機械設計では、ねじ・ボルトは部品同士を確実に締結するために欠かせない要素 です。しかし、適切なねじを選定しなければ、強度不足や緩み、組立不良などの問題が発生する可能性があります。
本記事では、ねじの種類や強度、設計時に考慮すべきポイントを分かりやすく解説 し、適切なねじ選定ができるようにまとめました。各項目の詳細については、リンク先の記事で詳しく解説していますので、ぜひ参考にしてください。
ねじ・ボルトは“なくてはならない存在”
私たちの身の回りにある機械や装置、たとえば自動車、ロボット、冷蔵庫、コピー機、工場の生産設備――それらが「きちんと組み立てられ、正しく動く」のは何のおかげでしょうか?
それを実現しているのが、実は「ねじ」や「ボルト」といった小さな部品なのです。
小さいけれど機械を支える“縁の下の力持ち”
ねじやボルトは、機械の部品と部品をしっかりつなぎ止める「締結部品」です。
- フレームとカバーを固定する
- モーターとシャフトをつなぐ
- 装置の土台をしっかり支える
このように、機械の構造をしっかりと安定させ、ガタつかず、安全に動作させるために不可欠な存在です。
言い換えれば、ねじやボルトがなければ、機械はバラバラになってしまい、正しく動くことすらできません。
簡単に“組み立て”も“分解”もできる便利な仕組み
ねじやボルトの最大の特長は「取り外しができる」ことです。
- 組み立てがしやすい
- 故障時に分解・修理できる
- パーツの交換が簡単にできる
つまり、「分解できる=メンテナンスがしやすい」ということ。設計者にとって、作りやすさ・直しやすさは非常に大切な視点であり、ねじ・ボルトはそのカギを握っているのです。
安全と信頼性を守る“見えない安全装置”
ボルトやねじの締結がゆるんでしまうと、最悪の場合、部品が外れて大事故につながる可能性もあります。
だからこそ、正しく選定し、正しいトルクで締めることが求められます。
- 締めすぎると壊れる
- 緩すぎると外れる
- 振動対策として緩み止め(スプリングワッシャ、ロックナットなど)が必要な場合もある
「ねじは締めればいい」ではなく、「適切に締める」ことが設計の大切なポイントなのです。
ねじ1本が機械全体の品質を左右することも
「そんなに大事なの?」と思うかもしれませんが、実際に工場の現場ではねじ1本の選定ミスが、機械の不具合や故障につながることがあります。
- 材質の違いで腐食する
- 締め付けトルクが足りずにゆるむ
- 摩耗して強度が落ちる
このように、ねじやボルトは単なる“部品のつなぎ役”ではなく、機械の性能・信頼性・寿命を左右するキーパーツなのです。
ねじ・ボルトなしでは、機械は“完成しない”
✔ 機械を組み立て、構造を支える
✔ メンテナンス性を高める
✔ 安全・信頼性を保つ
✔ 小さくても、設計上とても重要な存在
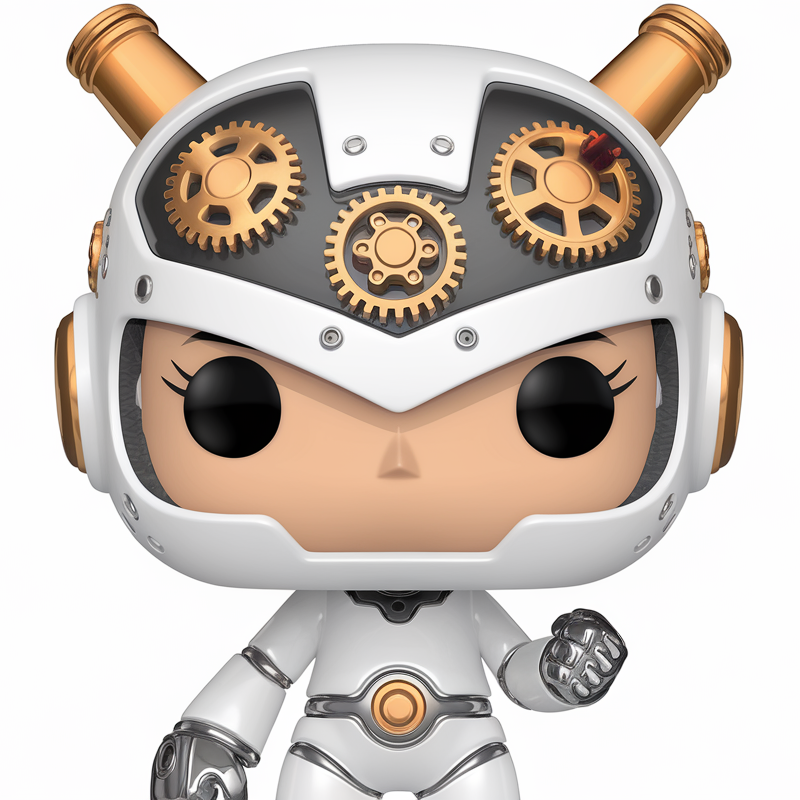
ねじやボルトは、目立たないけれど、まさに“機械の命綱”とも言える存在です。初心者の方こそ、「どのねじを、どこに、どう使うか」という視点を持つことが、良い機械設計の第一歩になります。
ねじの種類と選定ポイント
ねじの種類を理解する
まず最初に、ねじの基本的な種類を知ることが重要です。ねじには以下のようなものがあります。
✅ 六角ボルト:最も一般的な締結用ねじ
✅ 六角穴付きボルト(キャップボルト):工具が不要な側にスペースが必要な場合に適用
✅ 皿ねじ:表面をフラットに仕上げたい場合に使用
✅ タッピングねじ:タップなしで直接ねじ込める
用途に応じたねじを選定することで、適切な締結設計が可能 になります。
ねじのサイズを理解する
ねじを正しく選定するためには、ねじのサイズ(径・長さ)についての理解が欠かせません。
適切なサイズを選ぶことで、締結の強度と作業性のバランスが取れた設計が可能になります。
