材料選定は、機械設計のプロセスにおける重要なステップであり、部品や製品の性能、寿命、コストに大きく影響します。適切な材料を選ぶことで、製品の信頼性、安全性、効率性を高めることができます。
材料選定の基準
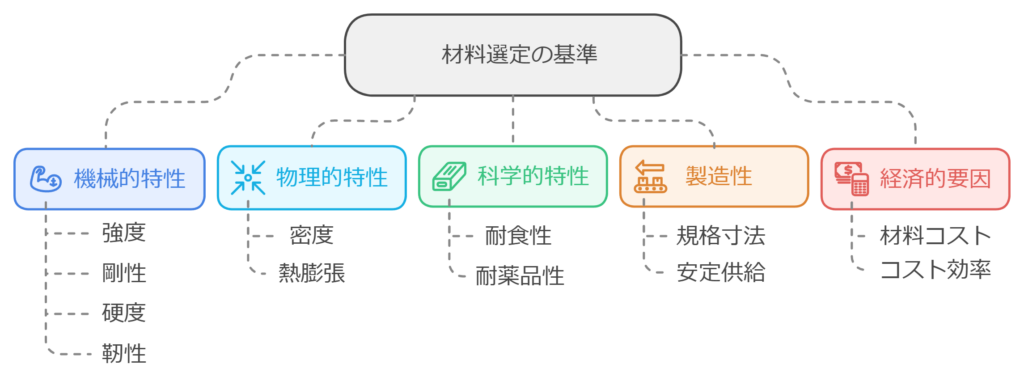
機械的特性
機械設計では、「どんな材料を使うか」が製品の性能・耐久性・コストに大きく関わってきます。
その中でも、「機械的特性」は、部品がどのくらいの力に耐えられるかを判断する上で非常に重要です。
✅ よく使われる機械的特性の種類と意味
特性名 | 説明 |
---|---|
引張強さ(MPa) | 材料が引っ張られて壊れるまでに耐えられる最大の力 |
降伏点(MPa) | 材料が永久に変形しはじめる力 |
硬さ(HB, HRCなど) | 表面の傷つきにくさ |
耐衝撃性(靱性) | 衝撃や急な荷重に対する強さ |
疲労強さ | 繰り返し荷重にどれだけ耐えられるか |
伸び(%) | 材料がどれだけ伸びるか(柔らかさ) |
✅ 設計における使い分けの例
- SS400(一般構造用鋼)
- 強度と加工性のバランスが良く、フレームや構造物に向いています。
- S45C(中炭素鋼)
- 強度が高く、熱処理すればさらに硬くなるので、シャフトや軸部に。
- SUS304(ステンレス鋼)
- 引張強さもあり、耐食性が必要な場合に最適です。
⚠️ 初心者がやりがちなミスと注意点
🚫強度が高ければ良いと思って加工性を無視する
→ 硬すぎて削れないことも…
🚫引張強さばかり見て降伏点を見落とす
→ 小さな力で変形する恐れ
🚫靱性の低い材料を衝撃部品に使って割れる
→ 壊れやすい設計に
✅ 材料は“設計条件に合った特性”で選ぶ!
材料を選ぶときは、「なんとなく硬そうだから」ではなく、
「どのくらいの力がかかるか」「どういう使われ方をするか」に応じて、
適切な機械的特性をもった材料を選定することが大切です。
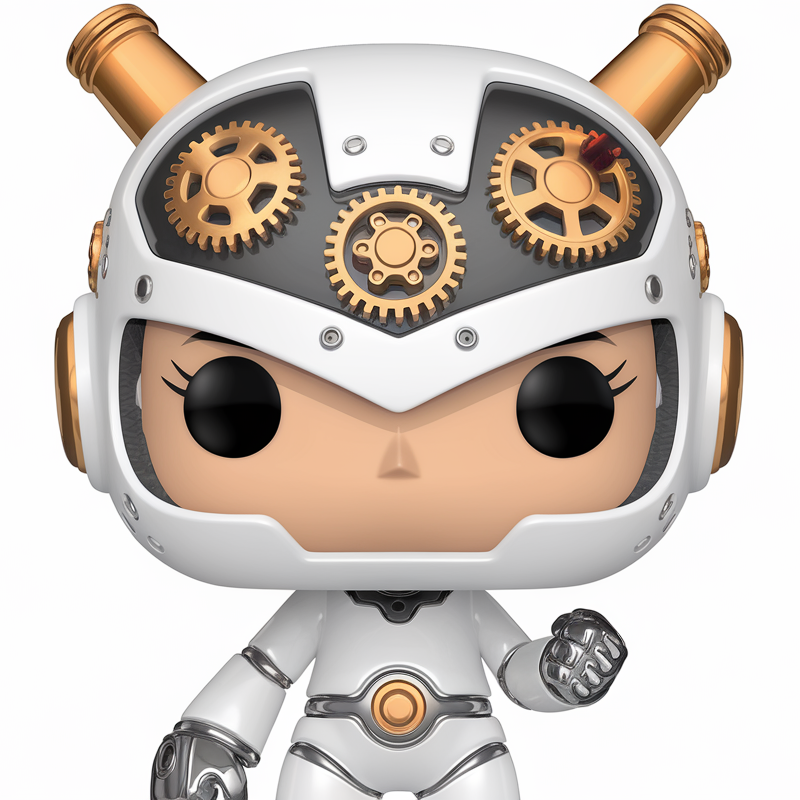
基本的な特性を知っておくだけでも、設計の精度と信頼性がぐっと上がります。
強度
- 外部から加わる力に対して材料がどれだけ耐えられるかを示す特性です。
- 強度は破壊や塑性変形が発生するまでの限界値です。
- 引張強度、圧縮強度、せん断強度などさまざまな形で表されます。
- 荷重がかかる部品や構造物に対して十分な強度を持つ材料を選定する必要があります。
- 安全性と耐久性を確保するために重要です。
剛性
- 外力が加わったときに材料が変形しにくい性質を指します。
- ヤング率(弾性係数)は材料がどれだけの力に対して形状を保持できるかを示す指標です。
