ねじおよびボルトは、機械設計における基本的かつ重要な機械要素であり、部品の固定や組立、分解を容易にするために広く使用されています。これらの要素は、種類や用途によって異なり、それぞれの特性に応じた選定が求められます。この記事では、ねじとボルトの代表的な種類とその特性について詳しく解説します。
そもそも「ねじ」と「ボルト」の違いって?
ねじとボルトの違い
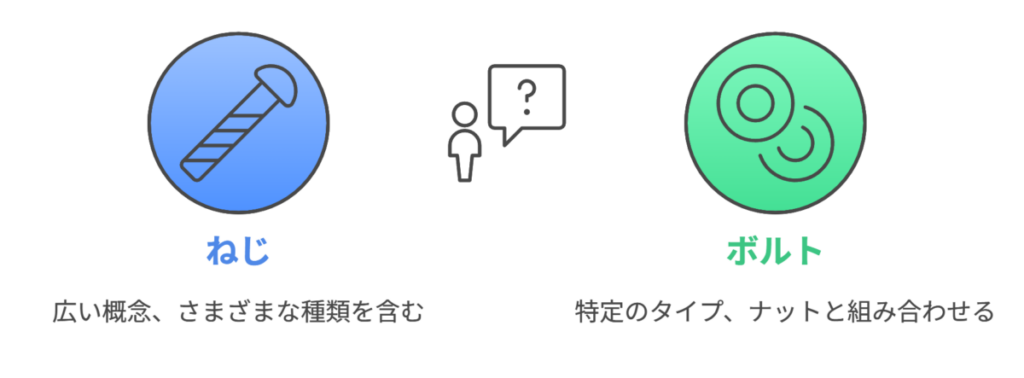
「ねじ」とは?
- ねじ(螺子)は、らせん状の溝がある部品の総称です。
- 外側に溝があるものを「おねじ」、内側に溝があるものを「めねじ」と呼びます。
- 「ねじ」という言葉は、ボルト・ビス・ナットなどを含む広い概念です。
「ボルト」とは?
- 「ボルト」はねじの一種で、主にナットと組み合わせて使う雄ねじを指します。
- 一般的には、直径が8mm以上で、頭部が六角形や四角形のものが多いです。
- ナットとセットで締結することで、部品同士を強固に固定できます。
用語 | 定義 | 特徴 |
---|---|---|
ねじ | らせん状の溝がある部品の総称 | 雄ねじ・雌ねじを含む広い概念 |
ボルト | ナットと組み合わせて使う「おねじ」 | 通常は太くて頭が六角形、強力な締結に使用 |
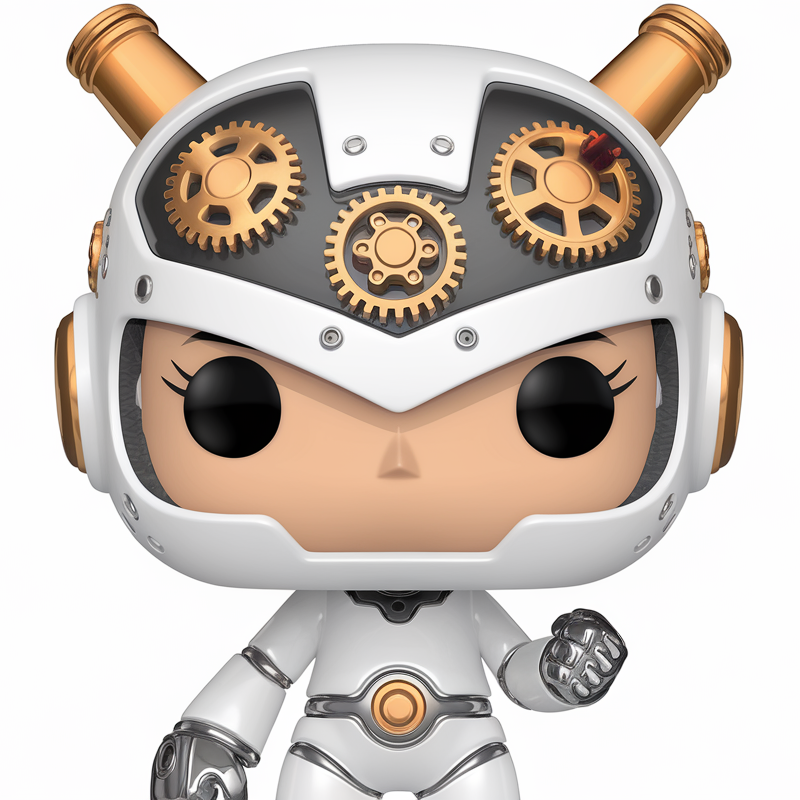
つまり、「ボルト」は「ねじ」の一種であり、ナットとセットで使うことが前提のねじです。
代表的なボルト・ねじの種類
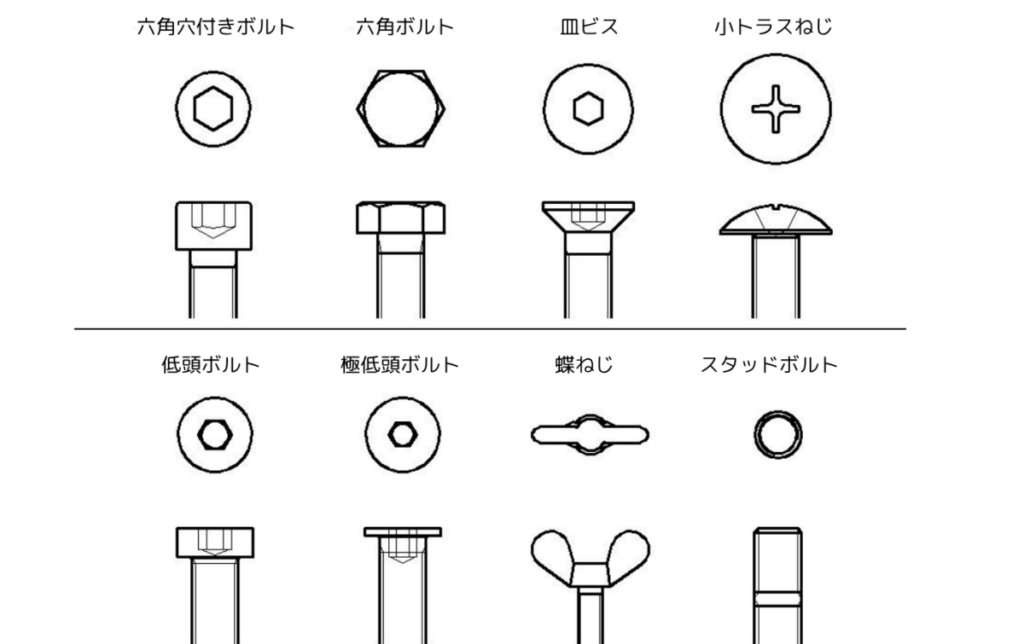
六角穴付きボルト(キャップボルト)
六角穴付きボルト(通称「キャップボルト」)は、機械設計において頻繁に使用されるねじの一種で、その特徴や利点、適用範囲から選定ポイントまで多岐にわたる要素が重要です。
六角穴付きボルトの特徴
- 形状
- 六角穴付きボルトは、その頭部中央に六角形の穴があります。
- 専用の六角レンチを使用して締め付けます。
- この構造により、外観がすっきりし、スペースの限られた場所でも使用しやすいのが特徴です。
- 高い締結力
- 六角穴は六角レンチを差し込むことでトルクをかけやすく、強い締結力を発揮します。
- 特に、振動や高負荷がかかる機械の部品固定に適しています。
- 省スペース設計
- 頭部が低くコンパクトなため、設計上スペースを有効活用する必要がある場合に最適です。
- 機械内部や狭い場所での使用にも対応できます。
- 座ぐり穴加工なら、フラット面で締結可能
耐久性と多様な材質
- 六角穴付きボルトは強度区分が明確に定められています。
- 高強度の炭素鋼やステンレス鋼、特殊合金など、多様な材質で提供されます。
- 用途や環境に応じて最適な材質を選択できます。
六角穴付きボルトの主な用途
- 精密機器の組み立て
- コンパクトな頭部形状のため、精密機器や小型装置で使用されることが多いです。
- 機械部品の固定
- 機械設計では、高負荷がかかる部分の固定に使用されます。
