装置や機械を設計する際、多くの機械設計者は「機構」や「構造の強度」「動作のスムーズさ」に意識が集中しがちです。
しかし、装置に欠かせないのが電気配線です。
センサ、モーター、スイッチ、ソレノイド、LED、カメラなど……
これらの部品を動かすためには、必ず配線(電線・信号線・通信ケーブルなど)が必要になります。
ところが、「配線スペース」や「配線ルートの確保」を忘れて設計してしまい、後で苦労することが非常に多いのです。
この記事では、初心者でもわかりやすく、
✔ なぜ電気配線を意識した設計が重要なのか?
✔ どんなトラブルが起こりやすいのか?
✔ 配線ルートの確保におけるポイント
✔ 実際の設計の工夫や考え方
を解説します。
電気配線を意識しないとどうなるか?
まず、「機械設計時に電気配線を考慮していない場合」の典型的な失敗例を紹介します。
配線の通り道がない!
🚫 モーターまでの間に板金やフレームがあってケーブルが通らない
🚫 センサの裏側にケーブルを通そうとしたら、フレームと干渉
🚫 動作中に配線が引っ張られて断線のリスク大
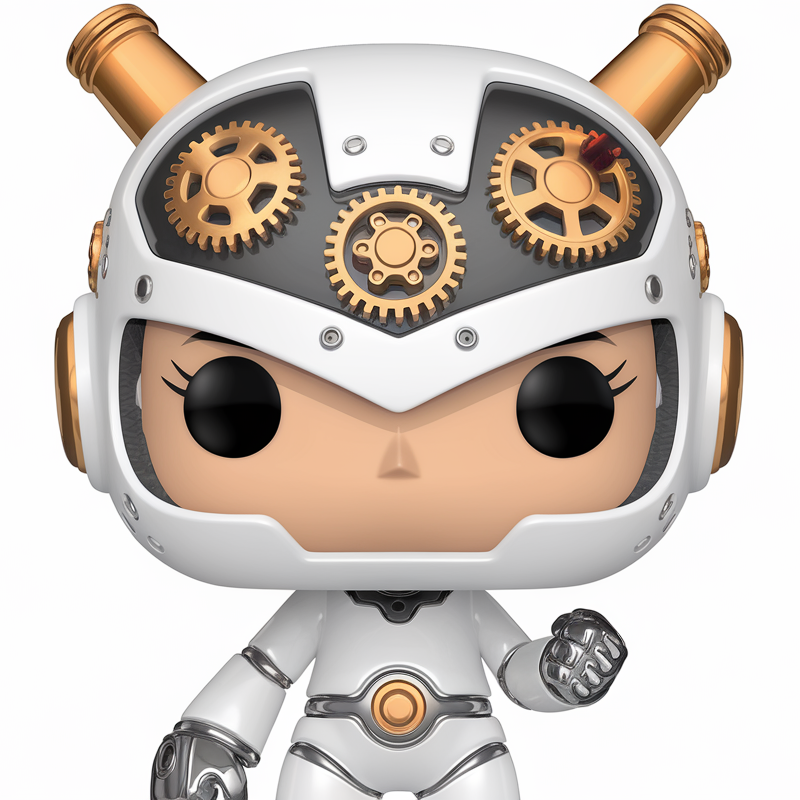
このような問題は、後から穴を開けたり、配線用の金具を追加したりと設計変更が必要になります。
動く部品に配線を固定してしまう
🚫 回転体やスライド部にケーブルを固定してしまい、ケーブルが捻れて破損
🚫 折り曲げ半径を無視した結果、配線の寿命が著しく短くなる
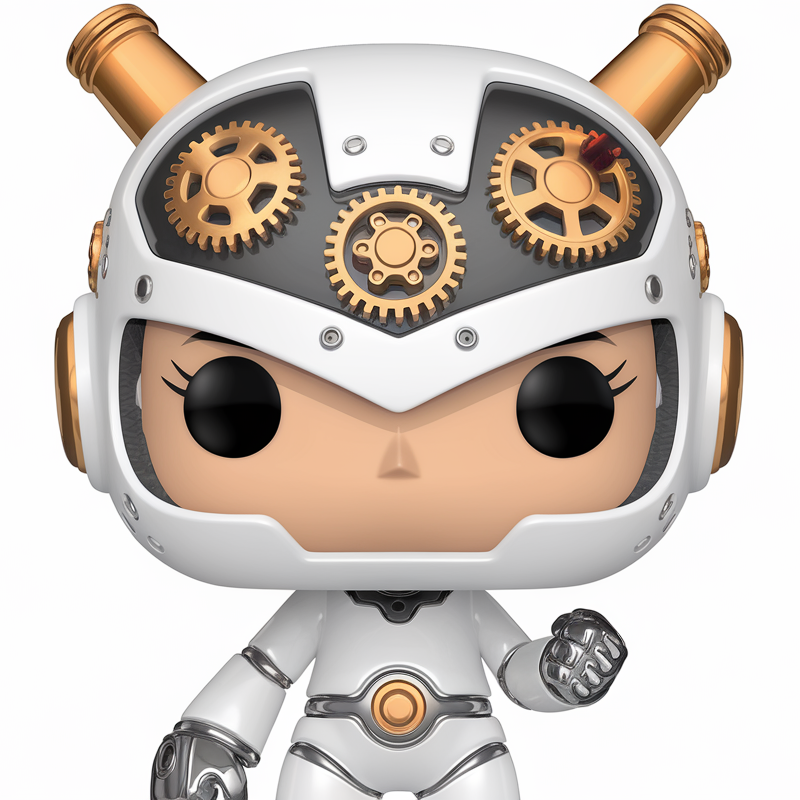
可動部には配線のゆとり・余長・ガイドが必要ですが、設計段階で考慮していないと事故の元です。
外観がゴチャゴチャになる
🚫 装置としての見た目が悪く、保守性も悪化
🚫 装置立ち上げ時に「どこに何が通っているかわからない」
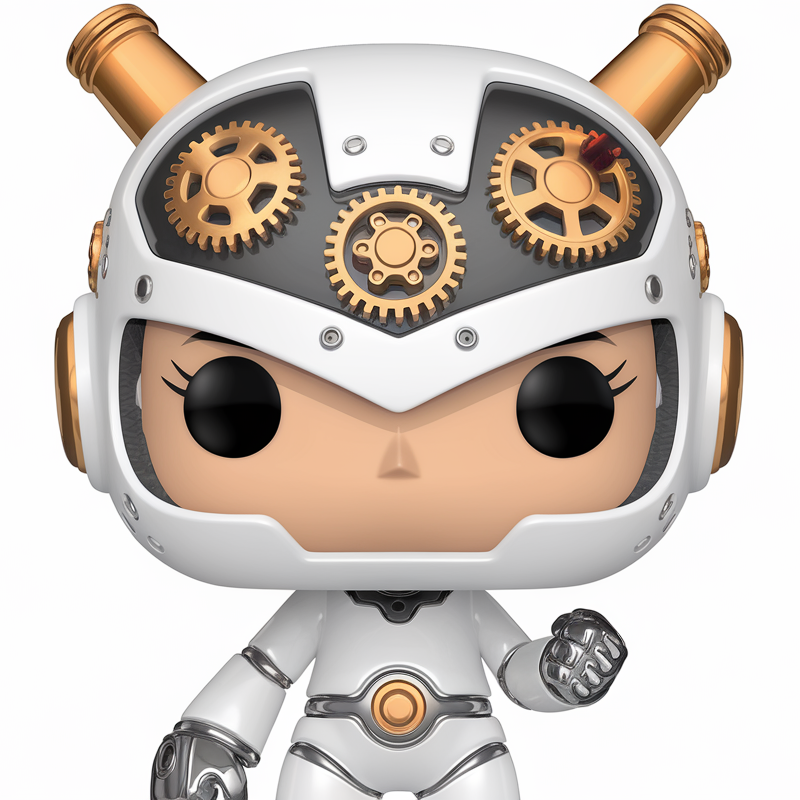
作業者が間違えて違うケーブルを外してしまうなど、トラブルのもとになります。
なぜ「設計段階」で配線を考えるべきなのか?