- 剛性が高い材料は、一般的に重量が増す傾向があります。
靭性
- 靭性は、材料が破壊される前にどれだけのエネルギーを吸収できるかを示す指標です。
- 外部からの衝撃や負荷に対して、材料がどれだけ変形しながら耐えられるかを評価します。
- 靭性の高い材料は、急激な衝撃や振動、繰り返し荷重に耐えることができます。
- それにより、割れたり破壊したりすることなく使用され続けることができます。
- 逆に、靭性の低い材料は脆く、割れやすい傾向があります。
硬度
- 材料の表面が変形や損傷に対してどれだけ耐えられるかを示す特性です。
- 使用環境や荷重条件に応じた硬度を持つ材料を選定することが、部品の耐久性と性能を左右します。
- 硬度が高すぎると脆さが増し、破損のリスクが高まるため、バランスが重要です。
摺動性
- 部品がスムーズに動作するためには、適切な摺動性が必要です。
- 摩擦を低減し、摩耗を抑えることで、部品の寿命を延ばすことができます。
- 潤滑剤の使用が難しい環境では、自己潤滑性のある材料が有効です。
- 相手材との組み合わせを考慮し、適切な硬度差や表面処理を選定することが重要です。
残留応力
- 残留応力とは、外部からの力が加わっていない状態でも材料内部に存在する応力のことです。
- この応力は、製造プロセス(圧延、鍛造、溶接、熱処理など)や機械加工の過程で発生します。
物理的特性
機械設計では、材料の「強さ」や「硬さ」だけでなく、熱や電気、重さに関する性質も重要です。
使用環境や目的に合わない材料を使うと、熱で変形したり、重すぎて動かせなくなったりといったトラブルが発生します。
✅ 主な物理的特性とその意味
特性名 | 説明 | 設計上のチェックポイント |
---|---|---|
比重(密度) | 材料の重さ(密度) | 軽量化設計・可搬性・慣性対策など |
熱伝導率 | 熱の伝わりやすさ | 放熱部品・ヒートシンク・断熱材選定など |
線膨張係数 | 熱でどのくらい伸びるか | 高温環境での寸法変化への対策 |
比熱 | 温まりにくさ(熱容量) | 急加熱による変形や故障防止 |
電気抵抗率(導電率) | 電気の流れやすさ | 静電気対策・導電部品・絶縁部品の判断 |
磁性 | 磁石にくっつくかどうか | センサ誤作動や磁気対策の要否 |
⚠️ 設計で気をつけたいこと
🚫軽量化したいからと樹脂を使ったら熱変形した
→ 熱伝導・線膨張の確認不足
🚫熱伝導率が高いと放熱効果が良い
→ ヒートシンクや放熱プレートに最適
🚫異なる膨張係数の部品を組み合わせたら
→ 温度変化でズレ・歪みが発生する可能性
✅ 使用環境に合った物理特性を選ぼう!
