表面処理は、機械部品の耐食性や耐摩耗性を向上させ、長寿命化や見た目の改善を図るために重要な工程です。
適切な表面処理を選定し、設計時にその注意点を把握しておくことで、機械部品の性能と信頼性を高めることができます。
この記事では、表面処理を考慮した機械設計における注意点を解説します。
表面処理の選定時の注意点 5選
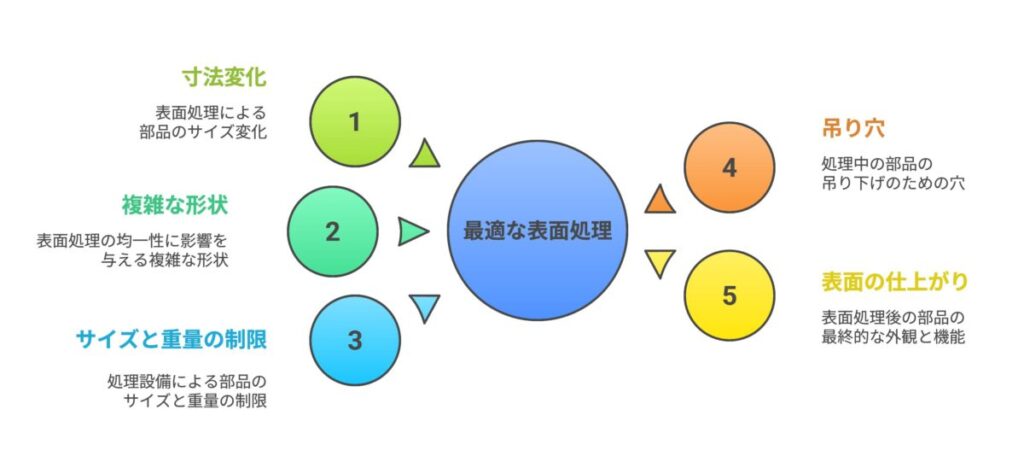
1.表面処理における寸法変化の考慮
メッキや塗装などの表面処理では、部品表面に物質が付着するため、寸法変化が発生します。この寸法変化を無視すると、精度の高い部品同士の組み合わせで不具合が生じる可能性があります。
寸法公差への影響
✅表面処理後の寸法変化を考慮した設計を行うことが必要です。
✅精度が必要な部品では寸法変化が少ない表面処理を選定するなど配慮が必要です。
重要な部分のマスキング処理
✅マスキング処理が可能かどうか、事前に確認しておくことが大切です。
✅ねじ穴や重要な接合面など、寸法が重要な箇所にはマスキング処理を施すことで、処理後も精度を維持することができます。
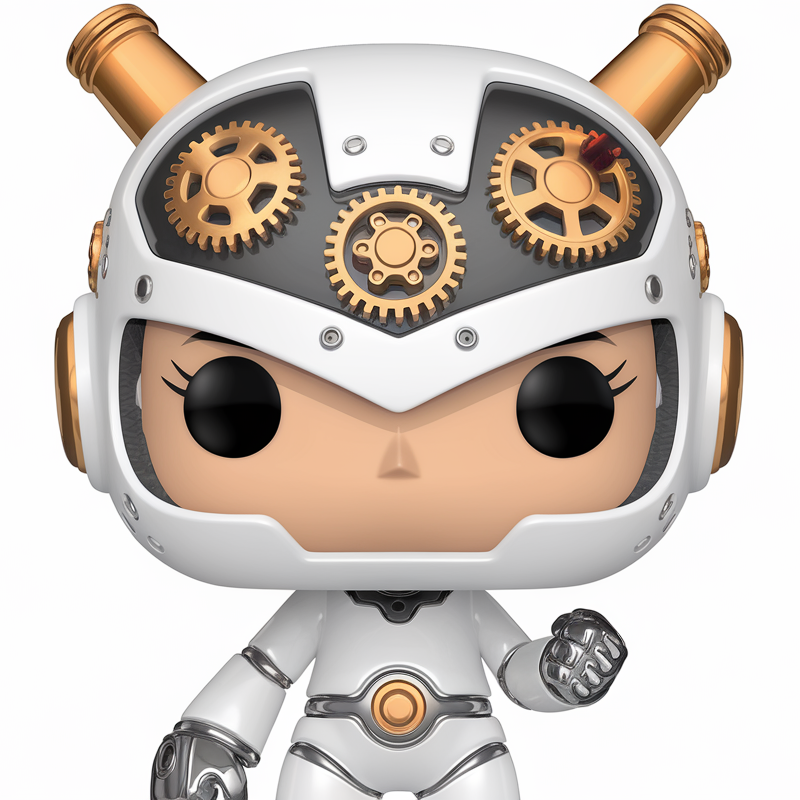
材質ごとに最適な処理を把握するとともに、寸法変化の有無についてもしっかり把握し最適な処理を選定するようにしましょう。
2.凹凸や複雑形状の処理
部品に複雑な形状や凹凸がある場合、表面処理が不均一になるリスクがあります。特に、メッキや塗装においては、部品の隅や狭い部分に処理液が均一に届かないことがあります。
均一な処理のための設計
✅凹凸や狭い部分を極力避けるか、形状を簡素化することが表面処理の均一性を高めます。
✅どうしても複雑な形状が必要な場合は、処理方法や装置の工夫が必要になるため、業者と相談し最適な方法を選定しましょう。
