機械設計において、材料選定は製品の性能や耐久性、コストに影響を与える非常に重要なプロセスです。その中で、規格寸法の材料を使用することは、製造性の観点から特に大きなメリットをもたらします。この記事では、製造性の向上という視点から、なぜ規格寸法の材料を使用することが重要なのかを解説します。
規格寸法の重要性
機械設計を行う際、材料選定と同様に重要なのが材料の規格寸法の考慮です。規格寸法は、設計の効率やコスト、加工の容易さに大きな影響を与えます。本項では、規格寸法の基本的な重要性や、設計プロセスでの具体的な活用方法について解説します。
規格寸法とは
規格寸法とは、JIS(日本工業規格)やISO(国際標準化機構)などの標準規格によって定められた材料の寸法です。たとえば、鋼材やアルミ材、プラスチック材には、それぞれ標準的な長さ・幅・厚さが規定されており、流通市場で入手可能な状態で製品化されています。
規格寸法を考慮することのメリット
✅コスト削減
- 規格寸法に準拠した材料は大量生産されているため、非標準寸法の材料に比べて価格が安いです。
- 規格寸法内で設計を完結させることで、特殊な加工や材料調達のコストを抑えることができます。
✅加工効率の向上
- 規格寸法に合った材料を使用すれば、切削や溶接などの加工工程が簡素化されます。
- 無駄な材料を削減できるため、加工時間も短縮できます。
✅材料調達の容易さ
- 標準的な規格寸法の材料は市場で容易に入手可能で、調達期間が短いです。
- 非規格品を選定した場合、調達が困難になり、設計プロジェクト全体の遅延を招くことがあります。
✅廃材の削減
- 設計時に規格寸法を考慮すれば、材料を効率的に利用でき、無駄を減らすことが可能です。
- 廃材を減らすことで、コスト面だけでなく環境負荷の軽減にも貢献します。
設計プロセスでの規格寸法の活用
📌設計段階での寸法確認
- 設計時に、選定した材料の規格寸法を確認し、それに合わせた設計を行います。
- 例えば、フレームの設計では、角パイプや丸パイプの規格寸法に基づいて部品サイズを調整します。
📌CADモデルでの寸法調整
- CADを使用して設計する際、規格寸法をそのまま適用するとモデル作成がスムーズになります。
- また、規格寸法に合わせることで、製図から実際の加工までの精度も向上します。
📌材料カットの最適化
- 大型の材料をカットして使用する場合、規格寸法を考慮することで、切り出しの効率が向上します。
- 例えば、2000×1000 mmの板材から効率的に部品を切り出せば、廃材の発生を抑えることができます。
規格寸法を適用できない場合のリスク
🚫コストの増加
非規格寸法の材料は、特注生産となるため価格が高くなります。また、加工が複雑になり、製造コストが増大するリスクがあります。
🚫納期遅延
