エアシリンダは圧縮空気を使って直線運動を行う機器ですが、シリンダ内部のピストンが急停止すると、衝撃(ショック)が発生します。
この衝撃はシリンダ本体の寿命を縮めたり、機械構造に悪影響を与えることがあります。
そこで使われるのがクッション機構です。
クッションとは、シリンダの終端近くでピストンを減速させ、衝撃を和らげる仕組みのことです。
エアシリンダのクッションには、大きく分けて
▶ ラバークッション
▶ エアクッション
の2種類があります。
それぞれの特徴と使い分けを詳しく見ていきましょう!
ラバークッションとは?
ラバークッションは、シリンダ内部に設置されたゴム部品(ラバー)によって、ピストンが当たったときの衝撃を吸収する方式です。
ラバークッションの特徴
🔹 構造がシンプルで安価
🔹 メンテナンスが少なく済む
🔹 クッション効果は一定(調整はできない)
🔹 中・小型シリンダでよく採用される
🔹 高速・高負荷にはやや不向き
ピストンがストローク終端に到達すると、ゴムにぶつかることでショックを一気に吸収します。
ゴムの弾力性を利用して衝撃を緩和するため、小型機器や低負荷用途に向いています。
エアクッションとは?
エアクッションは、シリンダ内部の空気(エア)を利用して減速させる方式です。
エアクッションの特徴
🔹 終端手前でピストンがエアを圧縮して減速
🔹 クッション効果を微調整できる(クッションバルブで調整)
🔹 高速運転や大きな負荷にも対応できる
🔹 構造はやや複雑で価格も高め
🔹 大型シリンダや高速シリンダで採用されることが多い
エアクッションはピストンが終端に近づくと空気を封じ込め、空気の圧縮抵抗を使ってじわじわと減速します。
そのため、急激なショックを防ぎ、シリンダ本体や周辺構造への負担を大きく減らせます。
ラバークッションとエアクッションの違いまとめ
比較項目 | ラバークッション | エアクッション |
---|---|---|
減速方法 | ゴムの弾力 | 空気の圧縮 |
クッション調整 | できない | 可能(バルブ調整) |
対応速度・負荷 | 低速・小負荷向き | 高速・大負荷向き |
構造 | シンプル | やや複雑 |
