加工精度や組立精度の向上を目指すうえで、「クランプ」だけでワークを固定するのは限界があります。ワークを“動かないように押さえる”クランプと、“狙った位置に正確に置く”ための位置決め要素は、別物として設計することが非常に重要です。
本記事では、クランプと位置決め要素を適切に組み合わせることで、どのようにして高精度な固定と位置決めを実現するかを、理論と実践の両面から詳しく解説します。
クランプと位置決めの役割は明確に分ける
設計初心者がやりがちなミスとして、クランプだけで位置決めを兼ねる設計がありますが、これはNG。なぜならクランプは「保持力を確保する」ための要素であり、繰り返し精度や基準位置の確保には向かないからです。
クランプの役割
- ワークを動かないように押さえる
- 加工時の振動や反力に対して安定させる
- 脱着を容易にする
位置決め要素の役割
- ワークを基準通りの位置に配置する
- 再現性のあるセットアップを実現する
- 加工精度・組立精度の確保
位置決めの基本原理「3-2-1の法則」
高精度な位置決めの基本は「3-2-1の原則」です。これは、立体物を空間的に完全拘束するために必要な最小限の拘束点を意味します。
拘束方向 | 点数 | 目的 |
---|---|---|
Z方向(底面) | 3点 | ワークを平面上に安定させる |
Y方向(側面1) | 2点 | 横方向のずれを防ぐ |
X方向(側面2) | 1点 | 前後方向のずれを防ぐ |
このように、ワークは計6点で拘束され、正確な位置決めが可能になります。
実際の位置決め要素
では、具体的にどのような要素を使って位置決めするのかを見ていきましょう。
位置決めピン(ノックピン)
もっとも一般的な位置決め要素。丸ピンとテーパーピンがあり、丸ピン+スリーブ穴の組み合わせで繰り返し高精度な位置決めが可能です。
- 丸ピン(平行ピン):簡易位置決め、脱着可能
- テーパーピン:精密位置決め(嵌合がきつく、外しにくい)
リニアガイドやボス形状
- ボス形状の突起+ザグリ穴:位置決めしやすく安価
- リニアガイドやVブロック:直線方向への高精度案内に有効
インローによる位置決め
製品の形状に合わせて作られたインローや段付きガイドも、高精度な位置決めに役立ちます。
クランプとの組み合わせ方法
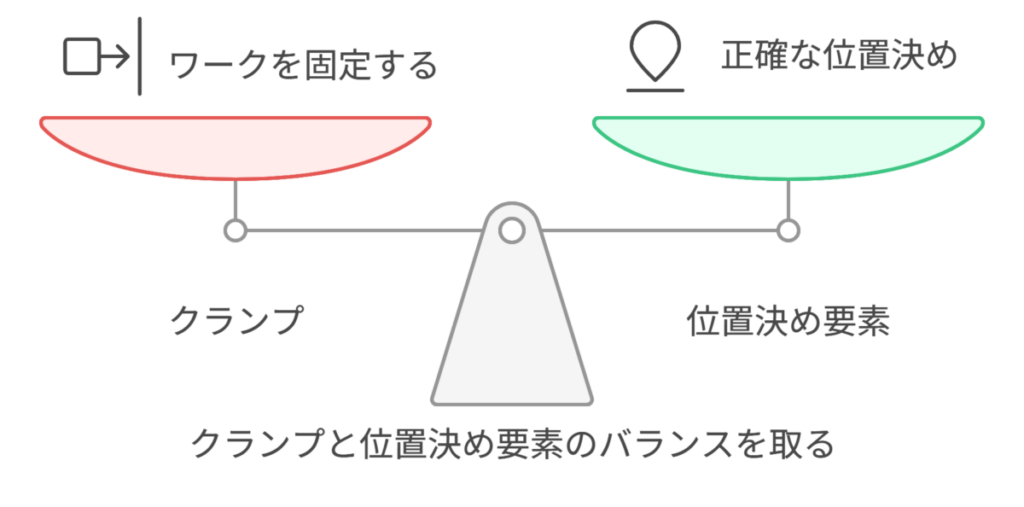
位置決めが完了したら、その状態をキープするためにクランプで固定します。クランプの力が位置決めピンにかからないよう設計することがポイントです。
推奨される組み合わせ例
位置決め要素 | クランプ方法 |
---|---|
位置決めピン(2点)+受け側スリーブ | トグルクランプやエアクランプで押さえる |
