機械設計においてよく使う代表的な材料の硬度ランキングを、高い硬度から低い硬度の順に以下に示します。
異なる硬度尺度(ロックウェル硬度 HRC、ビッカース硬度 HB)を使用しているため、比較の際には目安値としてご参考ください。
硬度比較表【HRC・HB】
No. | 材質 | 硬度(目安値) | 備考 |
1 | SKD11 | HRC58-62 | 熱処理後 |
1 | SKS3 | HRC58-62 | 熱処理後 |
3 | SCM440 | HRC50-55 | 熱処理後 |
4 | S45C | HRC40-45 | 熱処理後 |
5 | NAK55 | HRC37-43 | 処理なし |
6 | SUS304 | HB187 | 処理なし |
7 | A7075 | HB150 | 処理なし |
8 | SS400 | HB130 | 処理なし |
9 | A5052 | HB68 | 処理なし |
※目安:HRC10≈HB200程度
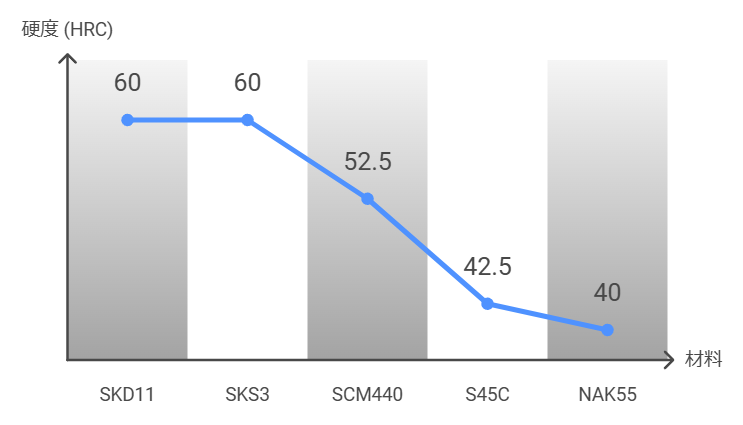
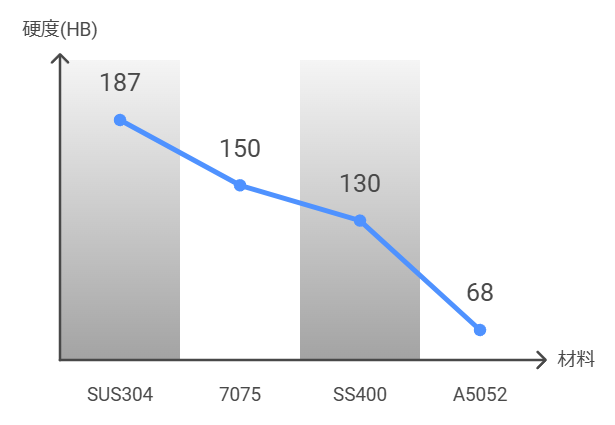
注意点
✅硬度尺度の違い
- 異なる硬度測定尺度(HRC、HB)は直接比較が難しいため、概算値としての順位付けになります。
✅熱処理の影響
- 一部の材料(例:S45C、SCM440)は熱処理により硬度が大きく変化します。
- 使用条件に応じた処理が必要です。
✅用途に応じた選定
- 硬度だけでなく、靭性、耐摩耗性、耐食性など他の機械的特性も考慮して材料を選定してください。
機械設計における材料選定と硬度の重要性
硬度とは?
