機械部品の強度や耐久性を高める方法のひとつに「焼入れ」があります。その中でも、部品全体を均一に硬くする代表的な処理が「全体焼入れ」です。別名「ズブ焼入れ」とも呼ばれ、古くから多くの産業機械部品に使用されている基本的な熱処理方法です。
この記事では、初心者の方にもわかるように、全体焼入れの仕組み、特徴、適した用途、注意点について解説します。
全体焼入れ(ズブ焼入れ)とは?
全体焼入れとは、金属部品全体を加熱し、その後急冷して材料全体の硬度を高める処理です。
処理の流れ
- 部品全体を焼入れ温度(800〜900℃程度)まで加熱
- 十分に加熱されたら、一気に冷却(油や水に浸す)
- 必要に応じて、焼戻しで靱性(粘り強さ)を調整
この加熱と急冷によって、鋼の組織が「マルテンサイト」という硬くて脆い状態に変化し、硬度と耐摩耗性が飛躍的に向上します。
「ズブ焼入れ」という呼び方の由来
「ズブ焼入れ」という言葉は、部品全体を“ズブン”と液に浸けることから来ています。※諸説あり
特別な専門用語ではありませんが、現場ではよく使われる呼び方です。焼入れ液に全体を浸すことがポイントなので、このように親しみやすく呼ばれています。
全体焼入れに適した材料
- S45C(機械構造用炭素鋼)
- SCM440(クロモリ鋼)
- SK材(工具鋼)
- SKD材(ダイス鋼)
鋼の炭素量がある程度以上でないと、マルテンサイト化できず十分な硬度が得られません。
一般的に炭素含有量が0.4%以上ある材料が全体焼入れに適しています。
全体焼入れの特徴
✅ メリット
- 部品全体が均一に硬くなる
→ 摩耗や荷重に全体で耐えられる - 比較的シンプルな処理方法
→ 設備が普及しておりコストも抑えやすい - 幅広い材料に対応可能
⚠️ デメリット・注意点
- 焼入れによる変形や歪みが出やすい
→ 高精度な部品には注意が必要 - 脆くなる(靱性の低下)ため割れのリスクあり
→ 焼戻しが必須 - 必要のない部分まで硬化する
→ 機械加工が困難になることもある
全体焼入れが適している用途
- シャフト類(曲げ荷重+摩耗に耐える)
- カムシャフト、ギヤ(中小型で精度が求められないもの)
- 工具や金型部品(全体的に高硬度が必要なもの)
- ピンやボルトなどの機械部品
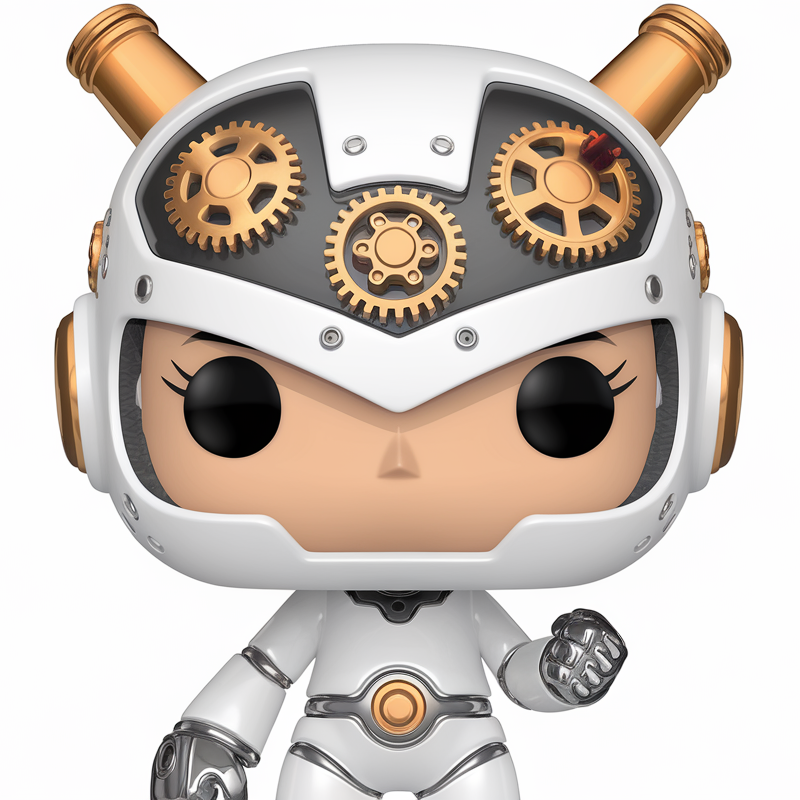
全体を均一に硬くしたい場合、コストと性能のバランスが良い処理として選ばれます。
全体焼入れ時の設計ポイント
✅ 焼入れ後の寸法変化を考慮する
精度が必要な箇所には研磨代を設けることが重要です。
✅ 応力集中部に注意
角が鋭すぎたり、断面急変部があると割れやすくなるため、R加工(面取り)や逃がし加工が有効です。
✅ 焼戻し処理の設計も忘れずに
焼入れ後そのままでは脆く割れやすいため、焼戻し温度の設定(400〜600℃程度)を適切に設計します。
他の焼入れ方法との違い
焼入れ方法 | 特徴 | 適用範囲 |
---|---|---|
全体焼入れ | 全体が硬化、変形しやすい | シャフト、工具、汎用部品 |
高周波焼入れ | 表面のみ硬化、芯は粘りあり | 局部硬化が必要な軸・歯車など |
浸炭焼入れ | 表面を炭素で硬化させる | ギヤ、カム、ピン類に最適 |
真空焼入れ | 歪みが少ない・酸化しにくい | 精密部品・金型 |
熱処理の硬度指定・変形・ひずみは熱処理業者と相談するのが正解!