- 特に振動が頻繁に発生する箇所に適しています。
- 外観を重視する設計
- 頭部が目立たないため、デザイン性が求められる製品にも採用されています。
六角穴付きボルトの利点と注意点
✅利点
- コンパクトで強度が高いため、スペース効率が良い。
- トルク伝達性に優れ、確実な締結が可能。
- 多様な材質と表面処理から選択可能で、幅広い用途に対応。
🚫注意点
- 六角穴が損傷するとレンチが滑り、取り外しが困難になる。
- 締め付け時に適切なトルク管理が必要。過剰な締め付けはボルトの破損につながる。
- 六角レンチのサイズが合わないと締結が不十分になることがある。
六角ボルト
六角ボルトは、機械設計において最も一般的で汎用性の高いねじの一種です。頭部が六角形でスパナやレンチを用いて締め付けができるため、取り扱いやすく、多様な用途に利用されています。
六角ボルトの特徴
- 形状のシンプルさと汎用性
- 六角ボルトは、六角形の頭部形状です。
- スパナやソケットレンチを用いることで効率的にトルクを加えることができます。
- このシンプルな形状により、強度と締結力に優れ、多くの設計で採用されています。
- 多様なサイズと規格
- JIS(日本工業規格)やISO(国際規格)に準拠した多様なサイズが用意されています。
- 長さ、太さ、ネジ山のピッチが幅広く揃っており、さまざまな用途に対応可能です。
- 材質と表面処理
- 炭素鋼、ステンレス鋼(SUS304やSUS316)、耐熱合金など
- さまざまな材質で提供されており、環境や用途に応じて選択できます。
- 表面処理(亜鉛メッキ、、黒染めなど)により、耐腐食性や外観の向上が図られます。
- 高い耐荷重性
- 頭部が大きいため工具がしっかりと固定でき、大きなトルクをかけることが可能です。
- この特性から、振動や大きな荷重がかかる箇所にも適しています。
六角ボルトの主な種類
- 全ネジボルト
- ボルト全体にネジ山が刻まれており、締結力を最大化したい場合に使用。
- 半ネジボルト
- ボルトの頭部近くにネジ山がなく、せん断力を受ける部分の強度を高める設計。
- 高強度ボルト
- 炭素鋼や合金鋼で製造され、特に高荷重や振動のある用途に使用される。
- 例として、強度区分8.8や10.9が挙げられます。
- ユニクロメッキ六角ボルト
- 錆びにくいメッキ処理が施されており、屋外環境や湿度の高い環境に適しています。
- ステンレス六角ボルト
- SUS材で製造され、耐食性が求められる用途に使用。
六角ボルトの主な用途
- 機械や構造物の組み立て
- 機械設計において主要な部品を固定する際に使用。
- 建築分野
- 建築構造物や配管設備の締結に活用。
- メンテナンスや修理
- 汎用性が高く、工具が揃っていれば取り外しや再利用も容易。
六角ボルトの利点と注意点
✅ 利点
- スパナやソケットレンチで締め付けやすく、作業性が高い。
- 汎用性が高く、入手しやすい。
- 材質や表面処理が多様で、幅広い環境条件に対応可能。
