キーの寸法や形状は、各国の規格によって定められています。日本ではJIS(日本工業規格)が一般的に使用されており、国際規格としてISOが存在します。キーの寸法は、軸径に基づいて選定され、以下のように規格化されています。
JIS規格(JIS B1301:1996 平行キーとキー溝)抜粋
JIS規格をもとによく使う軸径ごとのキー寸法表をまとめて表にしました。
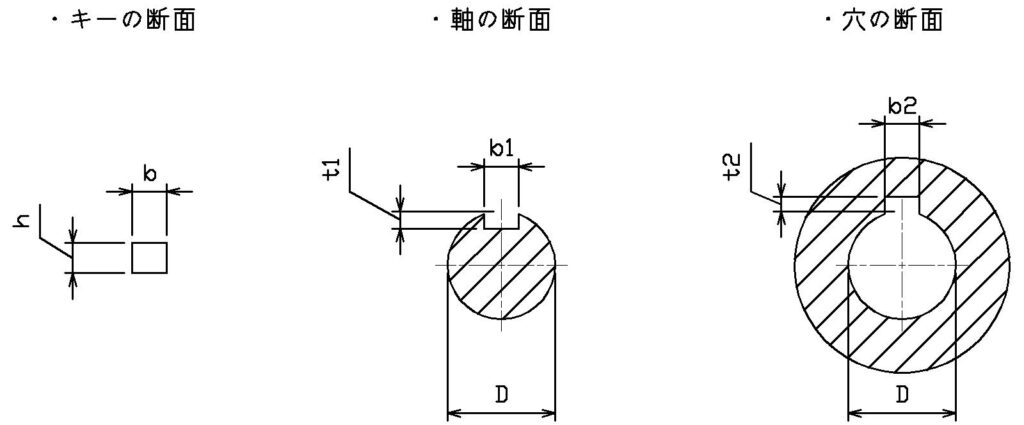
軸径D | キーの 呼び寸法 b×h | キー溝の寸法 | |||||
b1,b2 基準寸法 | 普通形 | t1 基準寸法 | t2 基準寸法 | t1,t2 許容差 | |||
b1許容差 (N9) | b2許容差 (Js9) | ||||||
6 | 2×2 | 2 | -0.004 -0.029 | ±0.0125 | 1.2 | 1.0 | +0.1 0 |
8 | 3×3 | 3 | 1.8 | 1.4 | |||
10 | |||||||
12 | 4×4 | 4 | 0 -0.03 | ±0.0150 | 2.5 | 1.8 | |
13 | 5×5 | 5 | 3.0 | 2.3 | |||
15 | |||||||
16 | |||||||
17 | |||||||
18 | 6×6 | 6 | 3.5 | 2.8 | |||
20 | |||||||
22 | |||||||
25 | 8×7 | 8 | 0 -0.036 | ±0.0180 | 4.0 | 3.3 | +0.2 0 |
30 | |||||||
35 | 10×8 | 10 | 5.0 | ||||
40 | 12×8 | 12 | 0 -0.043 | ±0.0215 | |||
50 | 14×9 | 14 | 5.5 | 3.8 |
キーと標準部品との適合、規格の重要性
機械設計では、動力を効率的に伝達するために軸と回転体を確実に締結する必要があります。その締結要素として代表的なものが「キー」です。キーは、軸とハブ(プーリーやギアなど)を連結する部品で、主に動力を伝達するために使用されます。本項では、キーの標準部品との適合性、適用される規格、設計時の注意点について解説します。
キーの基本構造と役割
キーは、軸の溝(キー溝)とハブの溝(キー座)に挿入され、以下の役割を果たします。
✅負荷分散
接触面で荷重を分散し、摩耗を防ぐ。
✅動力伝達
軸とハブの間でトルクを確実に伝達する。
✅位置決め
回転方向の位置を固定する。
キーと標準部品の適合
キーを使用する際、軸やハブに設ける溝の加工寸法が規格に準拠しているかが重要です。標準部品を活用することで、設計・製造の効率化が図れます。
📌適合例
