硬質クロムメッキは、機械設計において高い耐摩耗性や耐食性を求められる部品に広く使用される表面処理方法です。
クロムの硬度を利用して、部品の寿命を延ばし、過酷な使用環境でも安定した性能を維持することが可能です。
以下に、硬質クロムメッキ処理の特性と、材料選定における考慮すべきポイントを詳しく解説します。
硬質クロムメッキ処理(HCR)の特性
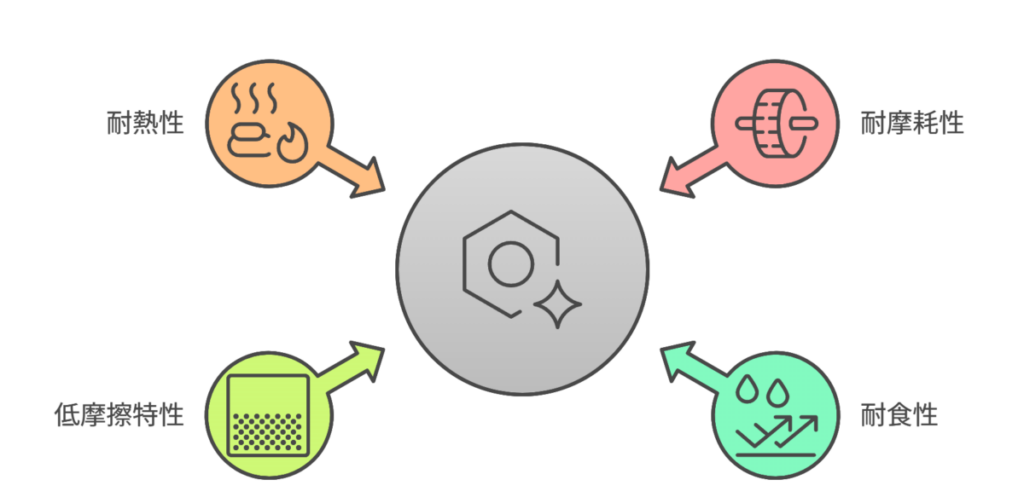
耐摩耗性の向上
- 硬質クロムメッキは、非常に硬度の高いクロム層を金属表面に形成させます。
- 摩擦や摩耗に対して優れた耐性を持ちます。
- 通常、クロムの硬度はHV800〜1000と非常に高く、摺動部品や接触が頻繁な部品に適します。
- 摩耗による寿命の延長が期待されます。
耐食性の向上
- クロムは優れた耐食性を持つため、硬質クロムメッキは腐食環境にも効果的です。
- 湿度の高い環境下で使用される部品には、この処理が最適です。
- クロム層が金属表面を保護し、錆や腐食の進行を防ぎます。
低摩擦特性
- 硬質クロムメッキの表面は非常に滑らかで、低摩擦特性を持つことが特長です。
- 摺動部品に適用することで摩擦を減少させ、エネルギー消費や熱の発生を抑制します。
- これにより、機械の効率を向上させる効果が期待できます。
耐熱性
- 硬質クロムメッキは耐熱性にも優れており、高温環境下でも性能が劣化しにくいです。
- 高温下で稼働する機械部品など、過酷な温度条件で使用される部品に対しても適用可能です。
硬質クロムメッキ処理の選定ポイント
使用環境
- 硬質クロムメッキは耐摩耗性と耐食性に優れているため、過酷な環境で使用される部品に最適です。
- 特に、摺動部品に対して、高い性能を発揮します。
- 耐熱性が必要な高温環境下でも安定した性能を維持できるため、産業用機械やエンジン部品にも適用されます。
機能要件
- 硬質クロムメッキは、膜厚が比較的薄くても高い耐摩耗性と耐食性を発揮するため、寸法精度が求められる部品にも適しています。
- 特に、表面硬度が求められるシャフトやピストン、プーリーなどの部品に対して有効です。
コスト管理
- 硬質クロムメッキは高性能である一方、処理コストはやや高めです。
- しかし、部品の寿命が大幅に延びるため、長期的なコスト削減が期待できます。
- 耐久性とメンテナンス頻度の削減を考慮すれば、コストパフォーマンスに優れた選択肢となります。
材質の適合性
- 硬質クロムメッキは、鉄鋼材料や工具鋼に適しています。
- 特に強度や硬度が必要な部品に対して効果的です。
- アルミニウムなどの非鉄金属には適用が難しいため、選定時には適合性を確認する必要があります。
硬質クロムメッキに適した材質とは?
