アルマイト処理(陽極酸化処理)は、アルミニウムやその合金に対して行われる表面処理の一つで、耐食性や耐摩耗性を向上させるために広く使用されています。
アルミニウム表面に人工的な酸化皮膜を形成することで、保護膜として機能し、外観の向上や腐食の防止に寄与します。
以下に、アルマイト処理の特性と、材料選定における考慮すべきポイントを詳しく解説します。
アルマイト処理の特性
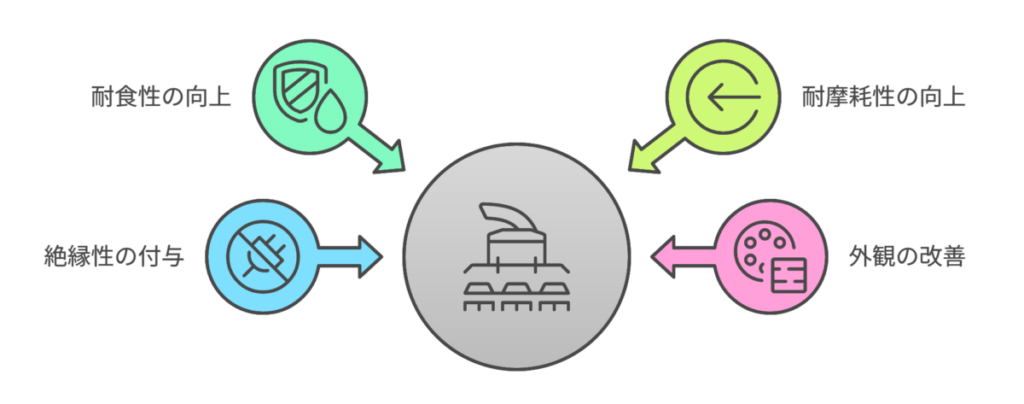
耐食性の向上
- アルミニウムの表面に酸化アルミニウムの層を形成し、金属を腐食や酸化から保護します。
- この酸化皮膜は、アルミ自体が持つ自然の酸化膜よりもはるかに厚く、耐食性を大幅に向上させます。
耐摩耗性の向上
- アルマイト処理は、酸化皮膜によってアルミニウムの表面硬度を高めます。
- 特に硬質アルマイト処理では、酸化皮膜の厚さをコントロールすることで、アルミニウムの柔らかさを補い、高い耐摩耗性が得られます。
- これにより、摩擦や接触が多い部品でも、長期間の使用に耐えることが可能です。
絶縁性の付与
- アルマイト皮膜は絶縁性を持ちます。
- 電気部品や電子機器において、導電性を避ける必要がある箇所に対してアルマイト処理を施すことで、表面を保護しつつ絶縁機能を付与することができます。
外観の改善
- アルマイト処理は、酸化皮膜を着色することで、美しい外観を得ることができます。
- 黒やシルバー、ゴールドなど、さまざまな色に仕上げることが可能です。
- 製品のデザイン性を高める目的でも広く使用されています。
- 耐久性の高い塗装として機能するため、装飾品、家電製品などの表面処理にも多用されています。
アルマイト処理の選定ポイント
使用環境
- アルマイト処理は、腐食や摩耗が問題となる環境に適しています。
- また、外観の改善が必要な場合や、絶縁性が求められる電気部品にも有効です。
- 一般的なアルマイト処理に加え、より高い耐摩耗性を求める場合は、硬質アルマイト処理が推奨されます。
機能要件
- アルマイト処理は、部品の耐摩耗性と耐食性を向上させるため、摺動や接触が多い部品に効果的です。
- 寸法精度に関しては、処理後の皮膜の厚さが部品に影響を与える場合があるため、クリアランスや公差の管理が必要です。
- 色や外観の仕上がりが重要な部品に対しては、アルマイト処理がデザイン的な要件も満たすことが可能です。
コスト管理
- アルマイト処理は、アルミニウムの寿命を延ばすため、コストパフォーマンスに優れた処理方法です。
- 外観の改善や防食機能に加え、耐摩耗性や耐熱性も向上するため、メンテナンスの頻度を減らし、長期的なコスト削減が期待できます。
- 特に、大量生産が必要な製品では、処理コストを抑えつつ機能性を高めることが可能です。
材質の適合性
- アルマイト処理はアルミニウムおよびその合金に対して最適な表面処理方法です。
- 他の金属には適用できないため、設計段階で材質がアルミニウムであることが前提となります。
- 合金成分によって処理後の酸化皮膜の色や硬度が異なるため、合金の種類に応じた処理条件の選定が重要です。
アルマイト処理に適した材質とは?