通気口や排出穴の設置
✅凹部に処理液が溜まってしまうと、表面が不均一になったり処理不良が発生することがあります。
✅これを避けるために、通気口や排出穴を設け、液体の循環を促す設計が重要です。
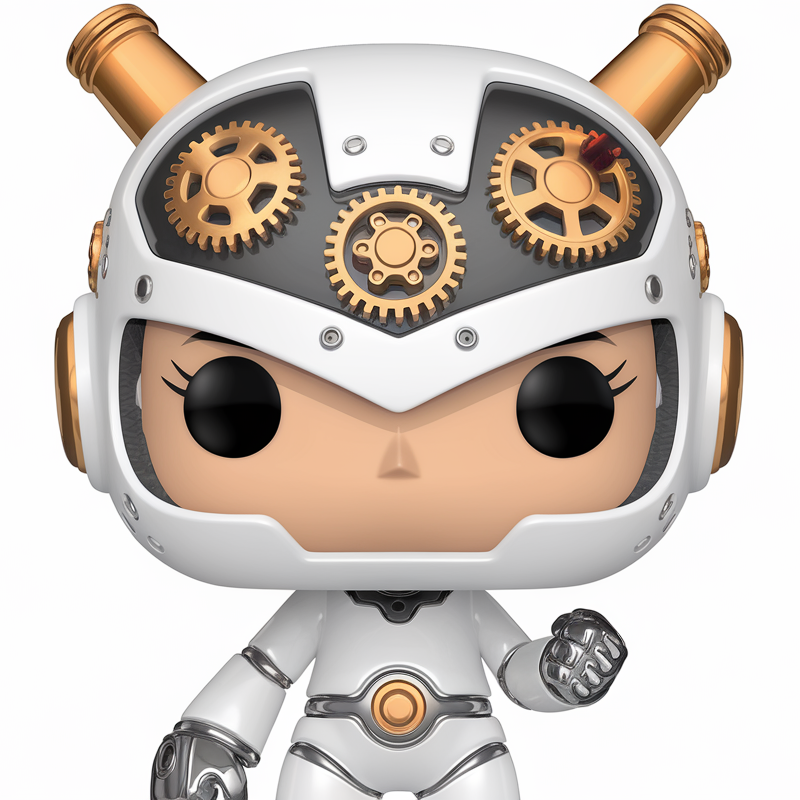
処理業者に相談するとともに、経験や感覚を身に付け、最適な形状を設計できるよう心がけましょう。
3.処理可能な最大サイズと重量
表面処理の設備には、処理できる部品の最大サイズや重量に制限があります。これは、処理槽の大きさや吊り下げ治具の耐荷重、または処理工程全体の制約によるものです。
設備の制限に注意
✅表面処理業者ごとに、最大サイズや重量の制約が異なるため、事前に確認しておくことが重要です。
✅特に大きな部品や重量のある部品は、専用の設備が必要な場合があるため、設計段階で対応可能な処理業者を選定しておくとスムーズです。
サイズや重量に応じた設計の工夫
✅部品を複数のパーツに分割して製作し、表面処理後に組み立てる方法も考慮しましょう。
✅これにより、設備の制約を回避しつつ、必要な機械性能を保つことが可能です。
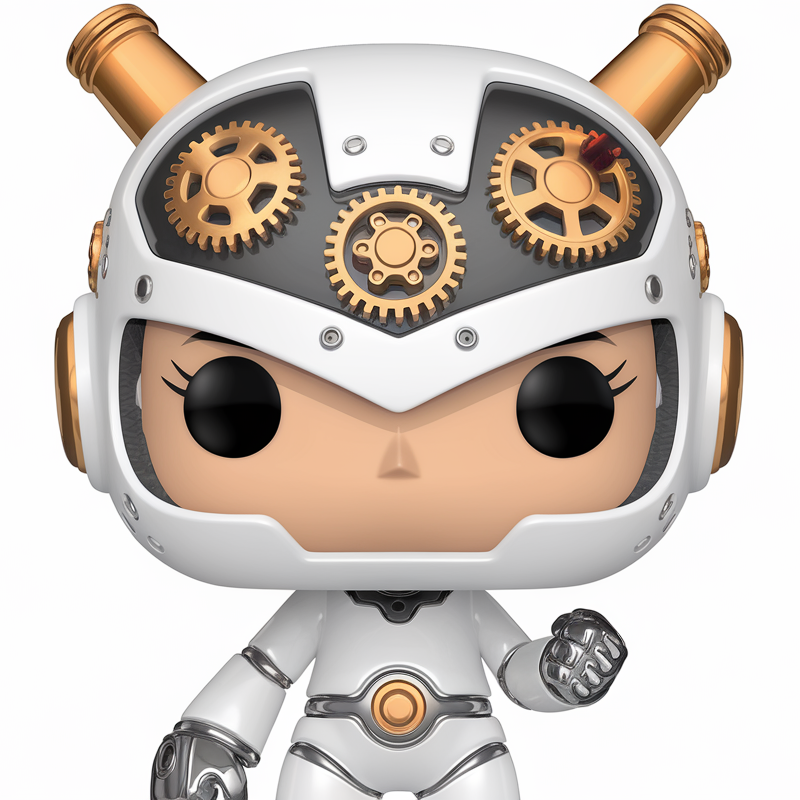
取引先の業者の処理槽の大きさなど把握し、処理可能サイズでの設計を行いましょう。
4.吊り穴の設置
表面処理(特にメッキや塗装)を行う際、部品を処理液や塗料に浸漬する工程が必要です。この際、部品を吊り下げるための吊り穴を設置しておく必要があります。
- 吊り穴の位置
- 吊り穴は、加工後に使用上影響がない箇所、または目立たない箇所に設けることが理想的です。
- 重要な締結部や精度が求められる面には、吊り穴が干渉しないように設計することが求められます。
