機械設計において、ボルトはさまざまな用途で使われ、設計の目的に応じて適切なボルトを選定することが重要です。その中でも、低頭ボルトと極低頭ボルトは、限られたスペースで締結が必要な場合や、特定の美観を求める場面で利用されます。この記事では、低頭ボルトと極低頭ボルトの寸法、特徴、選定ポイントについて解説します。
低頭ボルトと極低頭ボルトと座グリ穴の寸法表
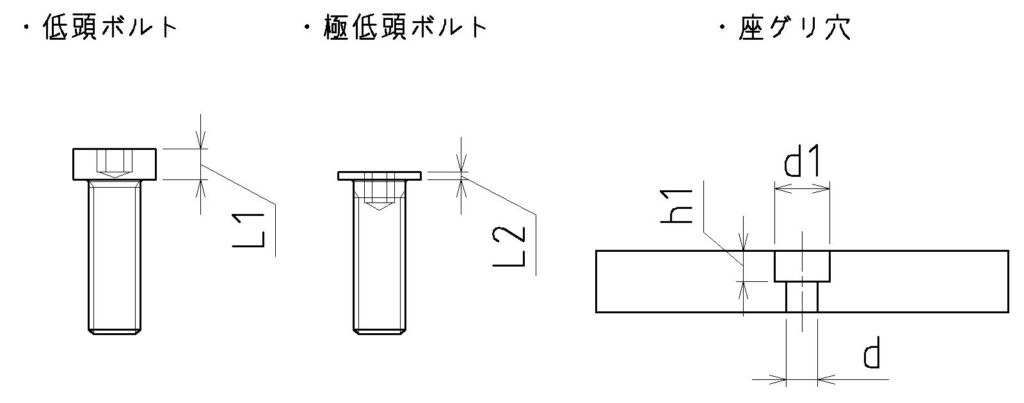
呼び径 | 低頭ボルト | 極低頭ボルト | 通し穴径(d) | 座グリ径(d1) | ||
L1 | h1 | L2 | h1 | |||
M3 | 2 | 2.5 | 1.3 | 2 | 3.4 | 6.5 |
M4 | 2.8 | 3.5 | 1.5 | 2 | 4.5 | 8 |
M5 | 3.5 | 4 | 1.5 | 2 | 5.5 | 9.5 |
M6 | 4 | 4.5 | 1.5 | 2 | 6.6 | 11 |
M8 | 5 | 5.5 | 1.5 | 2 | 9 | 14 |
M10 | 6 | 6.5 | 1.5 | 2 | 11 | 17.5 |
M12 | 7 | 7.5 | – | – | 14 | 20 |
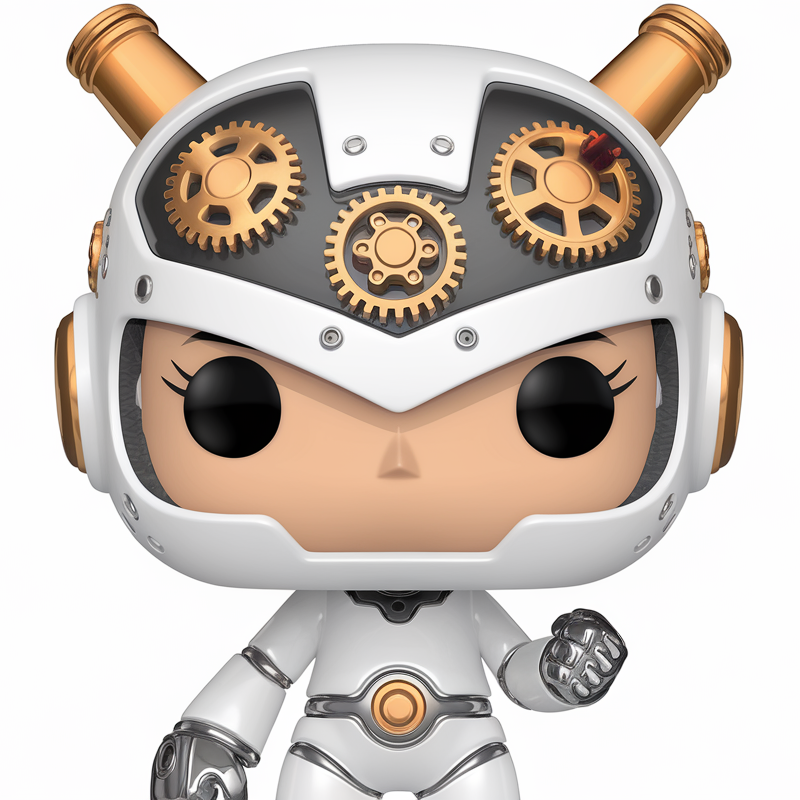
上記の表はわたしが普段使用している一般的な寸法になります。
適材適所により、寸法を調整します。
✅ ねじの通し穴・座グリ穴・皿穴の寸法表は下記をチェック!