アルマイト処理(陽極酸化処理)は、アルミニウム表面に酸化皮膜を作って耐食性・耐摩耗性・装飾性を高める表面処理です。
見た目をきれいにするだけでなく、アルミ部品の寿命や機能を向上させる効果があります。
アルマイト処理ができるのは基本「アルミ系材料」
アルマイト処理は、アルミニウムの化学的特性を利用した酸化反応によるものです。
そのため、鉄や銅、ステンレスには直接できません(別処理が必要)。
アルマイト処理に適した代表的な材質
純アルミ(1000系)
- 特徴:純度が高く、アルマイト皮膜がきれいで透明感のある仕上がり
- 用途:装飾品、光学部品、反射板
- メリット:皮膜の均一性・透明性が高い
- 注意点:強度は低め
アルミ合金 6000系(例:A6061、A6063)
- 特徴:強度・加工性・耐食性のバランスが良い
- 用途:機械部品、構造材、自転車フレーム
- メリット:皮膜が均一で、硬くて耐久性が高い
- 注意点:A6063は外観が美しく、A6061は強度が高いがやや外観は劣る
アルミ合金 5000系(例:A5052)
- 特徴:耐食性に優れ、海水環境でも強い
- 用途:船舶部品、屋外構造材
- メリット:耐食性が高く、腐食環境に強い
- 注意点:外観の仕上がりは純アルミや6000系ほど美しくない場合がある
アルマイトに不向きな材質
- 2000系アルミ合金(銅を多く含む):耐食性が低く、皮膜がムラになりやすい
- 7000系アルミ合金(亜鉛を多く含む):皮膜がやや荒れやすく、外観品質は劣る
- 鉄・ステンレス・銅:原理的にアルマイト不可(別の表面処理が必要)
まとめ
強度や外観、耐食性のバランスで材質を選ぶのがポイント
アルマイト処理はアルミ専用の表面処理
特に純アルミ(1000系)・6000系・5000系が適している
🔍アルミ合金の選定ポイント
🔗アルミ合金の特性と選定ポイント
🔗アルミ合金の引張強さランキング!どれが強い?使い分けのポイントも解説【熱処理と加工性】
🔗SS400とアルミ合金の違いと使い分けを徹底解説!【比重・剛性・コスト】
🔗SS400とA7075の違いと使い分け方をわかりやすく解説!【強度と剛性】
🔗アルミ合金と樹脂の違いと使い分けとは?【材料選定における軽量化】
🔍アルミ合金の種類について
🔗【アルミ合金】A2000番代とは?特性・用途・選定ポイントをわかりやすく解説!【ジュラルミン系】
🔗【アルミ合金】A5052・A5056の違いと特性【汎用アルミ】
🔗【アルミ合金】6000番代とは?特性と使い分けをわかりやすく解説!【アルミフレーム】
🔗【アルミ合金】A7075の特性と選定ポイント【超々ジュラルミン】
アルマイト処理の膜厚をコントロールする方法について
アルマイト処理(陽極酸化処理)は、アルミニウムやその合金の表面に酸化皮膜を形成する処理で、耐食性や耐摩耗性、美観を向上させる目的で広く使用されています。
膜厚(酸化皮膜の厚さ)は、製品の性能や用途に大きな影響を与えるため、適切にコントロールすることが重要です。本項では、アルマイト処理の膜厚をコントロールする方法について詳しく解説します。
アルマイト処理の基本原理
アルマイト処理は、電解液中でアルミニウムを陽極として電気を通すことで、表面に酸化皮膜を生成するプロセスです。この皮膜は、アルミニウムの酸化反応により形成され、その厚さや性質は、以下の処理条件により変化します。
膜厚をコントロールする主な要因
アルマイト処理の膜厚は、主に以下の要因でコントロールできます。
電解液の種類
- 使用する電解液の組成(硫酸、クロム酸、リン酸など)は膜厚形成に大きく影響します。
- 硫酸アルマイト処理