材料の物理的特性は、「見た目」や「強さ」では判断できません。
軽さ、熱の伝わりやすさ、電気の通しやすさなどは、用途や使用環境によって最適なものが異なります。
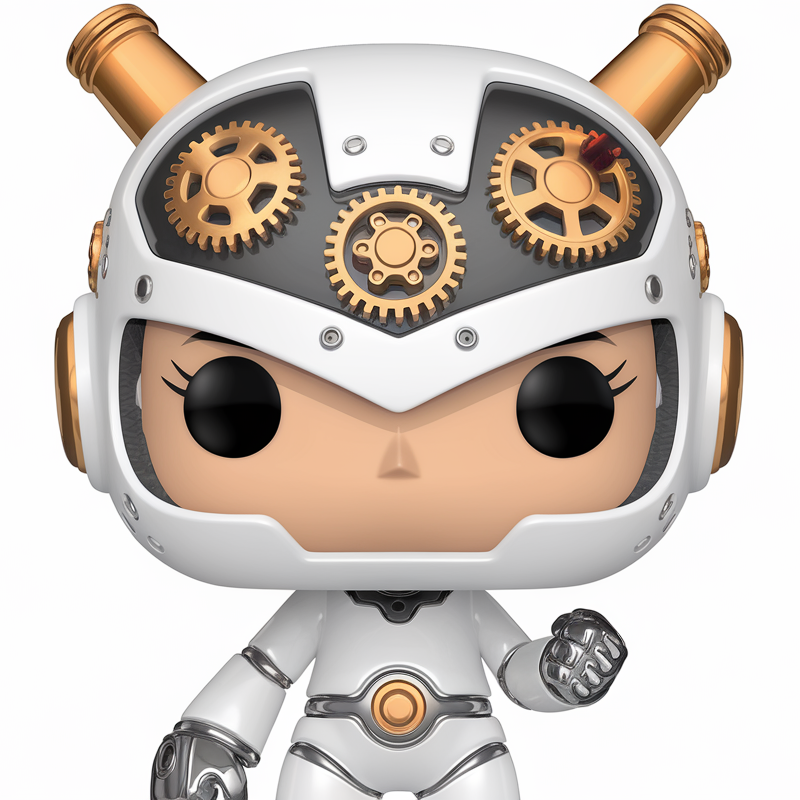
強度だけでなく、「重さ」「熱」「電気」の視点からも材料を選ぶことが、良い設計につながります。
密度
- 密度が高い材料は重く、低い材料は軽くなります。
- 単位体積あたりの質量を示す物理特性で、一般的には「g/cm³」や「kg/m³」で表されます。
- 部品の軽量化や構造の強度を考慮する際に、密度は重要な要素となります。
熱膨張・熱収縮
- 熱膨張とは、温度が上昇したときに材料が膨張する現象です。
- 線膨張係数や体膨張係数などで表され、値が大きいほど温度変化に伴う寸法変化が大きくなります。
- 温度環境に応じて適切な熱膨張特性を持つ材料を選定することが重要です。
電気伝導性・熱伝導性
✅ 電気伝導性
- 電流を効率よく流すために、導電性の高い材料が必要です。
- 電気回路や接点など、低抵抗で安定した導通が求められる部品では重要な要因となります。
✅ 熱伝導性
- 熱を効率よく伝えるために、高い熱伝導性を持つ材料が必要です。
- 放熱や温度管理が重要な部品では、適切な熱伝導性を持つ材料の選定が不可欠です。
▶ 電気伝導性と熱伝導性の相関関係
- 一般に、電気伝導性が高い材料は熱伝導性も高い傾向があります。(例:銅やアルミニウム)
- 金属材料では、「ウィーデマン・フランツの法則」により、電気伝導率と熱伝導率の間に比例関係があることが知られています。
- ダイヤモンドやセラミックスのように、電気を通さないが高い熱伝導性を持つ例外も存在します。
- 適切な材料選定を行うことで、電気特性と熱特性のバランスを考慮した設計が可能となります。
磁性
磁性とは、材料が磁場に反応する性質のことです。
磁石に引き寄せられる、磁力を通す、または磁力を帯びるなど、部品の動作やセンサー機能に大きく影響を与える重要な特性です。
✅ 磁性材料の種類
磁性は大きく以下の3つに分類されます。
- 強磁性:磁石に強く引き寄せられる(鉄、コバルト、ニッケルなど)
- 反磁性:わずかに磁場を打ち消す性質(銅、銀、水など)
- 常磁性:弱く磁場に引かれる(アルミニウム、酸素など)
このうち強磁性材料は、磁石にくっついたり、磁力を保持することができるため、モーター、リレー、磁気センサー、磁気保持具などでよく使われます。
磁性は目に見えませんが、製品の性能や安全性に大きく関わる物性です。
使用環境や設計目的に応じて、適切な磁性材料を選ぶことが、トラブルのない機械設計につながります。
科学的特性
機械設計では、強度や重さだけでなく、「サビにくいか? 薬品に強いか?」といった化学的な性質もとても重要です。
特に、水まわり、屋外、薬品を扱う装置などでは、化学的特性を考慮しないとすぐに劣化・腐食してしまいます。
✅ 主な化学的特性とその意味
特性名 | 説明 | 設計での注意ポイント |
---|---|---|
耐食性 | 錆びや腐食のしにくさ | 水回り、屋外、湿気の多い場所 |
耐薬品性 | 酸・アルカリ・溶剤に対する強さ | 薬品を扱う装置、クリーン環境など |
酸化しにくさ | 空気との反応のしにくさ | 高温環境・加熱部品での酸化防止 |
ガス透過性の低さ | ガスが通り抜けにくい性質 | 真空容器・密閉構造に使用する材料 |
電解腐食の防止性 | 異種金属同士の接触で起こる腐食への耐性 | 異素材の接触部に注意が必要 |
⚠️ 設計時に気をつけたいポイント
🚫SUS304は耐食性が高いが、塩素系薬品には弱い
→ プール設備や漂白剤のある場所には不向き
🚫鉄材(SS400など)は錆びやすい
→ 使うならメッキや塗装などの表面処理を検討
🚫異種金属(例:アルミと銅)を接触させると電解腐食が起きることがある
→ 絶縁処理やスペーサを入れるなどの工夫が必要
✅ 環境に合った化学的特性を選ぼう!