コスト | 低め | 高め |
使い分けのポイント
では、実際に設計する場面でどちらを選べばいいのでしょうか?
用途や条件に応じて、以下のように使い分けます。
ラバークッションを選ぶ場合
✅ 小型シリンダを使う場合
✅ 速度がそれほど速くない(中速以下)場合
✅ 取り付けスペースやコストを抑えたい場合
✅ シンプルでメンテナンスフリーな設計をしたい場合
🔍 例)
ストッパー用途、軽量ワークの搬送、簡易位置決め
エアクッションを選ぶ場合
✅ 高速運転を行う場合
✅ 重いワークを扱う場合
✅ 衝撃を極力抑えて機械寿命を伸ばしたい場合
✅ クッション特性を調整して最適化したい場合
🔍 例)
大型搬送装置、重機部品の移載、高速ピックアンドプレース
エアシリンダにおけるクッションの注意点
ラバークッションの注意点
- ウレタンゴムを介してピストンとカバーが直接当たるのを防ぎます。
- 衝撃音を小さくする効果はありますが、衝撃そのものの吸収効果は弱いです。
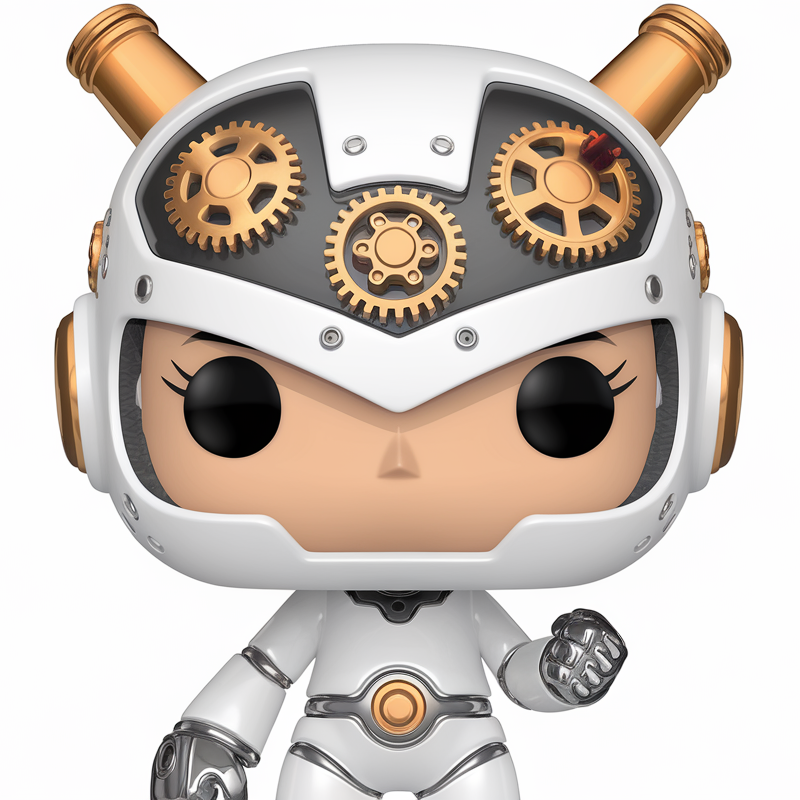
軽い負荷や小型シリンダ向け。ただし、大きな衝撃は抑えられないため注意。
エアクッションを使うときの注意点
✅ 吸収できる運動エネルギーには限界があります。
負荷の重さ(質量)や速度に応じて、適切なシリンダサイズを選定しましょう。
✅ 有効クッション長さ(ストローク終端付近)は、速度が自然に減衰します。
メーカーカタログを参照してクッション領域を確認しましょう。
✅ 負荷の運動エネルギーが大きすぎる場合や、エアクッション付きシリンダがない場合は、
- 外部にショックアブソーバを追加する
- 終端速度や負荷質量を見直す
といった対策が必要です。
✅ 終端速度は、ストローク全体の平均速度の2倍以上になることもあるため、
実際の速度をしっかり計算しておきましょう!
クッションバルブ(ニードル)を絞りすぎると、シリンダが最後までストロークできない
または動作できなくなる恐れがあるので注意が必要です。
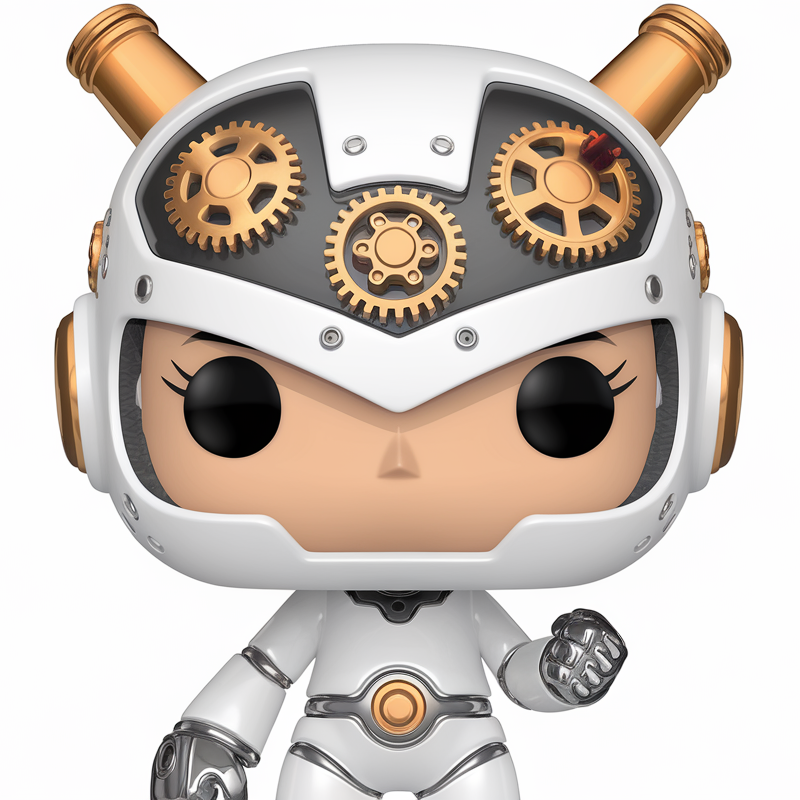
高速や重い負荷に対応可能。ただし、調整ミスに注意!