- 吊り穴のサイズ
- 吊り穴は、部品の重量や形状に応じた強度を確保するために十分な大きさでなければなりません。
- ただし、必要以上に大きな穴を開けると、製品強度に悪影響を及ぼす可能性があるため、注意が必要です。
- 吊り穴が不要な場合の対応
- 一部の表面処理業者では、部品の形状や重量に応じて、特殊な治具で吊り下げることが可能です。
- この場合、吊り穴を設置しなくても処理ができることがありますので、業者と事前に相談しましょう。
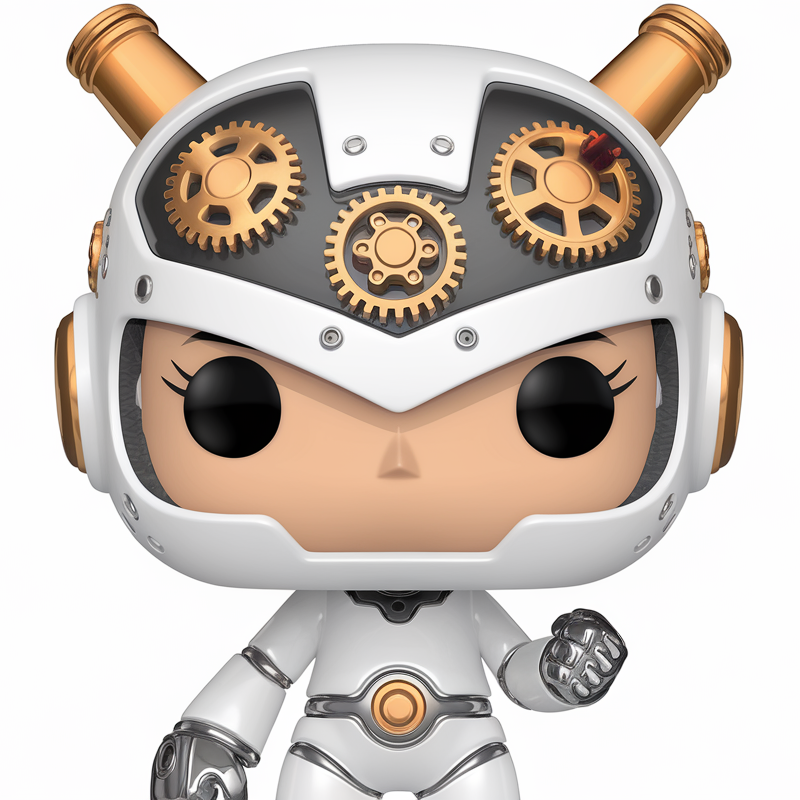
基本的には、もともと加工してある穴で対応してくれるとおもいます。穴がない部品などは処理業者に相談しよう。
5.表面処理後の仕上がりと機能
表面処理は、単に見た目や耐食性を向上させるだけでなく、部品の機能にも影響を与えることがあります。例えば、表面硬度を高める処理や、滑りやすさを向上させる処理などが挙げられます。
- 処理方法と機能の適合性
目的に応じた表面処理を選ぶことで、部品の性能を最大限に発揮できます。例えば、耐摩耗性を求める場合は硬質クロムメッキ、耐食性を高めるなら無電解ニッケルメッキなど、部品の使用環境に合わせて最適な処理を選定しましょう。
材料の表面処理(メッキ、塗装)の注意点
表面処理は、機械部品の耐久性、耐食性、美観、性能を向上させるための重要な工程です。しかし、適切な処理方法を選定しなければ、設計や機能に悪影響を及ぼす可能性があります。本項では、メッキや塗装といった表面処理における注意点を解説します。
表面処理の基本的な目的
表面処理の目的は以下の通りです:
- 耐食性の向上
- 環境による腐食(錆)から部品を保護する。
- 耐摩耗性の向上
- 接触や摩擦による部品の損耗を防ぐ。
- 外観の向上
- 美しい仕上げを施し、製品の価値を高める。