硬度とは、材料の表面が他の物体によって変形(押し込まれたり、傷つけられたり)しにくい性質を表す指標です。一般的な硬度測定には以下のような方法が使われます。
📌ロックウェル硬度(HRC)
- 鋼材などの硬さを測定する際によく使用され、工具や部品の強度評価に使われます。
📌ブリネル硬度(HB)
- 柔らかい金属やプラスチックの硬度を測定する際に適しています。
📌ビッカース硬度(HV)
- 硬度が非常に高い材料に適し、微細な部品や特殊材料の硬度評価に使用されます。
硬度は材料の他の特性(耐摩耗性や耐久性など)と密接に関連しているため、設計段階での材料選定に大きく影響します。
硬度が重要な理由
✅ 耐摩耗性の向上
硬度が高い材料は、摩耗に対して強い耐性を持ちます。これは、機械部品が長期間にわたって摩擦や接触の影響を受ける環境下で重要です。例えば、ギアやベアリングのような高摩耗環境で使用される部品は、高硬度材料が適しています。硬度が高いほど、摩耗に対しての寿命が延び、メンテナンスコストや交換頻度が減少します。
✅ 変形に対する抵抗
硬度の高い材料は、外部からの圧力や衝撃に対して変形しにくい特性を持ちます。これにより、精密部品や強度が要求される機械構造部品に使用されることが多いです。例えば、プレス機の金型や工具類は、高い硬度を持つことで繰り返しの圧力にも耐えることができます。
✅ 耐傷性と外観の維持
外部からの衝撃や擦れによって表面が傷つきやすい製品では、硬度の高い材料を選定することが有効です。これにより、美観を長期間維持することができ、特に装飾やデザインに関連する部品では重要なポイントとなります。例えば、ステンレス鋼や硬化処理を施したアルミニウム合金などがこの目的に使用されます。
硬度と他の機械的特性のバランス
ただし、硬度が高ければ必ずしもその材料がすべての設計要件を満たすわけではありません。硬度が高い材料は、その分だけ脆くなることがあり、衝撃や引張り強度が低下することがあります。そのため、硬度と靭性、延性、耐衝撃性などの特性とのバランスが重要です。
例えば、以下のような材料選定の例があります。
高硬度材料
SKD11やSKS3などの工具鋼は、硬度が高く耐摩耗性に優れていますが、脆さがあるため、衝撃の加わる用途では破損のリスクがあります。
中程度の硬度材料
S45CやSCM440などは、熱処理によって硬度を調整でき、適度な硬度と靭性を持つため、一般的な機械構造部品に広く使用されています。
低硬度材料