一般的な方法で、膜厚を比較的自由に調整可能。 - 硬質アルマイト処理
硫酸濃度を低く設定することで厚い皮膜を形成できます。
- 硫酸アルマイト処理
処理時間
- 処理時間を長くするほど膜厚は増加しますが、一定以上では増加が鈍化します。
- 膜厚を均一にするためには、時間管理が重要です。
電流密度
- 電流密度(電流値と処理面積の比率)を調整することで膜厚をコントロールできます。
- 高い電流密度では短時間で厚い膜を形成可能。
- 低い電流密度では薄い膜を均一に形成できます。
処理温度
- 電解液の温度は酸化反応速度に影響を与えます。
- 低温(0~10℃)
硬質な膜を形成しやすい。 - 高温(20~30℃)
薄く柔らかい膜を形成しやすい。
- 低温(0~10℃)
アルミニウム材質
- アルミニウムの純度や合金成分により、形成される膜厚や特性が異なります。
- 純アルミニウムは均一な膜を形成しやすい。
- 合金成分が多いほど膜厚が不均一になりやすいため、素材選定が重要。
電解液の攪拌(かくはん)
- 電解液を適切に攪拌することで、電流の均一化や熱の分散が行われ、膜厚の均一性が向上します。
後処理(シール処理)
- アルマイト処理後に行うシール処理も膜厚に影響を与える場合があります。
- 硬質アルマイトではシール処理が膜厚減少を抑えるよう配慮されます。
膜厚コントロールの具体例
要因 | 方法例 | 結果 |
---|---|---|
電解液 | 硫酸濃度を調整する | 硬質膜、薄膜を選択可能 |
処理時間 | 20分で標準膜(10~20μm)を形成 | 時間増加で膜厚も増加 |
電流密度 | 1~3A/dm²で制御 | 高密度で厚い膜を短時間で形成 |
処理温度 | 10℃で硬質膜、20℃で柔らかい膜を形成 | 高温は均一性を高める |
素材 | 純アルミ使用 | 均一で美しい膜を形成 |
攪拌 | 定常的な攪拌を行う | 膜厚を均一化 |
膜厚コントロールのメリットと注意点
メリット
✅性能の最適化
用途に応じて膜厚を調整することで、耐摩耗性や耐食性を最大限に発揮できます。
✅コスト効率の向上
必要最低限の膜厚に抑えることで、コストを削減可能です。
✅美観の向上
均一な膜厚により仕上がりが向上し、製品価値を高めます。
注意点
🚫膜厚の過剰設定
不必要に厚い膜は割れや剥がれの原因となる場合があります。
🚫電解液管理
電解液の劣化や不純物混入は膜厚不良の原因になります。
🚫合金成分の影響
素材の選定が適切でないと膜厚不均一が発生することがあります。
アルマイト処理の膜厚は、処理条件の調整によって精密にコントロール可能です。電流密度、処理時間、温度、素材などの要因を適切に管理することで、用途に応じた最適な膜厚を実現できます。膜厚の適切なコントロールは、製品性能を最大限に引き出し、コスト効率を高める重要な技術です。アルマイト処理を行う際には、処理条件を明確に設定し、プロセスを丁寧に管理することが求められます。
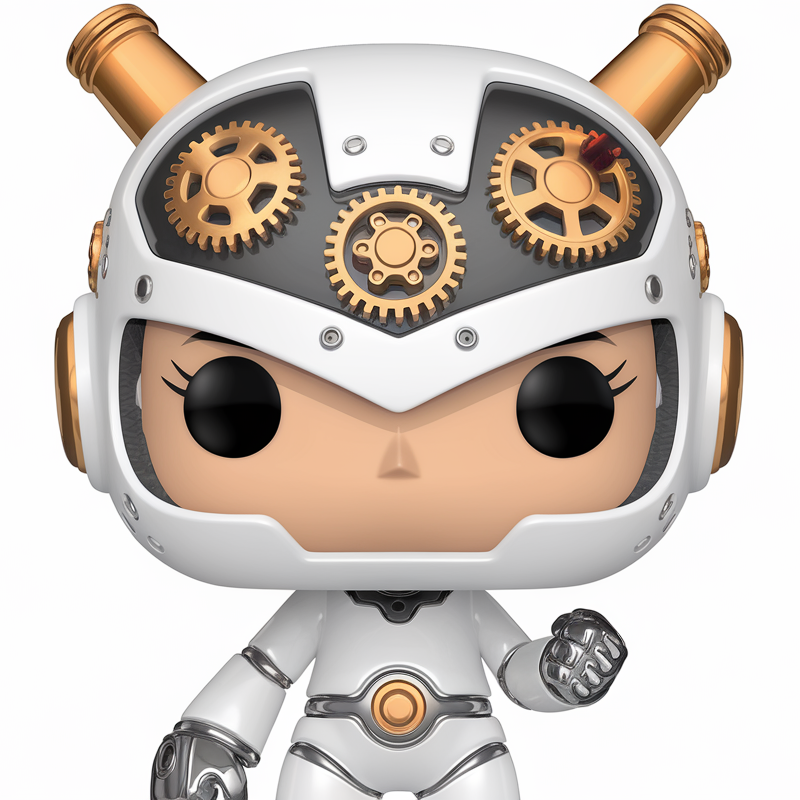
アルマイト処理はアルミニウムの表面を強化し、耐食性と美観を同時に実現する優れた処理方法です。
まとめ
アルマイト処理は、アルミニウム製品の耐食性、耐摩耗性、外観の改善、さらには絶縁性の付与など、さまざまな利点を提供する優れた表面処理方法です。
特に、腐食や摩耗が予想される環境で使用される部品や、外観や機能性が重要視される製品に最適です。
設計時には、使用環境や機能要件を踏まえてアルマイト処理を選択することで、部品の耐久性を高め、コスト効率を向上させることができます。
コメント