- 特殊な性能の付与
- 電気伝導性や絶縁性、非粘着性などを追加する。
表面処理ごとの注意点
メッキ処理
メッキは、部品の表面に金属を付着させる処理で、耐食性や耐摩耗性を向上させます。
代表的なメッキ処理には、電気メッキ(亜鉛、ニッケル、クロムなど)や無電解メッキがあります。
注意点
- 寸法変化に注意する
- メッキは部品の表面に層を形成するため、寸法が増加します。
- 設計段階で膜厚を考慮し、加工寸法を調整する必要があります。
- エッジ部の膜厚不足
- メッキ処理では、エッジ部(角部)や深い溝内で膜厚が均一にならない場合があります。
- 設計時にR加工や隅部の形状を工夫すると効果的です。
- 耐久性の限界
- 使用環境に応じたメッキを選定する必要があります。
- 亜鉛メッキは比較的安価ですが、耐食性が限られるため、過酷な環境ではニッケルメッキやクロムメッキが推奨されます。
塗装処理
塗装は、塗料を部品表面に塗布し、乾燥または硬化させて膜を形成する方法です。防錆性、美観、耐薬品性を向上させることが主な目的です。
注意点
- 表面下地の仕上げ
- 塗装の仕上がりは、下地処理に大きく依存します。
- 塗装前に脱脂処理やサンドブラストで表面を清浄化し、密着性を高めることが重要です。
- 膜厚管理
- 膜厚が不均一だと、美観や防錆効果に影響します。
- 厚すぎる塗膜は割れや剥がれの原因になります。
- 環境への適応性
- 使用環境に応じて塗料を選ぶ必要があります。
- 紫外線にさらされる屋外環境では、耐候性塗料が適しています。
- 耐薬品性の限界
- 塗料は特定の薬品に対する耐性があり、それを超える環境では劣化します。
- 化学プラントなどでは特に注意が必要です。
共通の注意点
表面処理後の寸法公差の管理