後から配線ルートを変更するのは難しい
設計が完了して、筐体やフレームができてしまったあとに「配線ルートがない!」と気づいても、構造を大幅に見直さなければならなくなることがあります。
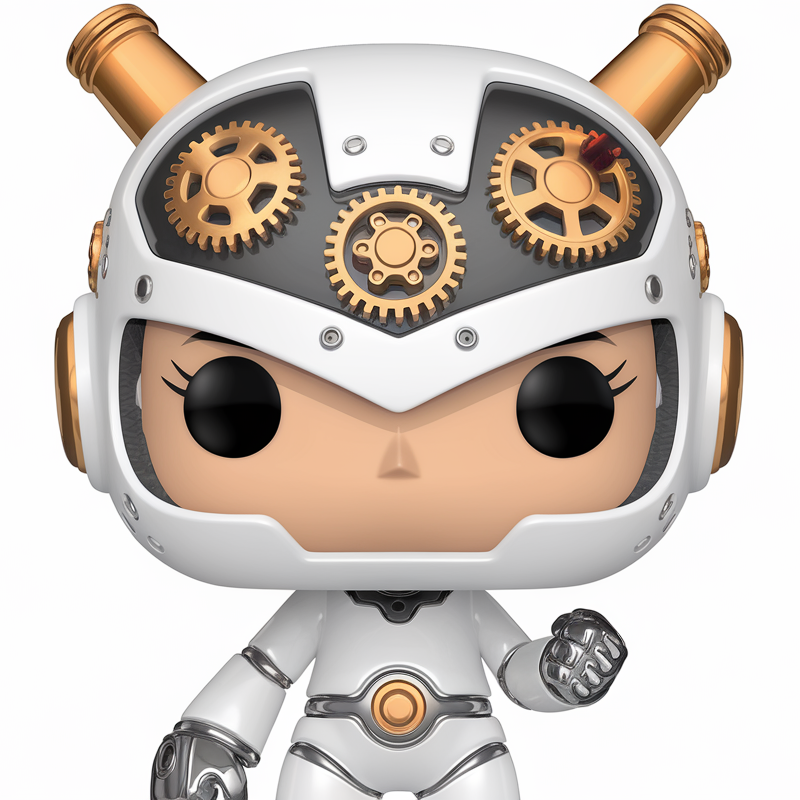
結果として工数増加、納期遅延、コスト増加につながります。
トラブルのリスクを大きく減らせる
可動配線や狭所配線は、トラブルが起こりやすいポイントです。
設計段階から意識することで、断線や誤配線、保守ミスを未然に防ぐことができます。
他部署との連携がスムーズに
電気設計担当者にとっても、配線ルートが確保されていると制御盤レイアウトや電線長の見積もりが楽になります。
配線ルート確保のための設計のポイント
ここからは、実際に設計で意識すべき配線対策について紹介します。
主要部品間の配線ルートをイメージする
まずは、次のような構成を3D CAD上でイメージしてみましょう。
✅ 制御盤 → モーター(電源線・エンコーダ線)
✅ 制御盤 → センサ(信号線)
✅ 制御盤 → カメラ(通信線)
✅ 空圧バルブ → ソレノイド(パイロット線)
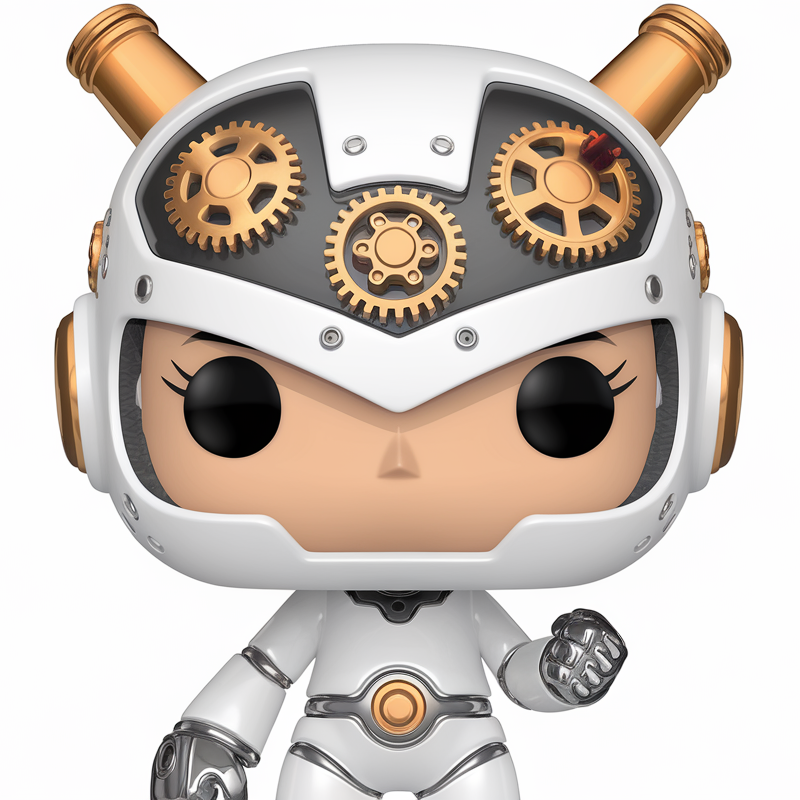
それぞれの始点と終点を結ぶ仮想のケーブルラインを頭の中で描き、それがスムーズに通る構造になっているか確認しましょう。
配線に必要な「スペースの確保」
配線ルートとして通すためには、以下のスペースが必要です。
ケーブル種別 | 必要な通路幅(目安) |
---|---|
信号線 | 約10〜20mm |