効果を最大限引き出すための素材選び
硬質クロムメッキは、金属の表面に非常に硬いクロム層を形成して耐摩耗性や耐食性を高める表面処理です。
機械部品や金型、自動車部品など、摩擦や衝撃にさらされる箇所で多く使われます。
しかし、どんな材料にも向いているわけではありません。
本項では、硬質クロムメッキに適した材質についてわかりやすく解説します。
硬質クロムメッキとは?
- 表面硬度:Hv800〜1000程度(非常に硬い)
- 摩耗に強く、滑り性も良い
- 錆びにくく、見た目もきれい
- 薄膜(数μm〜数十μm)での処理が可能
そのため、寸法変化をほとんど起こさず、表面だけを強化できるのが特徴です。
硬質クロムメッキに適した材質
基本的には、鉄鋼材料全般が適しています。
特に、機械部品や金型など耐摩耗性が求められる部品に使われる鋼種と相性が良いです。
よく使われる適材例
材料 | 特徴 | 適性 |
---|---|---|
SS400(一般構造用圧延鋼材) | 衝撃や曲げ応力がかかる用途には不向き | ○ |
S45C(機械構造用炭素鋼) | 加工性が良く、強度も十分 | ◎ |
SCM材(クロムモリブデン鋼) | 耐摩耗・耐衝撃性が高い | ◎ |
SK材(工具鋼) | 硬度が高く、金型部品に多用 | ◎ |
SUS材(ステンレス鋼) | 耐食性が高く、錆びやすい環境でも安心 | ○ |
🔗SS400とは?特性・規格・他材料との比較から選定ポイントまで徹底解説!
🔗S45Cとは? 特性・焼入れ・規格・他材料との違いまで徹底解説!
🔗【クロモリ鋼】SCM440の特徴と選定ポイント【高強度・高靱性】
🔗SKS3とSK3の特性の違いと材料選定のポイントをわかりやすく解説!
🔗【ステンレス鋼】SUS304の特性と材料選定のポイント【耐食性】
適さない、または注意が必要な材質
- アルミや銅などの非鉄金属
→ 下地処理(ニッケルメッキなど)を挟まないと密着しにくい - 非常に硬い焼入れ鋼
→ クラックが入りやすいので処理条件の調整が必要 - 多孔質の鋳物
→ 表面の気孔が原因でメッキムラや剥がれの恐れあり
適材選びのポイント
- 密着性が高い素材を選ぶ
→ 鉄鋼材料は基本的に相性が良い - 使用環境に合わせる
→ 腐食環境ならSUS、強度重視ならSCMやSK材 - 下地処理を検討する