特殊寸法の材料は、調達に時間がかかることが多く、プロジェクトのスケジュール全体に影響を与える可能性があります。
🚫加工や組立での問題
規格外の寸法を採用すると、加工精度や組立の適合性に問題が生じやすくなり、結果的に手戻り作業が発生することもあります。
規格寸法を活かした設計の工夫
👉複数部品の共通化
規格寸法を基準に複数部品を設計することで、同じ材料を流用しやすくなります。これにより、部品数や管理コストの削減が可能です。
👉最小限の加工で対応
材料の規格寸法をそのまま利用する場合、加工工程を減らせるため、時間やコストの削減につながります。
規格寸法がある材料の種類
🔗【SS400】平鋼の規格寸法【ミガキ】
🔗【S45C】 ミガキ丸棒の規格寸法と活用法【寸法表】
🔗【SUS304】平鋼の規格寸法
🔗【SUS304】平鋼と板の種類【HOT.COLD】
🔗【SPCC】板厚規格と特性と選定ポイント
🔗【キー材】キー材の規格寸法
🔗【山形鋼】アングルの規格寸法と選定ポイント【L字型断面】
🔗【溝形鋼】チャンネルの規格寸法と選定ポイント【U字型断面】
🔗【H鋼】H形鋼の規格寸法と選定ポイント【H型断面】
🔗【角パイプ】STKRの規格寸法と選定ポイント【箱型断面】
🔗【鉄パイプ】STKM13Aの規格寸法と選定ポイント【STKM】
🔗【配管材料】SGPの規格寸法と選定ポイント【鉄パイプ】
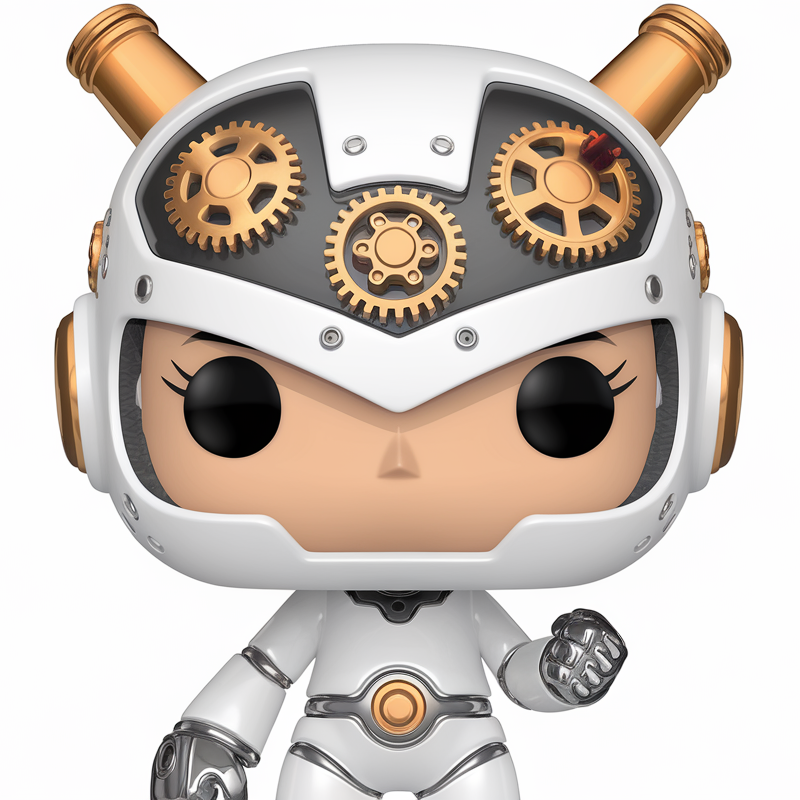
市販の規格寸法に合わせた設計を行うことで、材料調達が容易になりコスト削減につながります。
規格外の寸法が必要な場合、追加の加工や特注対応が必要となり、コストや納期に影響を与える可能性があります。
加工コストと時間の削減
規格寸法の材料を使用する最大の利点の一つは、加工コストと時間を大幅に削減できる点です。規格品の材料は、設計段階から製造工程での加工を見越して作られているため、追加の加工や特注の治具が不要な場合が多く、製造が効率的に進行します。
例えば、規格外の寸法の材料を使用すると、材料そのものを切削・成形する時間や、特殊な治具の設計・製作に時間がかかります。そのため、結果として製造コストが上昇し、納期が延びる可能性が高まります。規格寸法の材料を使用すれば、そのままの寸法で設計に組み込むことができ、加工の手間を減らすことでコストやリードタイムを抑えることが可能です。
標準工具との互換性
規格寸法の材料は、既存の工作機械や工具との互換性が保証されているため、特別な道具を使うことなく加工が可能です。これにより、標準的なフライス盤、旋盤、CNCマシンなどで加工がスムーズに進行します。標準工具の使用が可能であれば、加工精度が高く、再現性のある製造が実現します。
一方、規格外の寸法の材料は特別な工具が必要となる場合があり、設備投資や工具の調達に余計なコストがかかります。また、特注工具が適切に機能しない場合、再調整や再設計が必要になり、全体の製造プロセスに遅延をもたらします。