モーター線 | 約20〜30mm |
ケーブルベア | ベアのサイズ+10mm |
配線用の穴やスリットは最初から設計しておくことが重要です。
可動部にはケーブルベアやケーブルガイドを使う
可動部(スライド、昇降、回転など)がある場合は、以下を意識しましょう。
✅ ケーブルベア(キャリア)を設置できるレールや固定穴を用意
✅ 最小曲げ半径を守る
✅ ケーブルベア用の「予備スペース」も確保する
ロボットケーブル+ケーブルベアの併用で、断線リスクを大幅に減らせます。
メンテナンス性も意識する
- 配線をまとめる「ダクト」「チューブ」「ワイヤリングガイド」を使う
- カバーで隠しすぎない(簡単に開けられるようにする)
- 配線交換や点検がしやすい位置にする
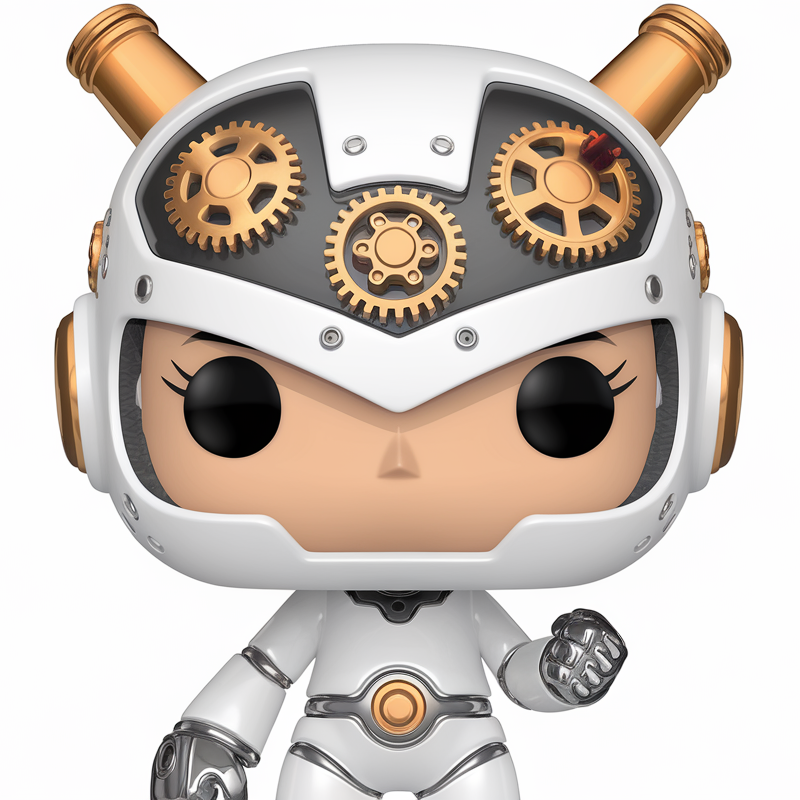
見やすく、触りやすく、交換しやすい構造を目指しましょう。
配線の通り道は“電気設計と共有”がカギ!
機械設計と電気設計は、装置開発における両輪のような存在です。
センサやモーター、アクチュエーターなどの電気部品を機械側に取り付ける際、電気設計者が考える配線経路や制御盤との接続点を、機械設計者がしっかり理解・反映できているかどうかが、装置の完成度に大きく関わってきます。
実は、「配線の通り道を共有していなかったことで、現場で苦労する」というトラブルは少なくありません。
この記事では、初心者の方でも理解できるよう、電気設計との連携を意識した配線設計の重要性とその実践方法について、わかりやすく解説していきます。
なぜ「配線の通り道の共有」が必要なのか?