SS400やA5052などは、硬度が低いため加工性や成形性に優れていますが、摩耗や変形に対する耐性が低いため、強度や耐摩耗性がそれほど要求されない部品に使用されます。
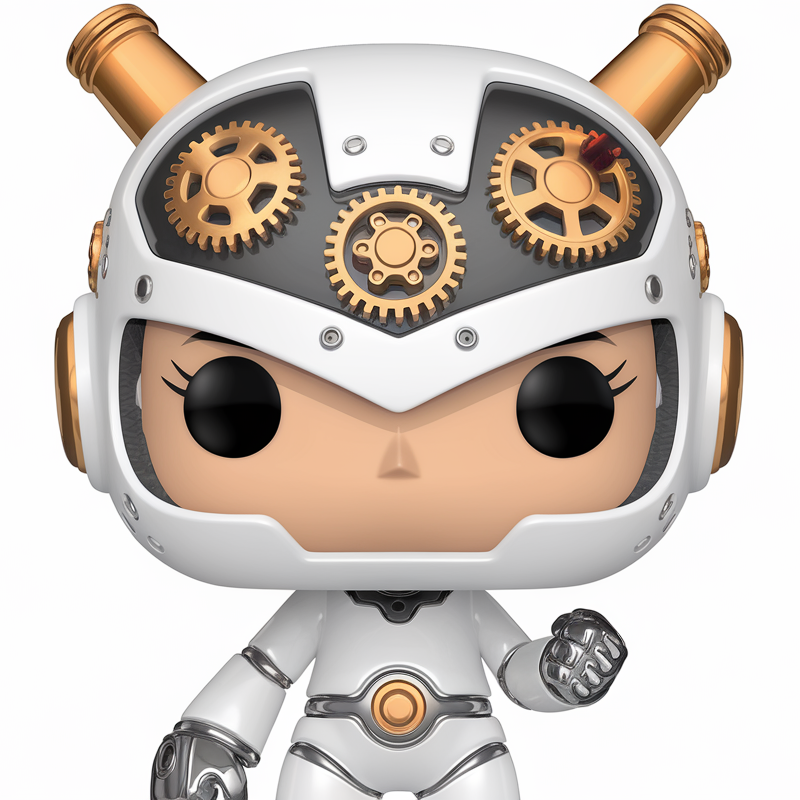
材料別の特性については下記の記事をチェックしてください。
硬度を付与する熱処理・表面処理
機械設計において、材料の特性を最適化するために、硬度を高める熱処理や表面処理は重要な技術です。硬度は材料の耐摩耗性や耐久性に大きな影響を与えるため、製品の信頼性や寿命に直結します。
熱処理による硬度付与
熱処理は、金属材料の内部構造を変化させ、硬度や靭性などの機械的特性を改善するプロセスです。
表面処理による硬度付与
表面処理は、材料の表面を加工して硬度や耐摩耗性を向上させる技術です。熱処理とは異なり、表面のみを硬化させるため、内部は柔軟性を保持できる点が特徴です。
材料硬度と摩耗対策:摺動部品の設計ポイント
材料硬度は、摺動部品の摩耗や耐久性に大きく影響します。摺動部品を適切に設計するためには、材料硬度の選定と摩耗対策が重要です。本記事では、 「硬度差を利用した摩耗対策」 と 「消耗部品と耐久部品の区別」 について詳しく解説します。これらの考え方を取り入れることで、メンテナンス性と製品寿命の向上が期待できます。
摩耗対策の基本原則
摺動する材料同士の摩耗を最小限に抑えるためには、材料の硬度や表面処理、潤滑の選定が重要です。特に以下の2つのアプローチは、機械設計において効果的です。
📌硬度差を利用した設計
同程度の硬度の材料を摺動させると、摩耗が双方に分散し、結果として部品全体の寿命が短くなることがあります。このため、 硬度差を設けることで摩耗する側を交換しやすい消耗部品にする 方法が広く採用されています。
💡ポイント
- 硬い部品と柔らかい部品の組み合わせ
- 硬い部品を耐久部品として保護し、柔らかい部品(消耗部品)が摩耗する設計にする。
- 例:鋼製シャフト(耐久部品)と樹脂製ブッシュ(消耗部品)。
- 交換部品のコスト削減
- 摩耗しやすい部品を簡単に交換できる設計とし、修理コストやメンテナンス時間を削減する。
📌消耗部品と耐久部品の区別を明確にする
機械設計では、 消耗部品(交換を前提とした部品) と 耐久部品(長寿命で保護すべき部品) を明確に区別することが重要です。これにより、摩耗管理やメンテナンスの計画が立てやすくなります。
💡ポイント
- 耐久部品には表面処理や高硬度材を使用する
