無電解ニッケルメッキは、機械設計において広く採用される表面処理方法の一つであり、金属部品に均一なニッケル層を形成することで、耐食性の向上や耐摩耗特性の改善が期待されます。は、多様な金属に対して適用できるため、非常に汎用性の高い表面処理です。以下に、無電解ニッケルメッキの特性と、材料選定における検討すべきポイントを詳しく解説します。
無電解ニッケルメッキとは?
「無電解ニッケルメッキ」とは、電気を使わず化学反応だけでニッケルの皮膜を素材に均一にコーティングする処理方法です。
- 電気を使わない → 複雑な形状にもムラなく均一な膜ができる
- 硬度が高く、耐摩耗性・耐食性が向上する
- 寸法変化が小さく、精密部品にも適している
そのため、精密機械部品・金型・電子部品など、さまざまな分野で使用されています。
無電解ニッケルメッキの特性
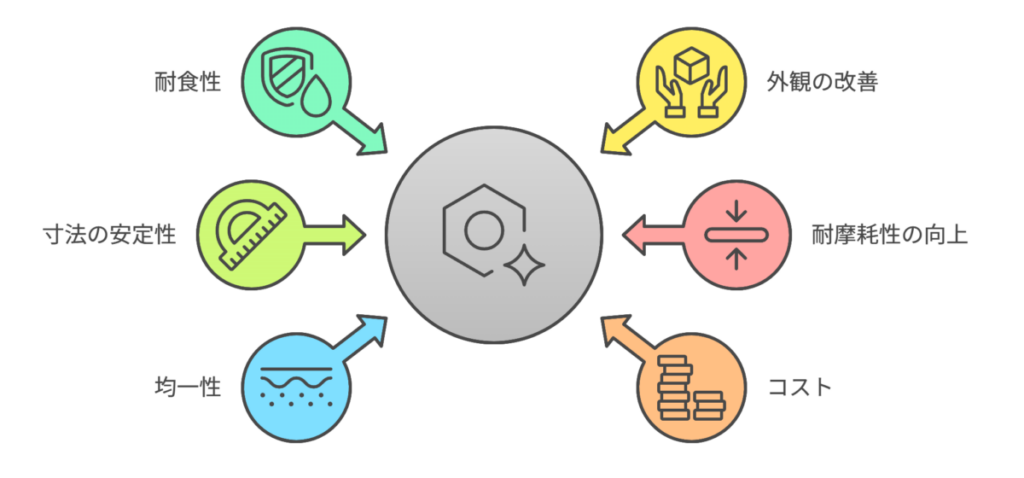
耐食性の向上
- 金属表面に化学的に均一なニッケル層を形成し、優れた耐食性を提供します。
- 特に、湿気や腐食性のある環境下での使用に適しています。
外観の改善
- メッキの表面は緩やかで光沢があり、見た目の美しさが求められる部品に適しています。
- 必要に応じてマット仕上げや光沢仕上げなど、様々な仕上げが可能です。
寸法の安定性
- 無電解ニッケルメッキは、均一な膜厚を形成できる。
- 複雑な形状や細かい寸法の部品でも、正確な仕上がりが得られます。
- 一般的な膜厚は5〜25μm程度ですが、目的に応じて調整可能です。
耐摩耗性の向上
- メッキ層は硬く、耐摩耗性に優れています。
- 特に熱処理を行うことで硬度がさらに向上し、摩耗性が求められる部品に適しています。
均一性
- 電解メッキとは異なり、無電解ニッケルメッキは電流を使用しないため、複雑な形状や凹凸部分にも均一にメッキを行うことができます。
コスト
- ほかのメッキにと比べると比較的コストは高い。
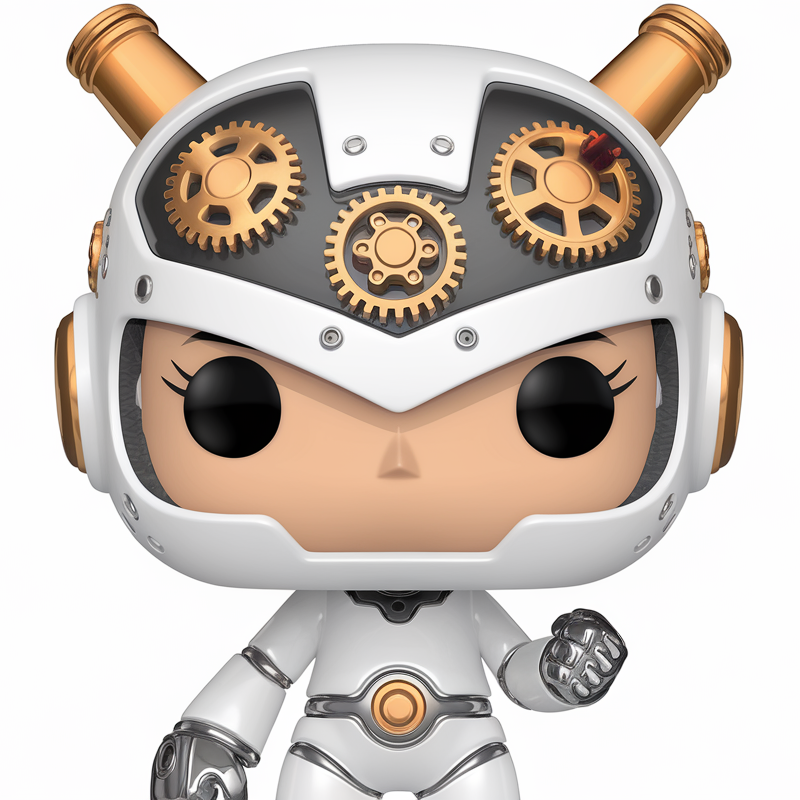
処理による寸法変化も少なく、耐食性も優れた黒染めの上位互換!