✅ ねじ径(呼び径)
- ねじの太さを表し、M4・M6・M8などの「M+数字」で表記されます。
- 数値が大きいほど太く、引張強度も高くなります。
✅ ねじ長さ(首下長さ)
- 締結される部品の厚み+ナット厚み+ワッシャー厚み+かかり代を考慮して決定します。
- 一般に、「ねじの有効ねじ込み長さはボルト径の1〜1.5倍以上」が目安とされています。
🚫 サイズ選定時の注意点
✔ 材料の強度と安全率も合わせて検討する
✔ 使用荷重を考慮して、過小なねじ径を避ける
✔ タップ穴の深さとボルトの長さのバランスを確認する
✔ 座面形状(皿、丸、フランジ)によって必要な長さが変わる
材質と表面処理の選定
✅鋼鉄製のねじ
引張強度やせん断強度が高く、一般的な使用に適している。
例) SCM435やS45Cなど
✅ステンレス製のねじ
耐食性が高く、腐食環境での使用に適している
✅特殊材質のねじ
アルミやチタンなど、軽量化や特殊な環境に合わせた材質選定
✅ユニクロメッキ
長期的な耐食性が要求される場合に有効
✅黒染め処理
主に見た目や軽度の防錆を目的とする場合
✅無電解ニッケルメッキ
高精度で腐食環境に適した表面処理
ねじの並目と細目の違い
ねじには並目ねじ(標準ピッチ)と細目ねじ(ピッチが小さい)があり、それぞれ異なる特徴があります。
🔹 並目ねじ:標準的なピッチで、一般的な締結部品に使用
🔹 細目ねじ:ピッチが小さく、緩みにくい・高い締結力が必要な場合 に使用
細目ねじは緩みにくいが、タップ加工や強度計算の考慮が必要 になります。
全ねじと半ねじの違い
ねじには全ねじ(シャンク全体にねじが切られている)と半ねじ(一部だけねじが切られている)があり、それぞれ異なる特徴があります。
🔹 全ねじ:ねじ部が軸全体にあり、汎用性が高く部品の長さ調整や多用途に適用
🔹 半ねじ:ねじ部が先端のみにあり、位置決めやせん断荷重に強く、ガタつきが少ない用途に使用
半ねじは精度と強度を両立できる反面、必要なねじ込み長さや軸長を考慮した設計が重要になります。
右ねじと左ねじの違い
ねじには右ねじ(時計回りで締まる)と左ねじ(反時計回りで締まる)があり、それぞれ異なる特徴があります。
🔹 右ねじ
- 最も一般的なねじで、時計回りに回すと締まる。
- 大半のねじ製品で使用されており、入手性や作業性に優れる。
🔹 左ねじ
- 反時計回りで締まる特殊なねじ。
- 回転体の逆回転による緩みを防止したい場合や、対称機構に用いられる。
左ねじは逆回転によるゆるみ防止や特殊用途に適している反面、加工や調達に注意が必要で、タップも左ねじ用を使う必要があります。設計時には回転方向や緩みのリスクに応じて使い分けることが重要です。
ミリねじとインチねじの違い
ねじにはミリねじ(メートルねじ)とインチねじがあり、それぞれ異なる単位系と規格を持っています。
🔹 ミリねじ
- 国際的に最も広く使用されているメートル単位のねじ。
- 日本を含む多くの国の機械や製品で採用されており、JIS(日本工業規格)やISO規格に準拠。
- ピッチ(ねじ山の間隔)がミリ単位で指定され、設計・加工・入手性に優れる。
🔹 インチねじ
- インチ(inch)を基準としたねじで、アメリカやイギリス、カナダなどの機械でよく使用される。
- ユニファイねじやウィットねじなどの規格があり、ピッチは「山数/1インチ」で表される。
- 日本国内でも古い輸入機械や特定の業界では今でも使用されることがある。
インチねじは特殊な用途や輸入機械に多く、測定や工具の選定にも注意が必要です。設計段階でねじの単位系を確認し、混在を避けることがトラブル防止の鍵となります。
コストと入手性
🔹標準品か特注品か
標準的なねじで対応可能か、特殊なねじが必要か
🔹コストパフォーマンス
必要な性能に対して、最適なコストを確保する
