトラブルの原因に!
センサーは“動作の確認役”
センサーの主な役割は、機械の動作を見張って知らせることです。
✅ ワークが正しくセットされたか
✅ シリンダーが前進しきったか
✅ 処理が完了したか
✅ 異常状態が起きたか
これらの判断ポイントをあらかじめ洗い出しておくには、フローチャートが非常に有効です。
フローチャートで見える「センサーが必要な場面」
フローチャートには、以下のような条件が頻繁に登場します。
- 「センサーAがONなら次へ」
- 「シリンダーが戻っていたら処理開始」
- 「エラーセンサーがONならストップ」
こうした判断の分岐点=センサーが必要な場所です。
つまり、フローチャートを描くことでセンサーの必要数と配置箇所が自然と見えてくるのです。
構想段階でセンサーを考えるメリット
設計変更を防げる
後からセンサーが足りないと、設計のやり直しやレイアウトの見直しが必要になることも。
構想段階で把握していれば、トラブルを未然に防げます。
電気設計との連携がスムーズに
センサーの仕様・型式・配線など、早い段階で電気設計者と打合せができます。
機械のスペースや干渉を考慮しやすい
「センサーをつける場所がない…」なんてことがなくなります。
フローチャートはセンサー設計の地図
構想段階でフローチャートを作ることにより、
▶ 機械の動作イメージが明確になる
▶ センサーの数・場所・役割が事前にわかる
▶ 後戻りのない効率的な設計ができる
という、機械設計における“見えないミス”の防止につながります。
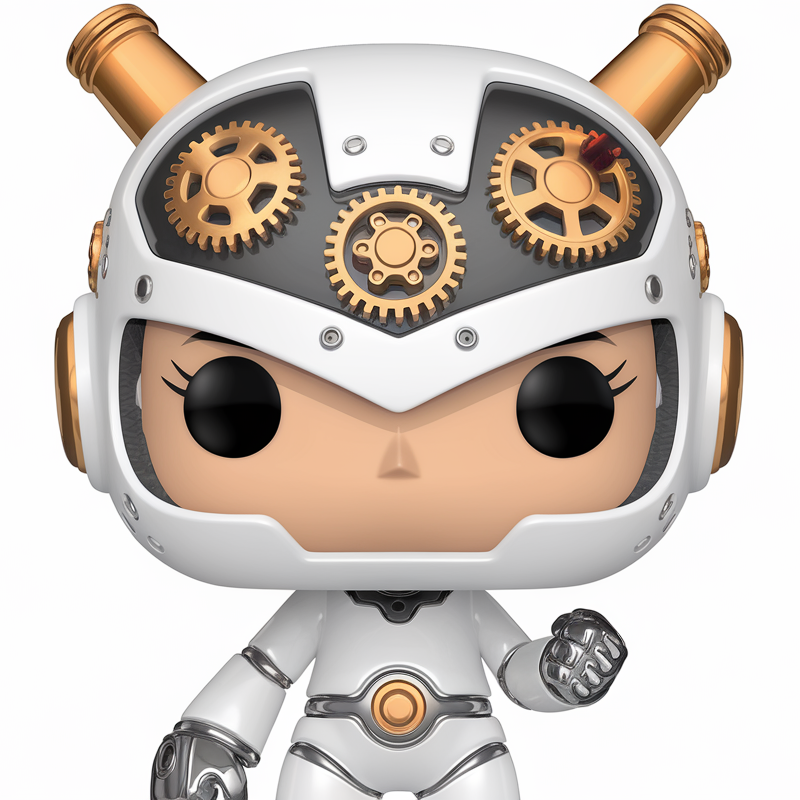
「とりあえず作って、あとでセンサーをつけよう」ではなく、
「動作フローを先に描いて、必要なセンサーを計画しよう」がこれからの基本です!
まとめ
センサー選定は、設備の動作をしっかり理解することから始まります。
作業の流れを見える化し、「どのタイミングで何を検知すべきか?」を整理することで、最適なセンサーの種類・設置場所を決めることができます。
設備が正しく動く・安全に動く・無駄なく動くために、まずは動作の流れの“見える化”から始めましょう!
コメント