低頭ボルトの特徴
低頭ボルトは、通常のボルトに比べて頭部の高さが低く設計されたボルトです。機械設計では、部品間のクリアランスが限られている場所や、突出部分を最小限に抑えたい場面で利用されます。低頭ボルトは、通常の六角ボルトよりも高さを抑えながらも比較的高い強度を持つため、狭い空間での使用に適しています。
✅ 低頭ボルトの利点
- スペース節約: 頭部の高さが低いため、限られたスペースに収まる。
- 美観向上: 機械部品の外観を整え、目立たない仕上がりを実現。
- 強度と機能のバランス: 通常のボルトに比べ頭部が薄いものの、強度は保持される。
極低頭ボルトの特徴
極低頭ボルトは、さらに頭部の高さが低く設計されたボルトで、低頭ボルトよりもさらにスペースを節約したい場合に使われます。頭部が非常に薄いため、強度がある程度制限されるものの、突出部分を最小限にしたい場面での使用が適しています。特に、超小型デバイスや精密機械で多く使用されます。
✅ 極低頭ボルトの利点
- 超薄型設計: 非常に狭いクリアランスでの使用が可能。
- 軽量化: 頭部が薄いため、全体の重量を減らすことができる。
- 設計の自由度向上: 極限までスペースを節約することで、他の部品の設計が柔軟になる。
選定ポイント
低頭ボルトや極低頭ボルトを選定する際には、以下のポイントに注意する必要があります。
クリアランスの確認
- 設計した機械の中で、ボルトが突出しないよう十分なクリアランスがあるかを確認することが重要です。
- 極限まで低くする場合は、極低頭ボルトが適していますが、強度も考慮する必要があります。
強度要件
- 低頭ボルトや極低頭ボルトは、頭部の高さを抑えた分、通常のボルトに比べて強度が低くなります。
- 締結する部品や場所に応じて、必要な強度を満たしているか確認することが重要です。
表面仕上げと素材
- ボルトの素材や表面処理は、使用環境や耐腐食性を考慮して選定します。
- ステンレス製の低頭ボルトは耐食性が高く、湿気の多い環境での使用に適しています。
使用環境
- 極低頭ボルトは、軽量化や美観を重視したい場面で特に有効ですが、強度に妥協があるため、高負荷がかかる部分には向きません。
- 振動や衝撃が加わる環境では、強度を優先して選定する必要があります。
低頭ボルト・極低頭ボルトと皿ねじの使い分け
ボルトやねじは、機械設計において部品の固定や機能の維持に不可欠な要素です。その中でも、(極)低頭ボルトと皿ねじは、設計スペースや用途に応じて使い分けが求められるねじです。本項では、それぞれの特徴と使い分けのポイントについて解説します。
低頭ボルト・極低頭ボルトとは?