材料は見た目や強度だけでなく、「腐食しにくいか? 薬品に負けないか?」といった化学的な特性にも目を向けることが、長く使える製品を設計するためには欠かせません。
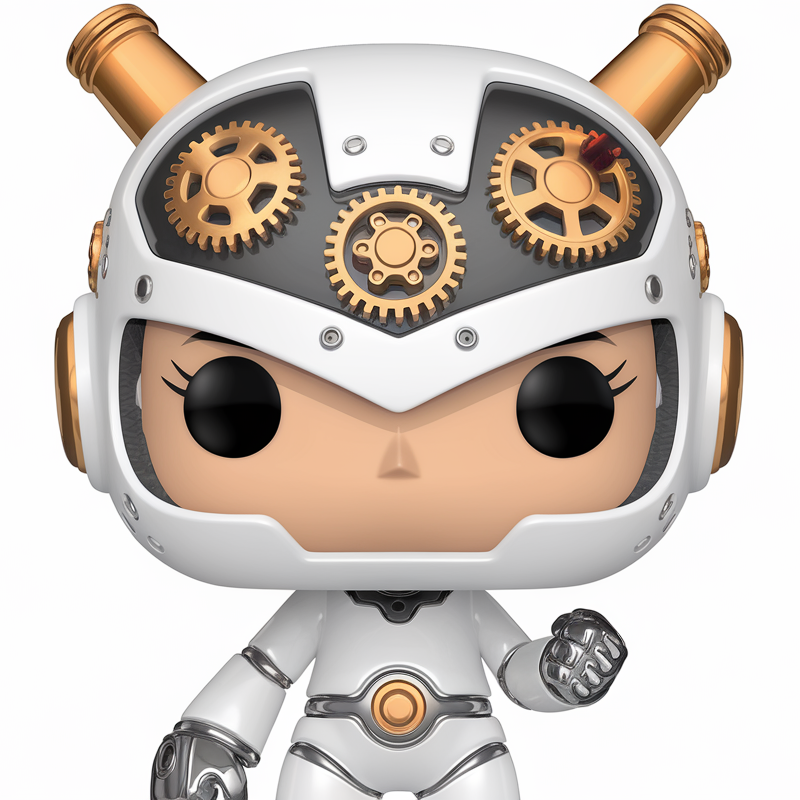
使用環境(屋外・薬品使用・水中など)をよく確認し、材料の化学的性質を考慮することが大切です!
耐食性
- さびや腐食に対する耐性が必要です。
- 特定の環境下で長期間使用される部品では重要な要因となります。
耐熱性
- 高温環境でも強度や寸法精度を維持できる材料が必要です。
- 熱膨張や酸化の影響を考慮し、適切な材料を選定することが重要です。
耐寒性
- 低温環境でも脆化せず、十分な靭性を維持できる材料が必要です。
- 極低温環境では、衝撃強度の低下や割れのリスクを考慮する必要があります。
耐薬品性
- 特定の化学物質に対して劣化や腐食しにくい材料が必要です。
- 使用環境に応じて、酸、アルカリ、有機溶剤などへの耐性を考慮することが重要です。
耐候性
- 紫外線・雨風・温度変化に対する耐性が必要です。
- 屋外や過酷な環境で使用される部品では重要な要因となります。
製造性
- 加工が容易であるか、コスト効率よく製造できるかを評価します。
- 加工技術に適した材料を選ぶことで製造工程が簡素化されます。
- 設計前に、使用する材料の規格寸法を確認し、設計に反映させる必要があります。
規格寸法
- 市販の規格寸法に合わせた設計を行うことで、材料調達が容易になりコスト削減につながります。
- 規格外の寸法が必要な場合、追加の加工や特注対応が必要となり、コストや納期に影響を与える可能性があります。
🔗【SS400】平鋼の規格寸法【ミガキ】
🔗【S45C】 ミガキ丸棒の規格寸法と活用法【寸法表】
🔗【SUS304】平鋼の規格寸法
🔗【SUS304】平鋼と板の種類【HOT.COLD】
🔗【SPCC】板厚規格と特性と選定ポイント
🔗【キー材】キー材の規格寸法【新JIS・旧JIS1種・2種】
🔗【山形鋼】アングルの規格寸法と選定ポイント【L字型断面】
🔗【溝形鋼】チャンネルの規格寸法と選定ポイント【U字型断面】
🔗【H鋼】H形鋼の規格寸法と選定ポイント【H型断面】
🔗【角パイプ】STKRの規格寸法と選定ポイント【箱型断面】
🔗【鉄パイプ】STKM13Aの規格寸法と選定ポイント【STKM】
🔗【配管材料】SGPの規格寸法と選定ポイント【鉄パイプ】
経済性(コスト)
- 材料費だけでなく、加工費やメンテナンス費用も考慮することが重要です。
- 高価な材料でも、耐久性や加工性が優れていればトータルコストを抑えられる場合があります。
- 大量生産の場合、入手しやすい規格品を選ぶことでコスト削減につながります。
- 必要以上に高性能な材料を選ばず、用途に適したコストバランスの良い材料選定が大切です。
材料の種類と選定
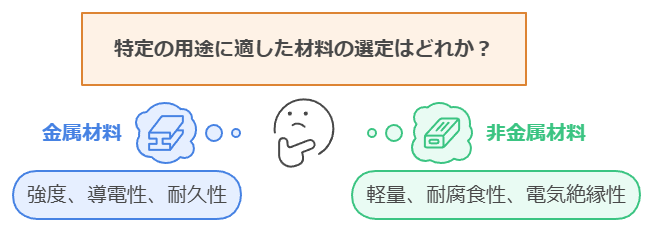
金属材料
機械設計において、材料選定は製品の性能やコストに大きく影響を与えます。特に金属材料は、強度・剛性・耐摩耗性・加工性などのバランスが求められるため、用途に応じた適切な選定が重要です。
鋼材やアルミ合金、ステンレス鋼、銅合金など、それぞれの金属材料には特性やメリット・デメリットがあり、使用環境や要求特性に応じて選択する必要があります。本項では、機械設計における主要な金属材料の特性と選定ポイントについて解説します。