コストさえ気にしなければオススメの処理です。
無電解ニッケルメッキは“下地選び”と“前処理”が重要!
無電解ニッケルメッキは、金属素材であれば幅広く対応可能ですが、
特に以下の材質とは相性が良く、よく使われています。
無電解ニッケルメッキに適した材質
炭素鋼(SS400、S45Cなど)
- 最も一般的な鉄鋼材料。
- 無電解ニッケルメッキにより耐摩耗性・耐食性が大幅にアップ。
- 軸・ギヤ・ブラケットなど、強度が必要な機械部品に多く使われます。
📌 ポイント:前処理(脱脂・酸洗い)が丁寧にされていれば、メッキ密着性も良好。
合金鋼(SCM435、SCM440など)
- 熱処理による高強度が特徴の鋼材。
- 無電解ニッケルでさらに表面硬度や錆びにくさが向上。
- 強度と耐摩耗が求められる構造部品や金型に多用されます。
無電解ニッケルメッキに不向きな素材
以下の素材は、そのままでは無電解ニッケルメッキに不向きですが、
適切な前処理を行えば対応可能な場合もあります。
素材 | 理由 | 備考 |
---|---|---|
プラスチック類 | 金属ではないため化学反応しない | メッキ用下地塗装が必要 |
セラミックス | 非導電性・化学反応しない | 種類や状態によって適切な前処理が必要 |
焼入れ後鋼材 | 表面酸化皮膜により密着性低下 | 酸洗・活性化処理で改善可能 |
設計者へのアドバイス
ただし、素材と前処理の相性が重要なので、図面に材質を明記したうえで、表面処理業者と事前相談するのがベストです。
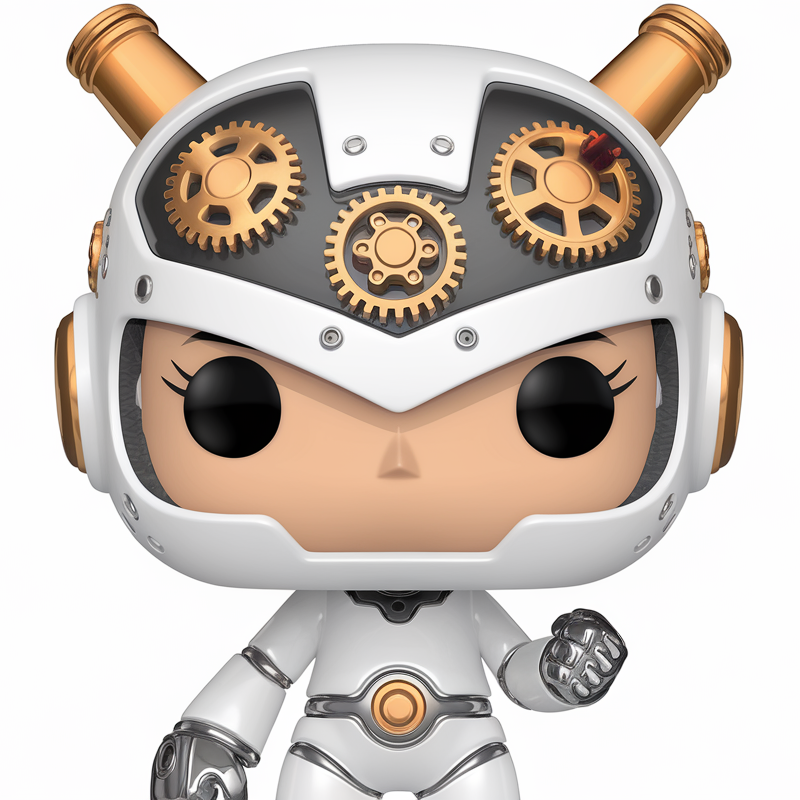
「強度はあるが錆びやすい」「表面がすぐに摩耗する」といった問題は、
無電解ニッケルメッキでかなり解決できます。
無電解ニッケルの選定ポイント
使用環境
- 耐久性に優れているので、耐食性、耐摩耗性、精度が求められる部品に適しています。
機能要件
- 処理後の寸法変化が少ない為、はめあい公差など寸法精度が必要な部品に適しています。
コスト管理
- 無電解ニッケルメッキは、一般的な電解メッキに比べてコストが高くなります。