エアシリンダのクッション機構は、正しく理解して設計・調整しないとトラブルの原因になります。
特に、エアクッションではバルブの調整や負荷エネルギー計算が重要です。
必要に応じて、外部ストッパーやショックアブソーバも併用し、安全でスムーズな動作を確保しましょう!
設計時の注意点
- エアクッションを採用する場合、適切に調整しないと効果が出ません。
- 初期調整は慎重に行うこと。
- 高速運転時は、エアクッションだけでなくショックアブソーバの併用も検討するとより効果的です。
- ラバークッションは経年劣化するため、長期間使う場合は定期的な点検も意識しましょう。
エアシリンダのクッションとショックアブソーバ併用について
エアシリンダを使った機械設計では、負荷をストローク終端で止めるときの衝撃対策がとても重要です。
この衝撃対策には、
✅ シリンダ内蔵の「クッション」
✅ 外付けの「ショックアブソーバ」 の2つを上手に使い分ける必要があります!
本項では、クッションとショックアブソーバを併用する理由や使い方のポイントをわかりやすく解説していきます。
ショックアブソーバとは?
ショックアブソーバは、油圧やばねの力を使って衝撃を滑らかに吸収する専用部品です。
✅ メリット:非常に大きな運動エネルギーも吸収できる
🚫 デメリット:別途コストがかかる、設置スペースが必要
どうして併用するの?
エアクッションだけでは吸収しきれない場合、ショックアブソーバを追加して負担を分散させるためです。
🔍 たとえば…
- 負荷が重い(質量が大きい)
- 移動速度が速い
- シリンダサイズが小さい などの場合は、エアクッション単体では衝撃を吸収しきれず、シリンダや装置にダメージが蓄積してしまいます。
このようなとき、エアクッションで「ざっくり減速」させて、ショックアブソーバで「最終的にしっかり停止」させるという役割分担をさせると、とても効果的なのです!
併用設計のイメージ
シリンダのストローク終端付近での減速イメージは次の通りです。
- エアクッションで速度をだんだん落とす(空気の圧縮反発)
- ショックアブソーバで残ったエネルギーをしっかり吸収して静止する(油圧ダンパー的役割)
これによって、
- シリンダ本体への負担を軽減
- 衝撃による振動や音を低減
- 長期的な耐久性アップ
が期待できます!
設計時の注意ポイント
併用する場合、以下のポイントに注意しましょう。
エアクッションは適度に効かせる
エアクッションを「全開」にしてしまうと、ストローク終端でいきなりショックアブソーバにすべての衝撃がかかってしまいます。
必ずエアクッション側である程度減速させましょう。
✅ エアクッションのニードルを絞りすぎず、でも開きすぎない「中間くらい」が目安です。
ショックアブソーバのサイズ選定に注意
ショックアブソーバにも吸収できるエネルギー量(定格運動エネルギー)が決まっています。
選定時は、
- 実際の負荷質量
- 速度(特にストローク終端速度) をもとに、吸収可能なモデルを選びましょう。
🚫 終端速度は「平均速度の2倍以上」になる場合もあるので注意!
ショックアブソーバの設置位置も重要
ショックアブソーバは、負荷にできるだけ近い位置に設置するのが理想です。
ロッド先端やワーク近くに取り付けることで、反動や振動を最小限に抑えられます。
併用した方がいい典型的な例
- 大きなワークを高速で搬送するライン
- ロングストローク(長い移動距離)のエアシリンダ
- ワーク着座時の衝撃を最小限にしたい設備
- シリンダを長寿命化したい重要な工程
こういう場合には、迷わず併用を検討しましょう!