溝ガイド+ボス付き形状 | 上から押さえる縦押し型クランプ |
Vブロックによる軸方向位置決め | 軸方向に対し引きクランプを使用 |
NG設計の例
🚫クランプ力が位置決めピンに干渉する
👉 ピンが変形したり、摩耗して精度が落ちる
🚫クランプ位置がワークの重心から遠すぎる
👉 振動や反力でワークが浮く・動く可能性あり
より高精度を求める場合の工夫
以下のような工夫を施すことで、さらに位置決め精度を高めることができます。
基準面の仕上げ精度向上
仕上げ面に研磨や切削加工を施し、位置決め要素との接触精度を確保します。
自動化・エアクランプの導入
位置決め完了後にエアでクランプを行うことで、人為的なバラツキを防止します。
ワークの形状に応じたカスタム治具
複雑形状には、専用形状の位置決めピンやコンタクトブロックを設計することで確実な固定が可能です。
脱着性とのバランスも重要
あまりに高精度を追求しすぎると、今度は「ワークが外れにくい」「位置決めが困難」といった問題も発生します。以下の工夫でバランスを取ることが大切です。
- テーパー+丸穴の組み合わせにして、片方は自由度を持たせる
- 一方向のみ拘束し、他方向はクリアランスを取る
- 位置決め用と加工用を分離して設計する(脱着ステージ vs 加工ステージ)
クランプにおける脱着性と固定力のバランスの考え方
機械設計において、ワーク(加工物)を「しっかりと固定」することは非常に重要です。しかし同時に、簡単に脱着できることも作業効率や設備稼働率を考えるうえで見逃せません。
本項では、クランプにおける固定力と脱着性のバランスについて、基本の考え方から実務で役立つ設計ポイントまでをわかりやすく解説します。
クランプに求められる2つの要素
クランプ設計では、主に以下の2つの性能が求められます。
固定力(保持力)
加工時や振動時にワークが動かないようにしっかり押さえる力。加工精度や安全性に直結する要素です。
脱着性(作業性)
ワークを容易に着脱できること。段取り時間の短縮や作業効率の向上に大きく貢献します。
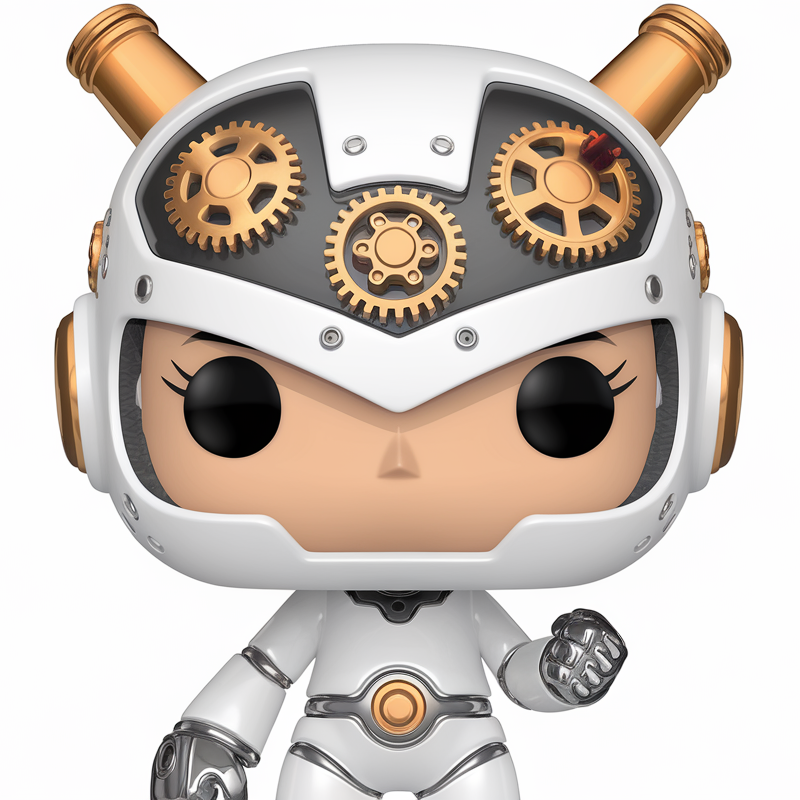
この2つはしばしばトレードオフの関係にあり、固定力を高めると脱着が困難になるという問題が発生します。そこで両立のための工夫が必要です。
固定力と脱着性のバランスを取るポイント
位置決めと固定を分けて設計する
よくあるミスが、「クランプで位置決めも兼ねる」設計。これは精度にも脱着性にも悪影響を及ぼします。
位置決めはピンやガイドで行い、クランプは押さえるだけにすることで、固定力を維持しつつ、スムーズな脱着が可能になります。
クランプのストロークとリンク機構に注目
