機械設計において、材料の耐食性は、長寿命で信頼性の高い製品を実現するために重要な要素です。特に過酷な環境にさらされる機械や装置では、材料の選定や表面処理を通じて、腐食による劣化を防ぐ対策が必要です。本記事では、機械設計における耐食性対策として、材料選定と表面処理方法を交えたアプローチについて解説します。
腐食とは?
腐食とは、金属や合金が環境要因(酸素、水分、化学物質、塩分など)に反応して化学的に分解し、劣化する現象です。腐食が進行すると、材料が脆くなり強度や機能が低下し、最終的には破損や故障に至る可能性があります。特に湿気の多い環境や海水にさらされる環境では、耐食性を考慮しないと、機械の寿命が大幅に短縮されることがあります。
耐食性のある材料の選定
耐食性を確保するためには、適切な材料を選定することが第一の防御策です。以下に、一般的な材料の耐食性の特徴を示します。
材料 | 特徴 | 耐食性 |
SUS304 | ステンレス鋼で、酸やアルカリに強く、一般的な耐食性を持つ。 | 高い |
SUS316 | SUS304よりさらに優れた耐食性を持ち、海水や化学環境にも対応。 | 非常に高い |
アルミニウム合金 | 軽量で、アルミナ皮膜によって自然に表面が保護される。 | 中程度 |
チタン | 非常に優れた耐食性を持ち、海洋環境や化学工場などで使用される。 | 非常に高 |
SS400 | 一般構造用鋼。低コストだが、腐食に対する耐性は低い。 | 低(表面処理で耐食性向上が必要) |
SKD11 | クロムの含有量が高いため、SS400に比べ錆びにくい。 | 中程度 |
SCM440 | 高強度を持つが、腐食環境では表面処理が推奨される。 | 中程度 |
特にステンレス鋼は、一般的な耐食性を持つため、湿気の多い環境や化学工場で使用されることが多いです。一方、鋼材(SS400やSCM440など)は、コスト面では優れていますが、腐食しやすいため、表面処理を施すことが推奨されます。
表面処理による耐食性向上
材料選定だけでなく、表面処理による腐食対策も有効です。以下に、耐食性向上のための一般的な表面処理方法を紹介します。
ユニクロメッキ
ユニクロメッキは、クロメート処理の一種で、亜鉛メッキの上に透明なクロメート層を施す処理です。これにより、耐食性がさらに強化され、見た目は銀色で美しい光沢があります。ユニクロメッキは、コストを抑えつつ耐食性を高めるため、様々な分野に広く使用されています。湿度の高い環境や、軽度の腐食に対する保護に有効です。
✅ メリット: 低コストで広く利用可能。見た目も美しく、耐食性が向上。
🚫 デメリット: 海水や強酸・強アルカリの環境では長期的な耐食性に限界がある。
無電解ニッケルメッキ
無電解ニッケルメッキは、電気を使わずに化学反応によって金属の表面に均一なニッケル層を形成する処理方法です。このメッキは、複雑な形状の部品でも均一な膜厚が得られることが特徴で、耐食性に優れているだけでなく、耐摩耗性や硬度も向上します。特に、化学薬品や高温環境にさらされる部品に対して非常に効果的です。