SS400(一般構造用圧延鋼材)
- 一般構造用鋼材として広く使用される汎用性の高い材料です。
- 加工性や溶接性に優れ、コストパフォーマンスが良好です。
- 強度は中程度で、過度な衝撃や高荷重には注意が必要です。
- 耐食性は低いため、防錆処理(塗装・メッキなど)が推奨されます。
S45C(中炭素鋼)
- 中炭素鋼であり、強度や耐摩耗性に優れています。
- 熱処理(焼入れ・焼戻し)を施すことで、さらに高い硬度や強度を得ることができます。
- 機械加工性は良好ですが、硬化処理後は切削が難しくなるため注意が必要です。
- 耐食性は低く、錆びやすいため、防錆処理(メッキ・塗装・防錆油など)が推奨されます。
SPCC(冷間圧延鋼板)・SPHC(熱間圧延鋼板)
- SPCC:冷間圧延による高い寸法精度と滑らかな表面。プレス加工や曲げ加工が容易。
- SPHC:熱間圧延のため表面が粗いが、コストが安く、大型部品や溶接用途に適する。
ステンレス鋼(SUS材)
- さびに強く、耐食性に優れるため、湿気や水分が多い環境でも使用可能です。
- 種類が豊富(SUS304、SUS316、SUS440C など)で、用途に応じた選定が可能です。
- 強度や耐熱性に優れたグレードもあり、食品機械、医療機器、化学設備など幅広く使用されます。
- 加工性や溶接性はグレードによって異なるため、用途に応じた選択が必要です。
- コストは一般鋼材より高めですが、メンテナンスの手間が少なく、長期的なコストメリットがある場合もあります。
工具鋼(SK材)
- 高硬度・高耐摩耗性を持ち、切削工具や金型、パンチなどの高荷重部品に適しています。
- 焼入れ処理を施すことで、さらに硬度や耐久性を向上させることが可能です。
- 種類によって特性が異なります。
- 炭素工具鋼(SK)、合金工具鋼(SKS,SKD)、高速度工具鋼(SKH)などに分類されます。
- 一般的な炭素鋼と比べて加工が難しく、切削や研削に適した工具の選定が重要になります。
クロムモリブデン鋼(SCM材)
- クロム(Cr)とモリブデン(Mo)の添加により、高強度・高靭性を兼ね備えた合金鋼です。
- 熱処理(焼入れ・焼戻し)を施すことで、さらなる強度・耐摩耗性の向上が可能です。
- 高温環境下でも優れた強度を維持するため、機械部品や航空・自動車部品などに多用されます。
- 炭素鋼(SS400、S45C)よりも耐食性が高いですが、使用環境によっては防錆処理が推奨されます。
高炭素クロム軸受鋼(SUJ)
- 炭素(C)とクロム(Cr)を多く含むことで、高硬度・高耐摩耗性に優れた鋼材です。
- 熱処理を行うことで、HRC60前後の高硬度を実現し、長寿命の軸受やシャフトに最適です。
- 表面に高周波焼入れを施すことで、耐摩耗性と芯部の靭性を両立させた設計が可能です。
- 主にベアリング部品、スライドシャフトなど、高精度・耐摩耗性が求められる用途に使われています。
プリハードン鋼(NAK材、PX材 など)
- あらかじめ焼入れ・焼戻しされた状態で供給される鋼材で、追加の熱処理なしで使用可能です。
- 硬度と靭性のバランスが良く、加工後の変形が少ないため、精密部品や金型用途に適しています。
- 切削性や放電加工性が良好で、熱処理を省略できるため、製造コストやリードタイムを削減できます。
- 一般的な炭素鋼(SS400、S45C)よりも耐摩耗性・耐衝撃性に優れる。
アルミ合金