トグルクランプやレバークランプなどは、少ない力で高い保持力を得ることができる反面、過剰な締付になることもあります。
- ストロークが大きすぎるとワークの位置ズレにつながる
- 過剰な締め付けは脱着困難や部品の変形を招く
適切なストロークと締付トルクのバランスを設計しましょう。
クランプ力を分散させる
1点に強い力をかけるのではなく、複数の軽い力でバランスよく押さえることで、固定力を保ちつつ脱着しやすくなります。
例えば、2つのトグルクランプで左右から押さえる設計にすると、どちらか一方を外せば片側が浮くため、取り外しが容易になります。
脱着性を高めるための実践テクニック
テクニック①:テーパーピン+丸穴の組み合わせ
位置決めピンは「2本ともきっちりはめる」と外しにくくなります。
そこで💡
- 1本はテーパーピン(高精度な固定用)
- もう1本は丸ピン+スリップフィット(案内用)
とすることで、精度を保ちながら脱着性を確保できます。
テクニック②:クランプレバーやカムクランプの活用
ネジ式のクランプはどうしても時間がかかります。
レバー操作でワンタッチで脱着できる機構を使うことで、段取り時間を大幅に短縮できます。
テクニック③:位置ガイドや傾斜面の活用
自然に所定位置に「スッ」と入るように、傾斜ガイドや受け面に面取りを設けると、着脱がしやすくなります。
治具の設計では見落とされがちですが、作業性に大きく影響します。
設計時の注意点
- クランプ力が過剰にならないように、耐荷重と締め付けトルクを見積もる
- ワークの材質によっては、締め過ぎると変形やキズの原因に
- 繰り返し使用により、ピンやクランプの摩耗・がたつきが生じるため、定期的な点検が必要
クランプ設計においては、固定力と脱着性を両立させることが重要です。以下のポイントを意識しましょう。
✅ 位置決めと固定は分離する
✅ 過剰な締め付けを避け、クランプ力を分散
✅ レバー式やカム式で作業性を高める
✅ ピンや受け面の設計で自然な脱着動作をサポート
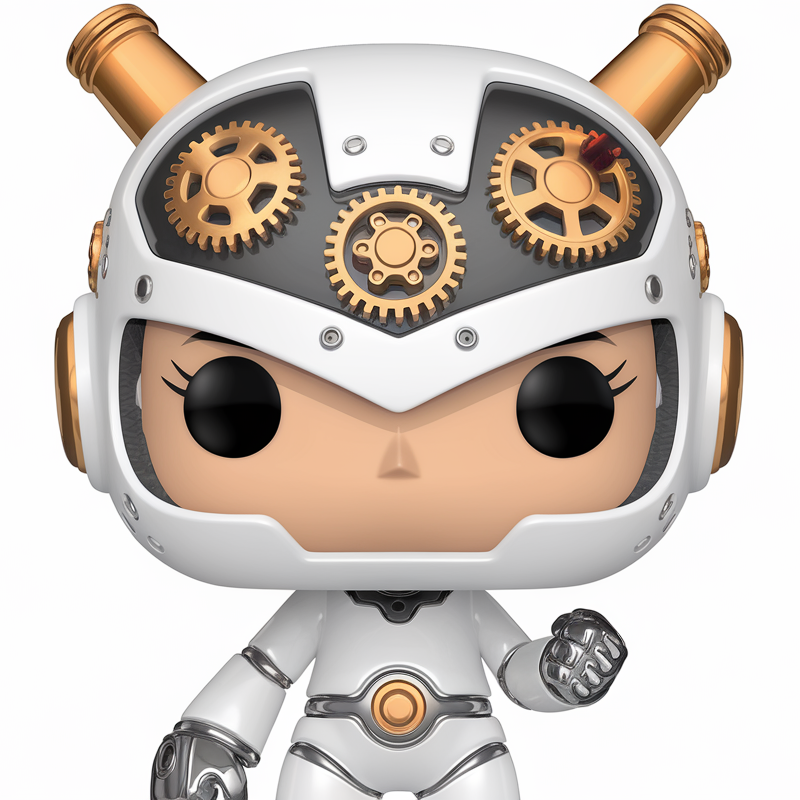
現場での「使いやすさ」も含めて考えることで、設計品質と作業効率の両立が実現できます。製品精度だけでなく、作業者の負担や生産性にも配慮したクランプ設計を目指しましょう。
まとめ
高精度な加工や組立を実現するには、クランプと位置決めを“別の役割”として設計し、両者を適切に組み合わせることが不可欠です。
✅ 位置決めは6点拘束を意識しよう(3-2-1の法則)
✅ クランプは固定のためであり、位置決めの妨げにならないように
✅ 加工精度だけでなく、作業性や脱着性にも配慮する
この原則を守るだけで、製品の精度や作業効率が格段に向上します。ぜひあなたの設計にも取り入れてみてください。
コメント