低頭ボルトは、頭部の高さが通常の六角ボルトよりも低く設計されたボルトです。さらに薄いものは極低頭ボルトと呼ばれ、限られたスペースでの使用に適しています。
✅ 特徴
- 頭部の高さが低く、スペースの節約が可能。
- 頭部が機械部品や構造体から飛び出さず、邪魔にならない。
- 六角穴付きが一般的で、工具を使用して締結する。
📌 使用例
- スペースが限られる箇所(例:小型機器や精密機器)。
- 部品が可動する箇所での干渉を避けたい場合。
- 外観をスッキリさせたい設計。
皿ねじとは?
皿ねじは、頭部が円錐状になっており、ねじ込むと部材表面とフラットになる形状のねじです。
✅ 特徴
- 頭部が部材の表面に埋まり、フラットな仕上がりになる。
- 見た目が美しいため、外観が重視される設計に適している。
- 締結面が広いため、ねじの頭が部材にめり込みにくい(専用の皿座面を加工した場合)。
📌 使用例
- 外観が重視される箇所(例:家電製品、家具、車両の内装部品)。
- 部材の表面に突起を残したくない箇所。
- 高速で移動する機械部品の表面(突起が空気抵抗や干渉を生じる場合)。
使い分けのポイント
項目 | (極)低頭ボルト | 皿ねじ |
---|---|---|
外観 | 頭部は薄いが突起が残る(座グリ加工を行えば完全に埋めることも可能) | 頭部が部材表面とフラットになる |
スペース | 狭いスペースで使用可能だが、頭部の高さはゼロにはならない | 完全に埋まるため、表面スペースを最大限活用可能 |
加工 | 部材に追加加工(座グリ)が必要な場合もある | 皿座面の加工が必要 |
締結強度 | 六角穴の形状によりトルクをかけやすい | 面積が広い分、引き抜きに強い場合が多い |
用途例 | 可動部品の固定、外観が気にならない場所 | 見た目重視の箇所やフラットな表面が求められる場所 |
注意点と設計のコツ
🚫 (極)低頭ボルトの注意点
- 頭部が薄いため、締め付けトルクが過剰になると工具がねじ穴を破損する可能性があります。
- トルク管理を適切に行うことが重要です。
- 締結面積が小さいため、大きな負荷をかける設計には不向きです。
🚫 皿ねじの注意点
- 部材に皿座面の加工が必要なため、加工コストが増加します。
- 部材が薄い場合、座面加工によって強度が低下する可能性があります。
📌 選定のコツ
- 部材の強度やスペース、コストを総合的に考慮し、どちらを採用するか決定します。
- 必要な締結強度に応じて、適切なサイズや材質を選びます。
📌 (極)低頭ボルトの座グリ加工
- 座グリ加工を行うことで、(極)低頭ボルトの頭部を部材表面とフラットにできます。
- この方法は、部材の厚みに余裕がある場合や、皿ねじを使用できない設計条件で有効です。
🔍選択時の検討
- 座グリ加工のコストと加工精度を考慮し、低頭ボルトを完全に埋める必要性が高い場合には皿ねじと比較して最適な選択を行いましょう。
(極)低頭ボルトと皿ねじは、それぞれ異なる特徴を持つ締結部品です。設計の目的や要求事項を明確にし、最適なねじを選定することで、製品の性能や外観を向上させることができます。正しい使い分けを行い、効率的で高品質な設計を実現しましょう。
まとめ
低頭ボルトと極低頭ボルトは、機械設計において限られたスペースや美観を重視した設計において非常に有効な締結部品です。頭部の高さが低いため、突出部分を最小限に抑え、コンパクトな設計が可能となります。しかし、強度やクリアランスなどの要素を十分に考慮し、使用箇所に最適なボルトを選定することが重要です。適切な選定によって、機械の性能や耐久性を保ちながら、空間の有効活用や美観の向上を図ることができます。
コメント