キー材の寸法は、JIS規格(日本産業規格)によって標準化されており、設計時にはこの規格に従って選定することが一般的です。
以下は、JIS B1301に基づく平行キーの規格寸法の一例です。
キー材の規格寸法表
新JIS規格表(JIS B 1301 – 1996 抜粋)
呼び寸法 | b(mm) | 許容差(h9) | h(mm) | 許容差 | 適応する軸径 (mm) | |
2×2 | 2 | 0 -0.025 | 2 | 0 -0.025 | h9 | 6 ~ 8 |
3×3 | 3 | 3 | 8 ~ 10 | |||
4×4 | 4 | 0 -0.030 | 4 | 0 -0.030 | 10 ~ 12 | |
5×5 | 5 | 5 | 12 ~ 17 | |||
6×6 | 6 | 6 | 17 ~ 22 | |||
8×7 | 8 | 0 -0.036 | 7 | 0 -0.090 | h11 | 22 ~ 30 |
10×8 | 10 | 8 | 30 ~ 38 | |||
12×8 | 12 | 0 -0.043 | 8 | 38 ~ 44 | ||
14×9 | 14 | 9 | 44 ~ 50 | |||
16×10 | 16 | 10 | 50 ~ 58 | |||
18×11 | 18 | 11 | 0 -0.110 | 58 ~ 65 | ||
20×12 | 20 | 0 -0.052 | 12 | 65 ~ 75 | ||
22×14 | 22 | 14 | 75 ~ 85 | |||
25×14 | 25 | 14 | 85 ~ 95 | |||
28×16 | 28 | 16 | 95 ~ 110 | |||
32×18 | 32 | 0 -0.062 | 18 | 110 ~ 130 |
旧JIS規格表(JIS B 1301 – 1959 抜粋)
呼び寸法 | 旧JIS規格 1種 | 旧JIS規格 2種 | ||||||
b(mm) | 許容差(p7) | h(mm) | 許容差 (h9) | b(mm) | 許容差(h8) | h(mm) | 許容差 (h10) | |
2×2 | 2 | +0.018 +0.009 | 2 | 0 -0.025 | 2 | 0 -0.014 | 2 | 0 -0.040 |
3×3 | 3 | 3 | 3 | 3 | ||||
4×4 | 4 | +0.024 +0.012 | 4 | 0 -0.030 | 4 | 0 -0.018 | 4 | 0 -0.048 |
5×5 | 5 | 5 | 5 | 5 | ||||
7×7 | 7 | +0.030 +0.015 | 7 | 0 -0.036 | 7 | 0 -0.022 | 7 | 0 -0.058 |
10×8 | 10 | 8 | 10 | 8 | ||||
12×8 | 12 | +0.036 +0.018 | 8 | 12 | 0 -0.027 | 8 | ||
15×10 | 15 | 10 | 15 | 10 | ||||
18×12 | 18 | 12 | 0 -0.043 | 18 | 12 | 0 -0.070 | ||
20×13 | 20 | +0.043 +0.022 | 13 | 20 | 0 -0.033 | 13 | ||
24×16 | 24 | 16 | 24 | 16 | ||||
28×18 | 28 | 18 | 28 | 18 | ||||
32×20 | 32 | +0.051 +0.026 | 20 | 0 -0.052 | 32 | 0 -0.039 | 20 | 0 -0.084 |
35×22 | 35 | 22 | 35 | 22 | ||||
38×24 | 38 | 24 | 38 | 24 | ||||
42×26 | 42 | 26 | 42 | 26 | ||||
45×28 | 45 | 28 | 45 | 28 | ||||
50×31.5 | 50 | 31.5 | 0 -0.062 | 50 | 31.5 | 0 -0.100 |
1種キーと2種キーの違いとは?