金属部品に強度や耐摩耗性を持たせるために行う「焼入れ」などの熱処理。設計図面に硬度や熱処理方法を指定することはよくありますが、「思ったより硬くならない」「変形して寸法が狂った」といったトラブルも珍しくありません。
こうしたトラブルを避けるために大切なのが、熱処理業者との事前相談です。
本項では、なぜ熱処理業者と相談することが重要なのか、どんなポイントを相談すればよいのかを、初心者の方にもわかりやすく解説します。
なぜ熱処理業者と相談が必要なのか?
熱処理は「材料」「形状」「要求性能」の3つのバランスで成り立っています。そのため、図面だけでは分からない細かい条件が、仕上がりに大きく影響することがあります。
主な相談ポイント
- 希望する硬度(HRCなど)が本当にその材料・形状で実現できるか?
- 焼入れによってどの程度の寸法変化や歪みが起こる可能性があるか?
- 焼戻し温度をどう設定すれば破損を防げるか?
- 量産時のバラつきをどうコントロールすべきか?
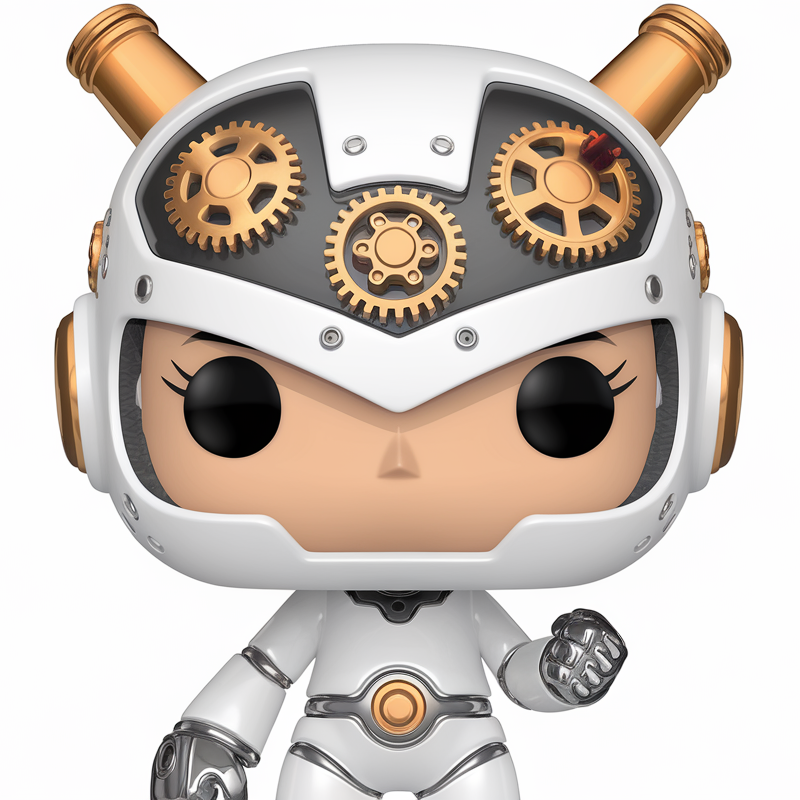
熱処理業者は、これらの点について実績や設備特性にもとづいたアドバイスをくれる、非常に頼りになる存在です。
硬度の指定は「材料と方法」によって実現できる範囲が違う
たとえば、以下のようなケースを見てみましょう。
材料 | 一般的な焼入れ後の硬度 | 備考 |
---|---|---|
S45C | HRC35〜45程度 | 高周波焼入れではHRC55以上も可 |
SCM440 | HRC50〜55 | 全体焼入れで安定した硬度が得やすい |
SKD11 | HRC58〜63 | 真空焼入れなどに適す |
SS400 | 焼入れ不可 | 炭素含有量が低いため硬化しない |
SUS304 | 焼入れ不可 | オーステナイト系のため硬化しない |
「とりあえずHRC60で」と指定しても、その材料や処理方法では実現不可能な場合があります。
無理に高硬度を要求すると、割れや変形、寿命短縮のリスクが高まります。
変形・ひずみの相談も重要!
