機械設計において、部品の摩擦や摩耗は避けて通れない課題です。潤滑油やグリースを使用することで摩擦を減らすことは一般的ですが、潤滑剤が使えない環境やメンテナンスが難しい場所では、潤滑を別の方法で確保する必要があります。
本記事では、自己潤滑性材料の特性とその活用ポイントについて詳しく解説し、適切な材料選定のための知識を深めていきます。
自己潤滑性とは?
自己潤滑性とは、外部からの潤滑剤(油やグリース)を使用せずに、材料自体が滑りやすい特性を持つことを指します。特に、摩擦が発生する部品において、潤滑剤なしでスムーズに動作できるため、メンテナンスの軽減や耐久性向上に貢献します。
自己潤滑性が優れている代表的な材料
✅樹脂系材料
✔ PTFE( テフロン)
極めて低い摩擦係数を持ち、耐薬品性にも優れる
✔ MCナイロン・POM(ポリアセタール)
強度・耐摩耗性が高く、機械部品に多用される
✔ PEEK(ポリエーテルエーテルケトン)
高耐熱性・耐摩耗性を持ち、過酷な環境下で使用される
✅ 金属系材料
✔ 含油軸受(オイルインプリーグブッシュ)
金属内部にオイルを含ませ、摩擦時に自動的に潤滑
✔ MoS₂(モリブデンジスルフィド)やグラファイト(黒鉛)を含む材料
金属や樹脂に添加することで、潤滑性を向上させる
自己潤滑性において金属材料より樹脂材料の方が優れていることが多い理由とは?
機械設計では、部品同士の摩擦を抑えることが重要です。一般的に金属は硬くて丈夫なため、多くの機械部品に使用されますが、摩擦を減らすためにはグリースやオイルなどの潤滑剤が必要になることがほとんどです。一方、樹脂材料の中には自己潤滑性を持つものがあり、潤滑剤なしでも滑らかに動くことができるという特徴があります。
では、なぜ樹脂材料の方が自己潤滑性に優れていることが多いのでしょうか?今回は、その理由をわかりやすく解説します。
樹脂は分子レベルで滑りやすい特性を持つ
樹脂の中には、分子自体が滑りやすい構造を持つものがあり、これが摩擦を低減する働きをします。例えば、PTFE(ポリテトラフルオロエチレン、通称「テフロン」)やPOM(ポリアセタール)は、表面が滑らかで摩擦係数が低いため、金属に比べてスムーズに動作します。
金属の場合、表面がどれだけ滑らかに見えても微細な凹凸が存在し、摺動(しゅうどう、滑る動き)の際に引っかかりやすくなります。そのため、潤滑剤なしでは摩擦が大きくなり、摩耗しやすいのです。
樹脂は柔軟性があり、相手材を傷つけにくい
金属同士が直接擦れ合うと、硬いもの同士なので摩耗が発生しやすく、長期間使用すると表面が削れてしまいます。しかし、樹脂は適度に弾性(しなやかさ)を持っているため、相手材との接触面に馴染みやすく、傷つきにくいという利点があります。
特に、アルミや真鍮(しんちゅう)などの比較的柔らかい金属部品と組み合わせる場合、樹脂の方が適しています。金属同士の摺動では硬い方が柔らかい方を削ってしまうことがありますが、樹脂ならそのリスクを減らせます。
軽量でエネルギー消費を抑えられる