🚫 注意点
- 過剰な締め付けにより、ねじ山が破損する恐れがある。
- 長期間使用後、錆びや固着により取り外しが困難になることがある。
- 強度区分を無視すると、過負荷で破損する可能性がある。
皿ねじ
皿ねじは、頭部が平らな円錐形をしたねじで、締結した際に頭部が部材に埋め込まれる特徴を持つ特殊なねじです。
機械設計や製造業において、製品の外観を整えたり、部材同士の接合を滑らかにするためによく使用されます。
皿ねじ特徴
- 埋め込み可能なデザイン
- 皿ねじの最も大きな特徴は、頭部が部材の表面に埋め込まれることです。
- これにより、表面が平らになり、製品の美観を損なうことがありません。
- また、他の部品と干渉しにくいため、部材同士を緊密に接合する場面で有効です。
- さまざまな材質と表面処理
- 炭素鋼やステンレス鋼、アルミニウムなど、用途に応じた多様な材質で製造されています。
- 亜鉛メッキや黒染め、クロメート処理などの表面処理により、耐腐食性や強度が向上します。
- 締結の精度
- 座面がテーパ状になっているため、適切に加工された皿穴に対して確実に位置決めができます。
- これにより、高い締結精度が求められる用途に適しています。
- 低プロファイル設計
- 締結後の頭部が平らになるため、可動部分や外部装置との干渉を最小限に抑えることが可能。
- 特に狭いスペースでの設計や動的要素を持つ機械に適しています。
皿ねじの主な種類
- 十字穴付き皿ねじ
- ドライバーを使用して簡単に締め付けが可能。
- 一般的な用途に最適。
- 六角穴付き皿ねじ
- 六角レンチを使用し、高いトルクで締め付けることが可能。
- 機械部品の固定に多用されます。
- トルクス皿ねじ
- 星型の溝を持ち、専用工具で締め付け。
- トルク伝達が効率的で、滑りにくい。
- 平頭皿ねじ
- 一般的な皿ねじよりも頭部が平らで、大きな接触面積を持つ。
- 特殊皿ねじ
- セキュリティ目的や特殊用途のための設計が施されたねじ。
- 例として、盗難防止ねじや絶縁用途のねじがあります。
皿ねじの主な用途
- 家電製品
- 表面が滑らかで外観が重要な製品で使用。
- 例として、パソコンや家電機器の筐体部。
- 機械部品の接合
- 機械要素を固定する際に、部品干渉を避けるために使用。
- 建築用途
- 内装や家具の接合部で使用。
- フラットな仕上がりが求められる場面に適している。
皿ねじの利点と注意点
✅ 利点
- フラットな仕上がり
- 頭部が部材の表面と同一平面になるため、外観が美しく仕上がります。
- 特に、見た目が重要な製品や機構では大きなメリットです。
- 部材干渉の防止
- 頭部が突出しないため、他の部品や可動部分と干渉しにくく、設計の自由度が向上します。
- 位置決めが容易
- テーパ状の座面が皿穴と正確に嵌合するため、締結時に自動的に位置決めが行われます。
- これにより、高い位置精度が求められる用途に適しています。
- 幅広い用途
- 家電製品、自動車部品、建築材料など、さまざまな分野で利用可能です。