✅ メリット: 均一な被膜を形成でき、耐食性と耐摩耗性がともに高い。複雑な形状にも対応可能。
🚫 デメリット: コストが高めで、電気メッキよりも時間がかかる場合がある。
アルマイト処理(アルミニウム)
アルミニウム合金に対して施されるアルマイト処理は、酸化皮膜を人工的に厚くすることで耐食性を向上させる処理です。この処理は、軽量なアルミニウム製品に使用され、航空機や自動車の部品などに広く採用されています。また、表面を硬化させる効果もあり、耐摩耗性も向上します。
クロムメッキ
クロムメッキは、材料の表面にクロムの層を形成し、耐食性を向上させる処理です。クロムメッキは、強い耐摩耗性とともに、光沢のある仕上がりが特徴です。高級感のある外観を求める場合や、高温や化学薬品に耐える必要がある部品に適しています。
フッ素コーティング
フッ素コーティングは、非粘着性と耐食性に優れたコーティング処理で、特に化学薬品にさらされる環境での使用に適しています。この処理は、化学工場の機器や、食品や医療分野でも利用されています。
材料選定と表面処理の組み合わせ
機械設計における耐食性対策は、材料選定と表面処理の組み合わせによって効果が最大化されます。例えば、ステンレス鋼(SUS304やSUS316)自体は高い耐食性を持ちますが、さらに過酷な環境では追加の表面処理を施すことで、さらに耐久性を向上させることができます。
一方、コスト面で優位性があるSS400やSCM440などの一般鋼材は、表面処理を行うことで耐食性を確保し、適用範囲を広げることができます。具体的な設計要件に応じて、以下のような材料選定と表面処理の組み合わせが推奨されます。
環境 | 材料選定 | 表面処理 |
一般的な屋内環境 | SS400, SCM440、SUS304 | ユニクロメッキ、無電解ニッケルメッキ |
高湿度環境 | アルミニウム合金、SUS316 | アルマイト処理 |
海洋環境 | SUS316, チタン | フッ素コーティング, クロムメッキ |
材料の錆が与える悪影響とは?
機械設計の現場では、材料選定において「錆(さび)」の発生が重要な課題となります。錆は、材料の機械的特性や外観に大きな影響を与え、設計者が見過ごすと製品寿命や安全性に重大な影響を及ぼす可能性があります。本項では、錆が機械設計に与える悪影響と、その対策について解説します。
錆の発生メカニズム
錆は、金属が環境中の酸素や水分と反応して酸化物や水酸化物を生成する化学反応の結果です。
- 鉄(Fe)の場合、酸化鉄(Fe₂O₃)が錆の主成分となります。
- ステンレス鋼(例: SUS304)は耐食性がありますが、塩分や強酸性環境では腐食を受けることがあります。
- アルミニウムの場合、酸化膜(Al₂O₃)が一種の防護膜として働きますが、環境次第では腐食が進むこともあります。
錆が材料に与える悪影響
🚫機械的強度の低下
錆は材料表面から内部に進行し、断面積が減少するため、強度が低下します。
- 例: 機械部品のボルトやナットが錆びると、せん断強度や引張強度が大幅に低下します。