- 例:シャフトやギアには熱処理(浸炭焼入れ、窒化処理)を施し、硬度を高めて摩耗を防止する。
- 消耗部品の設計を容易にする
- 例:ブッシュやパッキンなど、摩耗部品を取り外しやすい設計にする。
- 部品同士の硬度差を適切に設定する
- 硬度差が小さすぎる場合、双方が摩耗する可能性があるため、目安として HV200以上の硬度差 を持たせることが推奨されます。
設計の具体例
🔍 硬度差を活かした摺動部品の例
耐久部品 | 消耗部品 | 摩耗対策 |
---|---|---|
硬質クロムメッキを施した鋼製シャフト | 樹脂製ブッシュ | 樹脂ブッシュが摩耗したら交換 |
硬度の高い工具鋼製ギア | 銅合金製ベアリング | ベアリングを消耗品として設計 |
硬化処理したローラー | 軟鋼製サポートプレート | サポートプレート側を交換部品とする |
🔍 耐久部品を保護するための表面処理例
- 浸炭焼入れ:歯車やシャフトの表面を硬化させ、摩耗に強くする。
- 窒化処理:耐摩耗性や耐疲労性を向上。
- 硬質クロムメッキ:摺動部の耐摩耗性を向上。
注意点と設計時の工夫
🚫硬度差が大きすぎる場合のトラブル
- 硬度差が大きすぎると、柔らかい部品が急激に摩耗する可能性があるため、適切な潤滑や設計が必要です。
🚫潤滑剤の選定
- 硬度差を活用する場合でも、適切な潤滑剤を使用して摩擦を軽減することで、寿命を延ばせます。
🚫メンテナンス性を考慮する
- 消耗部品を簡単に交換できる構造にすることで、ダウンタイムを最小限に抑えられます。
まとめ
硬度は、機械設計における材料選定時に非常に重要な要素です。耐摩耗性や耐変形性を重視する用途では、高硬度材料が選ばれますが、他の機械的特性とのバランスを取ることが不可欠です。さらに、熱処理、表面処理や材料の種類によって硬度を調整することで、適切な性能を持つ材料を選定することが可能です。最適な材料選定は、製品の性能と寿命を最大限に引き出す鍵となります。
摩耗対策について
機械設計において、摺動部品の摩耗対策は信頼性とコスト管理において重要な要素です。硬度差を利用することで、消耗部品を交換しやすくし、耐久部品を保護する設計が可能になります。特に、消耗部品と耐久部品を明確に区別することは、メンテナンスの効率化やトラブルの予防につながります。
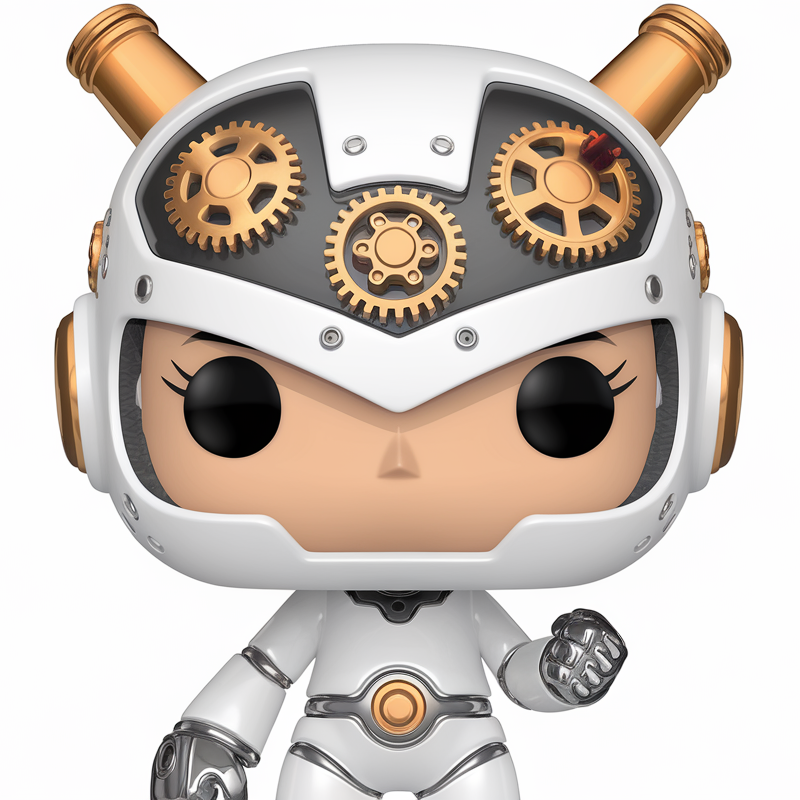
適切な硬度差の設定や潤滑剤の選定、さらには交換のしやすい設計を心掛けることで、機械の寿命とパフォーマンスを向上させましょう。
コメント