- また、専用工具を用いることで盗難防止用途にも活用できます。
- 軽量化への貢献
- 頭部が小さく、全体の質量を削減できるため、軽量化が求められる機械や構造物で有効です。
🚫 注意点
- 皿穴加工が必要
- 皿ねじを使用するには、接合部材に適切な皿穴を加工する必要があります。
- この加工が不正確だと、ねじが適切に座らず、締結力の低下や緩みの原因となります。
- 応力集中のリスク
- 円錐状であるため、締結部分に応力が集中しやすく、部材が損傷する可能性があります。
- 特に、薄い部材を締結する際には注意が必要です。
- 締め付けトルクの制限
- 過剰なトルクで締め付けると、頭部が変形したり、座面が潰れる恐れがあります。
- 適切なトルク管理が重要です。
- 工具選定の必要性
- 十字穴や六角穴など、頭部形状に応じた専用工具が必要です。
- 工具が適切でない場合、頭部が損傷してねじが取り外せなくなる可能性があります。
- 腐食の可能性
- 使用環境に応じて適切な材質や表面処理を選ばないと、ねじが腐食し、接合強度が低下します。
- 屋外用途や湿気の多い環境では特に注意が必要です。
- 分解の困難さ
- 頭部が埋め込まれるため、錆びたり損傷したりすると、ねじを取り外すのが困難になります。
皿ねじを使用する際のアドバイス
- 皿穴の加工には、ねじ頭部の直径と角度(通常90°)に合ったリーマーやドリルを使用してください。
- 素材の強度や使用環境に応じて、
耐腐食性の高いステンレス鋼や表面処理された皿ねじを選ぶと良いでしょう。 - 適切な締め付けトルクを確認し、トルクレンチを使用することで、部材損傷や緩みを防げます。
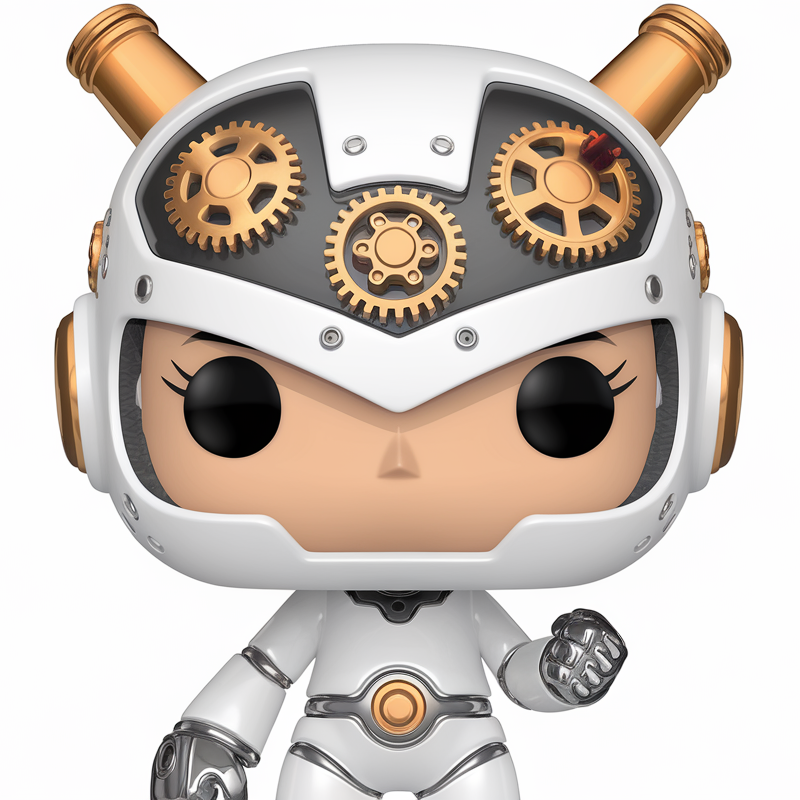
皿ねじは設計や施工の自由度を広げる便利な部品ですが、
適切に使用しなければその利点を十分に活かせません。
注意点を理解し、最適な形で活用しましょう。
小トラスねじ
小トラスねじは、頭部が広くて低い形状を持つねじの一種で、見た目が「きのこの笠」に似ていることから、トラス頭ねじとも呼ばれます。主に機械設計や家電製品、金属部材の固定など、幅広い分野で使用されています。
このねじは、特に締結部材を広い面積で押さえる必要がある場合や、美観を損ねたくない場面で役立ちます。また、頭部の高さが低いため、突出部分を抑えたい設計にも適しています。
小トラスねじの特徴
- 広い座面で締結力を分散
- 頭部は平らで直径が大きいため、接合部材にかかる力を広い範囲に分散できます。
- これにより、部材の変形や破損を防ぎやすくなります。
- 頭部の低いプロファイル
- 頭部の高さが低いデザインのため、突起が少なく、製品の外観がすっきりとします。
- また、狭いスペースでの使用にも適しています。
- 美観を損ねない設計
- 頭部が大きく平らで、目立ちにくい形状のため、見た目が重視される用途に適しています。
- 工具の取り扱いが簡単
- 十字穴や六角穴が採用されることが多く、一般的な工具で締め付けや取り外しが容易です。