- 1種キー(締込み形)
軸にキーをしっかり固定し、ハブ側を締め込むことでガタつきを防ぎます。キー寸法にはプラスの許容差があり、軸との嵌合がタイトです。高トルクの伝達や打ち込み式の構造に適しています。 - 2種キー(普通形)
軸にキーを固定し、ハブをはめ込むだけの構造。キー寸法にはマイナスの許容差があり、嵌合が緩めで軸方向に摺動が可能です。クラッチや変速機など、ハブの移動が必要な機構に向いています。
キーの材質
キー材の材質には、主に炭素鋼(S45Cなど)や合金鋼が使われます。これらの材料は、トルク伝達や振動、摩耗に対して高い耐久性を持っています。また、使用環境や負荷条件に応じて表面処理や熱処理が施されることもあります。
キーのはめあいと精度
緩やかなはめあいでは組み立てがしやすくなる一方で、タイトなはめあいは高いトルク伝達能力を持ちます。精度やクリアランスは、負荷条件や要求精度に応じて選定することが重要です。
平行キーは、機械設計において非常に重要な部品であり、主にシャフトとハブ間でのトルク伝達を実現するために使用されます。キーと軸、ハブの間の適切なはめあい精度は、設計の信頼性と性能に大きく影響します。以下に、平行キーのはめあい精度に関する要点をまとめます。
はめあいの種類
平行キーのはめあいには主に次のような種類があります。
✅すきまばめ
- 軽い組み付けが可能で、キーの挿入や取り外しが容易です。
- このはめあいは、メンテナンスや調整を頻繁に行う必要がある機構で使用されます。
- また、製造公差に対する要求が比較的緩やかです。
✅中間はめあい
- すきまばめとしまりばめの中間に位置するはめあい。
- キーがしっかりと固定され、なおかつ取り外しも可能なバランスの取れた形態です。
✅しまりばめ(圧入)
- 高いトルク伝達能力が求められる場合に用いられます。
- キーとキー溝の間にほとんどすきまがないため、組み立てには圧力や叩き込みが必要です。
- このはめあいは、強い固定力を提供しますが、取り外しが困難です。
はめあい精度の重要性
はめあい精度は、平行キーの性能と耐久性に直結しています。以下の点が特に重要です:
📌トルク伝達の効率化
適切なはめあいは、キーに余分な衝撃を与えず、滑らかなトルク伝達を実現します。
📌振動と騒音の低減
不適切なはめあいは、部品間の摩耗を促進し、振動や騒音の原因となるため、最適なはめあいが求められます。
📌部品の破損防止
過度なすきまや圧力がキーやキー溝にかかると、機械的な変形や破損を招く可能性があるため、高精度なはめあいはこれを防ぐ役割を担います。
設計および製造における考慮点
🔍製造公差
- キーとキー溝の寸法公差は、設計時に綿密に計算する必要があります。
- 一般的な公差は、ISOやJISなどの標準規格に基づいて決定します。
🔍材料の選定
- 使用する材料の硬度や表面状態も影響を与えます。
- 通常、キーはハブやシャフトよりも若干柔らかい材料が用いられ、摩耗が発生した場合にキーが先に劣化するようデザインされます。
🔍メンテナンス性
- 組み立てや分解が容易であることは、保守や修理の観点からも重要です。
- 設計段階で適切なはめあい種類を選択することが求められます。
平行キーのはめあい精度は、機械設計におけるトルク伝達の効率化や振動・騒音低減に多大な影響を与えます。設計工程では、適切なはめあいの種類を選択し、製造公差、材料選定、メンテナンス性を考慮することが重要です。これにより、機械システム全体の性能と信頼性が向上し、長期的な運用コストを削減することが可能となります。
トルク伝達以外の使い道と工夫
キー材料は、機械設計において主にトルク伝達のために使用されますが、その高い強度と加工性の良さから、トルク伝達以外の用途にも幅広く活用されています。