ねじの取付穴と締結方法
ねじの取付穴の設計
設計時には、ボルトが通る穴(通し穴)や、ボルトの頭を収める穴(座グリ穴)を適切に設計する必要があります。
✅ 通し穴の直径 を適切に設定することで、ボルトのスムーズな挿入が可能
✅ 座グリ穴を設計することで、ボルトの頭が邪魔にならないようにできる
✅ 工具のアクセススペースを確保 し、組立性を向上
低頭ボルト・極低頭ボルトの活用
🔹 低頭ボルト は、標準ボルトより頭が低く、スペースが限られる場所で有効
🔹 極低頭ボルト はさらに頭が低く、極めて狭いスペースで使用可能
設計時に工具スペースが確保できない場合 や、干渉を避ける必要がある場合 に有効活用できます。
貫通ねじ穴と非貫通ねじ穴
ねじを設計する際、「貫通ねじ穴」と「非貫通(止まり)ねじ穴」のどちらを採用するかは、加工性と機能面のバランスを考慮することが重要です。
✅ 貫通ねじ穴は加工が容易でコストを抑えやすい
✅ 止まりねじ穴は背面の気密性やデザイン上の制限がある場合に有効
貫通ねじ穴は、タップ加工時に切りくずが逃げやすく、工具破損のリスクが低いため加工が簡単で安定した品質を確保しやすいのがメリットです。特に量産や小径ねじでは貫通設計が推奨されます。
一方で、裏面に抜けてほしくない設計や、水・気体などの漏れを防ぎたい用途では止まり穴を採用せざるを得ない場面もあります。その場合は、下穴の深さに余裕を持たせる、切りくず排出性を考慮するなどの設計工夫が必要です。
設計段階で「貫通にできないか?」をまず検討することが、加工トラブルの回避とコストダウンにつながります。
ねじインサートでねじ穴を補強する
アルミや樹脂などの低強度材料 にねじを切る場合、ねじインサート(ヘリサート)を使用することで耐久性を向上 させられます。
✅ 繰り返しの脱着でもねじが摩耗しにくい
✅ 高負荷がかかるねじ穴の補強が可能
ねじインサートを活用することで、締結部の耐久性を高めることができます。
だるま穴の設計
設計時には、だるま穴を適切に設計することで、部品の取付・取外しのしやすさや、位置調整の自由度を確保することができます。
✅ だるま穴の小穴側は、ボルトがスムーズに挿入できる直径に設定する
✅ だるま穴の大穴側を広げることで、ボルトの頭を通過させ、部品をスライド脱着できる
✅ スライド方向に合わせた穴形状と、ボルト締結後の安定性を考慮して設計する
だるま穴をうまく活用することで、組立作業の効率化やメンテナンス性の向上が期待できます。
ねじ・ボルトの締結工具を考慮する
🔹 設計時に適切な工具を考慮しないと、ボルトを締められない場合がある
🔹 狭いスペースではショートヘッド六角レンチやエクステンションバーを活用
🔹 トルク管理が必要な箇所ではトルクレンチを使用
工具の選定とスペース確保が、組立性とメンテナンス性に直結 します。
おねじの逃がし加工を設計に取り入れる
🔹 おねじの端部に逃がし加工がないと、めねじと干渉して最後まで締め込めないことがある
🔹 加工工具には逃げが必要なため、ねじの端部に段差やR加工を設けるのが一般的
🔹 逃がしを設けることで、ねじ山が不完全になる部分を回避し、確実な締結が可能になる
逃がし加工の有無は、組立性だけでなく、ねじの精度・強度・トラブル防止にも直結します。
用途や荷重条件に応じて、適切な形状を設計しましょう。
ねじの強度と計算
ねじの強度区分を理解する
ボルトには強度区分 があり、用途に応じて適切なものを選定する必要があります。
🔹 4.8(一般的な低強度ボルト)
🔹 8.8(機械部品に多く使用)
🔹 10.9・12.9(高強度ボルトで締結力が必要な場合に使用)
用途に適した強度のボルトを選定することが重要 です。
ねじの強度計算
ボルトが十分な強度を持つかどうかを評価するために、強度計算 を行います。