エアクッション+ショックアブソーバで「安全・長寿命」設計へ
エアシリンダ単体で済ませるのもアリですが、
より高負荷・高速移動を安全にこなすなら、クッションとショックアブソーバの併用はとても効果的です。
▶ エアクッションでざっくり減速
▶ ショックアブソーバでピタッと停止
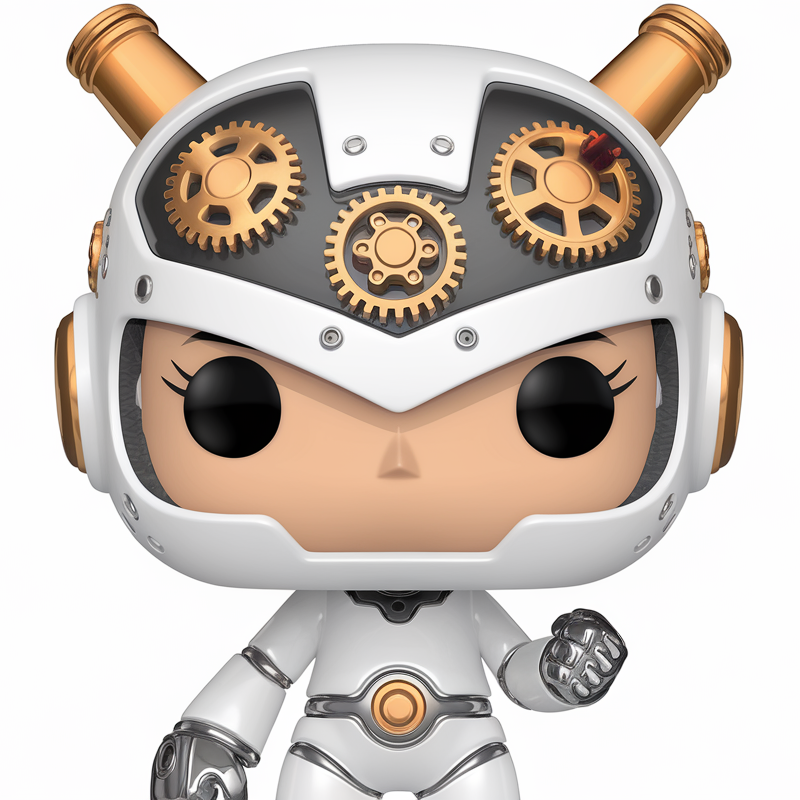
このコンビネーションをうまく設計に取り入れて、静かで壊れにくい装置を作りましょう!
まとめ
エアシリンダにおけるクッション機構は、ストローク終端で負荷が停止する際に発生する衝撃や騒音を緩和するために設けられています。主に次の2種類があります。
▶ ラバークッション
ピストンとシリンダカバーの金属同士の直接衝突を防ぐため、ウレタンゴムを介在させる方法です。
衝撃音の低減には効果がありますが、運動エネルギー自体の吸収力は小さいため、大きな負荷や高速移動には不向きです。
▶ エアクッション
ストローク終端の手前から排気を絞って空気を圧縮し、その反発力で負荷の運動エネルギーを吸収する方法です。
クッションニードルで吸収力の調整が可能ですが、絞りすぎるとストロークが途中で止まったり、動作不良を起こすため注意が必要です。
クッションには吸収できる運動エネルギー量に限界があり、負荷が重い・速度が速い場合にはショックアブソーバなど外部の緩衝機構を併用することが推奨されます。
クッション設計のポイントは、
✔ 負荷の質量と終端速度を正しく把握し、運動エネルギーを計算すること
✔ 適切なシリンダサイズとクッション設定を選定すること
✔ 必要に応じてショックアブソーバを併用し、シリンダの耐久性を高めること
エアシリンダのクッション機構を正しく理解・活用することで、装置の静粛性・耐久性・安全性を大きく向上させることができます。
コメント