- 軽量で高い比強度を持ち、重量を抑えたい構造部品に適しています。
- 優れた耐食性を備えており、特に海水や湿気の多い環境での使用に強みを発揮します。
- 加工性が良好で、切削・塑性加工・溶接が比較的容易なため、多様な製造方法に対応可能です。
- 熱伝導率が高く、放熱性が求められる部品(ヒートシンクなど)にも適用されます。
- 純アルミに比べて強度が高いものの、鋼材と比べると耐摩耗性・剛性が劣るため、用途に応じた選定が必要です。
🔍アルミ合金の選定ポイント
🔗アルミ合金の特性と選定ポイント
🔗アルミ合金の引張強さランキング!どれが強い?使い分けのポイントも解説【熱処理と加工性】
🔗SS400とアルミ合金の違いと使い分けを徹底解説!【比重・剛性・コスト】
🔗SS400とA7075の違いと使い分け方をわかりやすく解説!【強度と剛性】
🔗アルミ合金と樹脂の違いと使い分けとは?【材料選定における軽量化】
🔍アルミ合金の種類について
🔗【アルミ合金】A2000番代とは?特性・用途・選定ポイントをわかりやすく解説!【ジュラルミン系】
🔗【アルミ合金】A5052・A5056の違いと特性【汎用アルミ】
🔗【アルミ合金】6000番代とは?特性と使い分けをわかりやすく解説!【アルミフレーム】
🔗【アルミ合金】A7075の特性と選定ポイント【超々ジュラルミン】
アルミフレーム
- 軽量かつ高剛性を兼ね備えたアルミフレームで、各種機械や装置の構造材として広く使用されます。
- モジュール化された設計により、フレーム組立や変更が容易で、設計変更にも柔軟に対応できます。
- アルマイト処理が施されているため、耐食性が高く、屋内外を問わず安定した性能を発揮します。
- 鋼材(SS400、S45C)と比べて軽量で取り扱いやすく、搬送装置や作業台のフレームとして最適です。
形鋼(H形鋼、チャンネル、アングルなど)
- 建築・機械構造に広く使用される鋼材で、断面形状により強度や剛性が最適化されています。
- H形鋼は高い曲げ強度と剛性を持ち、大きな荷重を受ける構造部材に適しています。
- チャンネル(C形鋼)は軽量で加工性が良好なため、補強部材やフレーム構造に多用されます。
- アングル(L形鋼)はコーナー補強や小型フレームに適しており、強度と加工性のバランスが良好です。
- 一般的にSS400が使用されることが多いですが、用途に応じてS45Cやステンレス鋼も選定可能。
非金属材料
軽量かつ耐薬品性に優れる材料群で、摺動部品や絶縁部品などに幅広く使用されます。
金属材料(SS400、S45C、SUSなど)と比較して強度は劣るものの、軽量化や耐食性・耐薬品性の要求される環境で有用です。
樹脂(プラスチック)
- 軽量で加工性に優れた材料群であり、摺動部品や電気絶縁部品など幅広い用途に使用されます。
- POM(ポリアセタール)やMCナイロンは低摩擦特性を持ち、ギアやスライド部品に適用されます。
- PEEKやPPSは高耐熱性・耐薬品性を備え、過酷な環境下での使用が可能です。
ゴム
- 弾性と耐衝撃性に優れ、衝撃吸収材やシール材として広く使用される材料です。
- 耐薬品性・耐熱性・耐候性に優れた種類もあり、用途に応じた選定が可能です。
- 種類によって硬度や特性が異なり、ウレタンゴム、ニトリルゴム、フッ素ゴムなどが代表的です。
- 金属や樹脂と組み合わせることで、振動・騒音対策や防水・防塵機能を向上させることができます。
セラミックス