設計の食い違いが装置の完成度を下げる
- 電気設計者:「ここからケーブルを通すつもりだった」
- 機械設計者:「そこには穴もスペースも用意していない」
このような食い違いが発生すると、配線のために現場で穴開け作業をしたり、強引な取り回しになってトラブルの元になります。
配線の通り道が設計に含まれていないと…
- ケーブルが通らない、折れ曲がる、引っかかる
- 他の部品と干渉して動作不良
- 可動部でケーブルが断線
- 外観やメンテナンス性が損なわれる
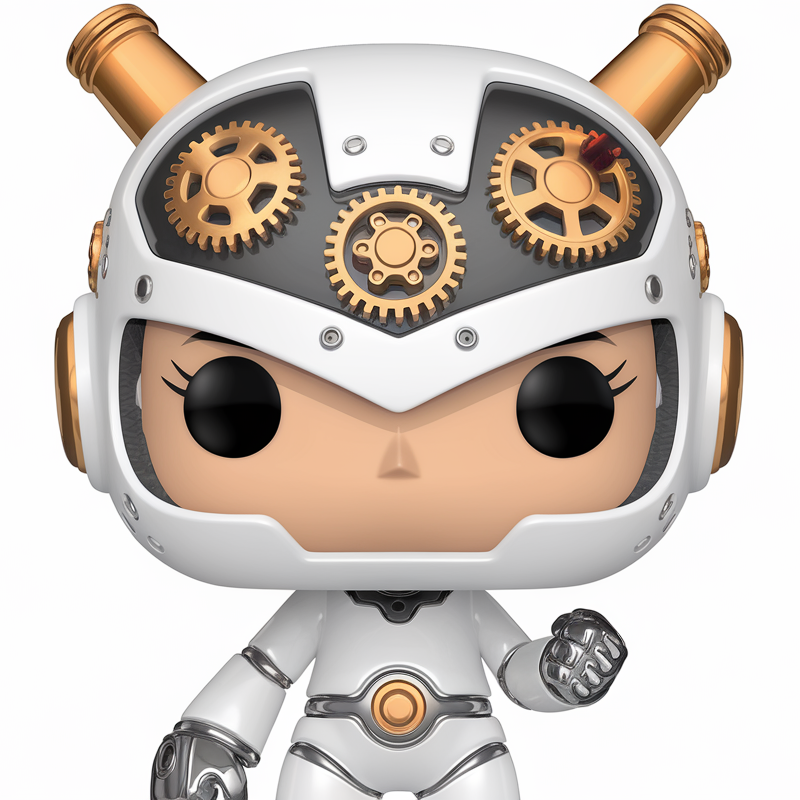
こういった問題は、事前に「通り道」を共有することで回避可能です。
電気と配線ルートを共有する3つのメリット
手戻りや現場改造が減る
配線が通ることを前提に機械設計が行われていれば、現場での急な加工や部品追加が減ります。
設計変更の手間や納期の圧迫も防げます。
配線の保守性が向上する
電気設計者が考える「ケーブル交換しやすいルート」や「ラベルが見やすい位置」などを反映すれば、保守性が良くなり、装置の信頼性も向上します。
組立てやすい構造になる
配線を通しやすい構造にすることで、組立工数の削減にもつながります。
作業者にとっても、配線がしやすい装置は完成後の品質が安定します。
具体的にどう共有すればいいのか?
以下のようなステップで、電気設計と情報を共有しましょう。
ステップ①:主要な配線ルートを設計初期にすり合わせる
- 制御盤の設置位置
- 各機器(モーター、センサ、カメラなど)との距離・向き
- ケーブルがどこから出て、どこを通るか
- 可動部の有無(ケーブルベアの必要性)
3Dモデル上で矢印やダミーケーブルを描くなど、簡単なスケッチでもOKです。
初期段階で方向性を合わせておくことが大切です。
ステップ②:機械設計上で「配線の通り道」を確保する
- ケーブルの逃げスペース(ベアやチューブが通る穴)
- 固定用のブラケットやタイラップの取付穴
- 配線ダクトの取り付けスペース
CADモデルに「配線ゾーン」を設けておくと、後工程で迷いません。
可動部がある場合は、曲げ半径や可動余長にも注意します。
ステップ③:図面・3Dモデルに情報を明記する
機械設計図面やアセンブリ図に、以下のような補足を記載すると親切です。
- 「ここは配線用スリット」
- 「ケーブル通線用のサービスホール」
- 「この穴は配線ベア用ブラケット取り付け穴」
また、配線モデルを簡易的に3D CAD上で表現しておくことで、誤解を防げます。
実際の設計現場ではこんな工夫をしている!