材料の安定供給と在庫管理の容易さ
規格寸法の材料は、市場に広く流通しているため、供給の安定性が高いです。一般的に使用される規格材料は、大量生産されているため、入手性が良く、サプライヤーが豊富です。これにより、材料の調達がスムーズになり、製造プロセスに遅延が発生しにくくなります。
さらに、規格寸法の材料を使用することで、在庫管理も容易になります。規格外の材料を使用すると、特殊な材料を確保しなければならず、万が一不足した場合にはリードタイムが大幅に延びるリスクがあります。しかし、規格品であれば常に入手可能であるため、在庫切れによる製造遅延を防ぎ、安定した生産体制を維持できます。
設計の柔軟性と変更への対応力
機械設計においては、製品の改良やカスタマイズが頻繁に行われることがあります。規格寸法の材料を使用することで、設計変更や改良に柔軟に対応できるメリットがあります。規格外の材料を使用すると、変更のたびに特注加工が必要となり、追加のコストや時間が発生することが多いですが、規格寸法の材料であれば、既存の在庫や標準的な部品をそのまま活用することが可能です。
品質と信頼性の向上
規格寸法の材料は、品質が安定しており、信頼性が高いことが保証されています。各規格に基づいて製造された材料は、強度、硬度、耐摩耗性、耐熱性などの特性が一定であるため、設計通りの性能を発揮します。特に、複数の部品が組み合わさる機械設計において、規格寸法の材料を使用することで、部品間のフィットが正確に行われ、設計通りの動作や寿命が期待できます。
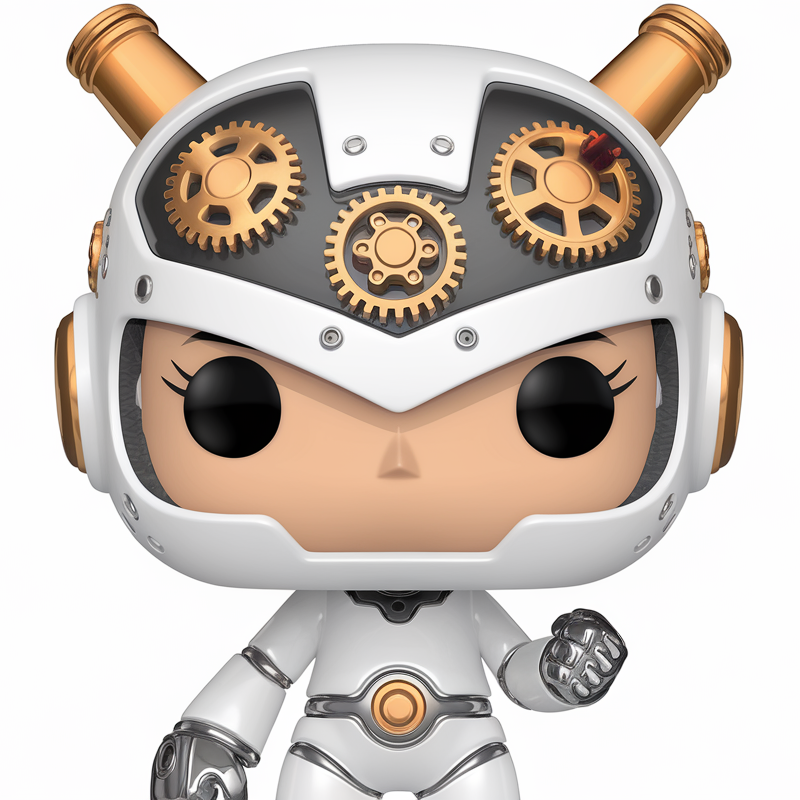
規格品を使用することで、製品の一貫した品質を保ちやすくなり、製造時の不良やトラブルの発生率を低減できます。これにより、顧客に対して高品質な製品を提供し、ブランドの信頼性を高めることができます。
まとめ
機械設計における材料選定において、規格寸法の材料を使用することは、製造性の向上に大きく寄与します。加工コストと時間の削減、標準工具との互換性、安定した材料供給、設計変更への柔軟性、そして品質の安定性といった多くのメリットがあります。規格寸法の材料を効果的に活用することで、効率的かつ信頼性の高い製品を製造し、競争力のある設計を実現することが可能です。
規格寸法の考慮は、機械設計において非常に重要な要素です。設計時に材料の規格寸法を正しく理解し、これを最大限に活用することで、コストの削減、効率的な材料利用、加工性の向上が実現します。また、規格寸法を意識した設計は、部品調達や加工の手間を軽減し、結果として設計全体の品質向上につながります。設計者は、規格寸法を活用しつつ、用途や性能要件に応じて最適な選択を行うことが求められます。
コメント