- 優れた耐熱性・耐摩耗性を持ち、高温環境や摩耗が激しい部品に適しています。
- 金属よりも軽量でありながら高硬度を誇り、耐食性にも優れています。
- 電気絶縁性が高く、電子部品や絶縁部材としても利用されます。
- 脆性があり、衝撃や急激な温度変化に弱いため、設計時には注意が必要です。
表面処理・熱処理の種類と選定
表面処理も材料の一部として選定することで、製品の特性を大きく変えることができます。
適切な表面処理を選ぶことで、性能向上やコスト削減につながり、製品の品質向上を実現します。
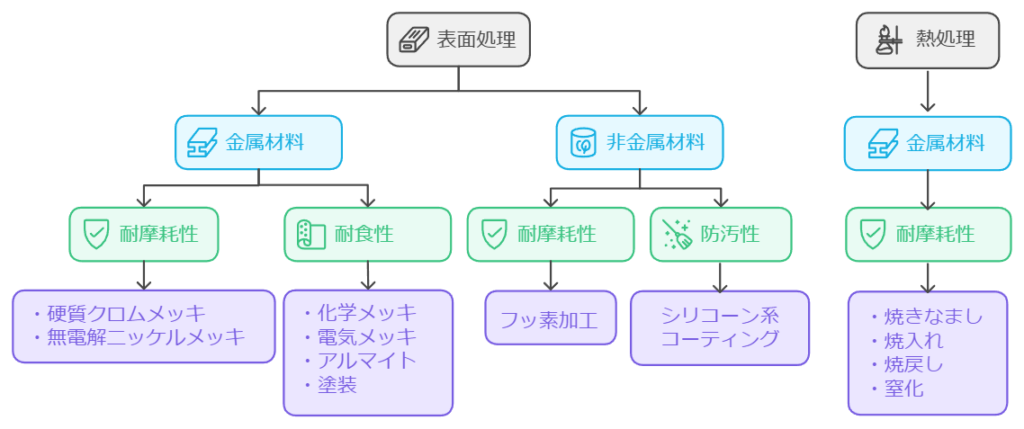
表面処理
- 電気メッキ: 金属表面に薄い金属層を形成し、耐腐食性や美観を向上させます。
- 化学メッキ: 化学反応を利用して均一なコーティングを施し、耐摩耗性や導電性を付与します。
窒化処理
- 窒化とは、金属表面に窒素を浸透させ、硬い窒化層を形成する処理です。
- 耐摩耗性、耐疲労性、耐食性を向上させる効果があります。
- ガス窒化、塩浴窒化(タフトライド)などの種類があり、用途に応じた選定が重要です。
アルマイト
- アルマイトとは、アルミニウムの表面に人工的に酸化被膜を形成する処理です。
- 耐食性や耐摩耗性を向上させるだけでなく、絶縁性や装飾性も向上します。
- 用途に応じて通常アルマイト、硬質アルマイト、カラーアルマイトなどを選定できる。
- 機能性やデザイン性を高めることができます。
熱処理
- 熱処理とは、金属材料を加熱・冷却することで、硬度や靭性などの性質を変化させる処理です。
- 目的は強度向上、耐摩耗性向上、残留応力の低減など多岐にわたります。
- 焼入れ、焼戻し、焼ならし、浸炭焼入れなどの種類があります。
- 用途に応じた適切な熱処理を選定することが重要です。
🔗なぜ鋼材は熱処理で硬くなるの?金属の変態と強度アップの秘密
🔗【焼入れ】【焼戻し】特性と選定ポイント【熱処理】
🔗全体焼入れ(ズブ焼入れ)とは?初心者にもわかる基本と注意点
🔗高周波焼入れとは?|表面だけを硬くする熱処理の基本と使いどころ
🔗真空焼入れとは?|クリーンな仕上がりが求められる部品に最適な熱処理法
🔗浸炭焼入れとは?機械設計でよく使われる熱処理をわかりやすく解説
🔗ソルト焼入れとは?特徴・メリット・使い分けをやさしく解説!【焼入れ種類の比較】
🔗シャフト・ベアリングに使われるSUJ2ってどんな材質?【高周波焼入れ】
🔗スプロケット・歯車の「歯先焼入れ」とは?その目的と効果をわかりやすく解説!
🔗熱処理前に研磨代を確保する重要性
塗装
- 粉体塗装: 静電気を利用して粉体塗料を付着させ、耐久性と美観を両立します。
- 液体塗装: スプレーや刷毛を使って液体塗料を塗布し、色や質感を自由に調整できます。
機械設計における材料選定のプロセス
機械設計において、材料選定は製品の性能、耐久性、コストに大きな影響を与える重要なプロセスです。適切な材料を選定することで、設計の目的を達成し、信頼性と効率性を高めることができます。本記事では、材料選定のプロセスを具体的なステップに分けて解説します。
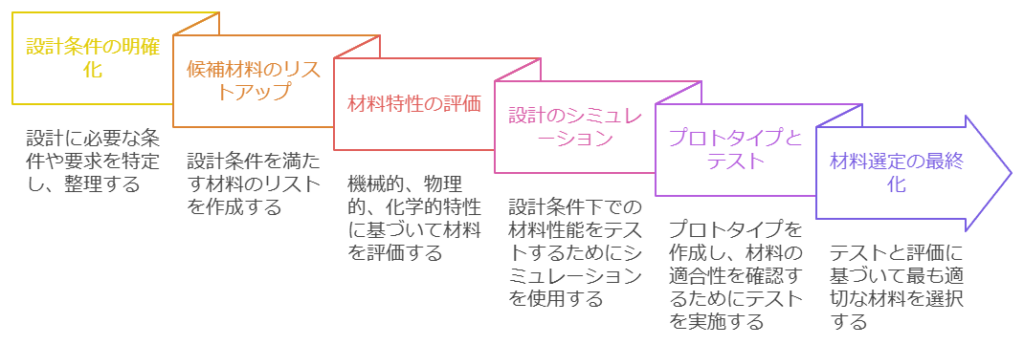
1. 設計条件の明確化
まず、設計に必要な条件や要求を明確にすることが重要です。
以下のような要素を洗い出します。
✅ 使用環境: 温度、湿度、腐食、摩耗の有無