以下に、キー材料のトルク伝達以外の使い道と工夫について、具体的な例を交えて解説します。
調整用ブロックのガイド
キー材料は、長穴や調整ねじを用いた調整用ブロックのガイドとして使用することができます。
キー材料を調整用ブロックのガイドとして利用することができます。例えば、長穴や調整ねじと組み合わせて使用し、設計時の微調整を簡易に行うためのガイドとして機能させることができます。これは、製造時やメンテナンス時の作業効率を向上させるのに役立ちます。
調整用ブロックの設計において、長穴や調整ねじを利用することができます。これにより、以下のような利点があります。
✅精密な位置調整
- 長穴の形状を活かして、微調整が可能になるため、部品の位置決めが非常に精密に行えます。
✅分解可能な設計
- 調整ねじを使用することで、部品の分解・再組立が容易になり、メンテナンス性が向上します。この機能は、構造の耐久性を評価するために重要です。
✅摩擦の軽減
- 材料の組み合わせや表面処理を工夫することで、ガイド部分の摩擦を低減し、調整作業をスムーズに行えるようにします。
嵩増しブロックとして使用
必要に応じて、キー材料を使用して嵩増しブロックを作成することができます。特に、設計変更時や既存のシステムに新しいコンポーネントを追加する際に、迅速に対応するための一時的な解決策として役立ちます。
✅寸法調整
- キー材料を組み込むことで、部品の寸法を調整し、設計上の要求を満たすことができます。
プレートの位置決め
キー材料をプレートや部品の位置決めとして使用することも可能です。これにより、組み立て時の正確な位置合わせを実現し、製造精度を高めることができます。特に、簡易な治具や固定具として、キー材料が有用です。
✅平行位置決め
キー材料をプレートと軸の間に挟むことで、プレートを平行に位置決めできます。
✅角度位置決め
キー材料を角度をつけてプレートに組み込むことで、プレートを角度位置決めできます。
- 互換性のある設計: 標準化された寸法と穴の配置を使用することで、異なる部品との互換性を持たせ、製造工程の効率を向上させます。
- 固定力の向上: 材材料の表面処理、例えば滑り止め加工やコーティングを行うことで、プレートの固定力を向上させ、所定の位置を確保することができます。
- 調整機構の統合: 位置決め用のプレートに調整機構を組み込むことで、取り付け時の微調整が可能になり、組み立てる際のストレスを軽減します。
その他の用途
📌スペーサーとしての利用
固定要素間に一定の間隔を保持するためのスペーサーとして使用することができます。
📌振動減衰、補強
キー材料をシャフトや部品の振動減衰材として利用することも可能です。特定の材質であれば、振動を効率的に吸収することができます。
📌仮固定治具
組み立てや加工途中の仮固定治具として、一時的にキー材料を使用することができます。
これらの工夫により、キー材料は多様な用途に応じて柔軟に対応でき、設計や製造のプロセスを最適化することが可能です。
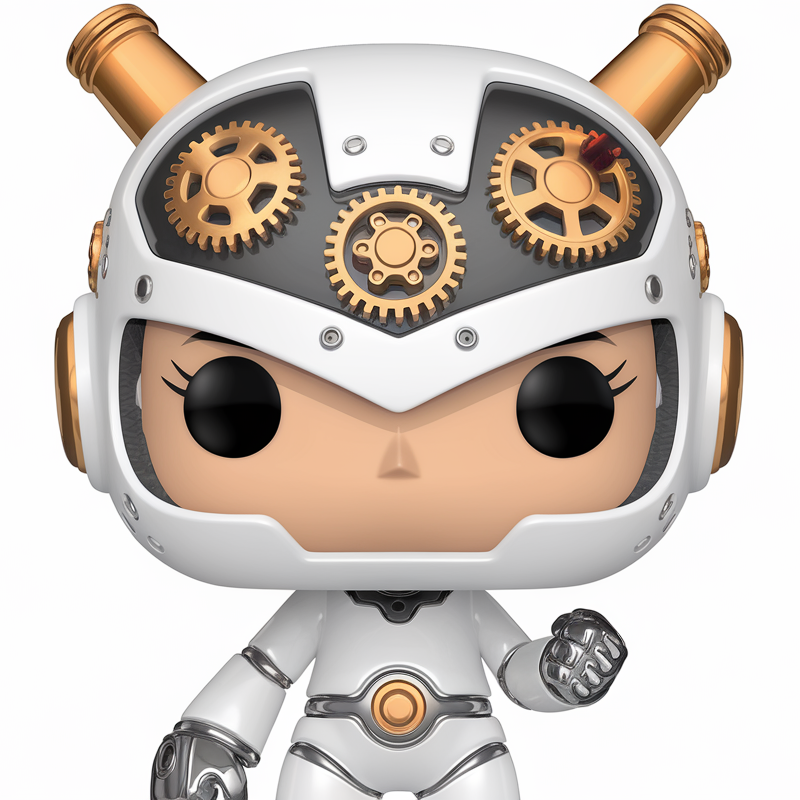
キー材料は、トルク伝達以外にも、調整用ブロックのガイド、嵩増しブロック、プレートの位置決めなど、様々な用途で活用できます。それぞれの用途に合わせて、キー材料の形状や材質を工夫することで、より効果的に利用することができます。
まとめ
キー材は機械設計において、回転軸と部品を結合してトルクを伝達するための重要な要素です。設計時には、軸径に応じた適切な規格寸法や材質、はめあいの精度を考慮することが求められます。規格に基づいた適切なキーの選定は、機械の信頼性や性能向上に直結しますので、慎重な設計が必要です。
コメント