✅ 引張強度計算:ボルトがどのくらいの引張荷重に耐えられるかを計算
✅ せん断強度計算:せん断荷重を考慮した強度計算
強度計算を行うことで、適切なボルトサイズ・材質を選定 できます。
引張荷重とせん断荷重の考え方
ボルトには引張荷重とせん断荷重 がかかる場合があり、適切な設計が求められます。
🔹 引張荷重:ボルトが引っ張られる力
🔹 せん断荷重:ボルトが横方向にずれる力
どの力が支配的になるかを考慮して、ボルトの強度を決定 する必要があります。
ねじ山のかかり代の確保
🔹 ねじ山のかかりが不足すると、締結力が弱くなる
🔹 十分なかかり代(1.2〜1.5倍のねじ径)が確保されているかを設計時に確認
適切なかかり代を確保することで、締結力の安定性を向上 させることができます。
ねじの使用環境と対策
摩擦や振動への対策
🔹緩み止め機構の検討
ワッシャー、ロックナット、ロックタイトなどを使用し、振動での緩みを防ぐ。
温度や環境条件
🔹高温や低温での使用
ねじが使用される環境の温度範囲に対応できるか
🔹腐食環境への対応
塩水、化学薬品、湿気などの環境に応じた耐食性の確認
ねじのトラブルシューティング
ねじのトラブルは、製品の信頼性や安全性に大きな影響を及ぼすため、原因を把握し、適切に対処することが重要です。
✅ ねじ山の潰れ対策
締付けトルクの過大、タップの精度不足、材質のミスマッチなどが原因です。
👉 適正トルク管理とねじの強度区分の見直しが有効です。
✅ 頭のなめり対策
ドライバーやレンチのサイズ不一致や斜め締めが原因で発生します。
👉 工具の適合確認と、確実な押し付け力での作業がポイントです。
✅ ねじ軸の破断対策
過大な荷重や疲労の蓄積による破断が起こります。
👉 強度計算と余裕のある設計、適切な材質選定が有効です。
✅ ねじの錆び付き対策
湿気・薬品・電食などにより固着します。
👉 防錆処理や潤滑剤の塗布、ステンレス製への置き換えが効果的です。
✅ タップ破損対策
斜め締めや下穴径ミスでタップが壊れるケースがあります。
👉 下穴径の確認と、垂直な締付け作業で防げます。
ねじトラブルを未然に防ぐには、適切な設計・正しい施工・定期点検が欠かせません。トラブルの傾向を知っておくことで、現場対応力が大きく向上します。
ねじを利用した機械要素
ボールねじの選定ポイント
ボールねじは、精密な直線運動を実現するための重要な要素であり、機械の効率や耐久性に大きく影響します。ボールねじの選定においては、以下のポイントを考慮することが重要です。
✅ ねじリード:送り速度や負荷条件に適したリード長を選定
✅ ねじ径:荷重が大きい場合はねじ径を大きくする
✅ 精度等級:C7、C5、C3など、用途に応じたリード精度を考慮
適切なボールねじを選定することで、高精度な直線運動や機械の長寿命化が可能になります。
台形ねじの選定ポイント
台形ねじは、回転運動を直線運動に変換するための重要な要素であり、適切な選定が機械の性能や耐久性に大きく影響します。台形ねじの選定においては、以下のポイントを考慮することが重要です。
✅ ねじリード:送り速度や負荷条件に適したリード長を選定
✅ 材質の選定:S45CやSCM440、SUS304など、強度や耐摩耗性を考慮
✅ ナットの材質:ブロンズやPOM、樹脂など、摺動特性や摩耗特性を考慮
適切な台形ねじを選定することで、確実な直線運動や機械の長寿命化が可能になります。
ストリッパーボルトの特徴
ストリッパーボルトとは、先端に段付きのガイド部(軸部)を持ち、一部だけにねじが切られている特殊なボルトです。主に金型や治具で使われる、「位置決め兼締結用の高精度ボルト」と理解するとよいでしょう。
✅ ストリッパーボルトの構造と特徴
部位 | 概要 |
---|---|
軸部(ガイド部) | 精密な外径(H7相当など)で、穴とのすきまを最小限にし、位置決め機能を果たす。 |
