ネジは機械設計で最も多く使用される締結要素の一つですが、その中でも「おねじ(外ねじ)」を加工する際には、“逃がし”と呼ばれる重要な加工が関係します。
この記事では、
✔ なぜ逃がし加工が必要なのか?
✔ どんな形状や寸法が適切なのか?
✔ 逃がし加工を省略した場合に起こる問題とは?
といったポイントを、図解イメージや実務例を交えてわかりやすく解説します。
そもそも「逃がし加工」とは?
逃がし加工とは、おねじ(外ねじ)の根元に設ける“段差や溝”のことを指します。
ねじ切りの端部、特にボルト先端やシャフトの端で「ねじ山が立たない部分」や「工具が届きにくい部分」に余裕を持たせるための加工です。
代表的な形状の例
✅ 幅広の段付きストレート逃がし(直角逃がし)
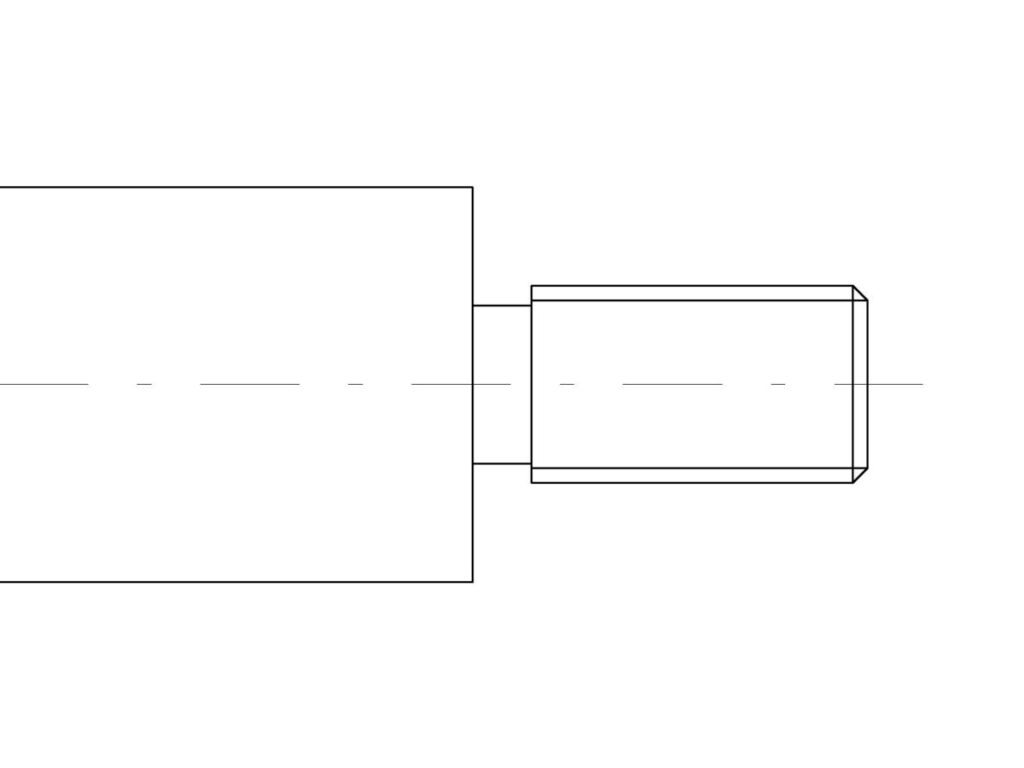
✅ 丸み(R)付きの逃がし
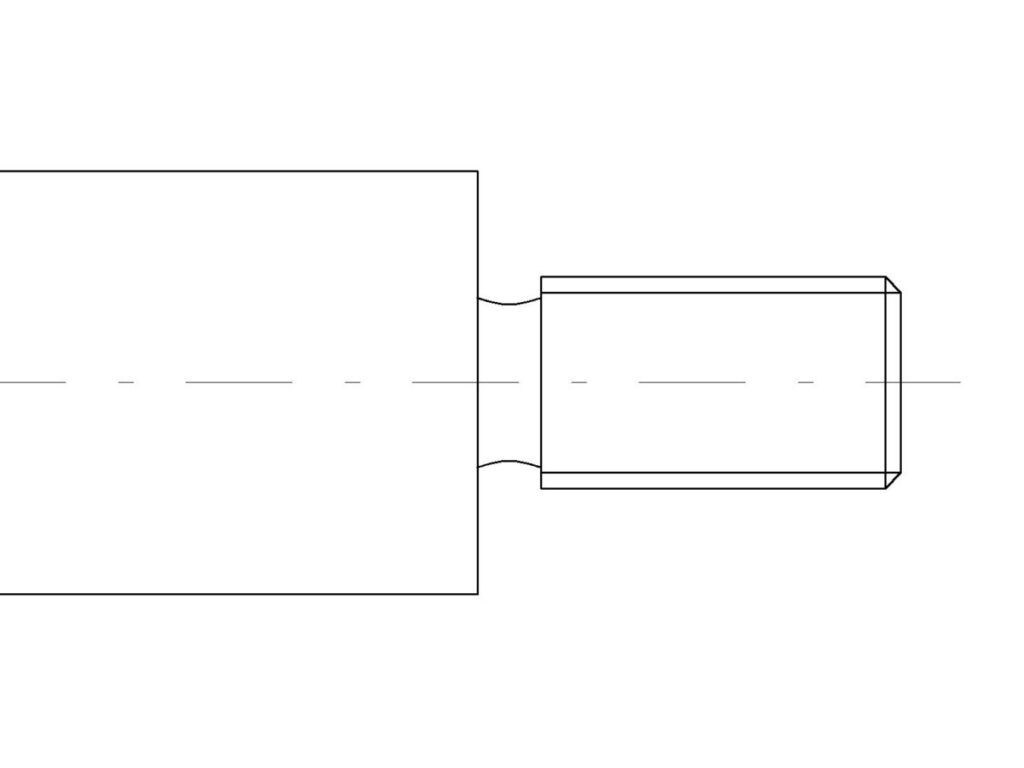
逃がし加工が必要な理由
逃がし加工が必要になる理由は、以下のような加工上・組立上の問題を防ぐためです。
ねじ切り工具の構造的限界
タップやダイス、旋盤用バイトには「逃げ」が必要です。工具の先端には切り込みできない部分(丸まった先端部)があるため、根元まできっちりねじ山を立てることができません。
👉 そのままだと、ナットやめねじが最後まで入らず締結不足になります。
ねじ山の干渉防止
おねじの根元部分が、相手部品の角に接触してしまうと、ねじが斜めに入りやすくなり、破損や偏心の原因になります。
👉 逃がしを設けておけば、相手部品とのスムーズな組立が可能です。
応力集中の低減
ネジ山の終端には応力が集中しやすく、特に繰返し荷重下では疲労破壊の起点になることがあります。
👉 逃がし部を滑らかに仕上げることで、応力集中を緩和できます(特に回転軸や振動環境では重要)。
逃がし加工の代表的な形状と用途
形状の種類 | 特徴 | 主な用途・メリット |
---|---|---|
ストレート逃がし (段付き) | 根元に径の小さな段差部を設ける | 組立時の干渉防止 ナット完全締結に有効 |
丸逃がし (R逃がし) | 半径R形状の逃がし (例:R0.5〜1.5) | 応力集中が少ない 主に回転軸・精密部品に多い |