小トラスねじの主な用途
- 金属部材の固定
- 薄い金属プレートを固定する際に適し、広い接触面で部材のゆがみを防ぎます。
- DIYや軽量構造物
- 木材や薄いプラスチック部材を締結する際に広く使用され、簡単な施工が可能です。
- 自動車や航空機部品
- 突起を抑えたい部位で採用され、空気抵抗や美観に配慮した設計に貢献します。
小トラスねじの利点と注意点
✅ 利点
- 高い保持力
座面が広いことで、部材への締結力が分散され、接合部の強度が向上します。 - 外観の向上
頭部のデザインにより、完成品の見た目が良くなるため、外装部品に最適です。 - 薄い部材への対応力
頭部の広さが薄い部材に適しており、変形や損傷を防ぎやすいです。 - 取り外しやすさ
工具がしっかりとフィットするため、ねじの脱着が簡単に行えます。
🚫 注意点
- 埋め込みができない
- 頭部が突出するため、完全に埋め込む必要がある設計には不向きです。
- 皿ねじなどの選択を検討する必要があります。
- トルク管理の重要性
- 頭部が広いため、締め付けトルクが過剰になると、接合部材を損傷する恐れがあります。
- 適切な締付けトルクを確認してください。
- 使用環境に注意
- 材質や表面処理によっては、腐食や摩耗が発生しやすい場合があります。
- ステンレス製やメッキ処理されたねじを選ぶと、耐久性が向上します。
低頭ボルト・極低頭ボルト
低頭ボルトと極低頭ボルトは、通常のボルトよりも頭部の高さを低くした特殊なねじです。これらは、スペース制限が厳しい設計や、美観を重視した設計に用いられます。機械設計においては、装置の小型化や高密度設計を実現する重要な部品です。
低頭ボルトの特徴
- 頭部高さが低い
- 標準ボルトの頭部高さと比べ、約半分程度の高さに設計されている。
- 設置スペースを節約できます。
- 高い強度
- 頭部が低くても強度を確保するため、材質や形状が最適化されています。
- 主にクロモリ鋼やステンレスが用いられます。
- 工具アクセスが容易
- 主に六角穴付きが採用されており、狭いスペースでも工具を使用しやすいです。
極低頭ボルトの特徴
- さらに薄い頭部
- 極低頭ボルトは、低頭ボルトよりもさらに頭部の高さを低くした設計です。
- 標準ボルトの1/3以下の高さで、超狭小スペースにも対応可能です。
- 限られたトルク対応
- 頭部の薄さゆえに、トルクの適用範囲が限定されます。
- 必要以上に締め付けると破損のリスクがあるため、注意が必要です。
- 専用の用途
- 一般的な使用よりも、特定の用途や設計上の制約に対応するために採用されます。
低頭ボルトの主な用途
- 産業機械
可動部やカバー部など、スペースに制限がある箇所で使用されます。 - 家電製品
内部構造の固定に使用され、コンパクトな設計を可能にします。 - 輸送機器
車両や航空機部品の組み立てで、軽量化とスペース効率を向上させます。
極低頭ボルトの主な用途
- 精密機器
精密部品の固定に使用され、干渉を最小限に抑えます。 - 電子機器