✅ 荷重条件: 静的荷重、動的荷重、衝撃荷重
✅ 寸法制約: 部品の大きさや形状,重量に関する制限
✅ 性能要求: 強度、硬度、耐熱性、耐腐食性など
✅ 法的・規格的要件: JIS、ISO、RoHSなどの基準に適合するか
2. 候補材料のリストアップ
設計条件を満たす可能性のある材料をリストアップします。この段階では、幅広い選択肢を考慮し、後の絞り込みに備えます。
✅金属材料
鋼(SS400、S45C)、ステンレス(SUS304、SUS440C)、アルミニウム合金(A5052、A7075)など
✅樹脂材料
MCナイロン、POM、PEEKなど
✅複合材料
CFRP、GFRPなど
候補材料の基本特性(比重、ヤング率、硬度、引張強度など)を比較するため、材料データシートやカタログを参照します。
3. 材料特性の評価
候補材料について、以下の特性を評価します。
▶ 機械的特性
引張強度、降伏強度、硬度、疲労強度など。
🔍例: 高負荷を受ける場合、S45CやSCM440のような強度の高い材料が適しています。
▶ 物理的特性
比重、熱膨張係数、導電性、熱伝導率など。
🔍例: 軽量化が必要な場合、アルミニウム合金やCFRPが有効です。
▶ 化学的特性
耐食性、耐薬品性、酸化防止性など。
🔍例: 腐食環境ではSUS304やSUS316が適しています。
▶ 加工性
切削、溶接、曲げ加工の容易さ。
🔍例: 複雑な形状が必要な場合は、加工性の良いSS400やPOMが選ばれます。
▶ 経済性
材料コスト、加工コスト、供給の安定性。
🔍例: コストを抑えたい場合は、汎用性が高く安価なSS400が適しています。
4. 設計シミュレーション
候補材料を用いた設計を仮想環境でシミュレーションします。
- 構造解析: FEA(有限要素解析)を用いて強度や変形を確認します。
- 熱解析: 材料の熱膨張や熱伝導を評価します。
- 寿命試算: 疲労強度や摩耗の進行を予測します。
これにより、理論上の適合性を検証できます。
5. 試作と実証試験
最適と思われる材料で試作品を製作し、実証試験を行います。
- 性能試験: 実際の使用条件下での強度、耐久性、摩耗性を確認します。
- 加工試験: 加工中に問題が発生しないか評価します。
- コスト試算: 試作工程を通じて、材料費や加工費が許容範囲内か確認します。
6. 最終選定
試作と試験結果をもとに、最終的な材料を選定します。この段階では、技術的な特性だけでなく、以下の要因も考慮します。
- 供給の安定性: 長期的に安定して入手可能か。
- 環境負荷: リサイクル可能性や環境規制への適合。
- 顧客要件: 見た目や触感などのデザイン的要求。
7. 材料選定の記録
選定した材料の理由やプロセスを文書化し、関係者と共有します。これにより、設計変更時やトラブル発生時に迅速な対応が可能になります。
まとめ
材料選定は、設計プロセスの中でも特に重要なステップです。設計条件を明確にし、適切な材料を選定することで、製品の信頼性と効率性を向上させることができます。プロセスを一貫して行うことで、設計ミスを防ぎ、コスト削減にもつながります。
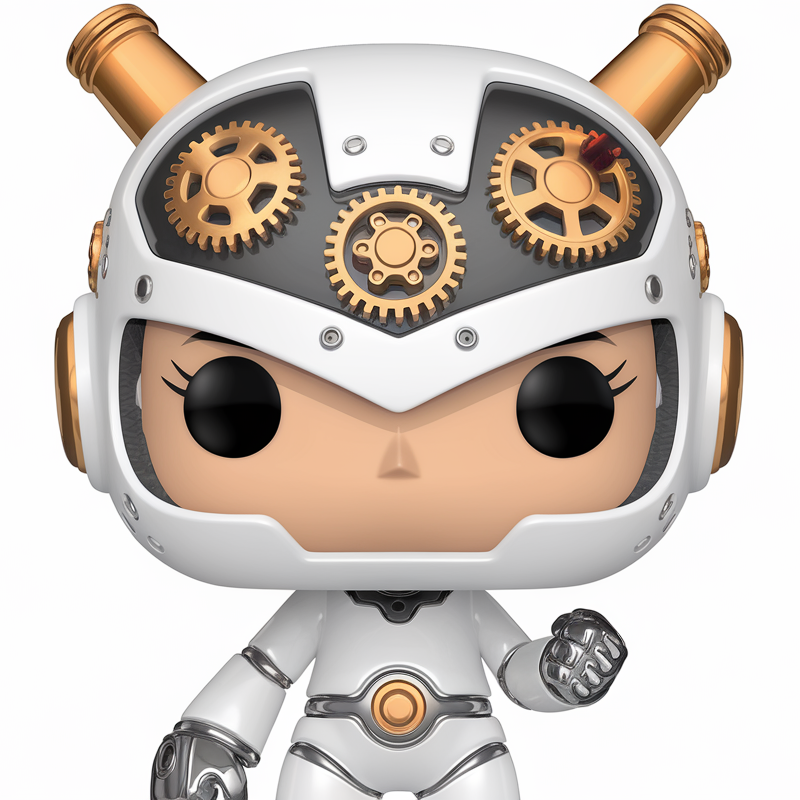
材料選定は、設計の初期段階でしっかりと考慮する必要があります。
適切な材料を選ぶことで、製品のパフォーマンスと寿命を最適化することができます。
このプロセスを慎重に行うことで、最終的な製品の品質を保証することができます。