寸法の目安と設計時のチェックポイント
逃がしの寸法には明確なJIS標準はありませんが、以下のような実務上の目安があります。
逃がしの径(φ)
- ねじのピッチ+0.2mm~0.5mm程度が一般的(例:M10ならφ8程度)
- ただし、加工工具に応じて調整が必要
幅(長さ)
- 少なくとも1.5山〜2山分の幅(ピッチ×1.5〜2)
- M10×1.5なら → 逃がし幅 約2.25〜3mm
逃がし形状の推奨
- スムーズな組立重視 → ストレート逃がしが有効
- 回転部・高応力部 → 丸逃がし
逃がしの目安寸法
ねじ径 | ピッチ(mm) | 逃がし径(mm) | 逃がし幅(mm) |
M3 | 0.5 | 2 | 1 |
M4 | 0.7 | 3 | 1 |
M5 | 0.8 | 4 | 1.5 |
M6 | 1.0 | 4.5 | 1.5 |
M8 | 1.25 | 6.5 | 2 |
M10 | 1.5 | 8 | 3 |
M12 | 1.75 | 9.5 | 3.5 |
M16 | 2.0 | 13.5 | 4 |
M20 | 2.5 | 17 | 5 |
M24 | 3.0 | 20 | 5 |
M30 | 3.5 | 26 | 5 |
逃がし加工を設けない場合のリスク
逃がしを省略してしまうと、以下のようなトラブルや不具合が発生する可能性があります:
問題 | 内容 |
---|---|
締結不足 | ネジ山が途中で止まり、ボルトが最後まで締められない |
組立不良 | 部品同士が干渉し、無理な押し込みで斜めネジが発生 |
工具破損 | バイトやタップが途中で干渉して折損するリスク |
図面での指示例と注意点
設計図面で逃がし加工を明示する際は、以下のように記載します。
- 【逃がし部 φ9.5×3(丸みR1.0)】など寸法と形状を明記
- JISに準拠した寸法公差を与える場合もあり
- 特殊な逃がし形状を使うときは「断面図」や「詳細図」で補足
🚫 注意
「ねじ部端まで加工」とだけ書いてあると、現場が判断に困ることがあるため、逃がし形状・寸法は必ず具体的に指示するのがベストです。
強度が必要なねじ部では“めねじ側で逃がす”のが有効!