回路基板や筐体内部の狭小空間での固定に最適です。 - 装飾デザイン
ボルト頭部を目立たせたくない装飾品や建築部材に使用されます。
低頭ボルトと極低頭ボルトの利点と注意点
✅ 利点
- 省スペース設計に対応
頭部の高さが低いため、狭い空間でも干渉を避けられます。 - 軽量化に寄与
頭部の体積が小さいことで、全体の重量を抑えられます。 - 美観に優れる
頭部が目立たず、製品の外観を損ねない設計が可能です。
🚫 注意点
- トルク管理の重要性
- 頭部の高さが低いため、締め付けトルクが適切でないと破損する可能性があります。
- 特に極低頭ボルトでは、トルクの上限に注意が必要です。
- 特殊な工具が必要な場合がある
- 狭いスペースで使用されることが多いため、専用の薄型工具が必要な場合があります。
- 材質選定の慎重さ
- 特に極低頭ボルトは、負荷が集中しやすいため、材質の強度や耐摩耗性が重要です。
- 入手性
- 標準ボルトに比べて特殊な部品であるため、
必要なサイズや材質の在庫が限られている場合があります。
- 標準ボルトに比べて特殊な部品であるため、
蝶ねじ
蝶ねじは、指で簡単に締め付けたり緩めたりできるように設計された特殊なねじです。ねじ頭部が「蝶」の形に似ていることから名付けられました。
工具を使わずに操作できるため、頻繁に着脱が必要な箇所や、工具が使いづらい場所でよく使用されます。
蝶ねじの特徴
- 工具不要の操作性
- 頭部が大きく、指で直接回すことができるため、簡単に取り付け・取り外しが可能です。
- デザイン性
- 特徴的な頭部形状は視覚的に目立ちやすく、装飾的な用途にも適しています。
- 多用途性
- 機械部品の一時固定や調整箇所、家具、家電、DIY製品など、幅広い分野で使用されます。
- 材質の多様性
- 鉄製、ステンレス製、真鍮製など、使用環境に応じた材質が選択可能です。
蝶ねじの主な用途
- 調整箇所の固定
- 設備や装置の位置調整用の部品として使用され、工具を使わずに素早く調整が行えます。
- カバーやパネルの取り付け
- 工具を用いずに頻繁に取り外しが必要なカバーやパネルの固定に適しています。
- 展示会や店舗装飾
- ディスプレイの設置・調整で簡単に扱えるため、作業効率が求められる場面に便利です。
- DIY製品や家具
- 手軽さを活かし、家庭用品や日曜大工での用途が広がっています。
蝶ねじの利点と注意点
✅ 利点
- 工具不要で手軽
- 工具がなくても取り扱えるため、設置や調整の時間を大幅に短縮できます。
- 見た目に優れる
- 他のねじと比べてデザイン性が高く、目立たせたい部分に使われることが多いです。
- 再利用可能
- 頻繁な着脱に耐えられるため、消耗品としてのコストが抑えられます。
- カスタマイズ性
- 頭部が大きいことで、装飾や塗装によるカスタマイズがしやすいです。
🚫 注意点
- 締付けトルクの限界
- 指で締め付けるため、工具を用いる六角ボルトなどに比べて締付け力が弱い。
- 緩みやすい。
- 使用環境の制限