- 耐久性や性能を向上させるために、長期的にはコストパフォーマンスに優れる選択肢です。
材質の適合性
- 無電解ニッケルメッキは主に鉄系の金属への処理が効果的です。
耐食性が向上する理由
密度が高いめっき層
無電解ニッケルめっきの層は、非常に高密度で均一な構造を持っています。
このため、微細なピンホールや欠陥がほとんどなく、腐食因子(酸素、水分、化学物質など)が基材に達することを防ぎます。
🔍高密度な層の形成
化学反応により、金属表面全体で同じ速度でニッケルが析出するため、隙間のない連続的な被膜が形成されます。
腐食耐性を高めるリンの効果
無電解ニッケルめっきには、リン(P)が含まれている場合が多く、このリンが耐食性を大きく向上させます。
🔍リン含有量と耐食性の関係
- めっき層のリン含有量が高いほど、腐食耐性が向上します。
- これは、リンがニッケル層を非晶質(アモルファス)構造にし、腐食因子が侵入しにくくなるためです。
🔍リン含有量の種類
- 低リンタイプ(1~5%): 硬度や耐摩耗性に優れるが、耐食性は中程度。
- 中リンタイプ(6~9%): 耐食性と硬度のバランスが良い。
- 高リンタイプ(10~13%): 耐食性が最も高く、特に酸やアルカリに強い。
均一な膜厚による基材の保護
無電解ニッケルめっきは、複雑な形状や凹凸、内部の穴に至るまで、均一な膜厚を形成できます。このため、部品のどの部分でも同じレベルの保護効果を得ることが可能です。
🔍全表面の均一な保護
電気めっきでは膜厚が均一にならず、薄い部分が腐食しやすくなりますが、無電解ニッケルめっきではそのリスクが大幅に軽減されます。
耐化学薬品性の向上
無電解ニッケルめっきは、酸やアルカリなどの化学薬品に対する耐性も高いです。特に、高リンタイプのめっき層は酸性環境に強く、化学工業の装置や部品に多用されます。
無電解ニッケルめっきは、その高密度な被膜構造、リンの含有による非晶質化、そして均一な膜厚形成により、優れた耐食性を発揮します。この特性は、過酷な環境で使用される部品の寿命を延ばし、メンテナンスコストを削減する効果があります。