おねじ(外ねじ)の端部には、通常「逃がし加工」が施されます。これは工具の制約や締結性向上のために必要な加工ですが、一方で逃がし部分が“応力の弱点”になるケースもあります。
本項では、
- なぜ逃がし加工を行わない方が良い場合があるのか?
- その代わりに“めねじ側にC面取り”を設けるとはどういうことか?
- 実際の設計上の注意点は?
という点を中心に、わかりやすく説明します。
逃がし加工は便利だが、強度的には弱点になることも
逃がし加工は、おねじの根元部分にRや段差を設けることで、以下のようなメリットがあります。
✅ 工具の逃げを確保できる
✅ 組立がスムーズになる
✅ 応力集中を緩和できる(※ただしR形状に限る)
しかし、実務では以下のような設計ニーズも存在します。
「ねじ部にできるだけ応力の弱点をつくりたくない」
「引張荷重や衝撃荷重がかかるため、ねじ部の根元は極力太く、段差をなくしたい」
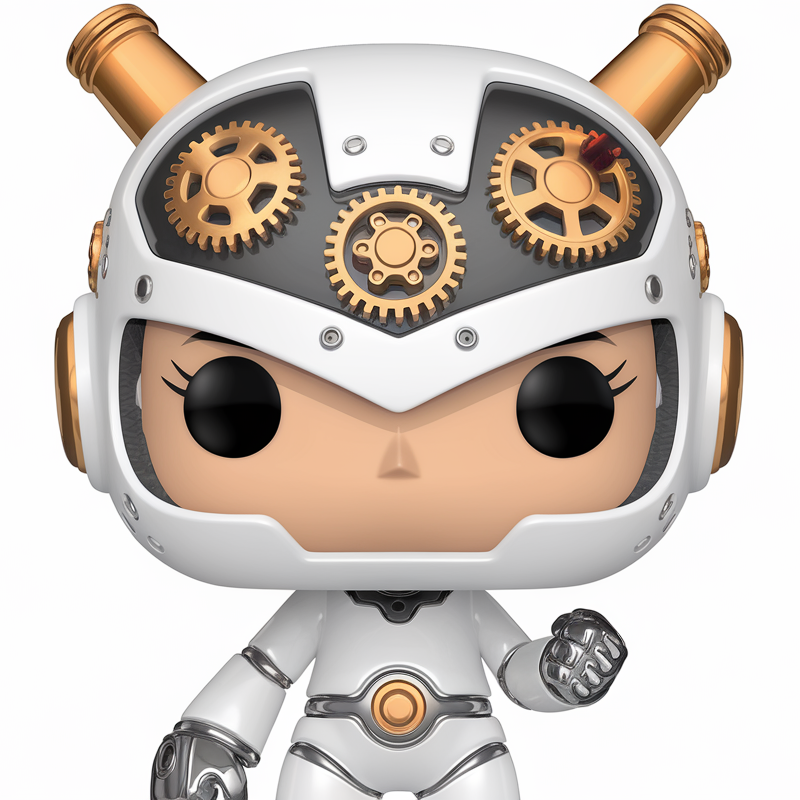
このようなとき、逃がし加工による“段付き部”や“削り込み”が強度的なリスクになります。
逃がし加工を行わずに済ませる方法:めねじの口元にC面取りを設ける
このようなケースでは、おねじ側に逃がし加工を設けない代わりに、めねじ側(ナットや部品側)に以下のような工夫をします。
めねじの口元に「C面取り(または面取り)を設ける」
🔍 例)
- C1.0
- 60°の面取り(先端角付き)など
この方法により、おねじのねじ山が立っていない端部が、めねじにうまく納まるようになります。
つまり、「逃げる側を“相手側”に持たせる」という発想です。
なぜこの方法が有効なのか?