通線スリットの設計
- フレームの隅にケーブル専用スリット(5~20mm幅)を設ける
- メンテナンス時に簡単に開閉できるカバー構造
制御盤近くに余長スペース
- 制御盤手前にケーブルのたるみを逃がすスペースを確保
- 複数ケーブルが集合する場所は、ケーブルタイレールを設計段階で用意
ベアやチューブのための固定ブラケット
- ケーブルベアがスムーズに動くように取り付け穴・固定金具の位置を設計で定義
- 取付け部材はミスミやイグスなどの標準品を活用することが多い
電気と機械、両者が歩み寄ることが成功のカギ!
「配線なんて後からなんとかなる」と思っていませんか?
しかし、設計段階で配線の通り道を意識することで、装置の完成度・保守性・信頼性は段違いに向上します。
そして、最大のポイントは、電気設計者との情報共有です。
ちょっとした声掛けや資料の共有で、トラブルを未然に防ぐだけでなく、チームとしての一体感も強くなります。
スムーズな設計のためのチェックリスト
✔ 電気設計と配線ルートの方向性を初期に共有したか?
✔ 配線スペース・固定方法を機械設計に反映しているか?
✔ 可動部の配線対策を事前に検討したか?
✔ 3Dモデルや図面に配線に関する情報を記載しているか?
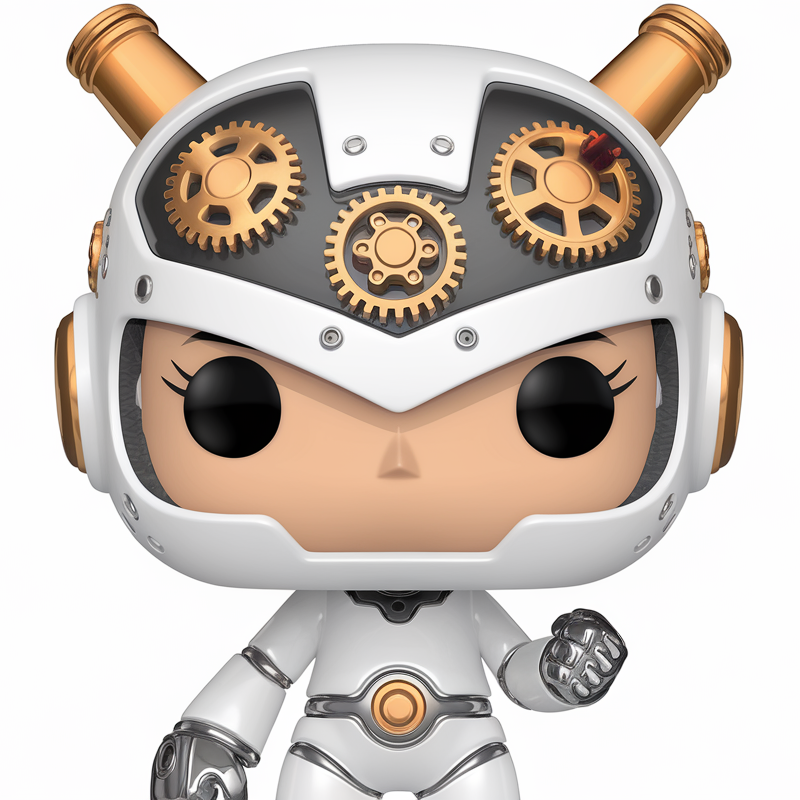
このような小さな意識が、設計のクオリティを一段上へと引き上げてくれます。
まとめ:配線の意識は「設計力」の証明
✔ 電気配線は「機械設計の一部」だと考えるべき
✔ 通り道がないと後で大きな手戻りになる
✔ 3D CADで事前に配線ルートを想定しておく
✔ 可動部・可視性・メンテナンス性も含めて計画する
配線をしっかり意識した設計ができるようになると、装置全体の完成度・信頼性が大きく向上します。
また、電気設計者や組立作業者との連携もスムーズになり、「わかってる設計者」として信頼されるようになりますよ!
コメント