樹脂は金属に比べて圧倒的に軽量です。そのため、摺動部品に使用すると、負荷が減り、モーターなどの駆動部のエネルギー消費を抑えることができます。
例えば、金属製のスライド部品と樹脂製のスライド部品では、樹脂の方が軽いため動かすための力が小さくて済みます。これにより、摩擦抵抗の低減だけでなく、機械の省エネルギー化にもつながるのです。
✅ 分子レベルで滑りやすい構造を持つため、摩擦が低い
✅ 柔軟性があり、相手材を傷つけにくい
✅ 自己潤滑成分を内部に含むことができ、潤滑効果が持続する
✅ 軽量なため、エネルギー消費を抑えられる
このような理由から、自己潤滑性が求められる場面では金属よりも樹脂材料の方が適していることが多いのです。ただし、樹脂は金属に比べて強度や耐熱性が劣ることがあるため、用途に応じた適切な材料選定が必要になります。
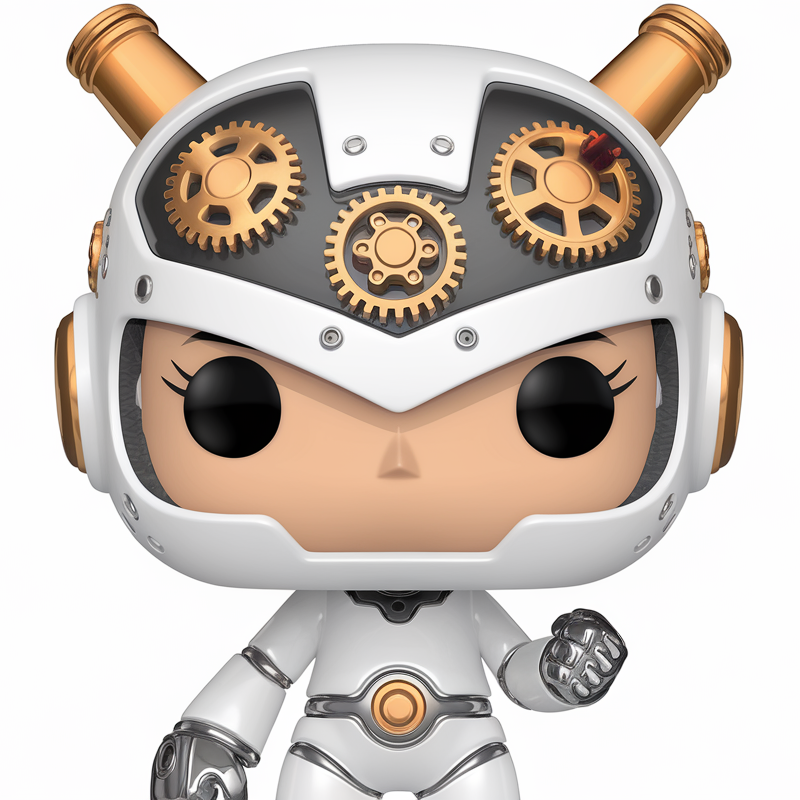
機械設計では、部品がどのような環境で使われるかを考慮しながら、金属と樹脂の特性をうまく使い分けることが重要です!
耐摩耗性について:摺動性と硬度の関係をわかりやすく解説!
機械設計では、「部品の摩耗をいかに抑えるか」が重要なポイントになります。特に、動く部品(摺動部品)では、摩耗によって寿命が短くなったり、性能が低下したりすることがあります。
では、摩耗を抑えるためには何が必要でしょうか?多くの人が「硬い材料なら摩耗しにくい」と考えがちですが、実は「硬度」だけでなく「摺動性(滑りやすさ)」も大きく影響します。
本項では、耐摩耗性を向上させるための「摺動性」と「硬度」の関係を、わかりやすく解説します!
硬い材料は本当に摩耗しにくいのか?
確かに、材料の硬度(硬さ)は耐摩耗性に大きく影響します。 一般的に、硬い材料ほど摩耗しにくく、長寿命になる傾向があります。
🔍例えば、以下のような例があります。
✅ S45C(炭素鋼)よりもSKD11(工具鋼)の方が摩耗しにくい
✅ アルミよりも焼入れした鋼の方が長持ちする
これは、硬い材料ほど「相手に削られにくい」ためです。柔らかい材料は、相手の表面に押し付けられると簡単に変形して削れてしまうため、摩耗が早く進みます。
しかし、硬ければ硬いほど良いというわけではありません。実際には、硬度が高すぎると逆に問題が生じることもあります。
硬すぎる材料の落とし穴:相手を削ってしまう
硬い材料は摩耗しにくいですが、相手の材料を削ってしまうことがあります。
🔍例えば、以下のようなケースが考えられます。
❌ 硬い金属同士を摺動させると、片方が削れたり、摩擦が増えてしまう
❌ ボールネジのナットを焼入れ鋼にすると、ネジが早く摩耗する
このような問題を防ぐために、適度な硬度差をつけることが重要です。例えば、シャフトと軸受けの組み合わせでは、硬いシャフトに対して軸受け側を少し柔らかい材料(青銅や樹脂など)にすることで、片方だけが適度に摩耗して全体の寿命を延ばす工夫がされています。
硬度だけでなく「摺動性」も重要!
