機械設計でねじを使用する際には、通し穴と座グリ穴と皿穴の設計が非常に重要です。通し穴はねじを通すための穴で、座グリ穴、皿穴はボルトや皿ねじの頭をきれいに収めるためのくぼみです。どちらも正しい寸法で設計することが、機械の信頼性や組み立て性に大きく影響します。本記事では、通し穴と座グリ穴と皿穴の寸法表、特徴、使い分けについて解説します。
通し穴・座グリ穴・皿穴の寸法表
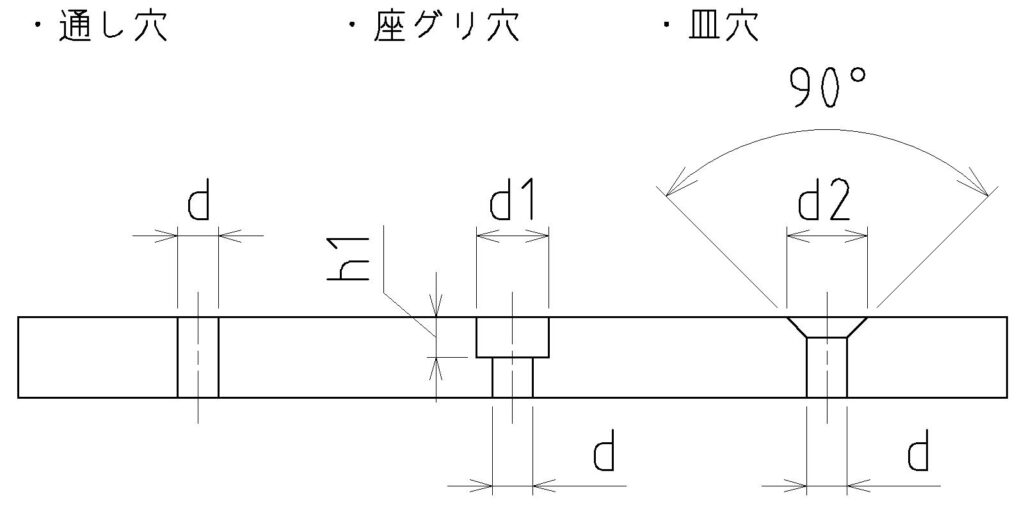
呼び径 | 通し穴径(d) | 座グリ径(d1) | 座グリ深(h1) | 皿もみ径(d2) |
M3 | 3.4 | 6.5 | 3.5 | 7 |
M4 | 4.5 | 8 | 4.5 | 9 |
M5 | 5.5 | 9.5 | 5.5 | 11 |
M6 | 6.6 | 11 | 6.5 | 14 |
M8 | 9 | 14 | 9 | 18 |
M10 | 11 | 17.5 | 11 | 22 |
M12 | 14 | 20 | 14 | |
M14 | 16 | 23 | 16 | |
M16 | 18 | 26 | 18 | |
M18 | 20 | 29 | 20 | |
M20 | 22 | 32 | 22 | |
M22 | 24 | 35 | 24 | |
M24 | 26 | 39 | 26 | |
M27 | 30 | 43 | 30 | |
M30 | 33 | 48 | 33 |
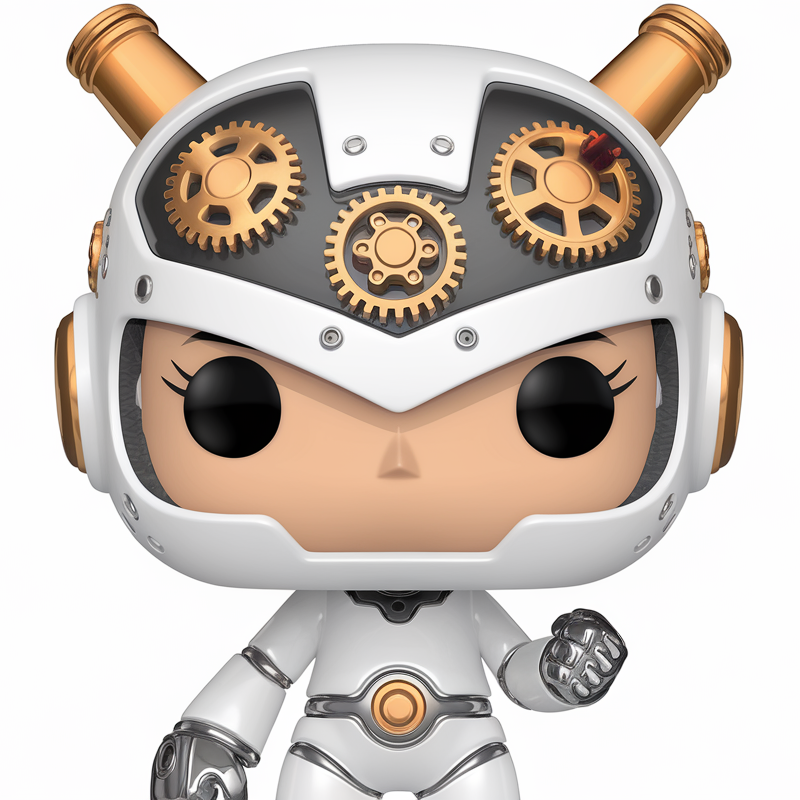
上記の表はわたしが普段使用している一般的な寸法になります。
適材適所により、寸法を調整します。
特に皿穴径(d2)の寸法は使用する皿ねじにより、沈みすぎたり、頭が飛び出る可能性があります。上記の寸法は少し沈み気味になる寸法になっております。
厳密な沈み代が必要な場合は皿ねじをもとに寸法を選定しましょう。
✅ 低頭ボルトと極低頭ボルトの座グリ寸法は下記をチェック!