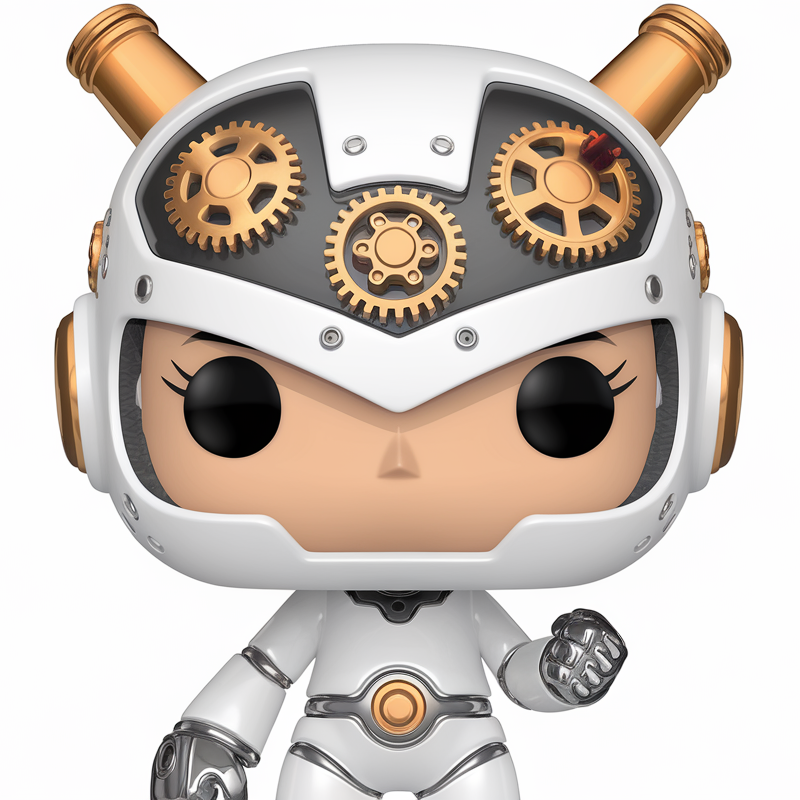
腐食環境での使用が想定される部品や装置において、無電解ニッケルめっきは最適な表面処理選択肢の一つと言えるでしょう。
均一な膜厚を形成できる理由
無電解ニッケルめっきの大きな特長は、複雑な形状や内外部の表面にわたって均一な膜厚を実現できることです。その理由は以下の通りです。
化学反応による析出
- 無電解ニッケルめっきは、化学反応によるニッケルの析出を利用しています。
- 電気めっきのように電流の流れによってめっき層が形成されるわけではないため、電流分布に依存しません。
- 凹凸のある部品や複雑な形状でも、どの部分でも同じ速度でニッケルが析出します。
電流依存性がない
- 電気めっきの場合、電流が強く流れる部位(角や突出部)ほどめっきが厚くなり、凹部や影になる部分では膜厚が薄くなる傾向があります。
- 一方、無電解めっきでは電流を使用しないため、このような膜厚の不均一が発生しません。
浴液の均一性
- めっき液の成分(ニッケルイオンや還元剤)が均一に分布しているため、処理対象の表面全体で均一に反応が進行します。
- さらに、浴液を攪拌することで、溶液の濃度が均一に保たれるため、膜厚の偏りが生じにくい構造になっています。
自触媒作用
- 無電解ニッケルめっきの化学反応には、自触媒作用(ニッケル自身が触媒として機能する現象)が関与しています。
- ニッケルが析出し始めると、それ自体が触媒となって化学反応を促進するため、表面全体で反応が進行します。
- これにより、平面だけでなく、凹部や角部でも均一な膜厚が得られます。
均一性が求められる用途
無電解ニッケルめっきの均一性は、以下のような用途で特に重視されます。
- 複雑な形状の部品
- ギア、バルブ、ポンプなど、凹凸や穴が多い部品。
- 精密機械の部品
- 均一な膜厚が必要な高精度機械部品。
- 耐食性が要求される部品
- 海洋環境や化学工業で使用される金属部品。
- 摺動部品
- 均一な表面処理で摺動性を向上させるために利用される。