硬度が高くても、表面がザラザラしていると摩擦が大きくなり、結果的に摩耗しやすくなります。そのため、「摺動性(滑りやすさ)」も非常に重要です。
例えば、以下のような材料は摺動性が良く、耐摩耗性に優れています。
✅ PTFE(テフロン):超低摩擦で自己潤滑性があり、摩耗しにくい
✅ POM(ポリアセタール):滑りが良く、金属の代替として使われることが多い
✅ 表面処理(DLCコーティング、ハードクロムメッキ):滑らかな表面を作り、摩擦を低減する
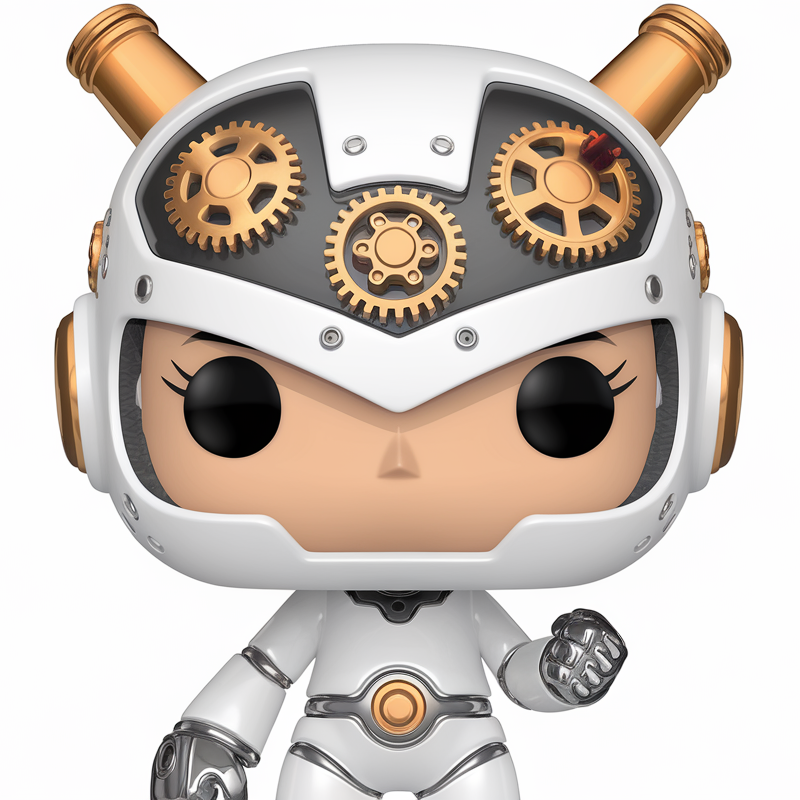
金属部品に潤滑コーティングを施すことで、摩擦を減らし、摩耗を防ぐことができます。
耐摩耗性を向上させるための材料選定のポイント
耐摩耗性を高めるには、以下の3つのポイントを意識すると良いでしょう。
硬度を上げる(ただし、相手材とのバランスが重要)
硬度の高い材料は基本的に摩耗しにくいですが、相手材も考慮しないと逆に削ってしまうことがあります。組み合わせのバランスが大切です。
🔹 例:SUS304(ステンレス) vs. PEEK(樹脂) → 樹脂側が少し摩耗することで寿命が延びる
🔹 例:ハードクロムメッキ vs. 無給油ブッシュ → ブッシュ側が適度に摩耗して長寿命
摺動性の高い材料を選ぶ(自己潤滑性があると◎)
自己潤滑性のある材料を使用すると、摩擦が減り、摩耗しにくくなります。特に樹脂系の材料は摺動性が良く、金属の代替として優れています。
🔹 例:PTFE(テフロン)、POM(ポリアセタール)、PEEK(スーパーエンジニアリングプラスチック)
🔹 例:無給油ブッシュ → 軸受本体に潤滑油を含浸、または個体潤滑剤を埋め込まれている。
潤滑剤やコーティングを活用する
摺動性を向上させるために、潤滑剤やコーティングを活用するのも有効です。
🔹 オイルやグリースを塗る(ただし、メンテナンスが必要)
🔹 DLCコーティングやテフロン加工で表面を滑らかにする
特に、メンテナンスフリーの環境では自己潤滑性のある樹脂材料やコーティングが有効です。
硬度と摺動性のバランスが重要!