- 高温や振動が多い場所では緩む可能性が高く、適切でない場合もあります。
- 耐久性
- 頻繁に取り扱う場合、材質によっては摩耗しやすいことがあります。
- 特に樹脂製蝶ねじは破損しやすいため注意が必要です。
- スペースの制約
- 頭部が大きい分、取り付け箇所に十分なスペースが必要です。
スタッドボルト
スタッドボルトは、両端にねじが切られており、中間部はねじがない棒状のねじです。主に機械設計や配管設備などで、部品同士を確実に固定するために使用されます。片端を対象物にねじ込み、もう片端にナットを取り付けて締結することで、安定した接続が可能です。
スタッドボルトは、強度が求められる場面や、頻繁な取り外しが必要な箇所で活躍します。
スタッドボルトの特徴
- 高い締付け力
- ねじの両端で締付けるため、強い締付け力を発揮し、確実に部品を固定します。
- 繰り返し使用に強い
- 主にナットを取り外すだけで着脱が可能。
- スタッドボルト本体が劣化しにくく、長期間の使用が可能です。
- さまざまなサイズと材質
- 小型部品から大型機械まで対応可能な多様なサイズがあります。
- 使用環境に応じた材質(ステンレス、合金鋼、炭素鋼など)が選べます。
- 片端固定が可能
- 片側が対象物にねじ込まれて固定できる。
- 片端がしっかりと動かない状態で作業を進めることができます。
📌 主な用途
- エンジン部品の固定
- シリンダーやエキゾーストマニホールドなど、強い締付けが求められる部分で使用されます。
- 配管のフランジ接続
- フランジをしっかり固定するために使われ、振動や圧力による影響を軽減します。
- 高負荷部品の締結
- 重機や大型機械の重要な部品同士を固定するために利用されます。
- メンテナンスが頻繁な箇所
- ねじ部が劣化しにくい構造のため、定期的な取り外し・交換が求められる場所に最適です。
スタッドボルトの利点と注意点
✅ 利点
- 高い耐久性
材料が劣化しにくく、長期間使用しても締付け力が維持されます。 - 柔軟な設計
ナットを交換することで簡単に締結の強度や緩み止め効果を調整できます。 - 振動に強い
特に配管やエンジンなど振動が発生する箇所において、締結部が緩みにくい特性を持ちます。 - 分解作業が容易
ナットを外すだけで取り外しができるため、メンテナンス作業の効率が向上します。
🚫 注意点
- 締付けトルクの管理
- 過剰なトルクで締付けると、ボルトの破損やねじ山の損傷が発生する可能性があります。
- 適切なトルクで締付ける必要があります。
- ねじ込み深さの確認
- 片端を対象物にねじ込む際、十分な深さまでねじ込まないと固定力が不足する場合があります。
- 材質選び
- 使用環境に適した材質を選ばないと、腐食や摩耗のリスクが高まります。
- 特に、高温や化学薬品の影響がある場所では材質の選定が重要です。
- 緩み止め対策
- ナットが振動や衝撃で緩む可能性があるため、スプリングワッシャーやロックナットの併用が推奨されます。
ねじの選定ポイント