→ アルミや銅は無電解ニッケルなどで下地を作ってから処理
硬質クロムメッキに適しているのは、S45CやSCM、SK材などの鉄鋼材料が中心です。
非鉄金属や多孔質材でも処理は可能ですが、下地処理や条件調整が必須です。
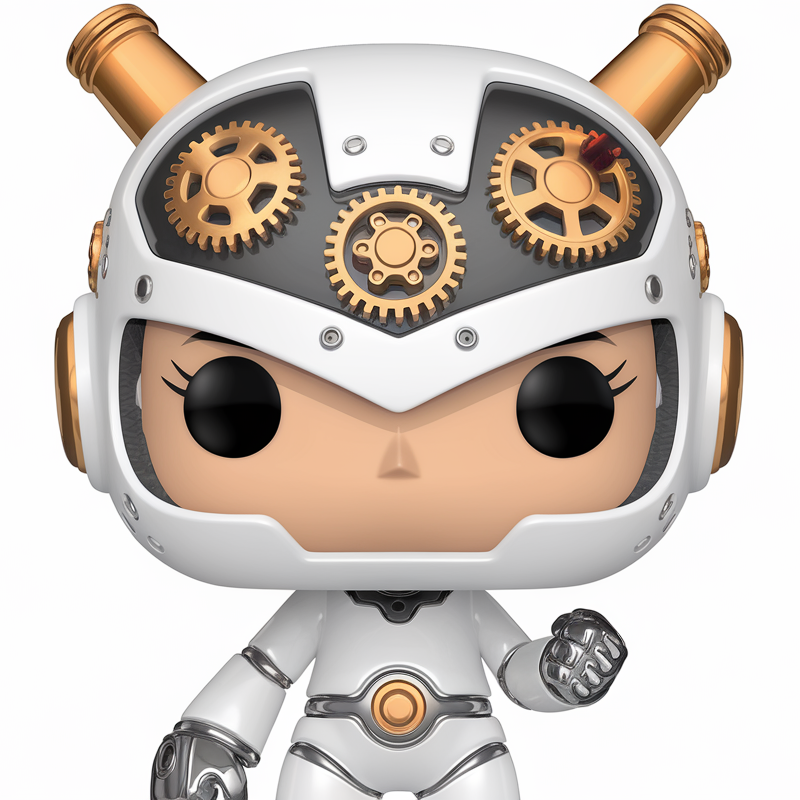
硬質クロムメッキは素材選び次第で、耐摩耗性・耐食性を大きく向上できる処理です。
特に機械設計では、材質+表面処理の組み合わせを意識すると、
部品寿命を大きく延ばせます。
硬質クロムメッキの部分的処理の特徴と利点
硬質クロムメッキは、高い耐摩耗性や耐食性を持つ表面処理として、機械部品や金型の寿命を延ばすために広く用いられています。
一般的には部品全体に施されることが多いですが、特定の部位のみに硬質クロムメッキを施す部分メッキも可能です。この技術は、特定の設計要件やコスト効率の向上を目的として使用されます。
以下では、部分メッキのメリットとデメリットについて詳しく解説します。
部分メッキのメリットとデメリット
メリット
✅コスト削減
- 部品全体ではなく必要な箇所だけにメッキを施すため、メッキ材料や加工工程の削減が可能です。
- 特に大きな部品や複雑な形状の部品ではコスト効率が高くなります。
✅設計要件への対応
- 部分メッキは、特定の箇所にのみ耐摩耗性や耐食性を付与したい場合に最適です。
- 例えば、回転部や摺動部のみが摩耗しやすい場合、そこにだけ処理を行うことで、余計な処理を省きつつ性能を向上させることができます。
✅機能的な最適化
- 部品の他の領域にメッキを施さないことで、機械特性を最適化できます。
- たとえば、メッキを施さない箇所は元の材質の特性(柔軟性や導電性など)を維持できます。
✅組み立て精度の確保
- ねじ部や嵌合部など、精密な寸法が求められる部分にメッキを施さないことで、組み立てのトラブルを回避できます。
- また、不要な箇所にメッキが施されると寸法が変わり、嵌合精度に影響を与える場合がありますが、部分メッキであればそのリスクを低減できます。
デメリット
🚫加工時間と工程の増加
- メッキを施さない箇所をマスキングする必要があるため、加工工程が複雑になります。
- このため、全体処理に比べて加工時間が増加する可能性があります。
🚫マスキングのコスト