✅ だるま穴の寸法は下記をチェック!
通し穴(バカ穴)
通し穴は、ねじを通すために設ける穴です。この穴の直径は、ねじの呼び径よりも少し大きく設定され、ねじがスムーズに通るようにします。通し穴が適切に設計されていないと、組み立て時にねじが通らなかったり、応力が集中して破損の原因になることがあります。
通し穴の設計ポイント
✅ 穴径は、ねじの呼び径よりもわずかに大きい値に設定します。
✅ 精度が要求される箇所では、ねじ径に対して厳密なクリアランスが必要です。
座グリ穴
座グリ穴は、ボルトやねじの頭を収めるための穴です。特に六角穴付きボルト(キャップボルト)や六角ボルトを使用する際に、ボルトの頭が平らに収まり、干渉を防ぐために座グリが設けられます。
座グリ穴の設計ポイント
✅ 座グリ穴径は、ねじの頭の直径よりも少し大きくします。
✅ 座グリ深さは、ねじの頭が完全に収まるように設定し、表面が平らになるようにします。
皿穴
皿穴は、ねじの頭が表面から突出しないように、部材に円錐状のくぼみを設けるものです。主に皿ねじ(フラットヘッドねじ)を使用する際に用いられます。ねじ頭が部材表面と一体化することで、デザイン性が向上するほか、機械や装置の可動部分に干渉しないようにするためにも使用されます。
皿穴の設計ポイント
✅ 頭部の角度
- 皿ねじには通常、90°の角度が付いていますが、用途に応じて異なる角度のものもあります。
- 設計時には、使用するねじに適した角度を確認することが重要です。
✅ 皿穴径
- 皿ねじの頭の直径に合わせて、少し余裕を持たせた穴径を設定します。
✅ 皿穴の深さ
- ねじの頭が表面と完全に一体化する深さに設定します。
- 深さが浅いと頭が飛び出し、深すぎるとテーパ部が目立ち見た目が悪くなります。
ボルトの通し穴設計の注意点
ボルトの通し穴は、機械設計において部品同士を確実に締結するための重要な要素です。しかし、この通し穴が大きすぎる場合や小さすぎる場合、締結の強度や組み立て性に悪影響を及ぼします。この記事では、通し穴設計時の注意点とその影響について解説します。
ボルトの通し穴の基礎知識
通し穴は、ボルトがスムーズに挿入され、かつ締結時に部品同士がしっかり固定されるための穴です。通常、穴径はボルト径に基づいて決定されます。
通し穴の推奨径
✅通し穴径は、ボルトの公称径 +10%程度の余裕が一般的です。
▶(例:M6ボルトの場合、穴径は6.6mm程度)
この「余裕」は、ボルトの加工誤差や取り付け時の位置ズレを吸収するために必要です。
通し穴が大きすぎる場合の問題点
🚫 部品のずれが発生する
通し穴がボルト径に対して大きすぎると、締結後にボルトと穴の間に隙間が生じます。この隙間により、以下の問題が発生します:
▶位置ズレ: 部品が期待する位置に正確に固定されない。
▶動作不良: 精密機構の場合、部品の位置ズレが機械全体の動作不良を引き起こす可能性がある。
🚫 振動や衝撃による緩みや破損
