有効締結長さとは、ねじの締結部において、適切な強度と信頼性を確保するために必要なねじのかかり長さのことを指します。これは、機械設計において重要な要素であり、適切な寸法を設定しないと、ねじの緩みや破損、接合部分の強度不足が発生する可能性があります。
本記事では、有効締結寸法の基本概念や設計の際の考慮点、材料による違いについて詳しく解説します。
有効締結長さの基本概念
有効締結長さは、通常「有効ねじ部の長さ」として表され、ねじ山がナットや母材にしっかりと接している部分を指します。つまり、ねじの機械的結合が強固に行われている部分であり、強度を持たせるために十分な長さが必要です。
この有効締結寸法が短すぎると、以下の問題が生じる可能性があります。
🚫 ねじの破損
引張荷重に対して強度不足になり、破断が発生する可能性が高まります。
🚫 緩みやすさ
ねじ山が十分にかかっていないため、振動や衝撃に対して緩むリスクが高まります。
最低有効締結長さについて
一般的に、ねじの有効締結寸法は、ねじ径(呼び径)を基準に決定されます。以下に代表的な計算式を示します。
最低有効締結寸法の目安
\( \displaystyle L=d×k\)
- L:有効締結寸法(mm)
- d:ねじ径(mm)
- k:係数(材質によって異なるが、通常鋼製の場合は0.8程度)
例えば、M10(ねじ径が10mm)のボルトを使用する場合、鋼製の母材との締結を考えると、有効締結寸法は最低8mm程度が必要です。
これは、JIS1種、2種のナットの厚みと同等の数値となっており、最低限の締結長さと言っていいでしょう。
ねじ山のせん断荷重について
ねじ山のせん断強度は0.6dの時にねじの引張強度と同等になるといわれています。
つまり、0.6dより締結寸法が長ければ、ねじ山が破壊される前に引張荷重によりねじが破壊されるということになります。
これは、締結寸法を0.6dより長くしておけば、引張荷重による強度計算だけで破壊のリスクを抑えられるとも考えられます。
また、JIS3種のナットは0.6dとなっており、設計上どうしても締結長さが確保できない場合は引張荷重などを考慮し、十分に注意して選定しましょう。
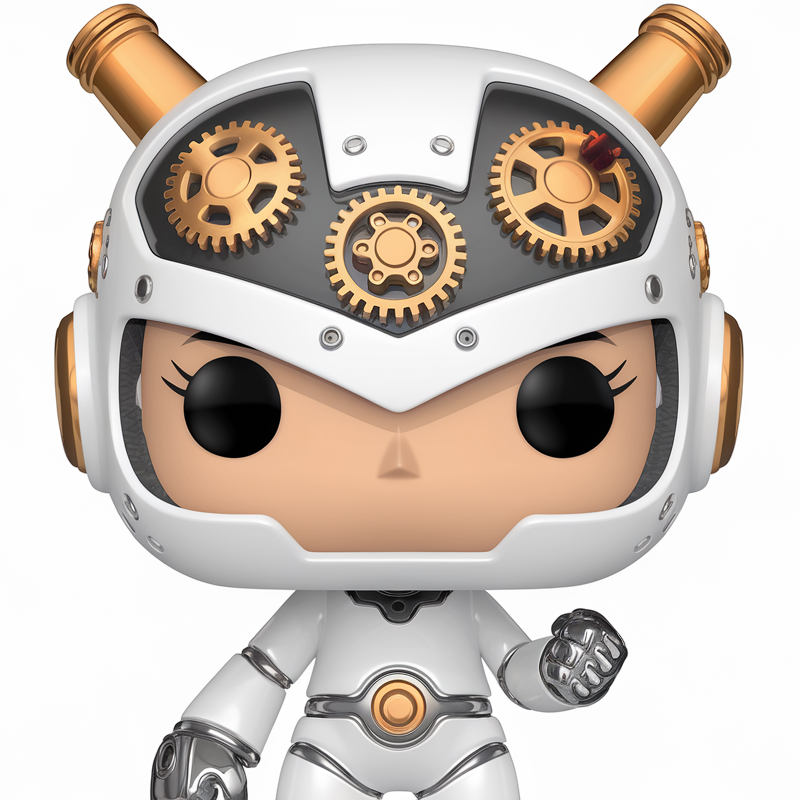
有効締結寸法に明確な基準はなく、可能であれば1dは確保しておきたいところです。
また、どうしても寸法を確保できない場所では荷重計算などして適材適所で設計していきましょう。
有効締結長さを確保するための設計ポイント
✅ 十分なかかり長さを確保する
- 使用する材料の特性に応じて、ねじのかかり長さを調整します。
- 鋼材ならねじ径の1~1.5倍、アルミニウムやプラスチックならそれ以上の長さを確保しましょう。
✅ 座金やナットの併用
負荷の分散やねじの締結力を向上させるために、座金やナットを適切に選定し使用することも重要です。
✅ タップ加工の精度
母材にタップ加工を施す場合は、精度の高い加工を行い、ねじ山がしっかりと形成されていることを確認します。
タップ加工:有効ねじ部深さの基準と重要性
タップ加工(ねじ穴加工)は、部品を固定するための接合手段として非常に一般的に使用されます。その中でも「有効ねじ部深さ」は、接合の強度や耐久性に直接影響する重要な設計要素です。
本項では、有効ねじ部深さの基準として一般的に使用される「ねじサイズ × 2」について解説し、その重要性や設計における考慮点を紹介します。
有効ねじ部深さとは