焼入れでは、部品内部の応力が変化するため、どうしてもある程度の変形やひずみが発生します。
特に以下のような部品は注意が必要です。
- 薄肉のプレート形状
- 軸径の急変部があるシャフト
- 内径・外径に高い同軸度が求められる部品
熱処理業者に相談すれば、
✔ どこに歪みが出やすいか
✔ どのくらいの研磨代を見込むべきか
✔ ひずみを抑える冶具の有無
などの実務的なアドバイスをもらうことができます。
どんな相談をすればいいの?
図面を作る段階から、以下のような情報をもとに相談すると効果的です。
相談項目 | 内容 |
---|---|
材料の種類 | S45C、SCM440など明記する |
部品の形状 | 寸法図面を添えて相談する |
必要な硬度 | 目標値だけでなく用途を説明するとベター |
加工後 or 焼入れ後の精度要求 | 仕上げ研磨が必要かどうかも含めて伝える |
どこを硬化させたいか | 全体 or 表面のみ(局所)など |
図面に「HRC60程度」などと書くだけでなく、「ここは摩耗対策で硬度が必要」「ここは加工しやすく柔らかく残したい」といった設計意図を共有することで、最適な処理条件を提案してもらえます。
熱処理は業者との連携がカギ
焼入れは、ただ硬くすればいいというものではありません。材料の性質、形状のクセ、求められる性能によって、最適な熱処理条件は変わります。
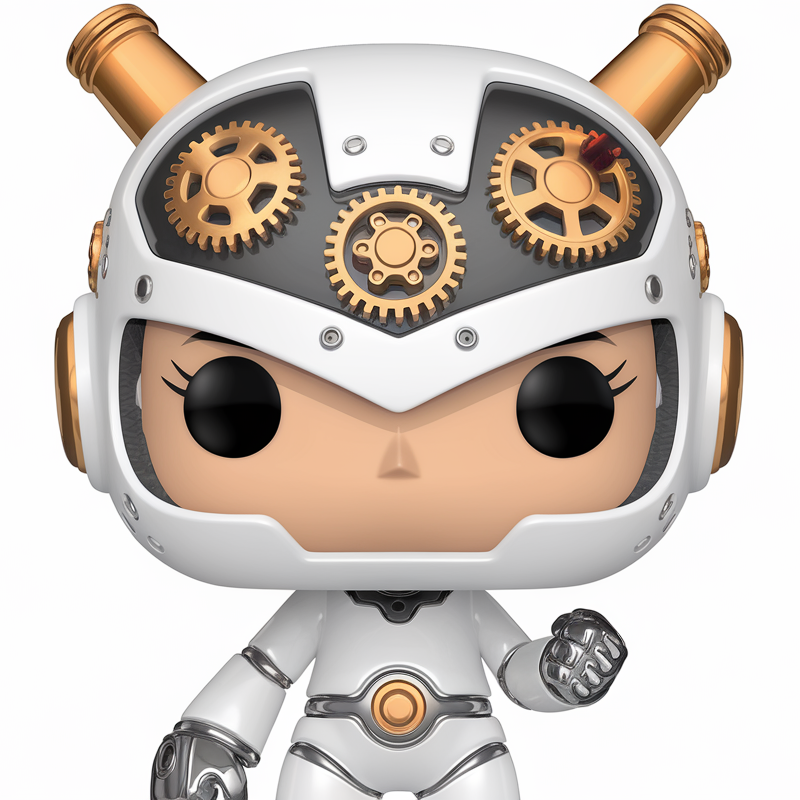
だからこそ、熱処理業者と早めに相談することが大切です。
相談を通じて、精度よく、品質の高い部品を効率的に仕上げることが可能になります。
設計段階で困ったら、まずは相談!
- 硬度指定に不安がある
- 焼入れ後の変形が心配
- コストや納期を抑えたい
そんなときは、遠慮せず熱処理の専門家(業者)に相談してみましょう。
設計の成功は、実はこうした「地味な対話」から始まっています。
まとめ:全体焼入れは基本かつ重要な熱処理方法
全体焼入れ(ズブ焼入れ)は、もっともオーソドックスな焼入れ方法のひとつであり、設計者・技術者にとって基本となる知識です。均一な硬度を得たい場合や、コストを抑えたい場面で非常に有効ですが、変形や割れのリスクもあるため設計段階での配慮が重要です。
「どこまで硬度が必要か?」「焼入れ後の精度はどう保つか?」といった点は、熱処理業者との相談も含めて最適化していく必要があります。
部品の用途や求められる性能に応じて、最適な焼入れ方法を選択することが、製品全体の品質向上につながります。
コメント