隙間があると、振動や衝撃によってボルトと穴の間でガタつきが発生し、以下のリスクを伴います:
▶ボルトが緩みやすくなる。
▶穴の周囲が摩耗や疲労で破損する。
🚫 強度低下
ボルトが締め付け力を効果的に伝えられず、設計上想定される締結強度が得られなくなる。
通し穴が小さすぎる場合の問題点
🚫 ボルトが通らない
穴径が小さいと、ボルトが通らず、組み立て作業が困難になります。この場合、現場での追加加工が必要になることがあり、手間やコストが増加します。
🚫 ボルトピッチに精密な公差が必要になる
穴が小さいとボルトとボルトのピッチ間に少しでもズレが生じると組み立てが困難になる。
🚫 ボルトに傷がつく
無理にボルトを通そうとすると、ボルトのねじ部分に傷がつく可能性があります。
▶締結強度の低下: 傷が応力集中の原因となり、破損しやすくなる。
▶耐食性の低下: コーティングが剥がれ、腐食が進みやすくなる。
🚫 締結不良
穴が小さすぎると、ボルトが正しく挿入されないため、均一な締め付け力を得ることが難しくなります。結果として、締結部が不安定になる可能性があります。
通し穴設計時のポイント
✅ 適切な穴径を選定する
- 上記の寸法表を基準に設計を行う。
- 精密機械や高精度を要求される箇所では、メーカーが推奨する穴径や公差を確認してください。
✅ 通し穴の位置精度を確保する
穴径が適切でも、穴位置がずれているとボルトが通らないことがあります。特に、複数の穴を通してボルトを締結する場合は以下を意識してください。
- 位置公差を適切に設定する。
- 部品の加工精度を確認する。
✅ ゆるみ防止対策を施す
振動や衝撃を受ける環境では、通し穴のサイズにかかわらずボルトが緩むリスクがあります。これを防ぐためには下記の対策を行う。
- スプリングワッシャーやロックナットを使用する。
- ねじロック剤を塗布する。
✅ 特殊な用途ではクリアランスを調整する
精密な位置決めが必要な場合や、動きが求められる場合は、以下のような設計を検討してください。
- リーマ穴: ボルトではなく位置決めピンを使用し、部品の位置を精密に決定する。
- 長穴: 熱膨張や位置ズレを吸収する場合に使用。
💡 ボルトの通し穴設計では、以下のポイントに注意する必要があります。
📌 穴径はボルト径に適した範囲に収める。
📌 大きすぎると位置ズレや緩み、小さすぎると組み立て不良や締結強度低下が発生する。
📌 精密な位置決めが必要な場合は、リーマ穴や位置決めピンの使用を検討する。
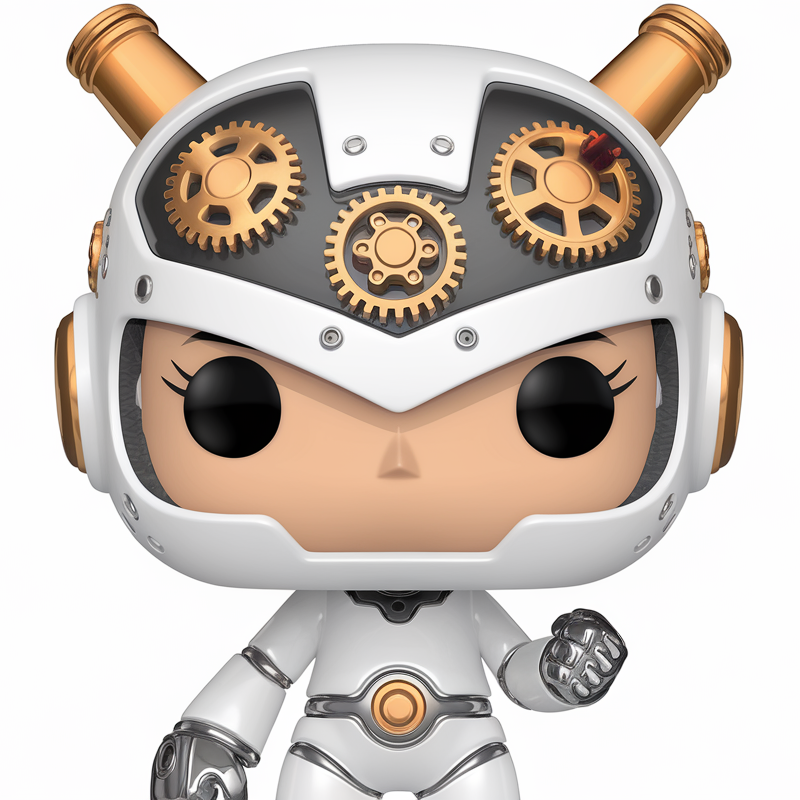
設計の初期段階で適切な通し穴サイズを設定することで、製品の信頼性と組み立て性を向上させることができます。
まとめ
通し穴、座グリ穴、皿穴は、それぞれの特徴と用途に応じて使い分けることで、設計の効率と美観、機能性を向上させることが可能です。設計時には、強度、外観、使用環境、加工精度などを考慮して、最適な穴の種類を選定することが重要です。
コメント