有効ねじ部深さとは、ねじが実際に締結力を発揮するねじ山部分の深さを指します。タップ加工で形成されたねじ山が完全な形状を維持し、十分な接合強度を確保できる範囲です。適切な深さを確保することで、以下の利点があります。
✅ 十分な締結強度の確保
✅ ねじの抜け防止
✅ 部品の長寿命化
「ねじサイズ × 2」の基準
多くの機械設計では、有効ねじ部深さを「ねじサイズ(直径) × 2」に設定するのが一般的です。これは、以下の理由からこの基準が有効であるとされています:
接合強度のバランス
- 有効ねじ部深さがねじサイズの2倍の場合、ほぼ全体の締結強度を発揮できる設計となります。
- これ以上深くすると加工コストが増加し、これ以下では強度不足となる可能性があります。
加工の効率性
ねじの深さを「サイズ × 2」に統一することで、加工工程の標準化が可能になり、生産性の向上に繋がります。
ねじ破損の防止
過剰な深さで加工を行うと、タップ折れやねじ山崩れのリスクが増加します。
ねじサイズと有効ねじ部加工深さ
以下に、一般的なねじサイズの有効ねじ部深さをまとめます。
ねじサイズ | 有効ねじ部加工深さ(推奨) |
---|---|
M3 | 6 mm |
M4 | 8 mm |
M5 | 10 mm |
M6 | 12 mm |
M8 | 16 mm |
M10 | 20 mm |
注意点
🔍 材料の特性を考慮
材質によっては、「ねじサイズ × 2」では十分な強度を確保できない場合があります。例えば、アルミ合金や樹脂などの低強度材料では、深さをさらに増やす必要があります。一方、高強度材料では深さを減らしても十分な強度を得られることがあります。
🔍 ねじ種類の違い
メートルねじ以外のねじ(例えばUNCねじやUNFねじ)では、ねじ山の形状が異なるため、別の基準が適用される場合があります。設計段階で規格を確認しましょう。
🔍 加工工具の選定
深いタップ加工を行う場合、タップの選定と加工条件(回転数、送り速度など)が重要です。不適切な条件ではタップ折れや加工不良が発生する可能性があります。
🔍 設計意図に応じた調整
設計要件によっては、推奨基準よりも浅い深さや深い深さが必要になる場合があります。その際はCAE解析や試験を通じて十分な検証を行いましょう。
「ねじサイズ × 2」を使わない例
場合によっては、「ねじサイズ × 2」以外の深さを選定することもあります。
以下はその一例です。
🚫 浅い深さ(例えば「ねじサイズ × 1.5」)
軽負荷で強度があまり必要ない場合や、薄板へのねじ加工を行う場合。
🚫 深い深さ(例えば「ねじサイズ × 3」以上)
大きな負荷がかかる締結部や、振動・衝撃の多い環境下での使用。
実務でのポイント
- 試験や解析の実施
推奨基準に基づいて設計を行っても、使用条件や材料の特性に応じて最適な深さを確認する試験が必要です。 - タップ加工の精度管理
加工後に深さやねじ山の状態を測定し、設計どおりに仕上がっているか確認しましょう。 - 標準化の推進
社内やプロジェクト内でのタップ加工基準を統一することで、設計・製造工程の効率化が図れます。
タップ加工における「ねじサイズ × 2」の有効ねじ部深さは、接合強度と加工効率を両立するための一般的な基準です。
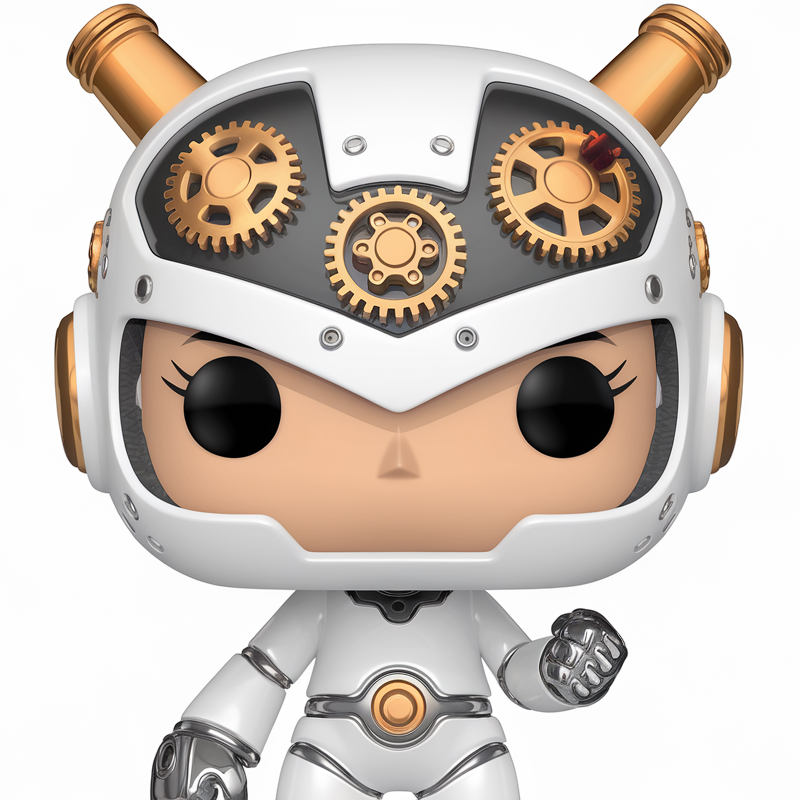
ただし、材質や使用条件によっては適切な深さが異なる場合もあるため、設計段階で慎重な検討が必要です。基準を守りつつ、状況に応じた柔軟な対応を行うことで、安全性と生産性を両立した設計が可能となります。
薄板にタップを立てるには? バーリング加工の活用!