材料の耐摩耗性を考えるとき、硬いだけでは不十分で、「摺動性(滑りやすさ)」も考慮することが大切です。
✅ 硬度が高いと摩耗しにくいが、相手材を削るリスクがある
✅ 摺動性の良い材料(PTFE、POM、DLCコーティングなど)は摩擦を減らし、摩耗を抑える
✅ 硬度と摺動性のバランスを取ることで、部品の寿命を延ばすことができる
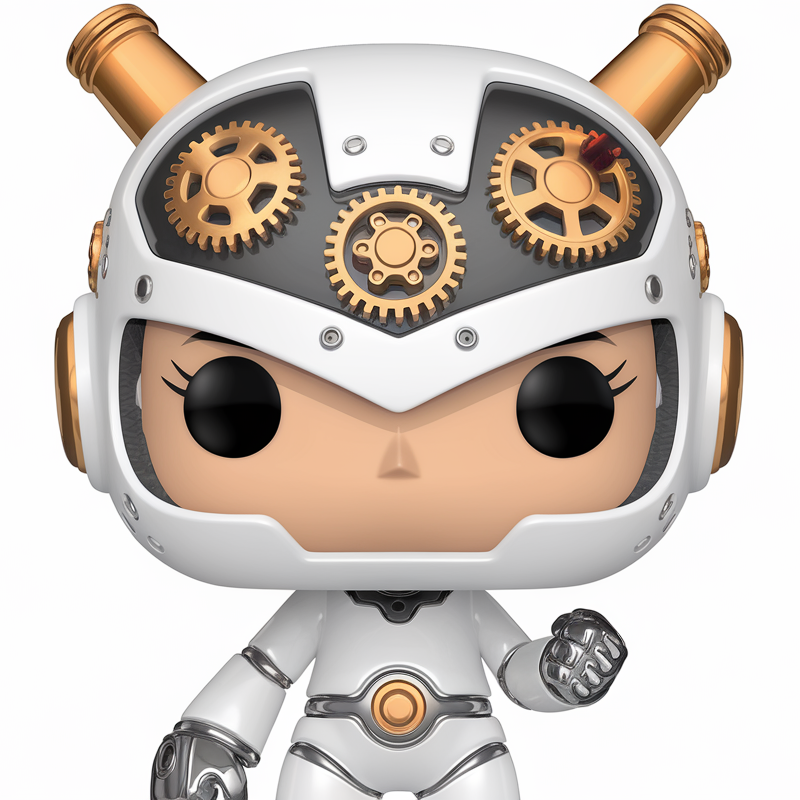
機械設計では、「ただ硬い材料を選ぶ」のではなく、摺動相手や使用環境を考えて最適な材料を選ぶことが重要です。
これから材料を選ぶ際は、「硬度」と「摺動性」のバランスをしっかりチェックしてみてください!
自己潤滑性材料の活用ポイント
1️⃣ メンテナンスフリーが求められる箇所に最適
👉 グリースやオイルを定期的に塗布することが難しい箇所(密閉部品、医療機器など)に適用されます。
2️⃣ 潤滑剤が使用できない環境でも活躍
👉 食品・医療分野では潤滑油が混入すると問題になるため、自己潤滑性材料が重宝されます。
3️⃣ 耐久性の向上とコスト削減
👉 長期間潤滑剤なしで使用できるため、保守コストやダウンタイムの削減に貢献します。
4️⃣ 摩擦による発熱や摩耗の低減
👉 高速回転や摺動(スライド)部品において、摩擦熱を抑えて長寿命化が期待できます。
自己潤滑性材料の選定時の注意点
🚫 荷重や温度条件の確認
PEEKやPTFEは耐熱性に優れますが、POMは高温環境では特性が低下するため、使用環境を考慮する必要があります。
🚫 コストと加工性のバランス
PEEKなどの高性能樹脂はコストが高いため、用途に応じて最適な材料を選定することが重要です。
🚫 摺動相手との相性
相手材が金属・樹脂・ゴムなど異なると、摩耗の進行速度が変わるため、適切な組み合わせを検討する必要があります。
摺動相手との相性とは?