- 標準モーターシャフト:キー溝がJIS規格に準拠して加工されている。
- 市販ギアやプーリー:キー座が標準規格に準拠して設計されている。
これにより、市販のキーを組み合わせるだけで高い互換性を確保できます。
🔍適合の確認
- 軸とハブの溝幅が規格通りか確認。
- 選定したキーの公差(h9やH7)と部品のはめあい公差を考慮。
設計時の注意点
✅トルク伝達能力の確認
キーの寸法や材質が適切でない場合、トルク不足やキーの破損が発生する可能性があります。
以下の公式で伝達トルクを計算し、必要な寸法を選定します。
\( \displaystyle T=\frac{τ・b・l・d} {2}\)
T: トルク、τ: 許容せん断応力、b: キー幅、l: キーの有効長さ、d: 軸径
✅過剰な干渉を避ける
キーの公差を無視した設計では、軸やハブへの過剰な応力が生じ、部品の摩耗や損傷につながる可能性があります。適切なはめあい公差(例えば、軸側h9、溝側H7)を考慮してください。
✅メンテナンス性
キーを取り外す際のアクセス性や、キー溝の清掃を考慮した設計を行うことで、メンテナンス効率を向上させられます。
規格と標準化の活用が設計の鍵
キーは、軸とハブの締結に欠かせない重要な要素であり、その規格化された寸法や適合性を活用することで、設計や製造の効率を高められます。
- JISやISO規格に準拠した標準部品の活用により、コスト削減や製造精度の向上が期待できます。
- 設計時には、キーの種類や寸法をトルク負荷や用途に合わせて適切に選定し、規格通りの加工を行うことが重要です。
これにより、製品の信頼性を高め、トータルコストを削減する効果が得られるでしょう。
キーの取り外しを簡単にする取り外し用タップの活用
機械設計で、動力伝達や位置決めのために使用される「キー」は、軸とハブ(ギアやプーリーなど)を締結する非常に重要な要素です。しかし、運転中のトルクや振動によってキーが圧着したり、錆によって固着した場合、取り外しが非常に困難になることがあります。
その解決策の一つが、「キーの取り外し用タップ」を加工しておくことです。本項では、その概要やメリット、設計時のポイントについて解説します。
キーの取り外しの課題
キーを取り外す際に直面する主な課題は以下の通りです。
🚫圧着や固着
- 運転中の負荷により、キーが軸やハブに圧着して取り外しが難しくなる。
🚫腐食や錆
- 長期間使用されたキーや軸が錆びると、キー溝内で固着してしまう。
🚫スペースの制約
- 周囲の部品によって作業スペースが限られ、工具が入りにくい場合がある。
取り外し用タップとは
キーの取り外し用タップとは、キー本体にねじ穴を設けておく加工のことです。このねじ穴を活用することで、ボルトをねじ込むだけでキーを簡単に引き抜くことが可能になります。