- 特定の箇所をメッキから保護するためにマスキング材料や作業が必要です。
- このマスキング工程は精密であるほどコストが高くなります。
🚫接合部の弱点
- 部分メッキを施した際、メッキ処理が行われた箇所と行われなかった箇所の境界部分が弱点になることがあります。
- たとえば、境界部分での剥離や亀裂が発生しやすくなる可能性があります。
🚫制限された形状
- 複雑な形状の部品では、部分メッキの適用が難しい場合があります。
- 特に内部の狭い空間や曲面が多い部品では、均一なメッキを施すのが困難になることがあります。
部分メッキの活用例
🔍摺動部品
摩擦が発生する箇所のみメッキを施すことで、耐摩耗性を強化し、寿命を延ばす。
🔍ねじ部や嵌合部
メッキを施さないことで、精密な寸法を維持し、組み立てやメンテナンスを容易にする。
🔍金型
製品と接触する箇所にだけメッキを施すことで、耐摩耗性を確保しつつ、コストを削減する。
部分メッキのポイントと注意点
📌マスキングの精度
マスキングの精度が仕上がり品質を大きく左右します。
特に高精度が求められる部品では、熟練した技術者が必要です。
📌境界部の仕上げ
メッキの境界部分に不連続性が生じないよう、注意深く処理を行う必要があります。
📌用途に応じた選択
部品の使用環境や性能要件を十分に考慮し、部分メッキが適しているかどうかを判断します。
硬質クロムメッキの部分処理は、コスト効率の向上や機能的な特性の最適化を可能にする有効な手段です。ただし、加工工程が複雑になることや境界部分での問題などの課題も伴います。そのため、使用目的や部品の特性に応じて適切に判断し、工程管理を徹底することが重要です。適切に活用すれば、耐摩耗性や耐食性を必要な箇所に効率よく付与できる優れた技術です。
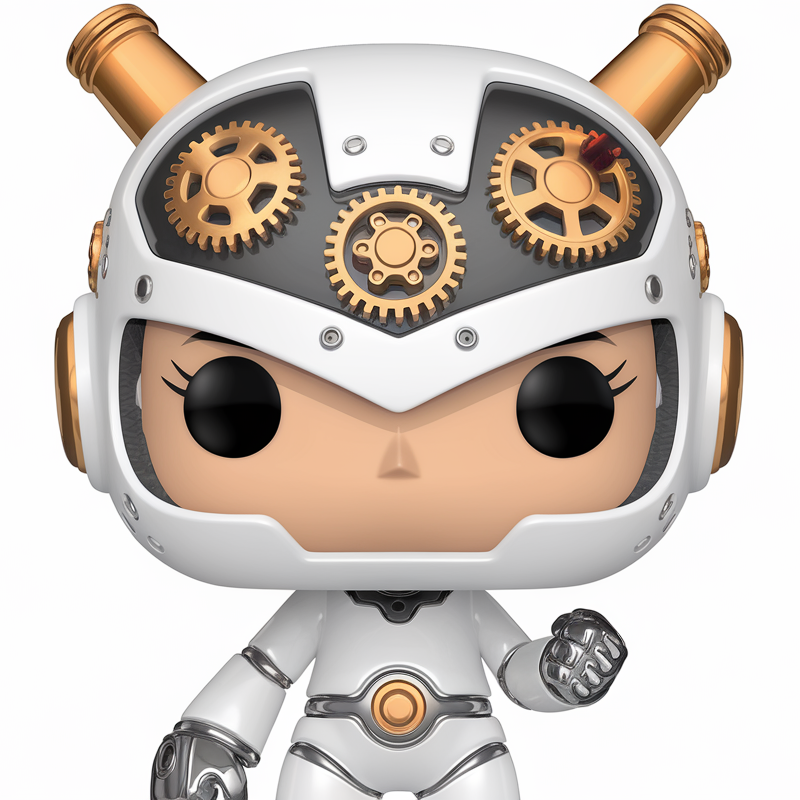
硬質クロムメッキは部分メッキにも対応できるため、
必要な面などを指示して適切に使用しましょう。
まとめ
硬質クロムメッキ処理は、優れた耐摩耗性、耐食性、耐熱性を提供する高性能な表面処理方法です。
特に、摺動部品や高温下で使用される部品に対して効果的で、部品の寿命を大幅に延ばすことが可能です。
設計時には、使用環境や機能要件を考慮し、硬質クロムメッキの適用を検討することで、耐久性と性能の向上を図ることができます。
コメント