この設計方法には以下のようなメリットがあります。
✅ おねじのシャフト径を逃がしで削らず、断面強度を維持できる
👉 引張りや曲げに強く、ねじの根元での破断リスクを抑えられます。
✅ 回転部や高負荷部でも、段差や応力集中を避けられる
👉 特に中実シャフト・細径軸・クランクピン等の強度設計に有効。
✅ ねじ加工がシンプルで、旋盤加工やNC加工でも効率がよい
👉 工程削減につながるため、コスト的にも◎
設計上の注意点とポイント
この方法を使う際には、いくつかの重要な設計ポイントがあります。
項目 | 内容 |
---|---|
C面の寸法 | 少なくとも「ピッチの2山分」以上(例:M10×1.5ならC3.0以上) |
C面の角度 | 標準45°が多いが、機械加工の工具やタップ形状に応じて調整可能 |
組立時の公差 | めねじ側のC面がしっかり形成されていることが前提 (C面なしの穴だと組立不可) |
適用例:どんな場面で有効か?
この設計法が特に効果を発揮するのは、以下のような場面です。
高強度が要求されるシャフト部品
- アクチュエーターの出力軸
- ピンジョイント部
- クランクピンなど
高荷重がかかる引張ねじ(特にボルトよりも軸側ねじ)
軽量化が必要で、おねじの余計な削り込みを避けたい場合
逃がし加工は万能ではない!用途に応じて設計を変えるのがコツ
項目 | 内容 |
---|---|
通常の逃がし加工 | 工具の都合、組立性、応力緩和には有効だが、強度は若干低下 |
めねじ側のC面取りで逃がす | おねじ側の断面強度を維持しながら、ねじ組み付けも可能 |
設計の使い分け | 回転部や高荷重部では「逃がしなし+C面取り」が安全なケースもある |
逃がし加工は設計者にとって基本的な考慮事項ですが、状況によっては「あえて逃がさない設計」の方が合理的な場合もあります。
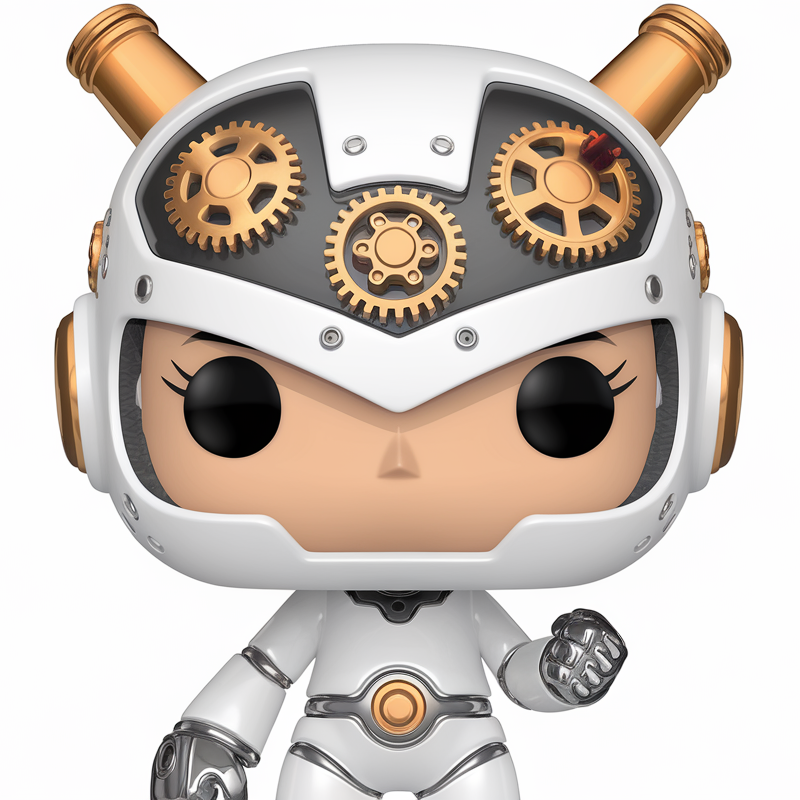
強度設計や応力解析を行う場面では、こうした代替手段を知っておくと、より柔軟な図面設計が可能になります。
ぜひ今回の内容を、今後の設計業務にお役立てください。
まとめ
ポイント | 要点 |
---|---|
逃がし加工とは? | おねじ端部の段差やRで、工具・組立・耐久性を考慮した加工 |
必要な理由 | 工具の限界、組立性、応力集中の緩和のため |
推奨形状 | 軸にはR逃がし、ボルトにはストレートや面取りが多い |
設計の注意 | ねじ径・ピッチに応じた幅と径を設計し、図面指示を明確に |
逃がし加工は地味な要素ですが、正しく設けることで加工トラブル・不具合・破損を防ぐ非常に重要な設計ポイントです。
とくに繰り返し負荷がかかる機械や精密機構においては、逃がしの有無が寿命を大きく左右します。
設計時にはぜひ、「ねじ端部には逃がしを入れる」という基本を意識して、より高品質な図面づくりに役立ててください。
コメント