📌加工方法
- キーの中央にねじ穴(タップ)を設ける。
- タップサイズはキーの幅に応じて選定(例:M5、M6など)。
📌作業方法
- タップ穴に適切な長さのボルトをねじ込む。
- ボルトの頭を押し出し代わりとして使用し、キーを引き抜く。
取り外し用タップのメリット
取り外し用タップを加工することで、以下のようなメリットが得られます:
✅作業効率の向上
- 固着したキーでもボルトを回すだけで簡単に取り外し可能。
- 特にメンテナンス時の時間短縮につながります。
✅部品の損傷防止
- ハンマーやバールで叩いて無理に外す必要がなくなるため、キーや溝を傷つけるリスクが減少します。
✅安全性の向上
取り外し作業がスムーズに行えるため、力を過度に使わず安全に作業できます。
設計時の注意点
取り外し用タップを加工する際には、以下の点に注意しましょう:
⚠タップ穴の位置と深さ
- キーの中央に設けることで引き抜き力が均等にかかります。
- 穴の深さはキーの厚みに応じて適切に設定。底突きしないよう注意。
⚠タップサイズの選定
- ボルトが十分な引き抜き力を発揮できるサイズを選ぶ必要があります。キー幅が8mmの場合はM4、10mmの場合はM5などが一般的です。
⚠キーの材質と加工性
- 硬度の高い材質(例:焼入れ鋼)のキーはタップ加工が難しい場合があります。その際は軟材のキーを選ぶか、事前に工具メーカーに相談するのがおすすめです。
⚠コストとのバランス
- タップ加工には追加コストが発生します。メンテナンス頻度や作業性向上の重要性を考慮し、必要な箇所に限定して採用するのが効果的です。
取り外し用タップの活用事例
🔍大型機械のトルク伝達部
- 大型モーターや減速機のシャフトに使用されるキーは、負荷が大きいため固着しやすい。
- 取り外し用タップを加工しておけば、点検や修理時の作業が効率化されます。
🔍頻繁に取り外しが必要な部位
- 試験装置や交換頻度の高い部品では、取り外し用タップが特に有用です。
🔍錆の発生が懸念される環境
- 湿気や腐食性ガスの多い環境では、キーが錆びやすい。
- タップ加工により、固着したキーでも確実に取り外し可能となります。
キーに取り外し用タップを加工しておくことで、固着や圧着の問題を解決し、作業効率や安全性を大幅に向上させることができます。設計段階で適切なタップサイズや位置を考慮し、コストとメリットを見極めて導入することが重要です。
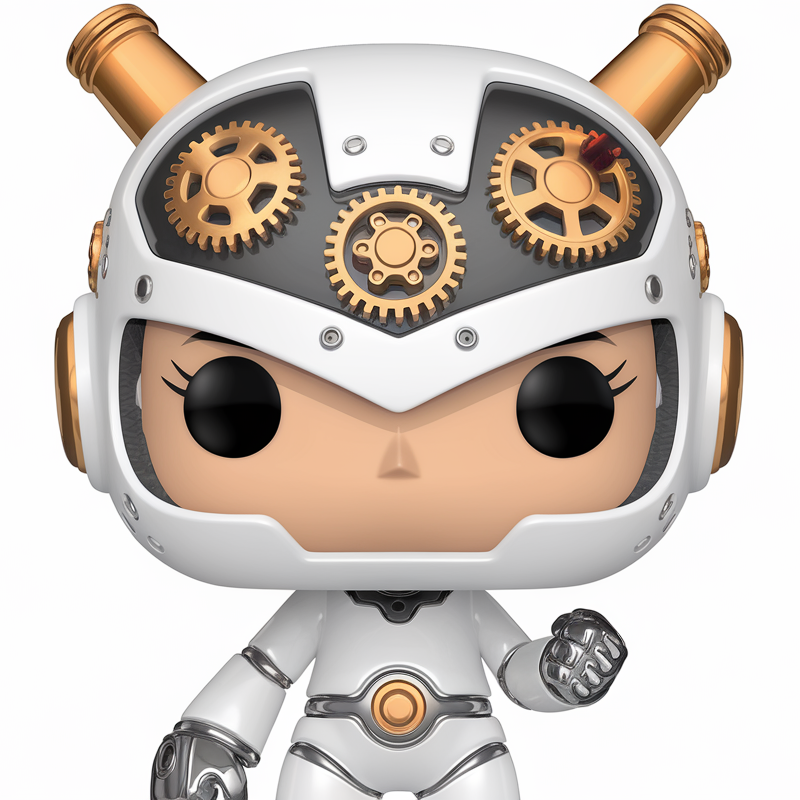
機械設計において、「取り外しやすさ」という観点も考慮することで、メンテナンス性の向上やトータルコストの削減につながります。
コメント