表面処理によって寸法が変化するため、仕上がり後の公差を満たすよう、事前に設計寸法を調整する必要があります。
例:H7のような精密な公差が求められる場合、表面処理前の加工寸法を適切に設定します。
部品の用途に適した選定
表面処理の種類は多岐にわたるため、部品の使用環境や機能に応じた適切な処理を選定することが重要です。コストも考慮して最適な方法を検討します。
接触部での考慮
塗装やメッキで滑らかな表面が形成される場合、摩擦力が低下し、滑りやすくなることがあります。特に締結部やトルク伝達部では、滑り止めの追加処理を検討してください。
耐久性の限界
どの表面処理も永久的ではありません。耐久年数や保守頻度を考慮し、適切なメンテナンス計画を立てることが必要です。
コストと作業性のバランス
高度な表面処理ほどコストが高くなるため、設計段階で処理の必要性を検討し、過剰仕様を避けることが重要です。
メッキや塗装といった表面処理は、材料の性能を大きく向上させる手段ですが、設計段階でその影響を十分考慮することが重要です。
寸法公差、耐久性、加工性、コストのバランスを見極め、適切な処理方法を選定することで、部品の品質と機能を最大限に引き出すことができます。
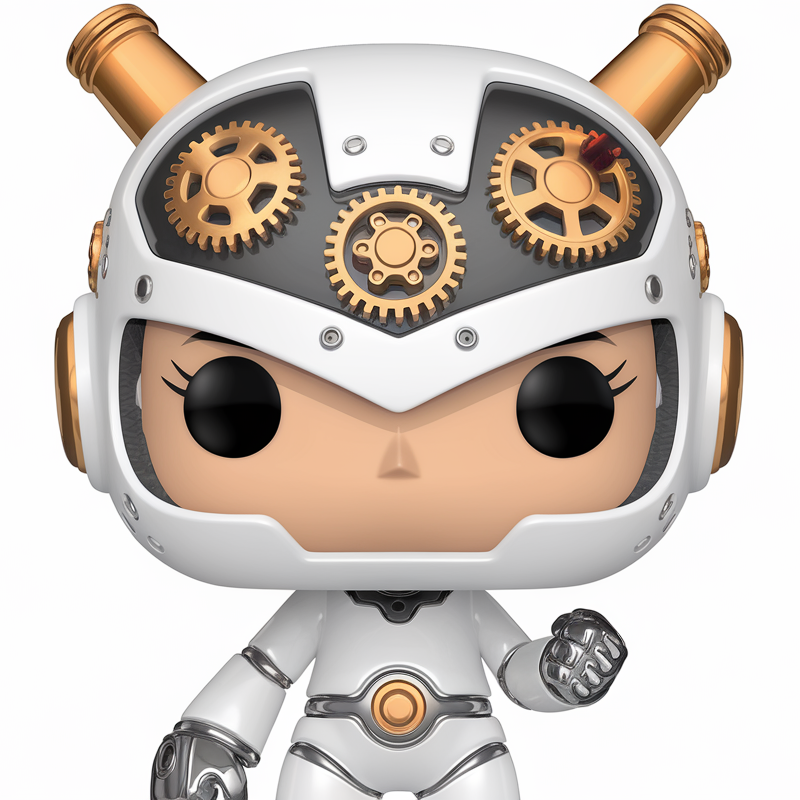
表面処理は製品の長期的な耐久性やメンテナンス性に直結するため、機械設計者としてはその選定と設計に注意を払うことが求められます。
まとめ
表面処理は、機械設計において部品の寿命や性能を左右する重要な要素です。吊り穴の設置、最大サイズや重量の制限、寸法変化の考慮、そして複雑な形状に対する均一な処理など、設計段階で注意すべき点は多岐にわたります。これらのポイントを考慮し、適切な表面処理を選定することで、機械設計の信頼性を高めることができます。
コメント