ねじ部 | 通常のボルトのように締結力を発揮する。 |
肩部(段差) | 部品との接触面。座面として荷重を受ける。 |
図面上では、段付きシャフトとねじを組み合わせたような形状をしています。
アジャスタパッドの選定ポイント
アジャスタパッドは、機械や装置の設置時に高さや水平を微調整するための重要な要素であり、安定性や振動対策に大きく影響します。アジャスタパッドの選定においては、以下のポイントを考慮することが重要です。
✅ 荷重条件:設置物の重量に応じて、標準タイプや重荷重タイプを選定します。
✅ 振動の有無:振動のある環境では防振タイプが適しています。
✅ 設置環境:位置を固定する必要がある場合は固定タイプを使用します。
✅ 高さ調整範囲:設置場所の凹凸や高さ調整の必要性を考慮して選定。
✅ レベル出しの重要性:機械設備の性能や安全性を向上させるための基本的な工程
適切なアジャスタパッドを選定することで、機械や装置の安定した設置や振動の低減が可能になります。
アンカーボルトの選定ポイント
アンカーボルトは、機械や設備をコンクリート基礎にしっかりと固定するための重要な要素であり、安全性や耐震性、精度に大きく影響します。アンカーボルトの選定においては、以下のポイントを考慮することが重要です。
✅ 取り付け方法の選定
施工時に使用するアンカーの種類には、「打込み式(メカニカルアンカー)」や「接着式(ケミカルアンカー)」などがあり、施工現場の条件や強度要件に応じて適切な方式を選びます。
✅ ねじのタイプ
取り付け対象によって、「おねじタイプ(オールアンカー)」か「めねじタイプ(グリップアンカー)」を選定。
おねじタイプは取り外し不要の機器に、めねじタイプは取り外し・交換が想定される設備に適しています。
✅ 引抜強度とせん断強度
設置物の重量や使用時に加わる力(振動・衝撃)に耐えられるか、アンカーの性能(引抜強度・せん断強度)を確認して選定します。
✅ 下地の材質と厚み
コンクリートの厚みや状態により、使用できるアンカーの長さや種類が異なります。
穿孔深さにも注意が必要です。
✅ 施工環境と作業性
湿気の多い場所や屋外では、耐食性のあるステンレス製アンカーを選ぶのが望ましく、狭所での施工には施工性の高いアンカーが適しています。
ねじの歴史についての雑学
ねじの大冒険 ~小さな螺旋が世界を動かす物語~
むかしむかし、まだ人類が石を削って道具を作り、縄を結んでものを固定していた時代のこと。ねじというものは、まだこの世に存在していませんでした。世界はもっぱら「叩いて固定する」か「縛ってつなぐ」方法だけで成り立っていたのです。しかし、それでは力加減が難しく、部品がすぐ緩んでしまったり、外れてしまったりして、人々は困り果てていました。
「もっと確実に、しかも楽にものを締結する方法はないものか!」
そう願った瞬間、人類の知恵の火種が灯ったのです。こうして、ねじの冒険が始まることになります。
第一章:アルキメデス、ねじに目覚める
物語の始まりは紀元前250年頃の古代ギリシャ。偉大な発明家アルキメデスは、ある日水を汲み上げる装置の改良を頼まれました。当時は水を運ぶのに桶や壺を何度も往復させるという非効率的な方法が使われていましたが、アルキメデスはこれに飽き飽きしていました。
「これでは効率が悪すぎる!もう少し楽に水を運べないものか?」
アルキメデスはしばし考え、木を削ってらせん状の構造を作り、筒に取り付けるという画期的なアイデアを思いつきます。これが後に「アルキメディアン・スクリュー」として知られる装置です。
「このらせん形状、すごく便利だ!」と村人たちは大喜び。これをきっかけに、人類はらせん形状の魅力に目覚めることになります。
もっとも、この時代のらせん構造は主に水を運ぶための装置として使われており、まだ締結や固定には使われていませんでした。それでも、後のねじの誕生に大きなヒントを与えたのです。