機械設計において、ねじを選定する際に重要となるポイントを以下に示します。
材料選定
ねじの材料は、その使用環境や強度要求に大きく影響します。以下の材料が一般的です。
✅ 炭素鋼(普通鋼)
- 一般的な強度を必要とする場合に使用されます。
- コストも安価で、広く使用されていますが、錆びやすいという欠点があります。
✅ ステンレス鋼(SUS)
- 耐腐食性が高く、湿気や水に強いです。
- 強度も十分に高く、屋外や食品関連設備でよく使用されます。
✅ 合金鋼
- 高強度を必要とする場面で使用されます。
- 通常の炭素鋼よりも強度が高く、耐摩耗性や耐熱性に優れています。
ねじの強度区分
ねじには「強度区分」という指標があり、使用する場所に応じた強度を選定する必要があります。特に高負荷のかかる箇所では、強度等級が高いものが要求されます。例えば、6.8や8.8などの数字は、ねじの引張強度と降伏強度を表しています。
- 一般用途: 4.6、4.8などの低強度等級
- 中程度の負荷: 6.8、8.8
- 高負荷: 10.9、12.9などの高強度等級
ねじのサイズ(径・長さ)
設計する機械の寸法や取り付け方法に合わせて、適切なサイズのねじを選定します。
ねじ径が大きくなるほど強度が上がりますが、それに伴い重量やコストも増します。設計時には、必要な強度を満たしつつ、最適なサイズを選定することが求められます。
引張強度、せん断強度
✅ 引張強度
ねじを軸方向に引っ張る力に対する強度
✅ せん断強度
ねじの断面に対して横方向に作用する力に対する強度
使用環境
ねじの使用環境も選定には重要です。例えば、屋外や湿度の高い環境では、錆びに強いステンレス製のねじが適しています。また、高温環境や化学物質が存在する場所では、耐熱性や耐腐食性のある材料を選ぶ必要があります。
✅ 屋内での一般使用: 炭素鋼
✅ 屋外や湿度の高い環境: ステンレス鋼
✅ 高温や化学的環境: 耐熱合金鋼や化学耐性のある材料
摩擦と緩み対策
ねじは、振動や衝撃で緩みやすいため、緩み対策が必要です。緩み防止には、ナイロンロックナットやスプリングワッシャー、ねじロック剤の使用が効果的です。また、繰り返しの締め直しが必要な箇所には、再利用可能なナイロンロックナットが推奨されます。
🚫 振動や衝撃がある場合
- ロックナットやスプリングワッシャー
🚫 緩み防止が必要な箇所
- ねじロック剤の使用
トルクと締め付け力
ねじを締め付ける際には、適切なトルク管理が必要です。過度なトルクはねじや材料を破損させる可能性があり、逆に不足したトルクは緩みの原因となります。トルク管理にはトルクレンチを使用し、適切な締め付けトルクを確認することが大切です。
まとめ
機械設計におけるねじの選定は、強度、材料、使用環境、摩擦や緩み対策など多くの要素を考慮する必要があります。正しい選定が行われることで、機械の安全性や性能を確保できるだけでなく、メンテナンスの効率も向上します。ねじの種類や選定ポイントを理解し、適切なねじを選ぶことが、機械設計の成功に繋がります。
コメント