摺動相手との相性が重要な理由
自己潤滑性材料を選ぶとき、摺動(しゅうどう)、つまりこすれ合う相手の材料との相性を考えることが非常に重要です。
相性が悪いと、以下のような問題が発生します。
✅ 摩耗が早まる → 材料がすぐにすり減り、寿命が短くなる
✅ 摩擦が大きくなる → 動きがスムーズでなくなり、エネルギーロスが増える
✅ 異音が発生する → 「ギーギー」「キーキー」といった音がする
✅ 焼き付きが起こる → 摩擦熱がこもり、材料が変形したり破損したりする
例えば、靴と床を考えてみましょう。
- フローリングの床ではスリッパがスムーズに滑るが、
- ゴム製の靴底だと摩擦が大きくなり、キュッと音が鳴る
同じように、機械部品でも摺動相手の材料を間違えると、スムーズな動作ができなくなるのです。
摺動相手との相性を考えた設計のポイント
材料の硬さを考える
硬すぎる材料同士を組み合わせると、一方が削れやすくなるため注意が必要です。
例えば、金属と金属の組み合わせは摩耗しやすく、異音が発生することがあります。
🔍解決策: 片方を樹脂にすることで、適度に摩耗をコントロールできる
摩擦係数を考える
摩擦係数が低すぎると、部品が滑りすぎて制御が難しくなることがあります。
例えば、PTFEは非常に滑りやすいため、固定するためのストッパーやガイドを設ける必要があります。
🔍解決策: 適度な摩擦が必要な場合は、POMや含油軸受を使う
使用環境を考慮する
- 水中で使う場合: 水に強い材料(POM、PEEK、PTFE)を選ぶ
- 高温環境: 耐熱性の高いPEEKやセラミックを使用する
- 粉塵が多い環境: 油を使わなくても滑る自己潤滑性材料を選ぶ
📌 摺動相手の材質と環境を考え、最適な材料を選ぶことが重要!
自己潤滑性材料は、適切な摺動相手を選ばないと、摩耗が早まったり、異音が発生したりする可能性があります。
✅硬さのバランスを考える
✅摩擦係数を適切に選ぶ
✅使用環境に合わせた材料を選定する
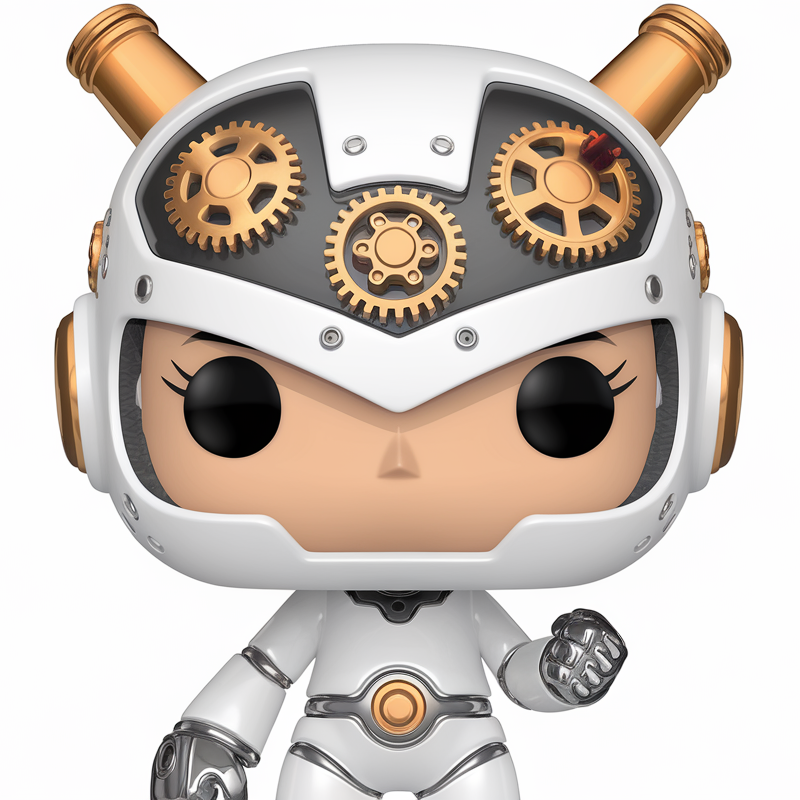
これらのポイントを押さえて、長寿命でメンテナンスの少ない設計を目指しましょう!
まとめ
自己潤滑性材料は、外部からの潤滑剤を必要とせず、摩擦の低減・耐摩耗性の向上を実現できるため、多くの分野で活用されています。特に、潤滑油の使用が難しい環境や長期間のメンテナンスフリーが求められる機械部品には最適です。
ただし、自己潤滑性材料を使用する際には、以下のポイントに注意する必要があります。
✅ 使用環境に適した材料を選ぶ(高温、湿度、薬品との相性など)
✅ 摺動相手の材質との適合性を考慮する(摩擦係数や摩耗の影響)
✅ 必要な強度・耐久性を確保する(荷重や速度に応じた選定)
自己潤滑性材料は万能ではなく、適材適所での選定が重要です。用途に応じた適切な材料を選び、より効率的で長寿命な機械設計を実現しましょう。
コメント