第二章:中世ヨーロッパ、ねじの誕生
アルキメデスの発明から1500年以上が経った中世ヨーロッパ。物語はあるワイン職人の村に移ります。この村では毎年秋になるとぶどうの収穫祭が開かれ、大量のぶどうジュースを絞るのが伝統でした。しかし、その作業はとても力が必要で、村人たちはいつも腕を痛めていました。
「これではぶどうを絞るのに一日がかりだ。なんとかならないものか?」
ある日、ひらめいた若き職人がいました。彼は木製のらせん状の棒を作り、それを圧搾機に取り付けたのです。これにより、少ない力で効率よくぶどうジュースが絞れるようになり、村人たちは大喜びしました。
「これがねじの力か!」と村中に広まり、宴会は夜通し続きました。
ただ、この時代のねじはまだ木製で、耐久性に問題がありました。しばらく使うと摩耗してしまうため、職人たちは「もっと丈夫なねじを作れないものか?」と夢を見るようになりました。
第三章:産業革命、ねじの大躍進
時は18世紀。産業革命が始まり、物語の舞台はイギリスに移ります。蒸気機関の開発で有名なジェームズ・ワットが頭を抱えていました。
「精密な部品を組み立てるのに、ただ叩いて固定するだけでは不十分だ。もっと確実で強力な締結方法が必要だ!」
そんな彼のもとに、ある鍛冶職人がやってきます。その職人は金属製のねじを作り、さらにねじを切るための専用の工具まで開発したのです。
「これなら力が分散されることなく、確実に締結できますよ!」
ジェームズ・ワットはその性能に感激し、自分の蒸気機関に採用しました。この金属製のねじの登場により、産業革命はさらに加速します。さらに、ねじの規格化に貢献したジョセフ・ホイットワースが登場し、ねじの統一規格が生まれることになります。
ホイットワースはこう言いました。
「規格がなければ、世界中で使われるねじが互換性を持たないだろう。それでは無駄が増えるだけだ。統一するのが人類の進むべき道だ!」
こうしてねじは「工業化の立役者」としての地位を確立しました。
第四章:現代と未来のねじ
現代においてねじの進化はとどまることを知りません。ねじはあらゆる産業に使われています。ステンレス製、チタン製、さらには樹脂製のねじまで、用途に応じた多様な素材が選ばれるようになりました。
さらに宇宙時代に突入すると、ねじの活躍は地球を越えます。宇宙ステーションでは、一つのねじの緩みが重大な事故につながる可能性があるため、設計者たちは「緩み防止」や「軽量化」に細心の注意を払います。技術者たちは宇宙用の特殊ねじを開発し、こう言いました。
「ねじ1本が地球と宇宙の未来を支えているんだ!」
そして現在、ねじはIoTや自動化技術と組み合わされ、新たな進化を遂げつつあります。未来では、ねじそのものがセンサー機能を持ち、自らの締結状態をモニタリングする「スマートねじ」も登場するでしょう。
ねじの教訓 ~小さな螺旋がつなぐ大きな世界~
ねじの物語は、私たちに小さな工夫が大きな変化を生むことを教えてくれます。ねじがなければ、私たちの生活は成り立たず、産業も発展しなかったでしょう。この小さな螺旋形状の部品こそ、人類の知恵と創造力の象徴です。
だからこそ、機械設計者の皆さんも、ねじの重要性を心に留め、賢く活用してください。ねじはただの部品ではなく、あらゆるものを支える「小さな英雄」なのです!
さあ、あなたの設計にねじという名の冒険を加えてみませんか?
まとめ
✅ ねじの種類や強度を理解し、適切な選定を行う
✅ 工具のアクセスや作業性を考慮し、締結スペースを確保する
✅ 強度計算を行い、必要な耐荷重を満たすねじを選ぶ
✅ かかり代や緩み対策を考慮し、信頼性の高い締結を実現する
ねじ・ボルトは機械設計において欠かせない要素です。適切な選定を行い、安全で効率的な設計を目指しましょう!
コメント