- 破損リスクが高まり、安全性に直結する問題を引き起こします。
🚫摩擦や動作不良
スライドや回転運動を伴う部品が錆びると、表面の滑らかさが失われ、摩擦係数が増加します。
- 例: リニアガイドやベアリングに錆が発生すると、摩耗が進み寿命が短縮します。
🚫電気的特性の劣化
錆は材料の電気伝導性を低下させます。
- 例: 電気接点が錆びると、接触不良や回路の断線が発生し、電気機器の誤作動につながります。
🚫外観品質の低下
錆は製品の見た目に直接影響し、顧客満足度を低下させます。
- 特に、外装部品や装飾部品では見た目の悪化が顧客に悪い印象を与える要因となります。
🚫化学反応による二次被害
錆が進行する過程で、周辺部品や環境にも悪影響を及ぼす場合があります。
- 例: 錆びた鉄が溶解して周囲の金属を腐食させる「異種金属腐食」や、錆による粉塵が電子部品に侵入するケース。
錆を防ぐための設計上の工夫
✅ 適切な材料選定
- 耐食性の高い材料を使用する。
- 例: ステンレス鋼(SUS304, SUS316)やアルミ合金。
- 腐食環境に応じて、防錆処理済みの材料を採用する。
✅ 表面処理の活用
表面処理により錆の発生を抑制することが可能です。
- メッキ処理: 亜鉛メッキ、クロムメッキなど。
- 塗装: 耐候性塗料の採用。
- アルマイト処理: アルミニウム合金の酸化皮膜処理。
✅ 環境条件の制御
- 部品が錆びやすい環境(湿度や塩分濃度が高い場所)に設置される場合は、防湿対策や適切な換気を行う。
- 絶縁処置: 異種金属接触部での腐食を防ぐために絶縁部材を挿入。
✅ メンテナンス性の向上
- 定期的な清掃や防錆剤の塗布。
- 点検しやすい設計(錆びやすい部分にアクセスしやすい構造)。
事例: 錆によるトラブルと教訓
👉 事例1: 海岸地域で使用される機械部品
海岸沿いの工場で、鉄製のボルトを使用していたが、塩分を含む湿気で錆が発生。
🚨 対策として、SUS304製ボルトへの変更や、定期的な防錆スプレーの使用でトラブルが解消。
👉 事例2: 屋外設備の配管
配管に使用された一般鋼材が雨水で錆びて破裂。
🚨 防錆塗料の塗布や、錆に強い亜鉛メッキ鋼材への切り替えで再発防止。
錆は機械設計において無視できない大きな問題です。材料選定や表面処理、設計工夫を通じて錆を予防することで、製品寿命を延ばし、トータルコストを削減できます。また、定期的なメンテナンスと点検を行うことも、錆によるトラブルを未然に防ぐ重要な手段です。
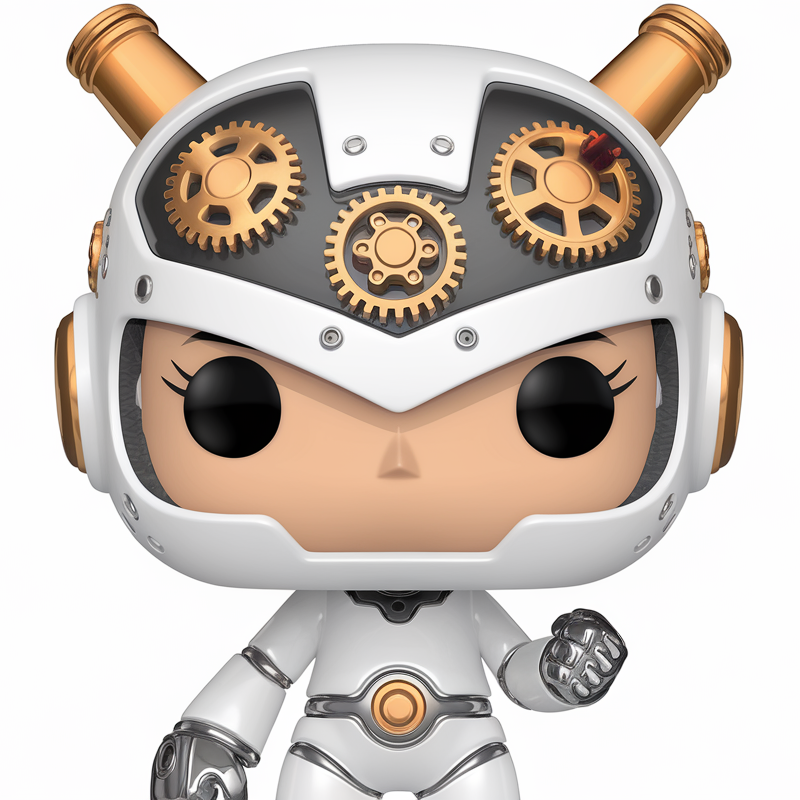
錆のリスクを適切に管理し、高品質で信頼性の高い製品を設計しましょう。
まとめ
機械設計における耐食性対策は、材料選定と表面処理の両方を適切に行うことが不可欠です。材料自体の耐食性を考慮しつつ、環境や使用条件に合わせて表面処理を選定することで、製品の耐久性と性能を大幅に向上させることが可能です。設計段階でこれらの要素を十分に検討することで、信頼性の高い機械や装置を作り上げることができます。
コメント