無電解ニッケルめっきが均一な膜厚を形成できる理由は、化学反応に基づく析出方法にあります。このプロセスは電流を必要としないため、電気めっきに見られる膜厚の不均一が発生しません。また、浴液の均一性と自触媒作用の特性により、部品の形状にかかわらず、全表面で均一な層を形成できます。
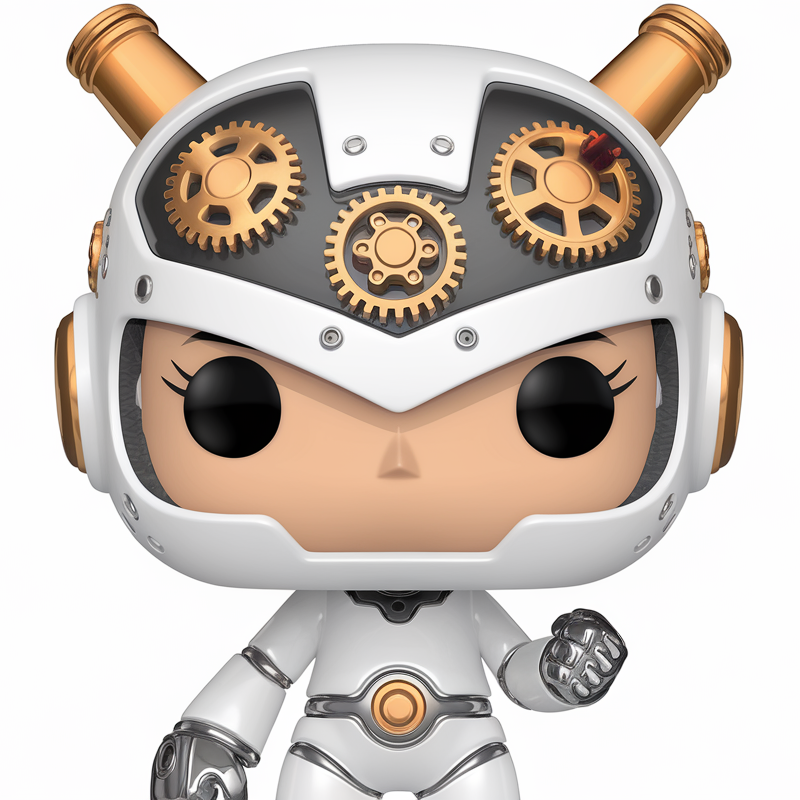
この特性により、無電解ニッケルめっきは耐食性や摺動性が求められる高精度な部品の表面処理に最適な選択肢となっています。
無電解ニッケルメッキとカニゼンメッキ:名称の違いについて
機械設計において、無電解ニッケルメッキとカニゼンメッキという名称を耳にすることがあります。これらは表面処理技術として同じものを指しますが、名称が異なるのには理由があります。
無電解ニッケルメッキは、技術や処理方法を説明する際の一般的な呼び方です。この処理は、電気を用いずに化学反応を利用してニッケルの薄い膜を素材表面に均一に形成するもので、耐食性や硬度の向上、寸法精度の改善などを目的としています。そのため、技術的な解説や仕様書では「無電解ニッケルメッキ」という表現がよく使われます。
一方、カニゼンメッキは、この技術を日本国内に普及させた企業である日本カニゼン株式会社が商標登録しているブランド名です。そのため、同じ処理であっても、日本カニゼンが提供する製品やサービスを指す場合に「カニゼンメッキ」と呼ばれることがあります。つまり、カニゼンメッキは無電解ニッケルメッキの商標名という位置付けです。
結論として、無電解ニッケルメッキとカニゼンメッキは同じ表面処理技術ですが、一般名と商標名という違いがあります。これを理解することで、設計書や取引先との会話において誤解を防ぎ、適切な選定や仕様決定が行えるようになります。
まとめ
無電解ニッケルメッキは、優れた耐食摩耗特性を備え、複雑な形状や寸法精度が必要な部品に適した表面処理方法です。 コストはやや高いですが、その性能と長期的なメリットを考慮すると、多くの用途で効果的な選択肢となります。用途や使用環境に応じて、最適なメッキ処理方法を検討することが重要です。
コメント