バーリング加工とは?
バーリング加工とは、薄板の穴の周囲を盛り上げて厚みを確保する加工方法です。
これにより、以下のメリットがあります。
✅ タップを切るための有効ねじ長さを確保できる
✅ 薄板でもボルトの締結力を強化できる
✅ ナットを使わずに組み立てが可能になるため、部品点数を削減できる
バーリング加工の流れ
1️⃣ 下穴を開ける
- まず、タップを立てる位置にドリルで下穴を開けます。
2️⃣ バーリング加工を行う
- プレス機や専用工具を使って、穴の周囲の材料を盛り上げて厚みを増やします。
3️⃣ タップ加工をする
- 盛り上がった部分にタップを立てて、ねじを切ります。
4️⃣ ボルトを締める
- ねじがしっかり切れていれば、薄板でも強固にボルトを締結できるようになります。
🔹 バーリング加工を活用する場面
🔹 板金製品のねじ固定(電気機器・自動車部品など)
🔹 アルミやステンレスなどの薄い金属板の組み立て
🔹 ナットの使用を避けて軽量化したい場合
薄板のタップ加工にはバーリング加工が有効!
✅ 薄板に直接タップを立てると強度不足になる
✅ バーリング加工で厚みを確保すれば、ねじ山が潰れにくくなる
✅ ナット不要でコストダウンや軽量化が可能!
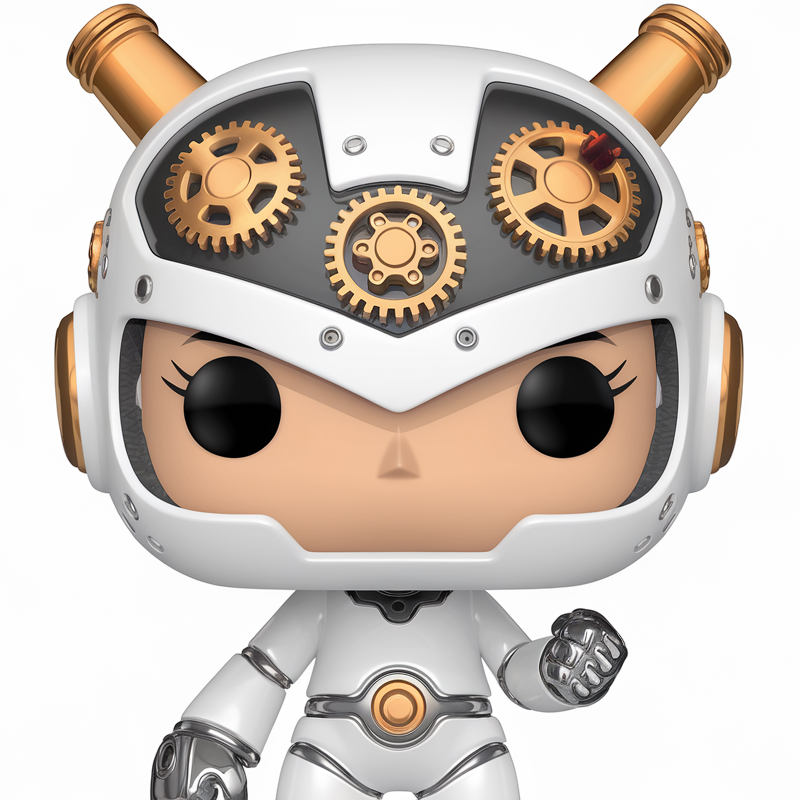
薄板にねじを切る必要がある場合は、ぜひバーリング加工を検討してみましょう!
まとめ
機械設計におけるねじの有効締結寸法は、接合部の強度や信頼性に直結する重要な要素です。適切な有効締結寸法を設定しないと、ねじが緩んだり破損したりするリスクが高まり、機械の安全性や耐久性に悪影響を及ぼします。
設計者は、使用する材料や荷重条件に応じて、最適なねじのかかり長さを計算し、必要な強度を確保することが求められます。
コメント